Introduction to PCB Equipment
Printed Circuit Board (PCB) manufacturing is a complex process that requires precision, accuracy, and efficiency. To achieve these goals, various types of PCB equipment are used throughout the production process. Among the most critical pieces of equipment are those responsible for loading and unloading PCBs during different stages of manufacturing.
PCB loading and unloading equipment plays a vital role in ensuring smooth and efficient production flow while minimizing the risk of damage to the delicate boards. These machines are designed to handle PCBs of various sizes, shapes, and thicknesses, and can be customized to meet the specific requirements of different manufacturing facilities.
Types of PCB Loading & Unloading Equipment
There are several types of PCB loading and unloading equipment, each designed for specific tasks and stages of the manufacturing process. Some of the most common types include:
-
Magazine Loaders and Unloaders
Magazine loaders and unloaders are used to transfer PCBs between magazines and conveyor systems. They are designed to handle large volumes of boards and can be automated to increase efficiency and reduce manual labor.
-
Conveyor Systems
Conveyor systems are used to transport PCBs between different stages of the manufacturing process. They can be customized to accommodate various board sizes and shapes and can include features such as edge protection and automatic alignment.
-
Robotic Loaders and Unloaders
Robotic loaders and unloaders are advanced systems that use robotic arms to pick up and place PCBs with high precision. They are often used in high-volume production environments where speed and accuracy are critical.
-
Shuttle Systems
Shuttle systems are used to transfer PCBs between different levels or sections of a manufacturing facility. They can be designed to handle multiple board sizes and can include features such as automatic alignment and board flipping.
Benefits of PCB Loading & Unloading Equipment
Investing in high-quality PCB loading and unloading equipment offers several benefits for manufacturing facilities, including:
-
Increased Efficiency
Automated loading and unloading systems can significantly increase production speed and reduce cycle times, allowing manufacturers to produce more boards in less time.
-
Improved Accuracy
Advanced loading and unloading equipment, such as robotic systems, can achieve high levels of precision and accuracy, reducing the risk of errors and ensuring consistent quality.
-
Reduced Manual Labor
Automated systems can minimize the need for manual handling of PCBs, reducing labor costs and freeing up workers to focus on other tasks.
-
Enhanced Safety
Loading and unloading equipment can be designed with safety features, such as sensors and emergency stop buttons, to protect workers from potential hazards.
Factors to Consider When Choosing PCB Loading & Unloading Equipment
When selecting PCB loading and unloading equipment for a manufacturing facility, several factors should be considered to ensure the best fit for the specific production requirements. These factors include:
-
PCB Size and Shape
The equipment should be capable of handling the specific sizes and shapes of PCBs being manufactured, including any variations or custom designs.
-
Production Volume
The capacity and speed of the loading and unloading equipment should be matched to the anticipated production volume to ensure efficient operation and avoid bottlenecks.
-
Integration with Existing Systems
The new equipment should be compatible with existing machines and systems in the manufacturing facility to ensure seamless integration and avoid disruptions to production flow.
-
Maintenance and Support
Manufacturers should consider the availability of maintenance and support services from the equipment supplier to ensure minimal downtime and quick resolution of any issues that may arise.
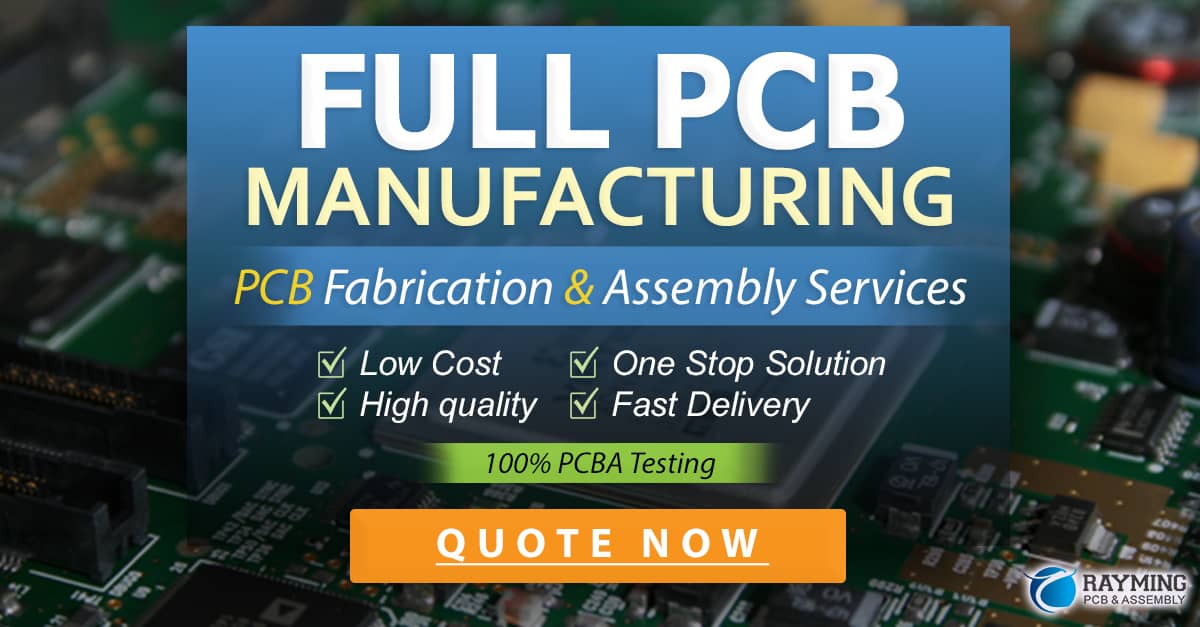
Advancements in PCB Loading & Unloading Technology
As the PCB industry continues to evolve, so too does the technology used in loading and unloading equipment. Some of the latest advancements include:
-
Vision Systems
Advanced vision systems can be integrated with loading and unloading equipment to inspect PCBs for defects and ensure proper alignment and orientation.
-
Artificial Intelligence (AI) and Machine Learning (ML)
AI and ML technologies can be used to optimize the performance of loading and unloading systems, enabling them to adapt to changing production requirements and identify potential issues before they cause disruptions.
-
Industrial Internet of Things (IIoT)
IIoT technologies can be used to connect loading and unloading equipment with other machines and systems in the manufacturing facility, enabling real-time monitoring and data analysis for improved efficiency and quality control.
Examples of PCB Loading & Unloading Equipment
To better understand the capabilities and applications of PCB loading and unloading equipment, let’s look at some specific examples:
Equipment Type | Example | Description |
---|---|---|
Magazine Loader/Unloader | Eunil E1100 | Automated system for loading and unloading PCBs from magazines, with a capacity of up to 1,100 boards per hour. |
Conveyor System | Yamaha YK Series | Modular conveyor system for transporting PCBs between different stages of the manufacturing process, with options for edge protection and automatic alignment. |
Robotic Loader/Unloader | FANUC M-10iA Series | High-speed robotic system for loading and unloading PCBs, with a payload capacity of up to 10 kg and a reach of up to 1,420 mm. |
Shuttle System | Pemtron PSS-6000 | Multi-level shuttle system for transporting PCBs between different sections of a manufacturing facility, with a capacity of up to 6,000 boards per hour. |
Frequently Asked Questions (FAQ)
-
Q: What is the difference between a magazine loader and a conveyor system?
A: A magazine loader is used to transfer PCBs between magazines and conveyor systems, while a conveyor system is used to transport PCBs between different stages of the manufacturing process. -
Q: How do I determine the appropriate capacity for PCB loading and unloading equipment?
A: The appropriate capacity should be based on the anticipated production volume and the specific requirements of the manufacturing process. It’s important to select equipment that can handle the expected throughput without causing bottlenecks or delays. -
Q: Can PCB loading and unloading equipment be customized for specific PCB designs?
A: Yes, many equipment suppliers offer customization options to accommodate specific PCB sizes, shapes, and thicknesses. It’s important to discuss these requirements with the supplier to ensure the equipment can handle the specific boards being manufactured. -
Q: How can I ensure the safety of workers when using PCB loading and unloading equipment?
A: Safety should be a top priority when selecting and using PCB loading and unloading equipment. Look for equipment with built-in safety features, such as sensors and emergency stop buttons, and ensure that workers are properly trained on the safe operation of the equipment. -
Q: What should I consider when integrating new PCB loading and unloading equipment with existing systems?
A: When integrating new equipment with existing systems, it’s important to ensure compatibility and avoid disruptions to production flow. Consider factors such as communication protocols, physical dimensions, and power requirements, and work closely with the equipment supplier to ensure a smooth integration process.
Conclusion
PCB loading and unloading equipment is an essential component of the PCB manufacturing process, enabling efficient and accurate handling of boards throughout production. By selecting the right equipment for the specific requirements of a manufacturing facility, manufacturers can improve efficiency, reduce costs, and ensure consistent quality.
As technology continues to advance, new opportunities arise for further optimization of PCB loading and unloading processes. By staying up-to-date with the latest developments and working closely with equipment suppliers, manufacturers can position themselves for success in an increasingly competitive industry.
0 Comments