Introduction
Printed Circuit Board (PCB) assembly is a critical process in the manufacturing of electronic devices. It involves the placement and soldering of electronic components onto a PCB to create a functional circuit. The PCB Assembly process can be complex and challenging, requiring careful planning and execution to ensure a smooth and efficient process. In this article, we will discuss nine tips on how to ensure a smooth PCB assembly process.
Tip 1: Choose the Right PCB Design Software
Choosing the right PCB design software is crucial for creating a high-quality PCB design. There are many PCB design software options available, each with its own set of features and capabilities. Some popular PCB design software options include:
Software | Features |
---|---|
Altium Designer | – 3D modeling and visualization – Real-time collaboration – Automated design rule checking |
Eagle | – User-friendly interface – Large component library – Affordable pricing |
KiCad | – Open-source – Cross-platform compatibility – Active community support |
When choosing a PCB design software, consider factors such as ease of use, feature set, compatibility with your existing tools and workflows, and pricing.
Tip 2: Create a Detailed Bill of Materials (BOM)
A Bill of Materials (BOM) is a list of all the components and materials required for the PCB assembly process. Creating a detailed and accurate BOM is essential for ensuring that all necessary components are available and that the assembly process runs smoothly.
A typical BOM should include the following information:
- Part number
- Description
- Quantity
- Manufacturer
- Supplier
- Unit price
To create an accurate BOM, it is important to work closely with your design team and component suppliers to ensure that all necessary information is included.
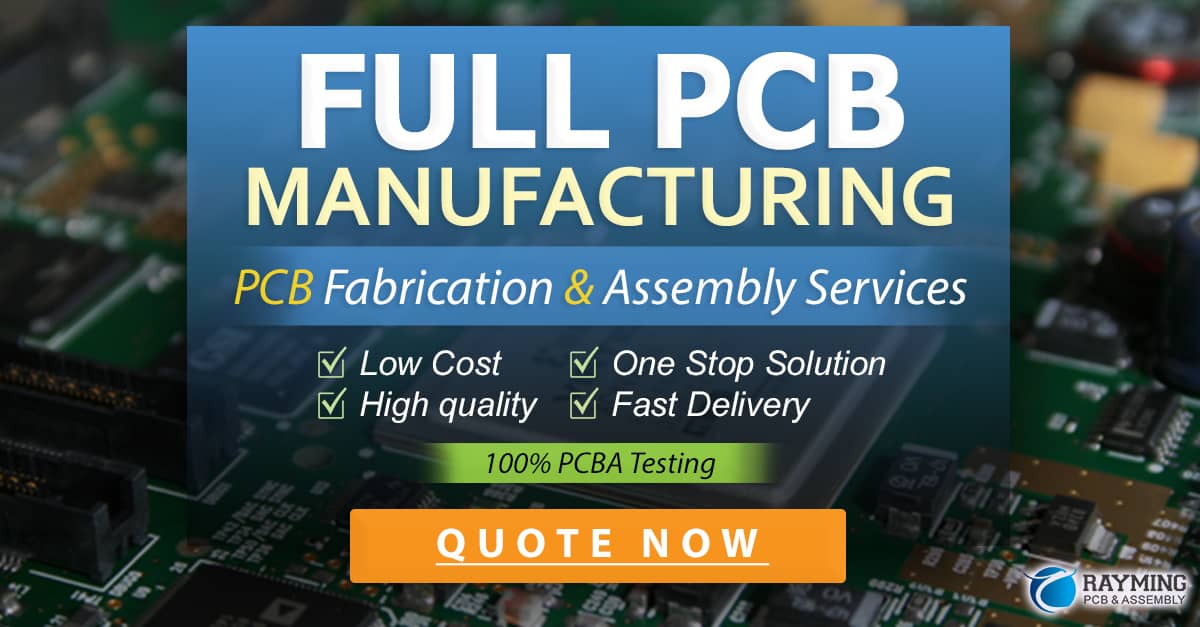
Tip 3: Use Standardized Components
Using standardized components can help simplify the PCB assembly process and reduce the risk of errors. Standardized components are widely available and have well-defined specifications, making them easier to source and work with.
Some benefits of using standardized components include:
- Reduced lead times
- Lower costs
- Improved reliability
- Easier maintenance and repair
When selecting components for your PCB design, consider using standardized components wherever possible.
Tip 4: Consider the Manufacturing Process
When designing your PCB, it is important to consider the manufacturing process that will be used to assemble the board. Different manufacturing processes have different requirements and limitations, and designing your PCB with these in mind can help ensure a smooth assembly process.
Some common PCB manufacturing processes include:
Process | Description |
---|---|
Surface Mount Technology (SMT) | Components are placed and soldered onto the surface of the PCB |
Through-Hole Technology (THT) | Components are inserted into holes drilled in the PCB and soldered in place |
Mixed Technology | A combination of SMT and THT processes |
When designing your PCB, consider factors such as component placement, pad size and shape, and soldermask and silkscreen requirements to ensure compatibility with your chosen manufacturing process.
Tip 5: Conduct Design Reviews
Conducting design reviews is an important step in ensuring the quality and reliability of your PCB design. Design reviews involve reviewing the PCB design with a team of experts to identify potential issues and opportunities for improvement.
Some key areas to focus on during a design review include:
- Component placement and orientation
- Signal integrity and electromagnetic compatibility (EMC)
- Thermal management
- Manufacturability and testability
Conducting design reviews early and often can help catch potential issues before they become problems and can help ensure a smooth PCB assembly process.
Tip 6: Use Automated Assembly Equipment
Using automated assembly equipment can help improve the speed, accuracy, and consistency of the PCB assembly process. Automated equipment can perform tasks such as component placement, soldering, and inspection with a high degree of precision and repeatability.
Some common types of automated assembly equipment include:
Equipment | Description |
---|---|
Pick-and-Place Machine | Automatically places components onto the PCB |
Reflow Oven | Heats the PCB and components to solder them together |
Automated Optical Inspection (AOI) | Uses cameras and image analysis to inspect the assembLED PCB for defects |
Investing in automated assembly equipment can help reduce labor costs, improve quality, and increase throughput.
Tip 7: Implement Quality Control Measures
Implementing quality control measures throughout the PCB assembly process can help ensure that the final product meets the required specifications and performance standards. Quality control measures can include:
- Incoming inspection of components and materials
- In-process inspection and testing
- Final inspection and testing
- Traceability and record-keeping
Implementing a comprehensive quality control program can help identify and correct issues early in the process, reducing the risk of costly rework or product failures.
Tip 8: Work with Experienced PCB Assembly Partners
Working with experienced PCB assembly partners can help ensure a smooth and successful assembly process. Experienced partners have the knowledge, skills, and equipment necessary to handle complex PCB designs and can provide valuable guidance and support throughout the process.
When selecting a PCB assembly partner, consider factors such as:
- Experience and expertise
- Quality certifications and standards
- Capacity and lead times
- Communication and customer service
Building a strong relationship with your PCB assembly partner can help ensure a successful and long-term partnership.
Tip 9: Plan for Testing and Debugging
Even with careful planning and execution, issues can arise during the PCB assembly process. Planning for testing and debugging can help identify and resolve these issues quickly and efficiently.
Some key considerations for testing and debugging include:
- Developing a comprehensive test plan
- Identifying critical test points and signals
- Using appropriate test equipment and software
- Documenting and tracking issues and resolutions
By planning for testing and debugging, you can minimize downtime and ensure that your PCB assembly process stays on track.
FAQs
- What is the difference between SMT and THT assembly processes?
-
SMT (Surface Mount Technology) involves placing components onto the surface of the PCB and soldering them in place, while THT (Through-Hole Technology) involves inserting components into holes drilled in the PCB and soldering them in place. SMT is generally faster and more efficient, while THT is often used for larger or heavier components.
-
How can I ensure the quality of my PCB assembly process?
-
Implementing a comprehensive quality control program that includes incoming inspection, in-process inspection and testing, final inspection and testing, and traceability and record-keeping can help ensure the quality of your PCB assembly process. Working with experienced PCB assembly partners and using automated assembly equipment can also help improve quality and consistency.
-
What should I consider when selecting components for my PCB design?
-
When selecting components for your PCB design, consider factors such as standardization, availability, cost, and compatibility with your chosen manufacturing process. Using standardized components can help simplify the assembly process and reduce the risk of errors, while selecting components that are widely available and cost-effective can help keep your project on budget.
-
How can I reduce the risk of issues during the PCB assembly process?
-
Conducting design reviews, implementing quality control measures, and planning for testing and debugging can all help reduce the risk of issues during the PCB assembly process. Working with experienced PCB assembly partners and using automated assembly equipment can also help minimize the risk of errors and ensure a smooth and efficient process.
-
What should I look for in a PCB assembly partner?
- When selecting a PCB assembly partner, look for a company with experience and expertise in your specific industry or application, as well as a commitment to quality and customer service. Consider factors such as capacity, lead times, and communication when evaluating potential partners, and look for a company that can provide valuable guidance and support throughout the assembly process.
Conclusion
The PCB assembly process can be complex and challenging, but by following these nine tips, you can help ensure a smooth and successful process. From choosing the right PCB design software and creating a detailed BOM to implementing quality control measures and working with experienced PCB assembly partners, each step of the process plays a critical role in the success of your project.
By taking a proactive and strategic approach to PCB assembly, you can minimize the risk of errors, reduce costs, and improve the quality and reliability of your final product. With careful planning and execution, you can ensure that your PCB assembly process is efficient, effective, and successful.
0 Comments