In the rapidly evolving world of electronics, the demand for high-quality and reliable Printed Circuit Boards (PCBs) has never been higher. PCBs are the backbone of virtually every electronic device, from consumer electronics to industrial automation systems, and their performance and reliability are critical to the overall success of any product. As the complexity of electronic designs continues to increase, sourcing the right PCB assembly service becomes a crucial decision for businesses and manufacturers.
RayMing Assembly, a leading provider of PCB assembly services, has established itself as a trusted partner for companies seeking high-quality, cost-effective, and timely PCB solutions. With a commitment to excellence, cutting-edge technology, and a team of skilled professionals, RayMing Assembly offers a comprehensive range of services that cater to the diverse needs of its clients.
Expertise and Experience
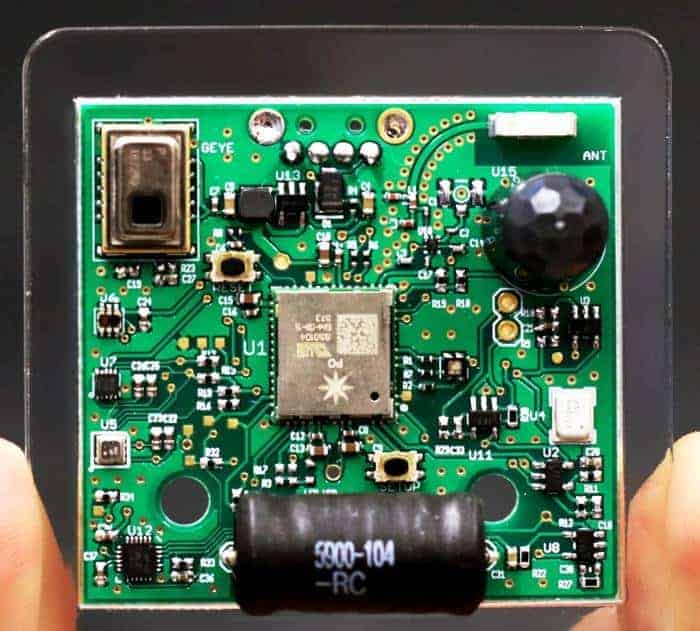
One of the key advantages of choosing RayMing Assembly is their extensive expertise and experience in the PCB assembly industry. With years of experience serving clients across various sectors, RayMing Assembly has developed a deep understanding of the unique challenges and requirements associated with different applications and industries.
Their team of highly skilled engineers and technicians possess a wealth of knowledge and hands-on experience in PCB design, manufacturing, and assembly processes. This expertise ensures that every project is approached with a keen attention to detail, ensuring that the final product meets the highest standards of quality and performance.
State-of-the-Art Facilities and Equipment
RayMing Assembly’s commitment to delivering top-notch PCB assembly services is further reinforced by their state-of-the-art facilities and advanced equipment. Their manufacturing facilities are equipped with the latest technology and automated systems, enabling them to handle even the most complex PCB designs with precision and efficiency.
From high-speed pick-and-place machines to advanced inspection and testing equipment, RayMing Assembly ensures that every step of the PCB assembly process is executed with utmost accuracy and quality control. This dedication to maintaining cutting-edge facilities and equipment allows them to stay ahead of the curve and consistently deliver exceptional results.
Comprehensive Service Offerings
RayMing Assembly offers a comprehensive range of PCB assembly services, catering to the diverse needs of its clients. Their service offerings include:
1. Prototyping and Small-Volume Production
For businesses developing new products or requiring small-volume production runs, RayMing Assembly provides efficient prototyping and low-volume manufacturing services. This allows clients to test and validate their designs before committing to large-scale production, minimizing risks and ensuring product success.
2. High-Volume Manufacturing
With their state-of-the-art facilities and streamlined processes, RayMing Assembly is well-equipped to handle high-volume PCB assembly projects. Their ability to scale production without compromising quality ensures that clients can meet increasing market demands while maintaining consistent product performance.
3. Box Build and System Integration
In addition to PCB assembly, RayMing Assembly offers box build and system integration services. This comprehensive approach streamlines the entire product development process, eliminating the need for multiple vendors and ensuring seamless integration of all components.
4. Testing and Quality Assurance
RayMing Assembly places a strong emphasis on quality assurance, employing rigorous testing and inspection procedures throughout the PCB assembly process. Their advanced testing facilities and experienced technicians ensure that every PCB meets the highest standards of quality and performance, minimizing the risk of defects and ensuring reliable operation.
Flexible and Customizable Solutions
RayMing Assembly understands that every client has unique requirements and specialized needs. To accommodate this diversity, they offer flexible and customizable solutions tailored to meet the specific demands of each project. Their team works closely with clients to understand their objectives, design constraints, and production requirements, ensuring that the final product aligns with their vision and exceeds their expectations.
Supply Chain Management and Logistics
In today’s global market, efficient supply chain management and logistics are critical for ensuring timely delivery and minimizing disruptions. RayMing Assembly excels in this area, leveraging their extensive network of suppliers and logistics partners to ensure seamless and reliable component sourcing and product delivery.
Their robust supply chain management processes and streamlined logistics operations enable them to minimize lead times, reduce costs, and deliver products to their clients promptly, regardless of their location.
Quality Certifications and Compliance
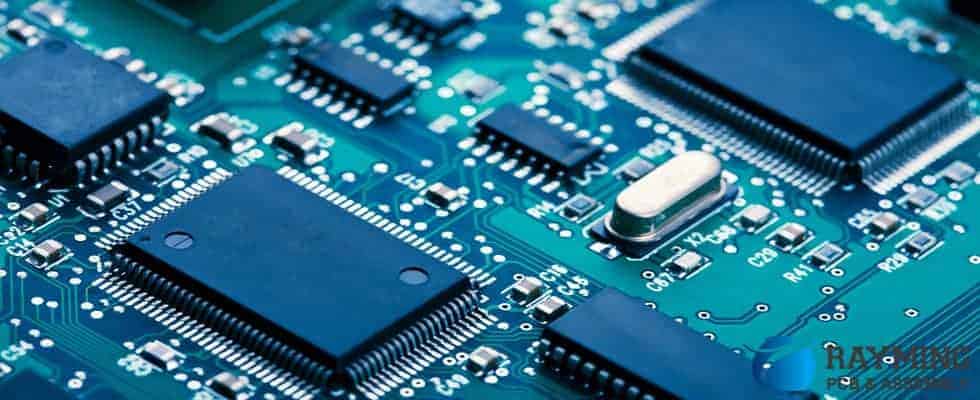
RayMing Assembly takes pride in adhering to the highest industry standards and certifications. They hold various quality certifications, including ISO 9001, ISO 13485, and IATF 16949, demonstrating their commitment to quality management and continuous improvement.
Additionally, RayMing Assembly ensures compliance with relevant industry regulations and standards, such as RoHS, REACH, and CE marking, providing clients with peace of mind and ensuring their products meet regulatory requirements in various markets.
Customer Support and Collaboration
At RayMing Assembly, customer satisfaction is a top priority. They understand the importance of effective communication and collaboration throughout the entire PCB assembly process. Their dedicated customer support team is available to address any questions or concerns, providing timely and knowledgeable assistance to ensure a smooth and successful project experience.
RayMing Assembly also encourages open communication and collaboration with their clients, fostering a partnership approach where ideas and feedback are welcomed and incorporated into the design and production processes. This collaborative approach ensures that the final product meets and exceeds the client’s expectations.
FQA (Frequently Asked Questions)
- Q: How does RayMing Assembly ensure the quality of their PCB assembly services? A: RayMing Assembly employs rigorous quality assurance processes, including advanced testing and inspection procedures, to ensure that every PCB meets the highest standards of quality and performance. They also hold various quality certifications, such as ISO 9001, ISO 13485, and IATF 16949, demonstrating their commitment to continuous improvement and quality management.
- Q: Can RayMing Assembly handle complex or high-density PCB designs? A: Yes, RayMing Assembly’s state-of-the-art facilities and advanced equipment, combined with the expertise of their skilled engineers and technicians, allow them to handle even the most complex and high-density PCB designs with precision and efficiency.
- Q: Does RayMing Assembly offer customizable solutions for unique PCB requirements? A: Absolutely. RayMing Assembly understands that every client has unique requirements and specialized needs. They offer flexible and customizable solutions tailored to meet the specific demands of each project, ensuring that the final product aligns with the client’s vision and exceeds their expectations.
- Q: How does RayMing Assembly manage supply chain and logistics for PCB assembly projects? A: RayMing Assembly leverages an extensive network of suppliers and logistics partners, combined with robust supply chain management processes and streamlined logistics operations. This approach enables them to ensure seamless and reliable component sourcing, minimize lead times, reduce costs, and deliver products promptly to their clients, regardless of their location.
- Q: What kind of customer support and collaboration can clients expect from RayMing Assembly? A: RayMing Assembly prioritizes customer satisfaction and fosters a collaborative approach throughout the PCB assembly process. They have a dedicated customer support team available to address any questions or concerns, and they encourage open communication and collaboration with their clients, incorporating ideas and feedback into the design and production processes to ensure the final product meets and exceeds expectations.
0 Comments