What is PCB Crosstalk?
PCB crosstalk refers to the unintended electromagnetic coupling between signals on a printed circuit board (PCB). This coupling can cause signals to interfere with each other, leading to signal integrity issues, increased noise, and potential malfunctions in the electronic device.
Crosstalk occurs when the electric or magnetic fields of one signal inadvertently influence another nearby signal. The severity of crosstalk depends on various factors, such as the proximity of the traces, the signal frequencies, the rise and fall times of the signals, and the overall PCB layout.
Types of PCB Crosstalk
There are two main types of PCB crosstalk:
-
Inductive Crosstalk: This type of crosstalk is caused by the magnetic fields generated by current flowing through a conductor. When two traces are close to each other, the magnetic field from one trace can induce a current in the other trace, leading to interference.
-
Capacitive Crosstalk: This type of crosstalk is caused by the electric fields between two conductors. When two traces are close to each other, the electric field between them can cause a change in the voltage level of the adjacent trace, resulting in interference.
Why is PCB Crosstalk a Concern?
PCB crosstalk is a significant concern in modern electronic designs for several reasons:
-
Signal Integrity: Crosstalk can degrade the quality of the signals on the PCB, leading to reduced signal-to-noise ratio (SNR), increased jitter, and potential data errors. This is particularly problematic in high-speed digital systems, where even small amounts of interference can cause significant issues.
-
EMI/EMC Compliance: Crosstalk can contribute to electromagnetic interference (EMI) and make it more difficult for a device to meet electromagnetic compatibility (EMC) regulations. Excessive crosstalk can lead to the radiation of unwanted electromagnetic energy, which can interfere with other electronic devices.
-
Reliability: In severe cases, crosstalk can cause malfunctions or even permanent damage to the electronic components on the PCB. This can reduce the overall reliability of the device and lead to increased maintenance costs.
Factors Affecting PCB Crosstalk
Several factors influence the severity of PCB crosstalk:
-
Trace Spacing: The closer the traces are to each other, the more likely they are to experience crosstalk. As a general rule, increasing the spacing between traces reduces the risk of crosstalk.
-
Signal Frequency: Higher frequency signals are more prone to crosstalk because they have shorter wavelengths and can couple more easily with nearby traces.
-
Signal Rise and Fall Times: Faster rise and fall times (i.e., shorter transition times between logic states) can increase the risk of crosstalk because they generate higher frequency components that can couple more easily with nearby traces.
-
Trace Length: Longer traces are more susceptible to crosstalk because they provide more opportunities for coupling to occur along their length.
-
PCB Stackup: The arrangement of the layers in the PCB stackup can affect crosstalk. For example, placing a ground plane between signal layers can help reduce crosstalk by providing shielding.
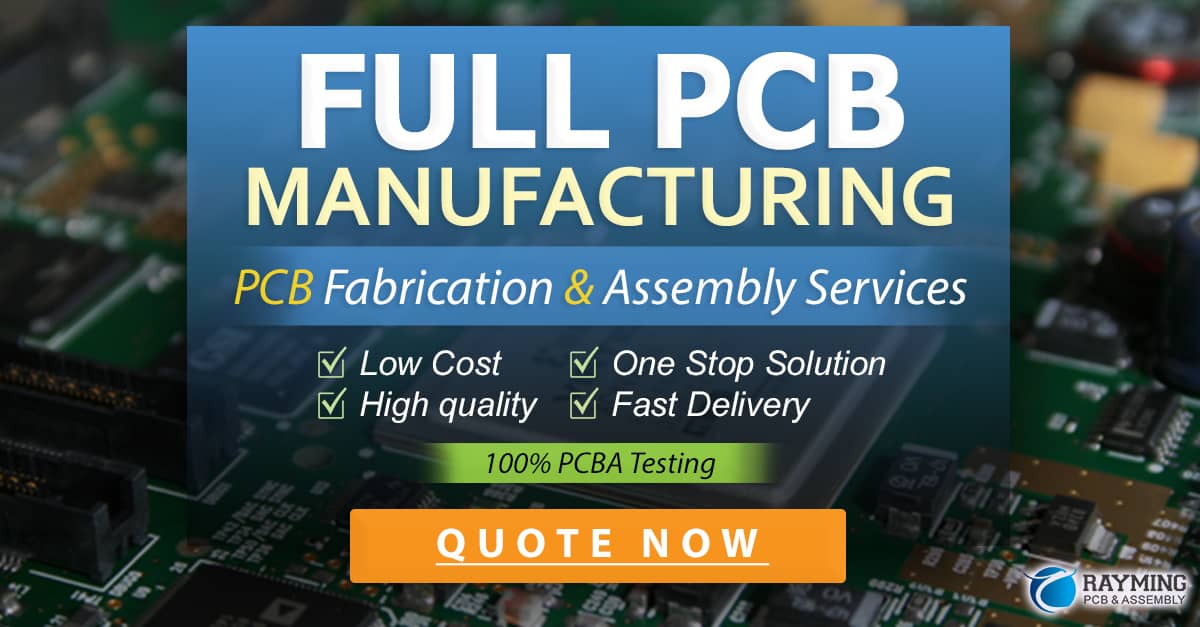
Techniques for Reducing PCB Crosstalk
There are several techniques that PCB designers can use to reduce the risk of crosstalk:
1. Increase Trace Spacing
One of the most effective ways to reduce crosstalk is to increase the spacing between traces. The following table provides general guidelines for minimum trace spacing based on the signal rise time:
Signal Rise Time | Minimum Trace Spacing |
---|---|
< 1 ns | 20 mil |
1-2 ns | 15 mil |
2-3 ns | 10 mil |
> 3 ns | 5 mil |
2. Use Ground Planes
Placing ground planes between signal layers can help reduce crosstalk by providing shielding. The ground planes act as barriers that prevent the electric and magnetic fields from coupling between traces on different layers.
3. Route Signals Orthogonally
When traces must cross each other, routing them orthogonally (at a 90-degree angle) can help minimize crosstalk. This is because the electric and magnetic fields are perpendicular to each other at the crossing point, which reduces the coupling between the traces.
4. Use Differential Signaling
Differential signaling involves using two traces to carry a single signal, with one trace carrying the signal and the other carrying its complement. This technique can help reduce crosstalk because any interference that couples onto both traces will cancel out when the receiver subtracts the two signals.
5. Terminate Traces Properly
Proper termination of traces can help minimize reflections and reduce the risk of crosstalk. There are several termination techniques, such as series termination, parallel termination, and AC termination, each with its own advantages and disadvantages.
6. Use Shielding
In some cases, it may be necessary to use shielding to reduce crosstalk. This can involve using shielded cables, enclosing sensitive circuits in metal enclosures, or adding shielding traces around critical signals on the PCB.
Simulating and Measuring PCB Crosstalk
To ensure that a PCB design is resistant to crosstalk, it is important to simulate and measure the crosstalk performance during the design process.
Simulation Tools
There are several software tools available for simulating PCB crosstalk, such as:
- Altium Designer
- Cadence Allegro
- Mentor Graphics HyperLynx
- Ansys SIwave
These tools allow designers to model the PCB stackup, trace geometry, and material properties, and then simulate the crosstalk performance under various operating conditions. By identifying potential crosstalk issues early in the design process, designers can make the necessary adjustments to minimize the risk of problems in the final product.
Measurement Techniques
Once a PCB Prototype has been fabricated, it is important to measure its actual crosstalk performance to validate the simulation results and ensure that the design meets the required specifications. There are several techniques for measuring PCB crosstalk, such as:
-
Time-Domain Reflectometry (TDR): TDR involves sending a fast-rising pulse down a trace and measuring the reflections that occur at impedance discontinuities. By analyzing the timing and amplitude of the reflections, designers can identify potential crosstalk issues.
-
Vector Network Analysis (VNA): VNA involves measuring the S-parameters of the PCB over a range of frequencies. The S-parameters characterize the transmission and reflection behavior of the PCB and can be used to calculate the crosstalk between traces.
-
Near-Field Probing: Near-field probing involves using a small probe to measure the electric and magnetic fields close to the surface of the PCB. This technique can help identify areas of high crosstalk and provide insight into the coupling mechanisms at work.
FAQ
1. What is the difference between inductive and capacitive crosstalk?
Inductive crosstalk is caused by the magnetic fields generated by current flowing through a conductor, while capacitive crosstalk is caused by the electric fields between two conductors. Inductive crosstalk is more common in situations where traces are carrying high-frequency or fast-changing currents, while capacitive crosstalk is more common in situations where traces are carrying high-voltage or slowly-changing signals.
2. How does differential signaling help reduce crosstalk?
Differential signaling involves using two traces to carry a single signal, with one trace carrying the signal and the other carrying its complement. Any interference that couples onto both traces will affect them equally, and when the receiver subtracts the two signals, the interference will cancel out. This makes differential signaling highly resistant to crosstalk.
3. What is the purpose of ground planes in reducing crosstalk?
Ground planes act as barriers that prevent the electric and magnetic fields from coupling between traces on different layers of the PCB. By placing ground planes between signal layers, designers can effectively shield the traces from each other and reduce the risk of crosstalk.
4. Why is it important to simulate and measure PCB crosstalk during the design process?
Simulating and measuring PCB crosstalk during the design process allows designers to identify potential issues early on, when they are easier and less expensive to fix. By validating the crosstalk performance of the PCB through simulation and measurement, designers can ensure that the final product will meet the required specifications and perform reliably in the field.
5. What are some common software tools used for simulating PCB crosstalk?
Some common software tools used for simulating PCB crosstalk include Altium Designer, Cadence Allegro, Mentor Graphics HyperLynx, and Ansys SIwave. These tools allow designers to model the PCB stackup, trace geometry, and material properties, and then simulate the crosstalk performance under various operating conditions.
Conclusion
PCB crosstalk is a critical issue in modern electronic design, with the potential to degrade signal integrity, increase EMI/EMC issues, and reduce overall system reliability. By understanding the causes and effects of crosstalk, and by employing appropriate design techniques and simulation/measurement tools, PCB designers can effectively minimize the risk of crosstalk and ensure the optimal performance of their products.
0 Comments