Understanding PCB Component Selection
Selecting the right components for your printed circuit board (PCB) is crucial for ensuring the reliability, functionality, and cost-effectiveness of your electronic device. With a wide variety of components available in the market, it can be overwhelming to make the right choices. In this article, we will discuss 14 important tips to help you navigate the process of PCB component selection.
1. Determine the Purpose and Specifications of Your PCB
Before selecting components, it is essential to have a clear understanding of the purpose and specifications of your PCB. Consider factors such as:
- The intended application of the device
- The operating environment (temperature, humidity, vibration, etc.)
- The power requirements
- The desired performance and functionality
- The size and form factor constraints
By defining these parameters, you can narrow down your component choices and ensure that they meet the specific needs of your project.
2. Choose Components with Appropriate Ratings
When selecting components, pay close attention to their ratings and ensure that they match the requirements of your PCB. Some key ratings to consider include:
- Voltage rating: Ensure that the component can handle the maximum voltage expected in the circuit.
- Current rating: Choose components that can safely carry the required current without overheating or failing.
- Power rating: Verify that the component can dissipate the necessary power without exceeding its limits.
- Temperature rating: Consider the operating temperature range of the component and ensure it matches the expected environmental conditions.
Selecting components with appropriate ratings helps prevent failures, ensures reliable operation, and prolongs the lifespan of your PCB.
3. Consider the Component Package Type
PCB Components come in various package types, such as through-hole, surface mount (SMT), and ball grid array (BGA). Each package type has its advantages and limitations. Consider the following factors when choosing the package type:
- Available board space: SMT components are smaller and allow for higher density layouts compared to through-hole components.
- Manufacturing capabilities: Ensure that your PCB Assembly process can handle the chosen package type. Some package types may require specialized equipment or skills.
- Mechanical stability: Through-hole components provide better mechanical stability and are suitable for applications with high vibration or stress.
- Thermal management: Certain package types, such as BGA, offer better thermal dissipation compared to others.
Select the package type that best suits your PCB design, manufacturing capabilities, and performance requirements.
4. Evaluate Component Availability and Lead Time
Component availability and lead time are critical factors to consider when selecting PCB components. Some components may have long lead times or may be in short supply, which can impact your project timeline and budget. To mitigate these risks:
- Research component availability from multiple suppliers and distributors.
- Check lead times and plan your procurement accordingly.
- Consider alternative components with similar specifications if the desired component is not readily available.
- Stay updated on market trends and potential supply chain disruptions that may affect component availability.
By proactively evaluating component availability and lead time, you can avoid delays and ensure a smooth manufacturing process.
5. Prioritize Component Quality and Reliability
The quality and reliability of PCB components directly impact the overall performance and longevity of your electronic device. To ensure high-quality and reliable components:
- Choose components from reputable manufacturers with a track record of producing reliable products.
- Look for components with appropriate quality certifications, such as ISO, RoHS, or UL, depending on your industry and application requirements.
- Consider the component’s failure rate and expected lifespan based on the manufacturer’s data and user reviews.
- Perform thorough testing and validation of components before mass production to identify any potential issues.
Investing in high-quality and reliable components may have a higher upfront cost but can save you from costly failures and repairs in the long run.
6. Optimize for Cost-Effectiveness
Cost is a significant factor in PCB component selection, especially for large-scale production. To optimize for cost-effectiveness:
- Compare prices from multiple suppliers and negotiate for better rates based on your order quantity.
- Consider the total cost of ownership, including not only the component price but also the assembly, testing, and potential rework costs.
- Evaluate the trade-offs between component cost and performance. In some cases, a slightly more expensive component may provide better reliability and long-term cost savings.
- Explore cost-saving opportunities, such as using standardized components or leveraging economies of scale.
Strike a balance between cost and quality to ensure that your PCB components meet your budget constraints while still delivering the required performance.
7. Ensure Compatibility and Interoperability
When selecting PCB components, it is crucial to ensure compatibility and interoperability between different components and subsystems. Consider the following aspects:
- Electrical compatibility: Verify that the component’s electrical characteristics, such as voltage levels, current ratings, and signaling standards, are compatible with other components in the circuit.
- Mechanical compatibility: Ensure that the component’s physical dimensions, mounting requirements, and connector types match the PCB layout and enclosure design.
- Software compatibility: If your PCB includes programmable components or interfaces with software systems, ensure that the selected components are compatible with the required software protocols and drivers.
Thorough compatibility checks and system-level testing can help identify and resolve any interoperability issues early in the design process.
8. Consider Thermal Management
Thermal management is essential for ensuring the reliable operation and longevity of PCB components. Overheating can lead to component failure and reduce the overall performance of your device. When selecting components:
- Evaluate the component’s power dissipation and thermal characteristics.
- Consider the PCB layout and component placement to optimize heat distribution and avoid thermal hotspots.
- Use thermal simulation tools to analyze the thermal behavior of your PCB and identify potential issues.
- Incorporate appropriate cooling mechanisms, such as heatsinks, fans, or thermal interface materials, if necessary.
Effective thermal management helps prevent component degradation, improves reliability, and ensures that your PCB operates within safe temperature limits.
9. Comply with Regulatory Requirements and Standards
Depending on your industry and target market, your PCB may need to comply with various regulatory requirements and standards. These may include safety standards, electromagnetic compatibility (EMC) regulations, environmental regulations, and industry-specific certifications. When selecting components:
- Identify the applicable regulatory requirements and standards for your product.
- Choose components that are certified and compliant with the relevant standards.
- Obtain necessary documentation, such as datasheets, compliance certificates, and test reports, from component manufacturers.
- Conduct appropriate testing and certification processes to ensure overall compliance of your PCB.
Failing to comply with regulatory requirements can result in legal and financial consequences, as well as potential product recalls or market entry barriers.
10. Plan for Obsolescence and Component End-of-Life
Electronic components have limited lifespans and may become obsolete or reach end-of-life (EOL) status over time. This can pose challenges for long-term product support and maintenance. To mitigate obsolescence risks:
- Research the lifecycle status of the components you are considering and choose components with longer expected lifespans.
- Stay informed about component EOL notifications from manufacturers and plan for timely replacements or redesigns.
- Consider using pin-compatible alternative components or designing for easy component substitution in case of obsolescence.
- Maintain accurate documentation of component specifications, suppliers, and potential replacements for future reference.
Proactive obsolescence management helps ensure the long-term viability of your PCB and minimizes the impact of component discontinuations.
11. Collaborate with Experienced PCB Design and Manufacturing Partners
Partnering with experienced PCB design and manufacturing experts can greatly facilitate the component selection process. These partners can provide valuable insights and recommendations based on their industry knowledge and practical experience. They can help you:
- Identify suitable components for your specific application and requirements.
- Optimize the PCB layout and component placement for manufacturability and reliability.
- Suggest alternative components or design modifications to improve performance or reduce costs.
- Navigate Supply Chain Challenges and ensure timely procurement of components.
Leveraging the expertise of PCB design and manufacturing partners can streamline your component selection process, reduce risks, and accelerate your time to market.
12. Prototype and Test Components
Before finalizing your component selections and proceeding with mass production, it is essential to prototype and test the components in a representative environment. Prototyping allows you to:
- Validate the functionality and performance of the selected components.
- Identify any compatibility issues or unexpected behaviors.
- Optimize the PCB layout and component placement based on real-world testing.
- Verify the manufacturability and assembly process of the chosen components.
Thorough prototyping and testing help catch potential issues early, reduce design iterations, and improve the overall quality and reliability of your PCB.
13. Maintain Detailed Component Documentation
Maintaining accurate and detailed documentation of your selected PCB components is crucial for future reference, maintenance, and troubleshooting. Your component documentation should include:
- Component datasheets and specifications
- Supplier information and part numbers
- PCB schematics and layout files
- Assembly instructions and bill of materials (BOM)
- Test reports and certification documents
Proper documentation ensures that all stakeholders, including designers, manufacturers, and maintenance personnel, have access to the necessary information to understand and support your PCB throughout its lifecycle.
14. Stay Updated with Industry Trends and Advancements
The electronics industry is constantly evolving, with new components, technologies, and manufacturing techniques emerging regularly. To make informed component selections and stay competitive, it is important to:
- Stay updated with the latest industry trends and advancements through trade publications, conferences, and webinars.
- Monitor the development of new component technologies and assess their potential benefits for your PCB design.
- Engage with component manufacturers and suppliers to learn about their latest offerings and roadmaps.
- Continuously evaluate and optimize your component selection process based on industry best practices and lessons learned.
By staying informed and adaptable, you can leverage the latest advancements in PCB components to improve the performance, reliability, and cost-effectiveness of your electronic devices.
FAQs
-
Q: How do I determine the appropriate voltage and current ratings for my PCB components?
A: The voltage and current ratings of components should be based on the maximum expected values in your circuit. Review your PCB’s power requirements, consider any transient or peak conditions, and select components with ratings that provide an adequate safety margin. -
Q: What should I do if a component I need is not readily available or has a long lead time?
A: If a component is not readily available, consider alternative components with similar specifications. Search for compatible substitutes from different manufacturers or distributors. If the lead time is long, plan your procurement early and consider redesigning your PCB to use more readily available components. -
Q: How can I ensure the compatibility of components from different manufacturers?
A: When using components from different manufacturers, carefully review their datasheets and specifications to ensure they meet your requirements. Pay attention to factors such as voltage levels, signaling standards, and pin configurations. Conduct thorough testing and validation to verify compatibility and interoperability. -
Q: What are some common certifications and standards I should look for when selecting PCB components?
A: Common certifications and standards for PCB components include RoHS (Restriction of Hazardous Substances), UL (Underwriters Laboratories), CE (Conformité Européenne), and ISO (International Organization for Standardization). The specific certifications required depend on your industry, application, and target market regulations. -
Q: How often should I review and update my component selections?
A: It is recommended to review and update your component selections periodically, typically every 6 to 12 months, or whenever there are significant changes in your PCB design or market requirements. Stay informed about component EOL notifications, new product releases, and industry trends to make timely updates and ensure the long-term viability of your PCB.
Conclusion
Selecting the right PCB components is a critical aspect of designing and manufacturing reliable and cost-effective electronic devices. By following these 14 important tips, you can navigate the component selection process with confidence and make informed decisions that align with your project requirements.
Remember to consider factors such as component ratings, package types, availability, quality, cost, compatibility, thermal management, regulatory compliance, obsolescence planning, and industry trends. Collaborate with experienced PCB design and manufacturing partners, prototype and test your components, maintain detailed documentation, and stay updated with the latest advancements in the field.
By applying these tips and best practices, you can optimize your PCB component selection, reduce risks, and ensure the success of your electronic projects. Happy designing and manufacturing!
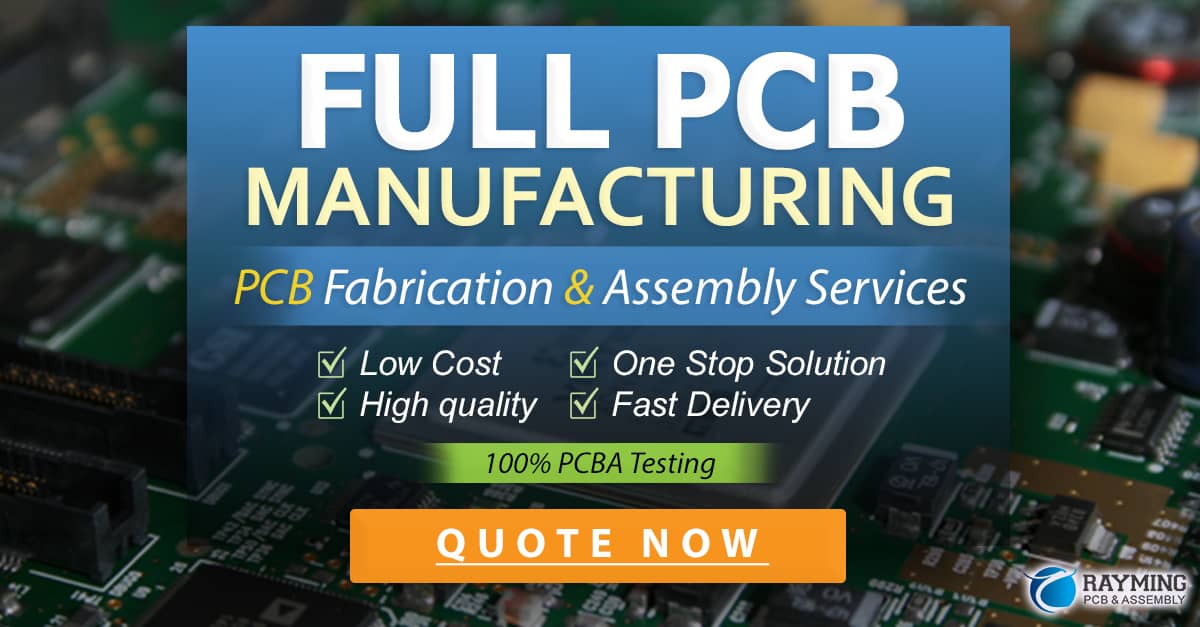
0 Comments