What is PCB Conformal Coating?
PCB conformal coating is a thin, protective layer applied directly onto the surface of a PCB, conforming to its contours and components. This coating acts as a barrier against environmental factors that could potentially damage the PCB, such as moisture, dust, chemicals, and extreme temperatures. Conformal coatings are typically applied using methods like spraying, dipping, or brushing, and can be composed of various materials, including:
- Acrylic
- Silicone
- Polyurethane
- Epoxy
- Parylene
Each material has its own unique properties, such as dielectric strength, flexibility, and resistance to specific environmental factors. The choice of material depends on the specific requirements of the application and the level of protection needed.
Advantages of PCB Conformal Coating
-
Thin and Lightweight: Conformal coatings are typically very thin, ranging from 25 to 250 microns in thickness. This allows for minimal added weight and volume to the PCB, which is especially important for applications where space and weight are critical factors, such as in aerospace and automotive industries.
-
Easy Repair and Rework: Since conformal coatings are thin and can be easily removed using solvents or mechanical methods, PCBs can be quickly repaired or reworked without causing significant damage to the board or its components.
-
Cost-effective: Compared to PCB encapsulation, conformal coating is generally more affordable, as it requires less material and can be applied using simple, automated processes.
-
Versatility: Conformal coatings can be applied to a wide range of PCB designs and configurations, including those with complex geometries and densely populated boards.
Disadvantages of PCB Conformal Coating
-
Limited Protection: While conformal coatings provide a good level of protection against moisture and dust, they may not be sufficient for more extreme environments, such as those with high levels of vibration, impact, or chemical exposure.
-
Potential for Defects: If the conformal coating is not applied properly, it can lead to defects such as bubbles, pinholes, or uneven coverage, which can compromise the level of protection provided.
-
Difficulty in Inspection: Once a PCB has been coated, it can be challenging to visually inspect the board and its components for any defects or issues.
What is PCB Encapsulation?
PCB encapsulation involves completely surrounding the PCB and its components with a protective material, typically a polymer resin. This creates a solid, impenetrable barrier that shields the PCB from environmental hazards, as well as providing structural support and insulation. Encapsulation materials can be categorized into two main types:
-
Potting Compounds: These are liquid resins that are poured over the PCB and allowed to cure, forming a solid, protective layer. Common potting compounds include epoxy, silicone, and polyurethane.
-
Overmolding: This process involves placing the PCB into a mold and injecting a thermoplastic or thermoset material around it, creating a custom-shaped protective enclosure.
Advantages of PCB Encapsulation
-
Superior Protection: PCB encapsulation provides the highest level of protection against environmental hazards, including moisture, dust, chemicals, vibration, and impact. This makes it ideal for applications in harsh environments, such as outdoor or industrial settings.
-
Improved Structural Integrity: The encapsulation material not only protects the PCB but also provides structural support, helping to prevent damage from physical stress and vibration.
-
Enhanced Insulation: Encapsulation materials often have excellent dielectric properties, providing superior electrical insulation compared to conformal coatings.
-
Tamper-evident: Any attempt to access or tamper with an encapsulated PCB will be clearly visible, making it suitable for applications requiring high levels of security.
Disadvantages of PCB Encapsulation
-
Increased Weight and Size: Encapsulation adds significant weight and volume to the PCB, which can be a drawback for applications where space and weight are limited.
-
Higher Cost: Due to the larger amount of material required and the more complex application process, PCB encapsulation is generally more expensive than conformal coating.
-
Difficult Repair and Rework: Once a PCB has been encapsulated, it is extremely difficult, if not impossible, to repair or rework without causing significant damage to the board and its components.
-
Limited Design Flexibility: Encapsulation may not be suitable for PCBs with complex geometries or densely populated boards, as it can be challenging to ensure complete and even coverage of the protective material.
Comparing PCB Conformal Coating and PCB Encapsulation
To help you better understand the differences between PCB conformal coating and PCB encapsulation, we have created a comparison table highlighting the key aspects of each method:
Aspect | PCB Conformal Coating | PCB Encapsulation |
---|---|---|
Protection Level | Moderate | High |
Thickness | Thin (25-250 microns) | Thick (several millimeters or more) |
Weight and Size Impact | Minimal | Significant |
Repair and Rework | Easy | Difficult |
Cost | Lower | Higher |
Design Flexibility | High | Limited |
Tamper Evidence | Low | High |
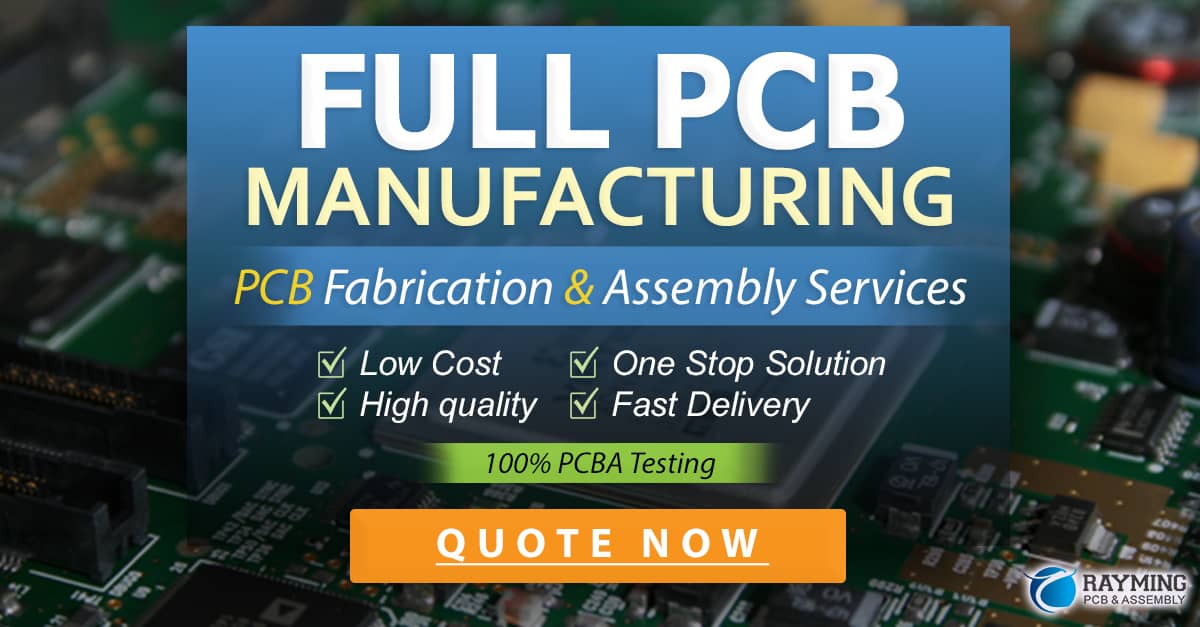
Applications of PCB Conformal Coating and PCB Encapsulation
Both PCB conformal coating and PCB encapsulation find applications in various industries, each with its own unique requirements for PCB Protection. Some common applications include:
Aerospace and Defense
In the aerospace and defense industries, PCBs are often exposed to extreme temperatures, vibration, and moisture. Conformal coating is widely used in these applications due to its lightweight nature and ability to provide adequate protection without adding significant weight to the PCB. However, for more critical applications, such as those in space or military environments, PCB encapsulation may be preferred for its superior protection and structural support.
Automotive
The automotive industry presents a challenging environment for PCBs, with exposure to temperature fluctuations, moisture, and vibration. Conformal coating is commonly used for PCBs in automotive applications, as it provides a good balance of protection and cost-effectiveness. However, for PCBs located in areas with more extreme conditions, such as under the hood or in the engine compartment, encapsulation may be necessary to ensure long-term reliability.
Medical Devices
Medical devices require high levels of reliability and protection against moisture and other contaminants. Conformal coating is often used for PCBs in medical devices, as it provides adequate protection while allowing for easy repair and rework if necessary. In some cases, such as implantable devices or those exposed to harsh disinfection processes, PCB encapsulation may be required to ensure the highest level of protection and long-term stability.
Industrial Automation and Control Systems
Industrial environments can be particularly harsh, with exposure to dust, moisture, chemicals, and extreme temperatures. In these applications, PCB encapsulation is often preferred due to its superior protection and structural support. However, for less critical applications or those where cost is a primary concern, conformal coating may be sufficient.
Consumer Electronics
In consumer electronics, cost and design flexibility are often key considerations. Conformal coating is widely used in this industry, as it provides adequate protection against moisture and dust while allowing for more complex PCB designs and easier repair or rework. PCB encapsulation is less common in consumer electronics, but may be used in applications requiring higher levels of protection or tamper evidence, such as in security systems or outdoor devices.
Frequently Asked Questions (FAQ)
-
Q: Can PCB conformal coating and encapsulation be used together?
A: Yes, in some cases, a combination of conformal coating and encapsulation can be used to provide the best balance of protection, cost, and design flexibility. For example, a PCB may be selectively encapsulated in areas requiring the highest level of protection, while other areas are conformal coated for easier repair and rework. -
Q: How do I choose the right conformal coating material for my application?
A: The choice of conformal coating material depends on several factors, including the specific environmental hazards the PCB will be exposed to, the required level of protection, and the compatibility with the PCB materials and components. It is essential to consult with a conformal coating expert or refer to industry standards and guidelines to select the most appropriate material for your application. -
Q: Can PCB encapsulation be removed for repair or rework?
A: In most cases, removing PCB encapsulation for repair or rework is extremely difficult and may cause significant damage to the PCB and its components. If repair or rework is a likely requirement, conformal coating may be a more suitable option. -
Q: How does the cost of PCB conformal coating compare to encapsulation?
A: PCB conformal coating is generally more cost-effective than encapsulation, as it requires less material and can be applied using simpler, automated processes. However, the total cost of ownership should be considered, taking into account factors such as the required level of protection, expected product lifespan, and potential repair or rework costs. -
Q: Are there any environmental concerns associated with PCB conformal coating or encapsulation?
A: Some conformal coating and encapsulation materials may contain substances that are harmful to the environment or human health. It is important to select materials that comply with relevant environmental regulations, such as RoHS (Restriction of Hazardous Substances) and REACH (Registration, Evaluation, Authorization, and Restriction of Chemicals). Additionally, proper disposal methods should be followed for any waste generated during the application or removal of these protective materials.
Conclusion
Choosing between PCB conformal coating and PCB encapsulation requires careful consideration of your specific application requirements, including the level of protection needed, environmental factors, cost, and design flexibility. While conformal coating provides a thin, lightweight, and cost-effective solution for moderate protection, encapsulation offers superior protection and structural support at the expense of added weight, size, and cost.
By understanding the advantages and disadvantages of each method and considering the unique demands of your industry and application, you can make an informed decision that balances performance, reliability, and cost-effectiveness. In some cases, a combination of both methods may provide the best overall solution.
As technology continues to advance and new materials and application techniques emerge, it is crucial to stay informed about the latest developments in PCB protection. By working closely with experienced professionals and staying up-to-date with industry standards and best practices, you can ensure that your PCBs are adequately protected, no matter how challenging the environment may be.
0 Comments