What is OSP PCB?
OSP (Organic Solderability Preservative) is a surface finish applied to printed circuit boards (PCBs) to protect the exposed copper pads from oxidation and contamination. This ensures that the PCB remains solderable during assembly and throughout its lifespan. OSP is a popular choice for PCB surface finish due to its cost-effectiveness, ease of application, and compatibility with a wide range of soldering processes.
Composition of OSP
OSP is typically composed of organic compounds such as benzimidazoles, benzotriazoles, or imidazoles. These compounds form a thin, transparent layer on the copper surface, protecting it from oxidation while allowing for excellent solderability. The thickness of the OSP layer is usually between 0.2 and 0.5 micrometers, which is much thinner compared to other surface finishes like ENIG (Electroless Nickel Immersion Gold) or HASL (Hot Air Solder Leveling).
Advantages of OSP PCB
- Cost-effective: OSP is one of the most economical PCB surface finishes available, making it an attractive option for high-volume production runs.
- Easy to apply: The OSP application process is relatively simple and can be easily integrated into the PCB manufacturing workflow.
- Flat surface: Unlike HASL, which can result in uneven surfaces, OSP provides a flat surface that is ideal for fine-pitch components and high-density designs.
- Good solderability: OSP offers excellent solderability, ensuring reliable connections between the PCB and components.
- RoHS compliant: OSP is compliant with the Restriction of Hazardous Substances (RoHS) directive, making it an environmentally friendly choice.
OSP PCB Application Process
The OSP application process typically involves the following steps:
- Cleaning: The PCB is thoroughly cleaned to remove any contaminants or residues that may affect the adhesion of the OSP layer.
- Micro-etching: A mild etching solution is used to remove any oxidation and create a uniform surface on the exposed copper pads.
- OSP application: The PCB is immersed in an OSP solution, which forms a thin, protective layer on the copper surface.
- Drying: The PCB is dried using hot air or infrared heating to ensure that the OSP layer is fully cured and adhered to the copper.
Factors Affecting OSP Performance
Several factors can influence the performance of OSP PCBs, including:
- Storage conditions: OSP PCBs should be stored in a cool, dry environment to prevent moisture absorption and oxidation.
- Handling: Proper handling techniques should be employed to avoid contamination or damage to the OSP layer.
- Soldering process: The soldering temperature, time, and flux compatibility should be carefully controlled to ensure optimal results.
- Shelf life: OSP has a limited shelf life, typically ranging from 6 to 12 months, depending on the specific formulation and storage conditions.
Comparing OSP to Other PCB Surface Finishes
OSP is just one of several PCB surface finishes available, each with its own advantages and disadvantages. Let’s compare OSP to some other popular surface finishes:
OSP vs. ENIG
ENIG (Electroless Nickel Immersion Gold) is a popular surface finish that offers excellent solderability and durability. However, it is more expensive than OSP and can be prone to “black pad” defects, which occur when the nickel layer separates from the copper substrate.
Characteristic | OSP | ENIG |
---|---|---|
Cost | Low | High |
Shelf life | 6-12 months | 12+ months |
Solderability | Good | Excellent |
Durability | Moderate | High |
Flatness | Excellent | Good |
OSP vs. HASL
HASL (Hot Air Solder Leveling) is a traditional surface finish that involves covering the exposed copper pads with a layer of solder. While HASL is inexpensive and offers good solderability, it can result in an uneven surface and is not suitable for fine-pitch components.
Characteristic | OSP | HASL |
---|---|---|
Cost | Low | Low |
Shelf life | 6-12 months | 12+ months |
Solderability | Good | Good |
Durability | Moderate | High |
Flatness | Excellent | Poor |
OSP vs. Immersion Silver
Immersion silver is a surface finish that provides excellent solderability and conductivity. However, it is more expensive than OSP and can be susceptible to tarnishing over time.
Characteristic | OSP | Immersion Silver |
---|---|---|
Cost | Low | Moderate |
Shelf life | 6-12 months | 12+ months |
Solderability | Good | Excellent |
Durability | Moderate | Moderate |
Flatness | Excellent | Excellent |
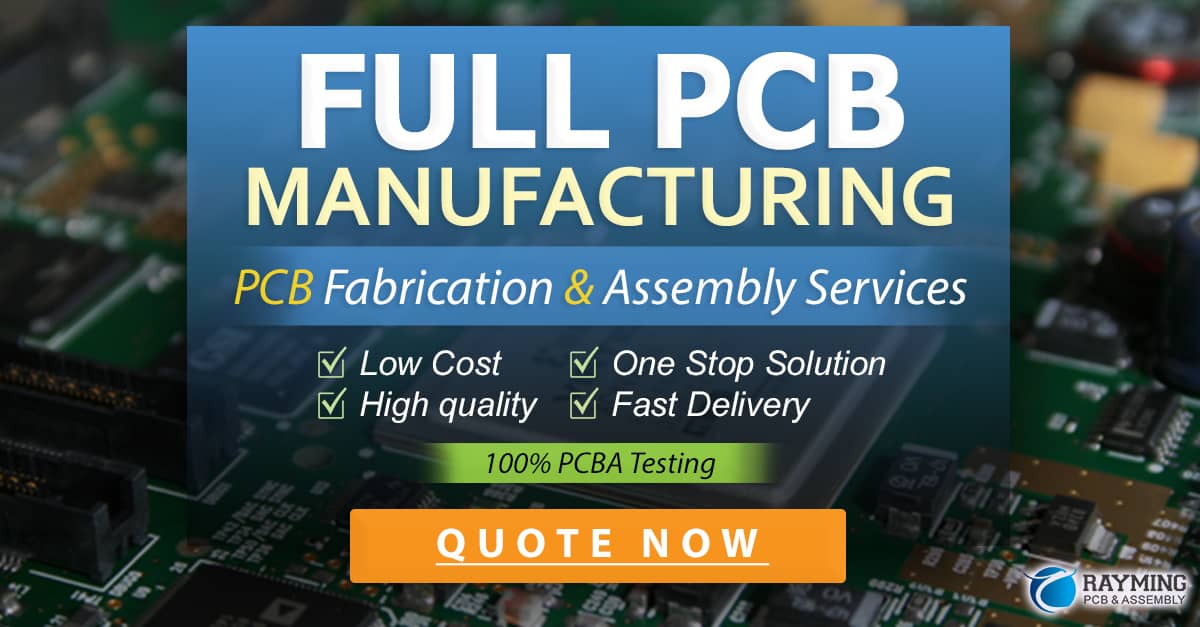
Applications of OSP PCB
OSP PCBs are widely used in various industries and applications, including:
- Consumer electronics: Smartphones, laptops, tablets, and other consumer devices often use OSP PCBs due to their cost-effectiveness and good solderability.
- Automotive electronics: OSP PCBs are used in automotive applications such as infotainment systems, engine control units, and sensors.
- Industrial electronics: OSP PCBs are employed in industrial control systems, power supplies, and automation equipment.
- Medical devices: Some medical devices, such as patient monitors and diagnostic equipment, use OSP PCBs for their reliability and cost-effectiveness.
Best Practices for Using OSP PCB
To ensure the best performance and reliability of OSP PCBs, consider the following best practices:
- Proper storage: Store OSP PCBs in a cool, dry environment with a relative humidity of 30-60% and a temperature of 20-30°C.
- Handling: Use gloves or finger cots when handling OSP PCBs to prevent contamination from skin oils and other contaminants.
- Soldering: Use a compatible solder paste and flux, and carefully control the soldering temperature and time to avoid damaging the OSP layer.
- Inspection: Regularly inspect OSP PCBs for signs of oxidation, contamination, or damage, and take corrective action as needed.
- Rework: If rework is necessary, use a low-temperature soldering iron and minimal heat to avoid damaging the OSP layer.
Future Trends in OSP PCB Technology
As PCB technology continues to advance, OSP is likely to evolve to meet the demands of new applications and manufacturing processes. Some potential future trends in OSP PCB technology include:
- Improved formulations: New OSP formulations may be developed to offer better durability, longer shelf life, and enhanced solderability.
- Compatibility with advanced packaging: OSP may be adapted to work with advanced packaging technologies such as 3D packaging and system-in-package (SiP) designs.
- Integration with additive manufacturing: As additive manufacturing techniques like 3D printing become more prevalent in PCB Fabrication, OSP may be optimized for use with these processes.
- Environmental sustainability: There may be a push for more environmentally friendly OSP formulations that minimize the use of hazardous substances and reduce waste.
Frequently Asked Questions (FAQ)
- What is the typical shelf life of OSP PCBs?
The shelf life of OSP PCBs typically ranges from 6 to 12 months, depending on the specific formulation and storage conditions. Proper storage in a cool, dry environment can help extend the shelf life of OSP PCBs.
- Can OSP be used for fine-pitch components?
Yes, OSP is well-suited for fine-pitch components due to its flat surface and thin coating. The flat surface allows for accurate placement of small components, while the thin coating ensures good solderability and minimal interference with the solder joint.
- Is OSP compatible with Lead-Free Soldering?
Yes, OSP is compatible with both lead-based and lead-free soldering processes. However, it is important to use a compatible solder paste and flux, and to carefully control the soldering temperature and time to avoid damaging the OSP layer.
- How does OSP compare to ENIG in terms of cost?
OSP is generally less expensive than ENIG, making it a more cost-effective option for high-volume production runs. The lower cost of OSP is due to the simpler application process and the use of less expensive materials compared to ENIG.
- Can OSP PCBs be reworked?
Yes, OSP PCBs can be reworked, but it is important to use a low-temperature soldering iron and minimal heat to avoid damaging the OSP layer. Proper handling and cleaning of the reworked area are also crucial to ensure the integrity of the PCB and its components.
Conclusion
OSP PCB is a popular and effective surface finish that offers a balance of cost-effectiveness, good solderability, and compatibility with a wide range of applications. By understanding the advantages, application process, and best practices associated with OSP PCBs, designers and manufacturers can make informed decisions when selecting a surface finish for their projects. As PCB technology continues to evolve, OSP is likely to remain a viable and valuable option for many applications in the electronics industry.
0 Comments