What is a PCB?
PCB stands for Printed Circuit Board. It is a thin board made of fiberglass or other composite material that is used to mechanically support and electrically connect electronic components using conductive pathways, tracks or signal traces etched from copper sheets laminated onto a non-conductive substrate.
PCBs are the foundation of modern electronics and are used in nearly all electronic devices, from smartphones and computers to medical equipment and aerospace systems. They provide a reliable and efficient means of connecting electronic components and allow for the miniaturization of complex circuits.
What are the different types of PCBs?
There are several types of PCBs, each with its own unique characteristics and applications. The most common types of PCBs include:
PCB Type | Description | Applications |
---|---|---|
Single-sided PCB | Has components on one side and conductive traces on the other side | Simple, low-cost devices such as calculators and radios |
Double-sided PCB | Has components and conductive traces on both sides of the board | More complex devices such as power supplies and amplifiers |
Multi-layer PCB | Has multiple layers of conductive traces separated by insulating layers | High-speed, high-density devices such as computers and smartphones |
Flexible PCB | Made of flexible materials such as polyimide, can be bent or folded | Wearable devices, medical implants, aerospace systems |
Rigid-Flex PCB | Combines rigid and flexible sections in a single board | Devices that require both stability and flexibility, such as cameras and displays |
What is the PCB manufacturing process?
The PCB manufacturing process involves several steps, each of which is critical to ensuring the quality and reliability of the final product. The main steps in the PCB manufacturing process are:
-
Design: The PCB design is created using specialized software such as Altium Designer or Eagle. The design includes the layout of the components, the routing of the conductive traces, and the placement of vias and other features.
-
Printing: The PCB design is printed onto a photosensitive film or directly onto the copper-clad board using a plotter or direct imaging system.
-
Etching: The exposed areas of the copper-clad board are etched away using a chemical solution, leaving only the desired conductive traces.
-
Drilling: Holes are drilled into the board to accommodate through-hole components and vias.
-
Plating: The holes are plated with copper to provide electrical connectivity between layers.
-
Solder Mask: A layer of solder mask is applied to the board to protect the conductive traces and prevent short circuits.
-
Silkscreen: Text and symbols are printed onto the board using silkscreen to provide identification and orientation information.
-
Surface Finish: A surface finish such as HASL (Hot Air Solder Leveling) or ENIG (Electroless Nickel Immersion Gold) is applied to the exposed copper to prevent oxidation and improve solderability.
-
Inspection: The finished PCB is inspected for defects and tested for functionality.
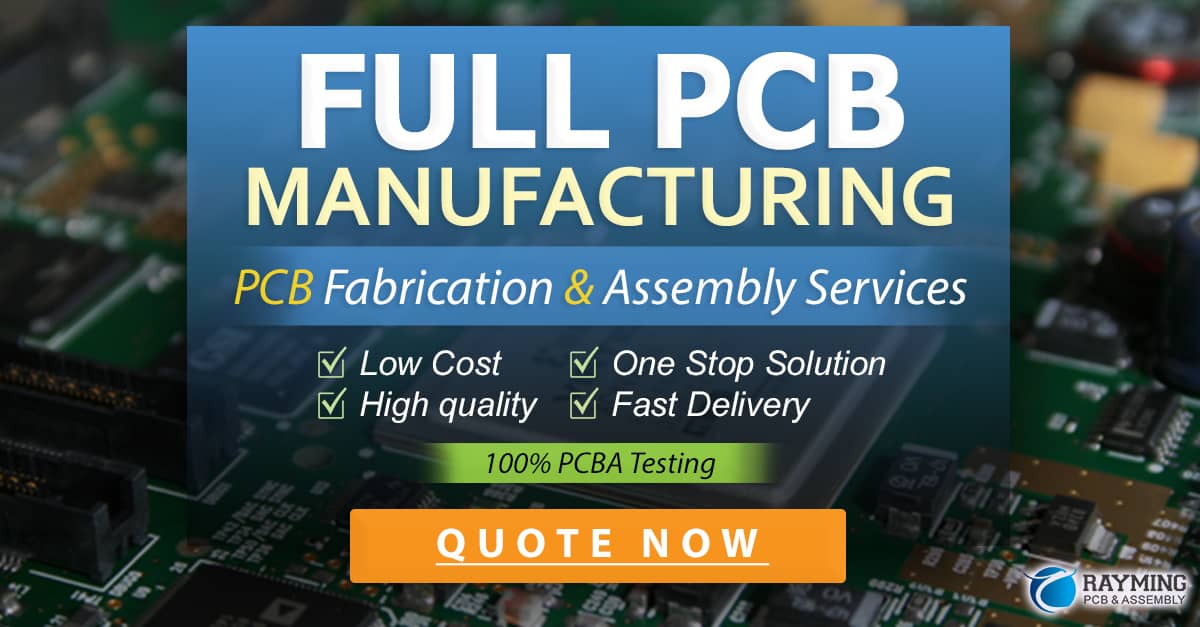
What is PCB assembly?
PCB assembly is the process of attaching electronic components to a printed circuit board to create a functional electronic assembly. The main steps in the PCB assembly process are:
-
Solder Paste Application: Solder paste is applied to the pads on the PCB where the components will be placed. This is typically done using a stencil and a squeegee.
-
Component Placement: The components are placed onto the PCB using a pick-and-place machine. The machine uses a vacuum nozzle to pick up the components from a feeder and place them onto the pads on the PCB.
-
Reflow Soldering: The PCB is passed through a reflow oven, which heats the solder paste to its melting point, allowing it to flow and create a permanent electrical and mechanical connection between the components and the PCB.
-
Inspection: The assembled PCB is inspected for defects such as missing or misaligned components, solder bridges, or insufficient solder joints.
-
Testing: The assembled PCB is tested for functionality using automated test equipment (ATE) or manual testing methods.
What are some common PCB design guidelines?
To ensure the reliability and manufacturability of PCBs, it is important to follow certain design guidelines. Some of the most common PCB design guidelines include:
Guideline | Description |
---|---|
Trace Width and Spacing | Ensure that the width and spacing of conductive traces are appropriate for the current and voltage requirements of the circuit |
Via Size and Spacing | Ensure that vias are sized and spaced appropriately to prevent signal integrity issues and manufacturing defects |
Component Placement | Place components in a logical and organized manner to minimize signal path lengths and improve manufacturability |
Thermal Management | Consider the thermal requirements of the components and design the PCB to dissipate heat effectively |
EMI/EMC | Design the PCB to minimize electromagnetic interference (EMI) and ensure electromagnetic compatibility (EMC) with other devices |
DFM | Design for manufacturability (DFM) by adhering to the capabilities and limitations of the PCB manufacturing process |
FAQ
1. What is the difference between through-hole and surface-mount components?
Through-hole components have leads that are inserted into holes drilled in the PCB and soldered to pads on the opposite side. Surface-mount components are placed directly onto pads on the surface of the PCB and soldered in place. Surface-mount components are smaller and can be placed more densely on the PCB, but through-hole components are more mechanically robust.
2. What is the difference between lead-free and leaded solder?
Lead-free solder is a solder alloy that does not contain lead, while leaded solder contains a small amount of lead. Lead-free solder is required for most consumer electronics products due to environmental and health concerns, but leaded solder is still used in some industrial and military applications due to its superior mechanical properties.
3. What is the purpose of a solder mask?
A solder mask is a layer of polymer material applied to the surface of a PCB to protect the copper traces from oxidation and prevent solder bridging between adjacent pads. The solder mask also provides electrical insulation and helps to prevent short circuits.
4. What is the difference between a single-sided and a double-sided PCB?
A single-sided PCB has components and conductive traces on only one side of the board, while a double-sided PCB has components and traces on both sides. Double-sided PCBs offer more routing options and higher component density than single-sided PCBs, but are more complex and expensive to manufacture.
5. What is the purpose of a via in a PCB?
A via is a small hole drilled in a PCB that is used to connect conductive traces on different layers of the board. Vias allow signals to pass through the board and provide electrical connectivity between components on different sides of the board. Vias are plated with copper to provide a low-resistance electrical path.
0 Comments