Introduction to PCB Etching with Ferric Chloride
Printed circuit board (PCB) etching is a crucial process in electronics manufacturing that involves removing unwanted copper from a PCB Substrate to create the desired circuit pattern. One of the most commonly used etchants for this process is ferric chloride (FeCl3), a chemical compound known for its ability to dissolve copper effectively. In this comprehensive guide, we will explore various tips and techniques to optimize your PCB etching process using ferric chloride, ensuring high-quality results and minimizing potential issues.
Understanding Ferric Chloride
Ferric chloride is an ionic compound with the chemical formula FeCl3. It is a dark brown, hygroscopic solid that readily absorbs moisture from the air. When dissolved in water, ferric chloride forms a yellowish-brown solution that is highly corrosive to metals, particularly copper. This property makes it an ideal choice for etching copper-clad PCBs.
Advantages of Using Ferric Chloride for PCB Etching
- Effective copper removal: Ferric chloride is known for its ability to dissolve copper quickly and evenly, making it suitable for etching fine details and intricate circuit patterns.
- Readily available: Ferric chloride is widely used in the electronics industry and can be easily purchased from various suppliers.
- Relatively safe: Compared to other etchants like ammonium persulfate or hydrochloric acid, ferric chloride is considered safer to handle, although proper safety precautions should still be followed.
Preparing the Ferric Chloride Solution
Choosing the Right Concentration
The concentration of the ferric chloride solution plays a crucial role in the etching process. A higher concentration will result in faster etching, but it may also lead to over-etching and loss of fine details. On the other hand, a lower concentration will slow down the etching process but provide better control and accuracy. A commonly used concentration for PCB etching is around 35-45% by weight.
Mixing the Solution
To prepare the ferric chloride solution, follow these steps:
1. Wear appropriate personal protective equipment (PPE) such as gloves, safety glasses, and an apron.
2. In a non-metallic container, add the desired amount of distilled or deionized water.
3. Slowly add the ferric chloride crystals to the water while stirring gently to avoid splashing.
4. Continue stirring until the ferric chloride is completely dissolved and the solution is homogeneous.
5. Allow the solution to cool down to room temperature before use.
Ferric Chloride Concentration | Water (ml) | Ferric Chloride (g) |
---|---|---|
30% | 700 | 300 |
40% | 600 | 400 |
50% | 500 | 500 |
Table 1: Ferric Chloride Solution Mixing Ratios
Storage and Handling
Ferric chloride solutions should be stored in a cool, dry place away from direct sunlight. Always use non-metallic containers, such as glass or plastic, to prevent contamination and unwanted reactions. Properly label the container with the concentration and date of preparation. When handling ferric chloride, take necessary safety precautions and work in a well-ventilated area.
Optimizing the Etching Process
Temperature Control
The temperature of the ferric chloride solution significantly affects the etching rate and quality. Higher temperatures accelerate the etching process but may lead to uneven etching or over-etching. Lower temperatures slow down the reaction but provide better control. The optimal temperature range for PCB etching with ferric chloride is between 40-50°C (104-122°F).
To maintain a consistent temperature during etching, consider using a temperature-controlled water bath or a dedicated PCB etching tank with built-in heating elements. Regularly monitor the solution temperature using a thermometer and adjust the heating as necessary.
Agitation
Proper agitation of the ferric chloride solution ensures even etching across the PCB surface and prevents the buildup of etch byproducts. There are several methods to agitate the solution:
- Manual agitation: Gently rock or swirl the container holding the PCB and ferric chloride solution at regular intervals.
- Bubble agitation: Use an aquarium air pump and an air stone to create a steady stream of bubbles in the solution, promoting circulation.
- Magnetic stirring: Place a magnetic stir bar in the etching container and use a magnetic stirrer to continuously mix the solution.
- Spray etching: Use a pump to spray the ferric chloride solution onto the PCB surface, ensuring even coverage and constant solution renewal.
Etching Time
The etching time depends on various factors such as the ferric chloride concentration, temperature, agitation method, and copper thickness. As a general guideline, a 35-45% ferric chloride solution at 40-50°C with proper agitation can etch a standard 1 oz Copper PCB in 10-20 minutes.
To determine the optimal etching time for your specific setup, it’s recommended to conduct test etches on scrap PCBs and closely monitor the progress. Remove the PCB from the solution periodically to check the etching status and avoid over-etching.
Post-Etching Cleaning
After the etching process is complete, promptly remove the PCB from the ferric chloride solution and rinse it thoroughly with water. Use a soft brush to remove any remaining etch resist or debris from the surface. For stubborn residues, you can use a gentle abrasive cleaner or a commercial PCB cleaner.
Once the PCB is clean, dry it with compressed air or a lint-free cloth. Inspect the etched pattern for any defects or irregularities, and make necessary corrections if needed.
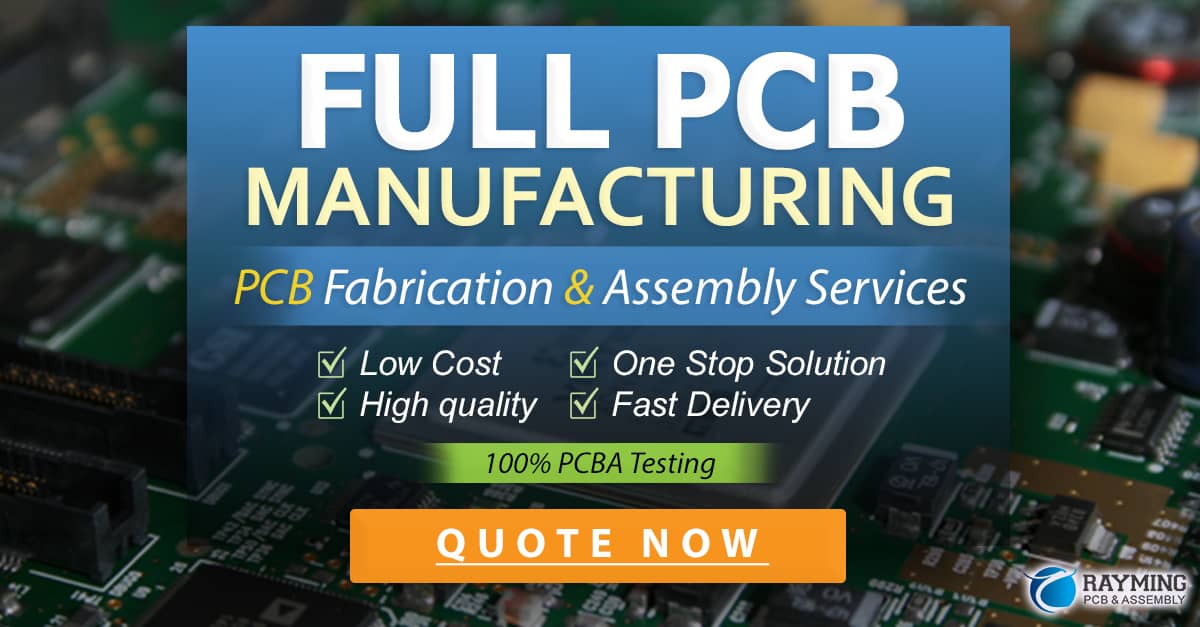
Troubleshooting Common Issues
Under-Etching
Under-etching occurs when the copper is not completely removed from the unwanted areas, leaving behind thin traces or residues. This can be caused by:
– Insufficient etching time
– Low ferric chloride concentration
– Inadequate agitation
– Low solution temperature
To resolve under-etching, increase the etching time, check the ferric chloride concentration, improve agitation, or raise the solution temperature within the recommended range.
Over-Etching
Over-etching happens when the ferric chloride solution removes too much copper, causing the traces to become thinner or completely dissolve. Over-etching can be caused by:
– Excessive etching time
– High ferric chloride concentration
– Aggressive agitation
– High solution temperature
To prevent over-etching, closely monitor the etching progress, reduce the etching time, dilute the ferric chloride solution, or lower the solution temperature.
Uneven Etching
Uneven etching results in inconsistent copper removal across the PCB surface, leading to variations in trace widths or incomplete etching in certain areas. Uneven etching can be caused by:
– Poor solution agitation
– Non-uniform temperature distribution
– Incorrect placement of the PCB in the solution
– Contaminated or exhausted ferric chloride solution
To achieve even etching, ensure proper agitation, maintain a consistent temperature, position the PCB correctly in the solution, and replace the ferric chloride solution when it becomes contaminated or exhausted.
Disposing of Ferric Chloride
Proper disposal of used ferric chloride solution is crucial to prevent environmental contamination and comply with local regulations. Follow these steps for safe disposal:
- Neutralize the ferric chloride solution by slowly adding a base, such as sodium bicarbonate or sodium hydroxide, until the pH reaches 7.0.
- Filter the neutralized solution to remove any solid precipitates.
- Contact your local waste management authority for guidance on disposing of the filtered solution and solid waste.
- Never pour ferric chloride solution down the drain or discard it in regular trash.
Frequently Asked Questions (FAQ)
1. Can I reuse ferric chloride solution?
Yes, ferric chloride solution can be reused multiple times until it becomes saturated with copper and loses its etching effectiveness. To extend the solution’s life, you can regenerate it by adding fresh ferric chloride and adjusting the concentration.
2. How do I know when the ferric chloride solution is exhausted?
An exhausted ferric chloride solution will have a dark green color and will etch significantly slower than a fresh solution. You may also notice a layer of copper sludge at the bottom of the container. When these signs appear, it’s time to replace or regenerate the solution.
3. Can I etch multiple PCBs simultaneously in the same solution?
Yes, you can etch multiple PCBs in the same ferric chloride solution, provided there is enough space between the boards to allow proper solution circulation. However, keep in mind that etching multiple PCBs will deplete the solution more quickly, so you may need to adjust the etching time or replace the solution more frequently.
4. How do I store unused ferric chloride solution?
Unused ferric chloride solution should be stored in a tightly sealed, non-metallic container in a cool, dry place away from direct sunlight. Avoid storing the solution near heat sources or incompatible materials. Always label the container clearly with the contents and safety information.
5. What safety precautions should I take when working with ferric chloride?
When handling ferric chloride, always wear appropriate PPE, including gloves, safety glasses, and an apron. Work in a well-ventilated area and avoid inhaling the fumes. In case of skin contact, rinse the affected area thoroughly with water. If ingested or inhaled, seek medical attention immediately.
Conclusion
PCB etching with ferric chloride is a reliable and effective method for creating high-quality circuit boards. By understanding the properties of ferric chloride, preparing the solution correctly, optimizing the etching process, and following proper safety and disposal procedures, you can achieve excellent etching results consistently.
Remember to experiment with different concentrations, temperatures, and agitation methods to find the optimal settings for your specific PCB Designs. Regularly monitor the etching progress, address any issues promptly, and maintain a clean and organized workspace.
With practice and attention to detail, you can master the art of PCB etching with ferric chloride and bring your electronic projects to life with precision and reliability.
0 Comments