Printed circuit board (PCB) assembly is the process of soldering electronic components onto a PCB to create a functional printed circuit assembly (PCA). The emergence of sophisticated consumer electronics and IoT devices has led to increasing demand for high-quality PCB assembly services. This article provides an overview of PCB assembly processes, common techniques, and best practices to produce robust and reliable circuit boards.
PCB Assembly Process Overview
PCB assembly involves sequentially integrating components on boards through soldering. Here are the typical steps:
1. Parts Acquisition
Obtain all required components for the build. Verify part numbers, quantities, and packaging. Pre-kit parts for each board assembly.
2. Solder Paste Preparation
Apply solder paste on PCB pads through stencil printing or dispensing. Ensure proper alignment and paste deposition.
3. Pick and Place
Use pick and place machines to mount components onto boards according to program instructions.
4. Reflow Soldering
Heat assemblies in ovens to melt solder paste and attach components. Different profiles suit lead-free or leaded solder.
5. Inspection and Testing
Inspect solder joints and boards for defects. Test functionality per the quality plan. Troubleshoot and rework any issues.
6. Conformal Coating
For added protection, apply coatings to shield against moisture, debris, and corrosion.
7. Final Packaging
Program boards are packaged and shipped safely to customers according to their specifications.
PCB Assembly Techniques
There are several techniques used during PCB assembly:
Solder Paste Printing
Solder paste is applied through metal stencils onto pads using either screen printing or jet dispensing methods:
- Screen Printing: A squeegee spreads paste over a stencil onto the board. Typically lower cost but can smear paste between openings.
- Jet Dispensing: Precisely deposits paste dots only where needed. Higher accuracy but slower than screen printing.
Pick and Place
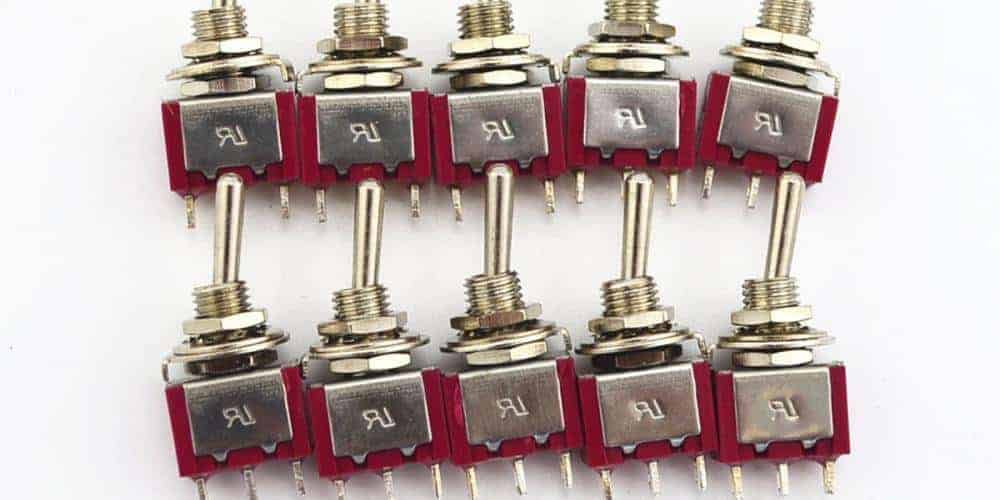
Automated pick and place machines efficiently mount components onto the solder paste. Key aspects include:
- Nozzle selection – Vacuum or mechanical grip nozzles to handle varying component packages.
- Accuracy – High precision robots accurately place tiny components like 0201 chips.
- Speed – Modern machines place over 25,000 components per hour.
Reflow Soldering
Heating boards in a reflow oven melts paste to attach components. Different soldering profiles are used:
- Convection heating – Hot forced air is ideal for low density boards.
- Infrared heating – Infrared lamps apply fast concentrated heat. Often used for lead-free soldering.
- Vapor phase – Boards pass through vapor to uniformly heat all surfaces.
Conformal Coating
Conformal coatings protect boards from environmental threats. Typical coating methods include:
- Spray coating – Automated selective sprayers apply coatings efficiently.
- Brushing – Manual brushing for coating complex board areas.
- Dipping – Dips the entire board into a coating bath.
Best Practices for PCB Assembly
Follow these best practices to achieve quality and reliability in circuit board assembly:
Design for Manufacturing
Optimize board layouts and component selection with assembly in mind. Consider solderability,density, and positioning.
Validate Component Packaging
Confirm all parts are in tape and reel or other suitable packaging for automated assembly. Avoid loose parts.
Control Solder Paste Printing
Use stencils optimized for each board design. Perform regular paste inspections. Plan for appropriate drying times.
Program Robust Component Placement
Strategize component grouping, positioning, and orientation to maximize efficiency and minimize defects.
Standardize Processes
Standardizing procedures, materials, and assembly steps for consistency across builds. Prevent variability.
Monitor Reflow Profiles
Closely control oven conveyor speed, zone temperatures, and heating ramps. Avoid thermal stresses.
Automate Inspection and Testing
Leverage automation technologies like automated optical inspection (AOI) and in-circuit testing (ICT) whenever possible for rapid quality control.
Qualify Assembly Partners
Select experienced assembly partners with qualified processes, modern equipment, quality control focus, and communication practices.
Comparison of Assembly Options
Here is an overview comparing the tradeoffs between assembly service providers:<div class=”table-responsive”>
Factor | Contract Manufacturers | Turnkey Assembly Services | In-house |
---|---|---|---|
Cost | Medium | Highest | Lowest |
Quality | Robust processes | Very high | Dependent on internal capabilities |
Speed | Medium turnaround | Very fast turnaround | Varies based on scale |
Scalability | Highly scalable | Medium volumes | Limited by facility size |
Customization | Highly customizable | Somewhat customizable | Maximum control |
</div>
Contract manufacturers offer a balance of quality, cost, and scalability. Turnkey assembly services provide fast turnaround for lower volumes at a premium. In-house assembly makes sense for high volume products when quality standards can be met.
PCB Assembly Case Study
Here is a case study on how strong PCB assembly delivered success for an automotiveDISPLAY project:
Scenario
XYZ Motors needed to develop a new touchscreen DISPLAY for their electric SUV model upgrade. The displayrequired complex and dense PCB assemblies to manage the elaborate infotainment system.
Solution
XYZ chose an experienced domestic contract manufacturer for the DISPLAY assembly. The CM conducted in-depth DFM analysis and design reviews to optimize the PCBs for manufacturing. They used a fine pitch pick-and-place machine to reliably assemble tiny 0201 components on the boards.
All assembly steps were tightly controlled and continuously inspected per an IPC Class 3 standard. Extensive functional testing validated each completed DISPLAY. Units passing testing were then coated with a protective conformal coating.
The CM’s robust assembly process delivered zero defects for over 50,000 display units. They worked closely with XYZ’s engineers throughout prototyping and ramp up to full production. XYZ was thrilled with the pristine quality and on-time delivery enabling a successful product launch.
Frequently Asked Questions
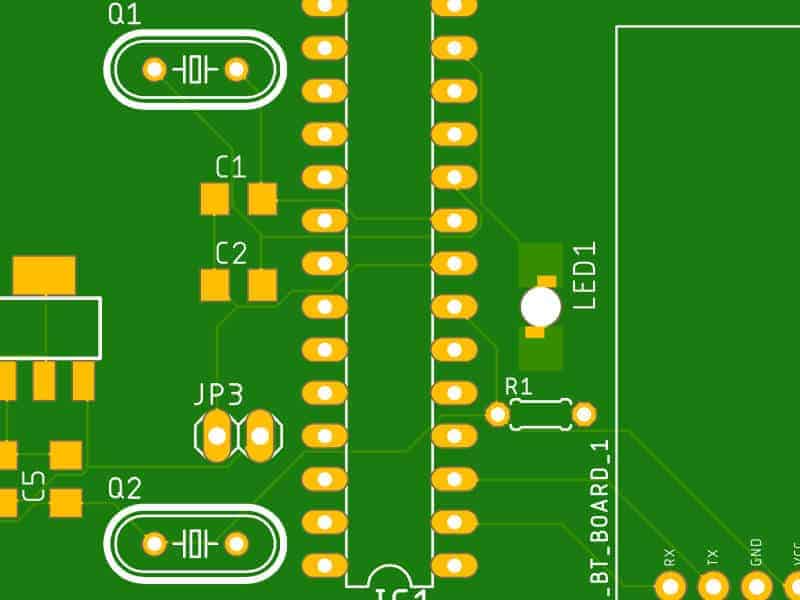
What is the most common defect in PCB assembly?
Insufficient soldering between component leads and pads, known as cold solder joints, are the most frequent defect. Causes include issues like insufficient heat, board warping, or impurities contaminating the joint.
What tolerances are expected for component placement?
For surface mount packages, manufacturers can routinely achieve 50 micron precision or better. For ultra-fine pitch parts below 300 microns, placement to within 25-30 microns is standard.
Can conformal coating be removed or repaired on a board?
Yes, conformal coatings can be removed using chemical strippers or abrasion methods. However, removal risks damage to boards and components. It is best to avoid needing coating removal if possible.
How are BGAs assembled without visible solder joints?
Ball grid arrays use reflow soldering to attach under the package directly to pads on the PCB. X-ray inspection is commonly used to examine these hidden solder joints under BGAs.
How long does it typically take to fully assemble and test a board?
While assembly can be completed very quickly in under a minute, full functional testing often requires 1-2 days. If automated optical inspection is used, total assembly and test time may range from 4 to 8 hours on average.
In summary, PCB assembly demands well-controlled manufacturing practices and close attention to quality. Utilizing qualified assembly services and inspecting boards thoroughly ensures reliable, defect-free circuit boards ready for end products. Proactive optimization and communication between engineering and manufacturing teams is key for assembly success.
0 Comments