What are Multilayer PCBs?
Multilayer PCBs are printed circuit boards that consist of three or more conductive copper layers separated by insulating layers. These layers are laminated together using heat and pressure, creating a single board with multiple layers of circuitry. The number of layers can vary depending on the complexity of the circuit design, with some multilayer PCBs having up to 50 layers or more.
Number of Layers | Typical Applications |
---|---|
4-8 | Consumer electronics, industrial controls |
10-20 | Telecommunications, automotive, medical devices |
20-50+ | High-performance computing, aerospace, defense |
Advantages of Multilayer PCBs
Multilayer PCBs offer several advantages over traditional single or double-layer PCBs:
-
Increased Density: By stacking multiple layers of circuitry, multilayer PCBs can accommodate more components and connections in a smaller space, allowing for more compact and efficient designs.
-
Improved Signal Integrity: The use of ground and power planes in multilayer PCBs helps to reduce electromagnetic interference (EMI) and crosstalk, ensuring cleaner and more reliable signal transmission.
-
Enhanced Thermal Management: Multilayer PCBs can incorporate dedicated layers for heat dissipation, helping to manage the thermal requirements of high-power components and prevent overheating.
-
Greater Flexibility: The ability to route signals through multiple layers allows for more complex and Flexible Circuit Designs, accommodating various component placements and interconnections.
Manufacturing Process of Multilayer PCBs
The manufacturing process of multilayer PCBs is more complex than that of single or double-layer boards, involving several key steps:
-
Design and Layout: The circuit design is created using computer-aided design (CAD) software, which generates the necessary files for manufacturing, including Gerber files and drill files.
-
Layer Preparation: The individual layers of the PCB are prepared by printing the circuit patterns onto Copper-Clad Laminates using a photolithographic process. Each layer is etched to remove unwanted copper, leaving only the desired circuit traces.
-
Lamination: The prepared layers are stacked together with insulating layers (prepreg) between them and subjected to high pressure and temperature in a lamination press. This process fuses the layers together into a single board.
-
Drilling: Holes are drilled through the laminated board to accommodate through-hole components and create vias that connect the different layers of the PCB.
-
Plating: The drilled holes are plated with copper to establish electrical connections between layers and provide a surface for soldering components.
-
Surface Finishing: A protective surface finish, such as HASL (Hot Air Solder Leveling) or ENIG (Electroless Nickel Immersion Gold), is applied to the outer layers of the PCB to prevent oxidation and enhance solderability.
-
Solder Mask and Silkscreen: A solder mask is applied to the outer layers of the PCB to protect against short circuits and provide insulation. A silkscreen layer is then added to label components and provide assembly instructions.
-
Testing and Inspection: The completed multilayer PCB undergoes various tests and inspections to ensure its functionality, reliability, and compliance with specifications.
Applications of Multilayer PCBs
Multilayer PCBs find applications in a wide range of industries and products, including:
-
Consumer Electronics: Smartphones, tablets, laptops, gaming consoles, and wearable devices all rely on multilayer PCBs to accommodate their complex circuitry in compact form factors.
-
Telecommunications: Network equipment, routers, switches, and base stations utilize multilayer PCBs to handle high-speed data transmission and signal processing.
-
Automotive: Modern vehicles incorporate numerous electronic systems, such as infotainment, driver assistance, and engine management, which require multilayer PCBs for reliable and efficient operation.
-
Medical Devices: Multilayer PCBs are essential for medical devices like patient monitors, imaging systems, and implantable devices, where high reliability and compact size are critical.
-
Aerospace and Defense: Avionics, radar systems, and military communications equipment employ multilayer PCBs to meet the stringent requirements for performance, reliability, and durability in harsh environments.
-
Industrial Automation: Multilayer PCBs are used in industrial control systems, PLCs (Programmable Logic Controllers), and robotics to enable complex automation and process control.
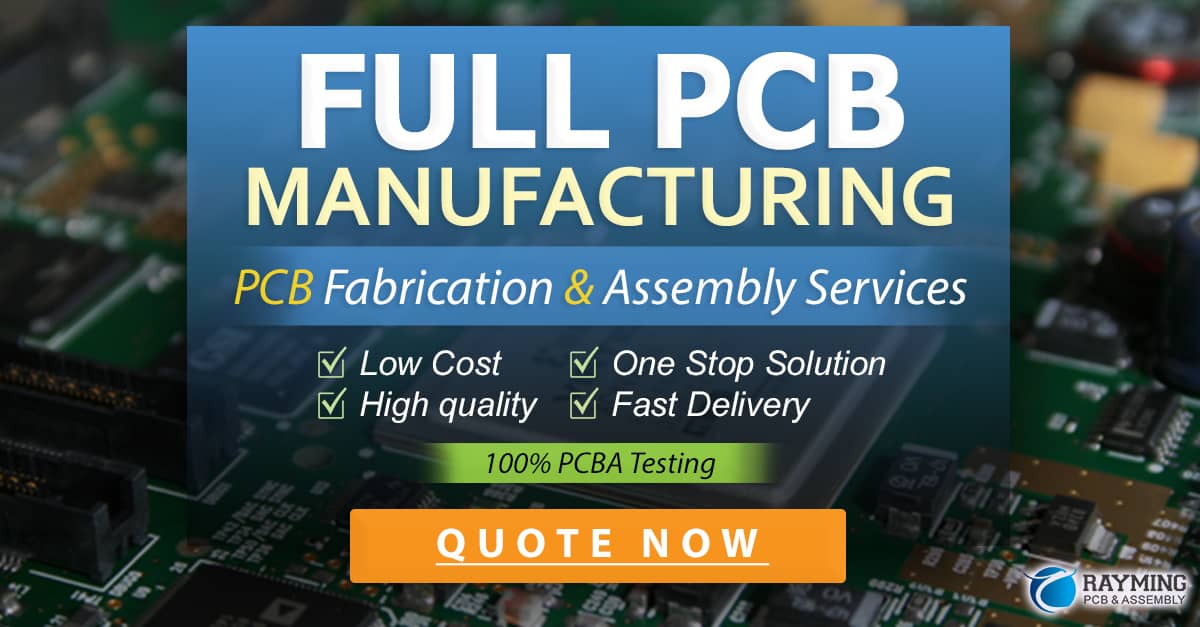
The Future of Multilayer PCBs
As electronic devices continue to become more advanced and miniaturized, the demand for multilayer PCBs is expected to grow. Several trends and developments are shaping the future of multilayer PCBs:
-
High-Density Interconnect (HDI): HDI technology allows for even greater circuit density by using smaller vias, finer trace widths, and thinner dielectric layers. This enables the development of ultra-compact and high-performance devices.
-
Embedded Components: Multilayer PCBs can incorporate passive components, such as resistors and capacitors, directly into the board layers, saving space and improving signal integrity.
-
3D Printing: Advancements in 3D printing technology may enable the production of multilayer PCBs with complex geometries and unique features, opening up new design possibilities.
-
Advanced Materials: The use of new materials, such as high-frequency laminates and low-loss dielectrics, can enhance the performance of multilayer PCBs in demanding applications like 5G communications and high-speed computing.
-
Sustainable Practices: As environmental concerns grow, the PCB industry is focusing on developing eco-friendly materials and processes, such as halogen-free laminates and lead-free soldering, to reduce the environmental impact of multilayer PCB production.
Frequently Asked Questions (FAQ)
-
Q: What is the difference between a multilayer PCB and a single-layer PCB?
A: A single-layer PCB has only one conductive layer, while a multilayer PCB has three or more conductive layers separated by insulating layers. Multilayer PCBs offer higher circuit density, better signal integrity, and improved thermal management compared to single-layer PCBs. -
Q: How many layers can a multilayer PCB have?
A: The number of layers in a multilayer PCB can vary depending on the complexity of the circuit design and the application requirements. Some multilayer PCBs can have up to 50 layers or more, although most common designs range from 4 to 20 layers. -
Q: Are multilayer PCBs more expensive than single-layer PCBs?
A: Yes, multilayer PCBs are generally more expensive than single-layer PCBs due to the additional materials, processing steps, and complexity involved in their manufacturing. However, the benefits of multilayer PCBs, such as increased functionality and space savings, often justify the higher cost for many applications. -
Q: Can multilayer PCBs be repaired if damaged?
A: Repairing a multilayer PCB can be challenging due to the complex internal structure and the difficulty in accessing the inner layers. In most cases, it is more cost-effective to replace a damaged multilayer PCB rather than attempting to repair it. -
Q: What are the challenges in designing multilayer PCBs?
A: Designing multilayer PCBs requires careful consideration of factors such as signal integrity, power distribution, EMI/EMC, and thermal management. Designers must also ensure proper layer stackup, via placement, and impedance control to achieve optimal performance. Specialized CAD tools and simulation software are often used to address these challenges and ensure a successful multilayer PCB design.
In conclusion, multilayer PCBs have become an essential component in the development of advanced electronic devices across various industries. Their ability to accommodate complex circuitry in compact form factors, improve signal integrity, and enhance thermal management makes them a key enabler for technological progress. As demands for more sophisticated and miniaturized electronics continue to grow, multilayer PCBs are poised to play an increasingly important role in shaping the future of electronics.
0 Comments