Introduction to PCB Quality and Failure Analysis
Printed Circuit Boards (PCBs) are the backbone of modern electronic devices, connecting various components to form complex circuits. The quality of PCBs is crucial for the proper functioning and reliability of these devices. PCB failure can lead to malfunctions, safety hazards, and costly repairs. To ensure the production of high-quality PCBs, manufacturers employ various quality control measures, including PCB failure analysis.
PCB failure analysis is a systematic approach to identifying the root causes of PCB Failures and implementing corrective actions to prevent future occurrences. By conducting thorough investigations into PCB failures, manufacturers can improve their processes, enhance product reliability, and ultimately, assure customers of the good quality of their PCBs.
The Importance of PCB Quality
PCB quality is essential for several reasons:
- Reliability: High-quality PCBs ensure the reliable performance of electronic devices, reducing the risk of malfunctions and failures.
- Safety: Poor-quality PCBs can pose safety hazards, such as electrical shocks, fires, or explosions, endangering users and the environment.
- Cost-effectiveness: Investing in quality control measures and failure analysis helps manufacturers avoid costly repairs, replacements, and recalls.
- Reputation: Consistently delivering high-quality PCBs enhances a manufacturer’s reputation, leading to increased customer satisfaction and loyalty.
Common Causes of PCB Failures
To effectively conduct PCB failure analysis, it is essential to understand the common causes of PCB failures. These can be categorized into design-related, manufacturing-related, and environmental factors.
Design-Related Failures
- Inadequate design for manufacturability (DFM): Designs that do not adhere to DFM guidelines can lead to manufacturing challenges and defects.
- Incorrect component selection: Using components that are not suitable for the intended application or environment can cause failures.
- Insufficient thermal management: Poor thermal design can result in overheating and component damage.
- Inadequate electrical clearances: Insufficient spacing between conductive elements can lead to short circuits and electrical failures.
Manufacturing-Related Failures
- Soldering defects: Improper soldering techniques, such as cold joints, bridging, or insufficient solder, can cause connection issues and failures.
- Contamination: Foreign particles, such as dust, dirt, or chemicals, can contaminate the PCB during manufacturing, leading to defects and failures.
- Mechanical damage: Mishandling, improper storage, or transportation can cause physical damage to the PCB, such as cracks, delamination, or broken components.
- Incorrect component placement: Misaligned or incorrectly placed components can result in functional failures and mechanical stress.
Environmental Factors
- Temperature and humidity: Exposure to extreme temperatures or humidity levels can cause component degradation and PCB failures.
- Vibration and shock: Excessive vibration or shock can lead to mechanical damage and connection issues.
- Electromagnetic interference (EMI): Exposure to EMI can disrupt the proper functioning of the PCB and its components.
- Chemical exposure: Exposure to corrosive or reactive chemicals can degrade the PCB and its components over time.
PCB Failure Analysis Techniques
To identify the root causes of PCB failures, manufacturers employ various failure analysis techniques. These techniques can be categorized into non-destructive and destructive methods.
Non-Destructive Techniques
- Visual inspection: A thorough visual examination of the PCB using magnification tools can reveal surface defects, such as cracks, contamination, or soldering issues.
- X-ray inspection: X-ray imaging allows for the examination of internal structures, such as vias, buried components, and solder joints, without damaging the PCB.
- Automated optical inspection (AOI): AOI systems use high-resolution cameras and image processing algorithms to detect surface defects and component placement issues.
- Thermal imaging: Infrared cameras can detect hot spots and thermal anomalies on the PCB, indicating potential component failures or design issues.
Destructive Techniques
- Cross-sectioning: Cutting the PCB to examine its internal structure can reveal manufacturing defects, such as voids, delamination, or insufficient plating.
- Decapsulation: Removing the encapsulation material from components allows for the examination of die and wire bond integrity.
- Scanning electron microscopy (SEM): SEM provides high-magnification images of PCB surfaces and cross-sections, enabling the detection of microscopic defects and material composition analysis.
- Energy-dispersive X-ray spectroscopy (EDX): EDX is used in conjunction with SEM to identify the elemental composition of materials, helping to detect contamination or material defects.
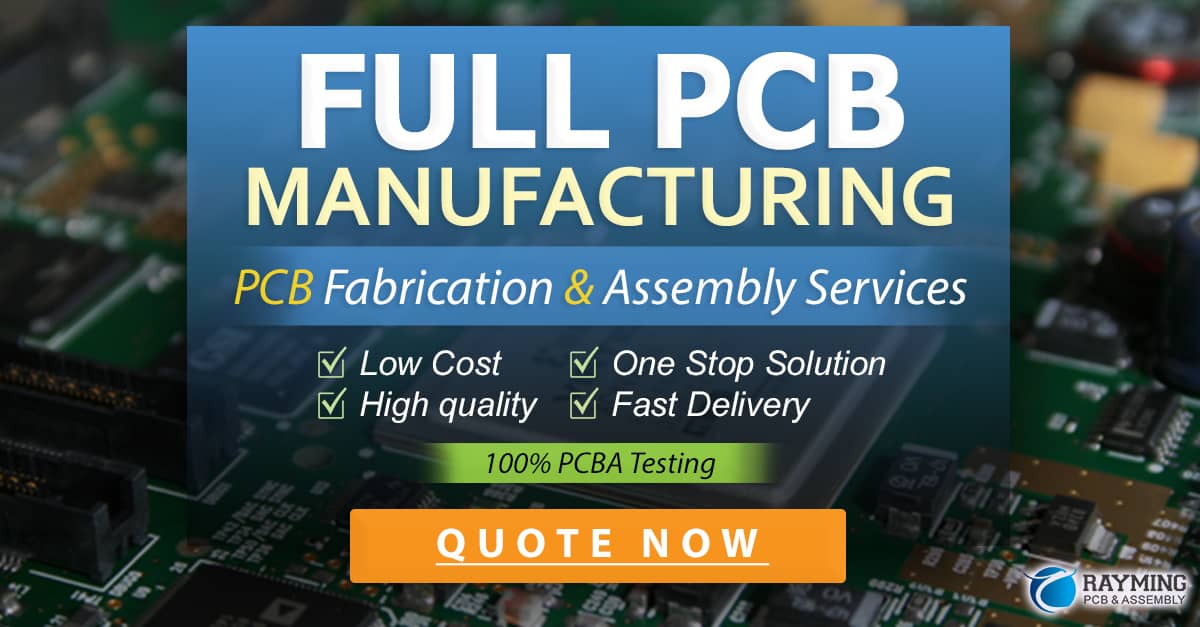
PCB Failure Analysis Process
A typical PCB failure analysis process involves the following steps:
- Failure identification: The first step is to identify the specific failure mode and gather relevant information, such as application conditions, failure symptoms, and frequency of occurrence.
- Visual inspection: A thorough visual examination of the PCB is conducted to identify any obvious defects or anomalies.
- Non-destructive testing: Appropriate non-destructive techniques, such as X-ray inspection or thermal imaging, are employed to gather additional information about the failure.
- Destructive testing: If necessary, destructive techniques, such as cross-sectioning or decapsulation, are used to examine the internal structure of the PCB and its components.
- Data analysis: The data collected from the various testing methods is analyzed to identify the root cause of the failure.
- Corrective action: Based on the root cause analysis, corrective actions are implemented to address the issue and prevent future occurrences.
- Validation: The effectiveness of the corrective actions is validated through further testing and monitoring of the PCB production process.
Step | Purpose | Techniques |
---|---|---|
Failure Identification | Identify specific failure mode and gather relevant information | – Application conditions – Failure symptoms – Frequency of occurrence |
Visual Inspection | Identify obvious defects or anomalies | – Magnification tools – Microscopy |
Non-Destructive Testing | Gather additional information about the failure without damaging the PCB | – X-ray inspection – Automated optical inspection (AOI) – Thermal imaging |
Destructive Testing | Examine the internal structure of the PCB and its components | – Cross-sectioning – Decapsulation – Scanning electron microscopy (SEM) |
Data Analysis | Identify the root cause of the failure | – Analyzing data from testing methods |
Corrective Action | Address the issue and prevent future occurrences | – Implementing changes based on root cause analysis |
Validation | Validate the effectiveness of the corrective actions | – Further testing – Monitoring of PCB production process |
Benefits of PCB Failure Analysis
Conducting thorough PCB failure analysis offers several benefits to manufacturers and customers:
- Improved reliability: By identifying and addressing the root causes of failures, manufacturers can improve the overall reliability of their PCBs, reducing the risk of malfunctions and failures in the field.
- Enhanced safety: Failure analysis helps identify potential safety hazards, allowing manufacturers to implement necessary changes to ensure the safety of users and the environment.
- Cost savings: Detecting and addressing failures early in the production process can help manufacturers avoid costly repairs, replacements, and recalls.
- Increased customer satisfaction: Consistently delivering high-quality PCBs that meet customer expectations leads to increased customer satisfaction and loyalty.
- Continuous improvement: PCB failure analysis provides valuable insights into the design and manufacturing processes, enabling manufacturers to continuously improve their practices and stay competitive in the market.
Case Studies
Case Study 1: Intermittent Connection Failure
A customer reported intermittent connection issues with a PCB used in a medical device. The failure analysis process involved the following steps:
- Visual inspection revealed no obvious defects.
- X-ray inspection showed a potential issue with a ball grid array (BGA) component.
- Cross-sectioning of the BGA component revealed insufficient solder joint formation.
- The root cause was identified as incorrect reflow soldering parameters.
- Corrective actions included adjusting the reflow profile and implementing stricter process controls.
- Validation testing confirmed the effectiveness of the corrective actions, and the issue was resolved.
Case Study 2: Overheating Component
An Automotive PCB experienced frequent component failures due to overheating. The failure analysis process involved the following steps:
- Thermal imaging identified a specific component consistently running at higher temperatures than expected.
- Visual inspection and X-ray analysis showed no defects in the component or its soldering.
- Reviewing the design files revealed that the component was undersized for the application’s power requirements.
- The root cause was identified as an inadequate component selection during the design phase.
- Corrective actions included updating the design with a suitable component and reviewing the design process to prevent similar issues in the future.
- Validation testing confirmed the effectiveness of the corrective actions, and the overheating issue was resolved.
Frequently Asked Questions (FAQ)
-
Q: How long does a typical PCB failure analysis take?
A: The duration of a PCB failure analysis depends on the complexity of the issue and the techniques required. Simple cases may be resolved within a few days, while more complex investigations can take several weeks. -
Q: Can PCB failure analysis be performed on any type of PCB?
A: Yes, PCB failure analysis can be performed on various types of PCBs, including rigid, flexible, and rigid-flex PCBs, as well as single-layer and multi-layer boards. -
Q: Is PCB failure analysis expensive?
A: The cost of PCB failure analysis varies depending on the techniques employed and the time required to complete the investigation. However, the cost of failure analysis is often justified by the potential savings from avoiding future failures and improving overall product quality. -
Q: Can PCB failure analysis help improve the design of future products?
A: Yes, the insights gained from PCB failure analysis can be used to inform the design of future products, helping to avoid similar issues and improve overall product reliability. -
Q: What should I do if I suspect a PCB failure in my product?
A: If you suspect a PCB failure in your product, contact the manufacturer or a specialized PCB failure analysis service provider. They will guide you through the process of submitting the affected PCBs for analysis and provide a detailed report of their findings and recommendations.
Conclusion
PCB failure analysis is a critical aspect of ensuring the production of high-quality PCBs. By systematically investigating the root causes of failures and implementing corrective actions, manufacturers can improve the reliability, safety, and cost-effectiveness of their products. A well-structured failure analysis process, employing a combination of non-destructive and destructive techniques, enables manufacturers to identify design, manufacturing, and environmental issues that may lead to PCB failures.
Investing in PCB failure analysis not only helps resolve immediate issues but also contributes to the continuous improvement of PCB design and manufacturing processes. By leveraging the insights gained from failure analysis, manufacturers can enhance their competitive edge, increase customer satisfaction, and build a reputation for delivering high-quality, reliable PCBs.
As the demand for electronic devices continues to grow, the importance of PCB quality and failure analysis will only increase. Manufacturers who prioritize these aspects will be well-positioned to meet the evolving needs of their customers and maintain a strong presence in the market.
0 Comments