What is PCB Engineering?
PCB engineering, or printed circuit board engineering, is the process of designing and creating circuit boards that are used in a wide range of electronic devices. From smartphones and laptops to medical equipment and aerospace technology, PCBs are an essential component of modern electronics.
PCB engineers are responsible for designing and laying out the circuit board, selecting the appropriate components, and ensuring that the board meets all necessary specifications and standards. This requires a deep understanding of electrical engineering principles, as well as proficiency in specialized software tools used for PCB design.
The Role of a PCB Engineer
A PCB engineer plays a crucial role in the development of electronic products. They work closely with other members of the design team, including electrical engineers, mechanical engineers, and product managers, to ensure that the PCB meets all functional and performance requirements.
Some of the key responsibilities of a PCB engineer include:
- Designing the circuit schematic and layout
- Selecting appropriate components and materials
- Conducting simulations and testing to verify the design
- Collaborating with manufacturing teams to ensure proper fabrication and assembly
- Troubleshooting and resolving any issues that arise during the design or manufacturing process
Skills and Qualifications
To become a successful PCB engineer, one must possess a combination of technical skills and practical experience. Some of the essential skills and qualifications include:
- Bachelor’s degree in electrical engineering or a related field
- Proficiency in PCB design software such as Altium Designer, Eagle, or KiCad
- Knowledge of electronic components and their characteristics
- Understanding of signal integrity, power integrity, and electromagnetic compatibility (EMC) principles
- Familiarity with PCB manufacturing processes and standards
- Strong problem-solving and communication skills
PCB Design Process
The PCB design process typically consists of several stages, each requiring specific skills and tools. Let’s take a closer look at each stage:
1. Schematic Design
The first step in PCB design is creating the schematic diagram. This involves defining the electrical connections between components and ensuring that the circuit functions as intended. PCB engineers use schematic capture software to create the diagram, which serves as a blueprint for the physical layout of the board.
2. Component Selection
Once the schematic is complete, the next step is to select the appropriate components for the design. This includes choosing the right type of resistors, capacitors, inductors, and integrated circuits (ICs) based on their electrical characteristics, package size, and cost. PCB engineers must also consider factors such as power dissipation, thermal management, and signal integrity when selecting components.
3. PCB Layout
With the schematic and components in place, the PCB engineer can begin laying out the physical board. This involves arranging the components on the board and routing the electrical connections between them. The goal is to create a compact, efficient layout that minimizes signal interference and ensures proper functionality.
PCB layout software, such as Altium Designer or Eagle, is used to create the physical design. These tools provide a range of features for placing components, routing traces, and generating manufacturing files.
4. Simulation and Testing
Before sending the PCB design for manufacturing, it is essential to simulate and test the design to verify its functionality and performance. PCB engineers use specialized software tools to conduct signal integrity analysis, power integrity analysis, and electromagnetic compatibility (EMC) simulations.
These simulations help identify potential issues such as signal reflections, crosstalk, and electromagnetic interference (EMI), which can be addressed through design modifications.
5. Manufacturing and Assembly
Once the PCB design has been finalized and tested, it is ready for manufacturing. The PCB engineer generates a set of manufacturing files, including Gerber files and drill files, which are sent to the PCB Fabrication house.
After the PCBs have been fabricated, they are then assembled with the specified components using automated assembly lines or manual soldering techniques. The PCB engineer may work closely with the manufacturing team to ensure that the boards are assembled correctly and meet all quality standards.
Best Practices in PCB Design
To create high-quality, reliable PCBs, engineers must follow a set of best practices throughout the design process. Some of these best practices include:
-
Proper Component Placement: Components should be placed in a logical, organized manner that minimizes the length of traces and reduces signal interference. Critical components, such as clocks and power supplies, should be placed close to their respective circuits to minimize signal degradation.
-
Efficient Routing: Traces should be routed in a way that minimizes signal reflections, crosstalk, and EMI. This can be achieved by using appropriate trace widths, spacing, and shielding techniques. Traces carrying high-speed signals should be routed away from sensitive components to avoid interference.
-
Power and Ground Planes: Using dedicated power and ground planes can help reduce EMI and improve power distribution across the board. These planes should be designed with appropriate clearance and isolation to minimize noise and ensure signal integrity.
-
Thermal Management: Proper thermal management is crucial for ensuring the long-term reliability of PCBs. This involves selecting components with appropriate power ratings, providing adequate cooling, and designing the board layout to minimize heat buildup.
-
Design for Manufacturing (DFM): PCB engineers should design boards with manufacturing in mind, following DFM guidelines to ensure that the board can be easily fabricated and assembled. This includes providing appropriate clearances, using standard component sizes, and avoiding complex geometries that may be difficult to manufacture.
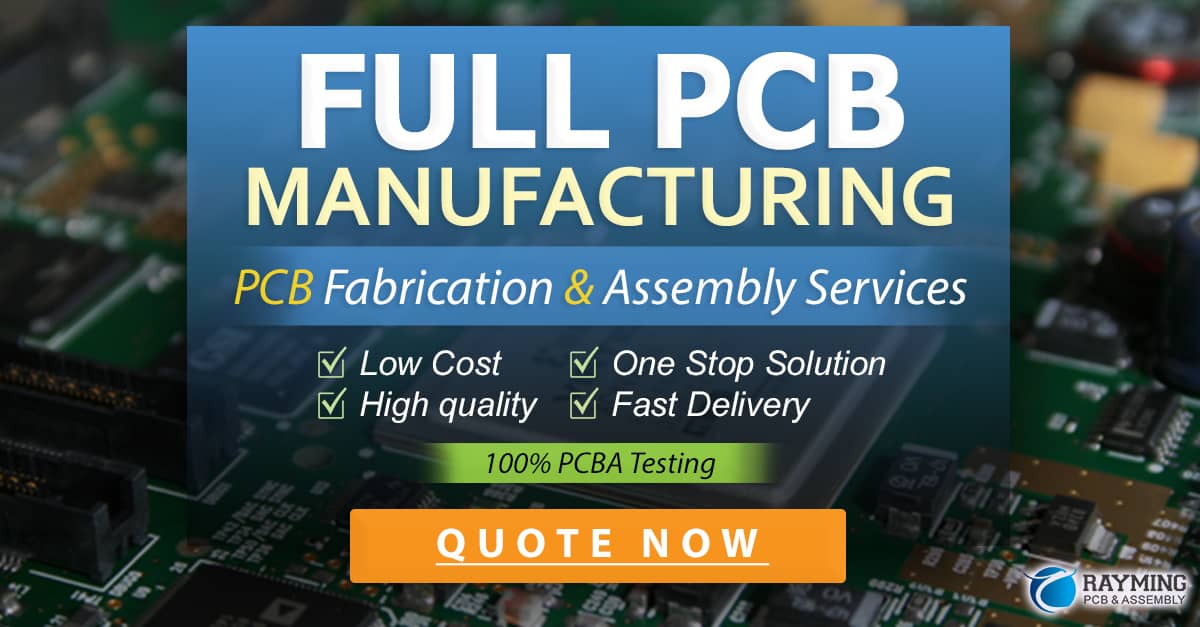
Future Trends in PCB Engineering
As technology continues to advance, PCB engineering must also evolve to keep pace with new challenges and opportunities. Some of the key trends shaping the future of PCB engineering include:
1. Miniaturization
The demand for smaller, more compact electronic devices is driving the need for miniaturized PCBs. This requires PCB engineers to design boards with smaller component packages, tighter tolerances, and higher component densities.
Advanced packaging technologies, such as chip-on-board (COB) and system-in-package (SIP), are becoming increasingly popular for creating compact, high-performance PCBs.
2. High-Speed Design
As data rates continue to increase, PCB engineers must design boards that can handle high-speed signals without compromising signal integrity. This requires a deep understanding of signal propagation, impedance matching, and EMI suppression techniques.
High-speed design often involves the use of advanced materials, such as low-loss dielectrics and high-frequency laminates, to minimize signal attenuation and distortion.
3. Flexible and Rigid-Flex PCBs
Flexible and rigid-Flex PCBs are gaining popularity in applications that require compact, lightweight, and flexible designs. These boards consist of flexible substrates that can be bent or folded to fit into tight spaces or conform to unique shapes.
Designing flexible and Rigid-Flex PCBs requires specialized knowledge of flexible materials, bend radius limitations, and strain relief techniques.
4. 3D Printing
3D printing technology is emerging as a potential game-changer in PCB manufacturing. With 3D printing, it is possible to create complex, three-dimensional PCB structures that would be difficult or impossible to fabricate using traditional methods.
This technology enables the creation of embedded components, conformal antennas, and multi-layer PCBs with intricate geometries. As 3D printing technology advances, it may open up new possibilities for PCB design and manufacturing.
Frequently Asked Questions (FAQ)
- What education is required to become a PCB engineer?
To become a PCB engineer, a bachelor’s degree in electrical engineering or a related field is typically required. Some employers may also require a master’s degree for advanced positions.
- What software tools do PCB engineers use?
PCB engineers use a range of specialized software tools for schematic capture, PCB layout, and simulation. Some of the most popular tools include Altium Designer, Eagle, KiCad, and OrCAD.
- How do PCB engineers ensure signal integrity in high-speed designs?
To ensure signal integrity in high-speed designs, PCB engineers use techniques such as impedance matching, differential signaling, and careful routing of traces. They also use simulation tools to analyze signal behavior and identify potential issues.
- What are some common challenges faced by PCB engineers?
Some common challenges faced by PCB engineers include managing signal integrity, minimizing EMI, ensuring proper thermal management, and designing for manufacturability. They must also stay up-to-date with the latest technologies and design techniques to remain competitive.
- What is the future outlook for PCB engineering?
The demand for PCB engineers is expected to remain strong in the coming years, driven by the growing demand for electronic devices and the increasing complexity of PCB designs. The rise of new technologies, such as 5G, IoT, and autonomous vehicles, is also expected to create new opportunities for PCB engineers.
Conclusion
PCB engineering is a critical skill in the development of modern electronic devices. From designing circuit schematics to laying out physical boards, PCB engineers play a vital role in ensuring that electronic products function reliably and meet all necessary specifications.
To succeed in this field, PCB engineers must possess a combination of technical expertise, practical experience, and problem-solving skills. They must also stay up-to-date with the latest design tools, manufacturing processes, and industry trends.
As technology continues to advance, the role of PCB engineers will become increasingly important in shaping the future of electronics. By following best practices and embracing new technologies, PCB engineers can create innovative, high-performance designs that push the boundaries of what is possible.
Stage | Description | Tools Used |
---|---|---|
Schematic Design | Creating the electrical diagram of the circuit | Schematic capture software (e.g., Eagle, KiCad) |
Component Selection | Choosing appropriate components based on electrical characteristics, package size, and cost | Component databases, datasheets |
PCB Layout | Arranging components and routing connections on the physical board | PCB layout software (e.g., Altium Designer, Eagle) |
Simulation and Testing | Verifying the design’s functionality and performance through simulations | Signal integrity analysis tools, power integrity analysis tools, EMC simulation software |
Manufacturing and Assembly | Fabricating the PCB and assembling it with components | Gerber files, drill files, automated assembly lines, manual soldering techniques |
Table 1: Stages of the PCB Design Process
By following a systematic approach and utilizing the appropriate tools at each stage, PCB engineers can create reliable, high-performance designs that meet the ever-increasing demands of modern electronics.
0 Comments