What is PCB Insulation?
PCB insulation refers to the process of applying a non-conductive material to specific areas of a printed circuit board to prevent electrical current from flowing between adjacent conductors, such as traces, pads, and vias. This insulating layer acts as a barrier, ensuring that the electrical signals travel only through the intended paths, thus preventing short circuits and signal interference.
The Importance of PCB Insulation
PCB insulation plays a vital role in the overall performance and reliability of electronic devices. Here are some key reasons why PCB insulation is essential:
-
Preventing Short Circuits: By separating conductive elements on the PCB, insulation prevents unintended electrical connections, known as short circuits, which can cause device malfunction or permanent damage.
-
Reducing Electromagnetic Interference (EMI): Proper insulation helps minimize the effects of EMI, which can cause signal distortion and compromise the device’s performance. Insulation materials with good dielectric properties can absorb or reflect electromagnetic waves, reducing their impact on the PCB.
-
Protecting Against Environmental Factors: PCB insulation provides a barrier against moisture, dust, chemicals, and extreme temperatures, which can degrade the PCB’s performance and lifespan. Insulation materials with high resistance to these factors ensure the PCB remains protected in various operating conditions.
-
Improving Signal Integrity: Insulation materials with low dielectric constants and dissipation factors help maintain signal integrity by reducing signal loss, cross-talk, and impedance mismatch. This is particularly important in high-frequency applications where signal quality is critical.
-
Enhancing Mechanical Strength: Some insulation materials, such as Conformal Coatings, can provide additional mechanical support to the PCB, protecting it from vibrations, shocks, and physical damage during handling and operation.
Types of PCB Insulation
There are several types of PCB insulation, each with its own characteristics and applications. The most common types include:
Solder Mask
Solder mask, also known as solder resist, is a thin layer of polymer applied to the copper traces on a PCB. It serves two primary purposes: insulation and protection. The solder mask covers the copper traces, leaving only the exposed pads and vias for soldering components. This selective coverage prevents solder bridges and short circuits during the soldering process.
Solder mask is available in various colors, with green being the most common. Other colors, such as red, blue, yellow, and black, are used for specific applications or to improve the PCB’s aesthetics.
Conformal Coating
Conformal coating is a type of insulation that involves applying a thin, protective layer over the entire PCB Assembly. This coating conforms to the PCB’s surface, providing insulation, environmental protection, and mechanical support. Conformal coatings are typically applied after the components have been soldered onto the PCB.
There are several types of conformal coatings, each with its own properties and advantages:
-
Acrylic: Acrylic conformal coatings offer excellent moisture and fungus resistance, as well as good dielectric properties. They are easy to apply and remove, making them suitable for PCB Repairs and rework.
-
Silicone: Silicone conformal coatings provide superior protection against extreme temperatures, humidity, and UV radiation. They are highly flexible and have good dielectric properties, making them ideal for applications exposed to thermal cycling or vibrations.
-
Polyurethane: Polyurethane conformal coatings offer excellent chemical resistance and mechanical strength. They provide good protection against abrasion, moisture, and solvents, making them suitable for harsh industrial environments.
-
Epoxy: Epoxy conformal coatings provide the highest level of protection against moisture, chemicals, and abrasion. They have excellent adhesion and durability, but are more difficult to apply and remove compared to other coatings.
-
Parylene: Parylene conformal coatings are applied through a vapor deposition process, resulting in a thin, uniform, and pinhole-free layer. They offer exceptional moisture and chemical resistance, as well as excellent dielectric properties. Parylene coatings are often used in medical and aerospace applications.
Potting and Encapsulation
Potting and encapsulation are methods of insulating and protecting PCBs by completely encasing them in a solid compound, such as epoxy, silicone, or polyurethane. This process provides the highest level of protection against environmental factors, mechanical stress, and tampering.
Potting involves filling a container or housing with the PCB assembly and then pouring the insulating compound over it. Encapsulation, on the other hand, involves directly molding the insulating compound around the PCB assembly.
Potting and encapsulation are commonly used in applications exposed to extreme conditions, such as outdoor electronics, underwater devices, and high-voltage systems.
PCB Insulation Materials
The choice of insulation material depends on the specific application, environmental conditions, and performance requirements of the PCB. Some common PCB insulation materials include:
FR-4
FR-4 (Flame Retardant 4) is the most widely used PCB substrate material. It is a composite material made of woven fiberglass cloth impregnated with an epoxy resin. FR-4 offers good mechanical strength, dimensional stability, and dielectric properties, making it suitable for a wide range of applications.
Polyimide
Polyimide is a high-performance polymer used in PCB substrates for applications requiring high temperature resistance and mechanical stability. It has excellent dielectric properties and can withstand temperatures up to 260°C, making it ideal for aerospace, automotive, and military applications.
PTFE (Teflon)
PTFE (Polytetrafluoroethylene), commonly known as Teflon, is a fluoropolymer with outstanding dielectric properties, low dissipation factor, and high temperature resistance. PTFE-based PCB substrates are used in high-frequency applications, such as radar systems and wireless communication devices.
Ceramic
Ceramic PCB substrates, such as alumina and beryllia, offer excellent thermal conductivity, high dielectric strength, and low dielectric loss. They are used in high-power applications, such as power electronics and LED lighting, where efficient heat dissipation is critical.
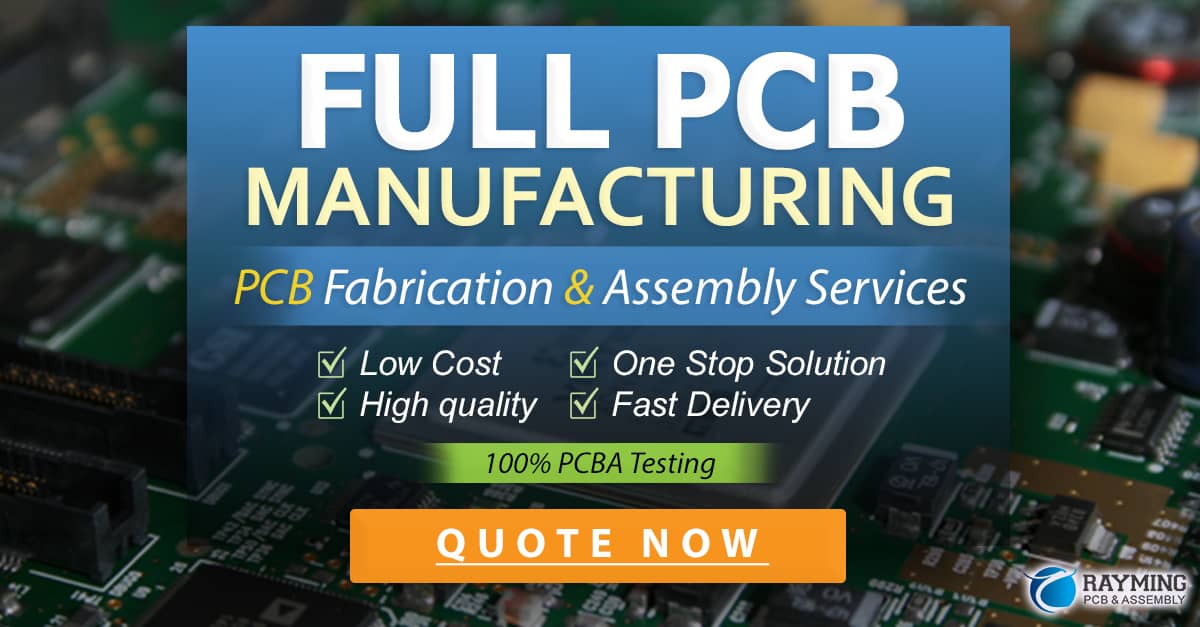
PCB Insulation Application Methods
The application method for PCB insulation depends on the type of insulation material and the specific requirements of the PCB. Some common application methods include:
Screen Printing
Screen printing is the most common method for applying solder mask to PCBs. A stencil with the desired pattern is placed over the PCB, and the solder mask ink is forced through the openings using a squeegee. The PCB is then cured to harden the solder mask.
Dip Coating
Dip coating is a simple and cost-effective method for applying conformal coatings to PCBs. The PCB assembly is dipped into a tank containing the liquid coating material, which adheres to the surface of the PCB. The excess coating is allowed to drip off, and the PCB is then cured.
Spray Coating
Spray coating involves applying the conformal coating material using a spray gun. This method allows for more precise control over the coating thickness and can be automated for high-volume production. The PCB is typically placed in a ventilated enclosure during spraying and then cured.
Brush Coating
Brush coating is a manual method for applying conformal coatings to specific areas of the PCB. A brush is dipped into the coating material and then used to apply the coating to the desired areas. This method is suitable for small-scale production or touch-up work.
Vacuum Potting
Vacuum potting is a process used for potting and encapsulation. The PCB assembly is placed in a mold, and the potting compound is poured over it. The mold is then placed in a vacuum chamber to remove any air bubbles trapped in the compound. This ensures a void-free insulation layer with excellent adhesion to the PCB.
PCB Insulation Testing
To ensure the effectiveness and reliability of PCB insulation, various tests are performed during and after the manufacturing process. Some common PCB insulation tests include:
Dielectric Withstanding Voltage (DWV) Test
The DWV test, also known as the high potential (HiPot) test, involves applying a high voltage between the conductive elements of the PCB to ensure that the insulation can withstand the specified voltage without breaking down. This test helps detect any weak spots or pinholes in the insulation layer.
Insulation Resistance (IR) Test
The IR test measures the resistance between the conductive elements of the PCB to ensure that the insulation provides sufficient electrical resistance. A high resistance value indicates good insulation quality, while a low value may indicate the presence of contaminants or moisture.
Thermal Shock Test
The thermal shock test exposes the PCB to rapid temperature changes to evaluate the insulation’s ability to withstand thermal stress. The PCB is subjected to alternating cycles of high and low temperatures, and any cracks, delamination, or other insulation failures are recorded.
Humidity Test
The humidity test assesses the insulation’s resistance to moisture. The PCB is placed in a controlled environment with high humidity levels for an extended period. Any deterioration in the insulation’s properties or the presence of corrosion is noted.
Salt Spray Test
The salt spray test evaluates the insulation’s resistance to corrosion in a salt-laden environment. The PCB is exposed to a fine mist of salt solution in a controlled chamber. Any signs of corrosion or degradation in the insulation are recorded.
Best Practices for PCB Insulation
To ensure optimal performance and reliability of PCB insulation, consider the following best practices:
-
Choose the Right Insulation Material: Select the insulation material based on the specific requirements of your application, such as temperature range, dielectric properties, chemical resistance, and mechanical strength.
-
Follow Manufacturer’s Guidelines: Adhere to the manufacturer’s recommendations for storage, handling, application, and curing of the insulation material to ensure the best results.
-
Ensure Proper Surface Preparation: Clean the PCB surface thoroughly before applying the insulation material to ensure good adhesion and avoid contamination.
-
Control the Insulation Thickness: Apply the insulation material in a uniform thickness, as specified by the design requirements. Too thin a layer may compromise insulation performance, while too thick a layer may affect the PCB’s dimensional tolerances and heat dissipation.
-
Perform Regular Inspections: Conduct visual inspections and perform periodic insulation tests to monitor the condition of the PCB insulation over time. This helps detect any degradation or failures early, allowing for timely maintenance or repairs.
-
Consider Environmental Factors: Take into account the environmental conditions the PCB will be exposed to, such as temperature, humidity, and chemical exposure, when selecting the insulation material and application method.
-
Design for Manufacturability: Ensure that the PCB design is compatible with the chosen insulation method. Consider factors such as component spacing, pad sizes, and solder mask openings to facilitate the insulation application process.
Frequently Asked Questions (FAQ)
-
Q: What is the difference between a solder mask and a conformal coating?
A: A solder mask is a thin layer of polymer applied to the copper traces on a PCB, leaving only the exposed pads and vias for soldering components. It primarily serves to prevent solder bridges and short circuits during the soldering process. On the other hand, a conformal coating is a protective layer applied over the entire PCB assembly after soldering. It provides insulation, environmental protection, and mechanical support to the PCB. -
Q: Can PCB insulation materials be removed?
A: Some PCB insulation materials, such as acrylic conformal coatings, can be easily removed using solvents for rework or repair purposes. However, other materials, like epoxy potting compounds, are more difficult to remove and may require mechanical methods or specialized solvents. -
Q: How do I choose the right insulation material for my PCB?
A: The choice of insulation material depends on several factors, including the operating temperature range, environmental conditions, dielectric properties, and mechanical requirements of your application. Consider the specific needs of your PCB and consult with insulation material manufacturers or PCB fabrication experts to select the most suitable material. -
Q: Can PCB insulation affect the thermal performance of the board?
A: Yes, PCB insulation materials can impact the thermal performance of the board. Some insulation materials, such as ceramic substrates, have high thermal conductivity and can help dissipate heat more effectively. However, thicker insulation layers or materials with low thermal conductivity can impede heat transfer and lead to higher operating temperatures. It’s important to consider the thermal requirements of your application when selecting the insulation material and thickness. -
Q: How often should I perform insulation testing on my PCBs?
A: The frequency of insulation testing depends on the criticality of the application, the environmental conditions, and the expected lifespan of the PCB. For high-reliability applications, such as aerospace or medical devices, insulation testing may be performed more frequently, such as during production, qualification, and periodic maintenance. For less critical applications, testing may be done during initial production and then on an as-needed basis. It’s important to establish an appropriate testing schedule based on the specific requirements of your application and industry standards.
Conclusion
PCB insulation is a critical aspect of PCB production that ensures the proper functioning, reliability, and longevity of electronic devices. By understanding the importance of PCB insulation, the various types and materials available, and the best practices for application and testing, designers and manufacturers can make informed decisions to optimize the performance of their PCBs.
As technology advances and the demand for high-performance electronics grows, the role of PCB insulation will continue to be crucial. Staying up-to-date with the latest insulation materials, techniques, and standards will help companies produce PCBs that meet the evolving needs of various industries, from consumer electronics to aerospace and beyond.
Insulation Type | Advantages | Disadvantages |
---|---|---|
Solder Mask | – Prevents solder bridges and short circuits – Available in various colors – Easy to apply and remove |
– Limited environmental protection – Does not provide mechanical support |
Conformal Coating | – Provides environmental protection – Offers mechanical support – Various material options (acrylic, silicone, etc.) |
– Requires additional processing steps – Can affect PCB dimensions and weight |
Potting and Encapsulation | – Highest level of protection against environmental factors and mechanical stress – Prevents tampering |
– Difficult to remove for rework or repair – Can impact heat dissipation – Increases PCB weight and size |
By selecting the appropriate insulation type and material based on the specific requirements of the application, PCB designers and manufacturers can ensure optimal performance, reliability, and longevity of their electronic devices.
0 Comments