Introduction to Multilayer PCBs
Printed Circuit Boards (PCBs) have revolutionized the electronics industry by providing a reliable and efficient way to connect electronic components. As technology advances and devices become more complex, the need for high-density interconnections and compact designs has led to the development of multilayer PCBs. This article will dive deep into the world of multilayer PCBs, exploring their structure, manufacturing process, advantages, and applications.
What is a Multilayer PCB?
A multilayer PCB is a printed circuit board that consists of three or more conductive layers bonded together with insulating layers in between. These layers are interconnected using plated through-holes (vias) that allow signals to pass from one layer to another. Multilayer PCBs offer higher component density, improved signal integrity, and better electromagnetic compatibility compared to single or double-layer boards.
Structure of a Multilayer PCB
A typical multilayer PCB consists of the following layers:
-
Copper layers: These are the conductive layers that carry electrical signals and power. The number of copper layers can vary depending on the complexity of the design, ranging from 4 to 12 or more.
-
Insulating layers: Also known as substrate or dielectric layers, these are non-conductive materials that separate the copper layers. The most common insulating materials are FR-4, Rogers, and Polyimide.
-
Solder mask: A thin layer of polymer applied on top of the outer copper layers to protect them from oxidation and prevent Solder Bridging during assembly.
-
Silkscreen: A layer of text and symbols printed on the solder mask to identify components, test points, and other information.
Layer | Material | Thickness (mm) |
---|---|---|
Copper | Copper foil | 0.018 – 0.07 |
Insulating | FR-4, Rogers, Polyimide | 0.1 – 0.5 |
Solder Mask | Epoxy or acrylic-based polymer | 0.01 – 0.03 |
Silkscreen | Epoxy or acrylic-based ink | 0.01 – 0.03 |
Advantages of Multilayer PCBs
-
Higher component density: Multilayer PCBs allow for more components to be placed on a smaller board, reducing the overall size and weight of the device.
-
Improved signal integrity: By separating signals on different layers and using proper grounding and shielding techniques, multilayer PCBs can minimize crosstalk, noise, and electromagnetic interference (EMI).
-
Better thermal management: The increased number of copper layers helps to dissipate heat more efficiently, preventing components from overheating.
-
Enhanced reliability: Multilayer PCBs are less susceptible to mechanical stress and vibration, making them more reliable in harsh environments.
Manufacturing Process of Multilayer PCBs
The manufacturing process of multilayer PCBs involves several steps, each requiring precision and attention to detail.
Step 1: Design and Layout
The first step in manufacturing a multilayer PCB is to create a design using Electronic Design Automation (EDA) software. The designer must consider factors such as component placement, signal routing, power distribution, and manufacturability. The output of this step is a set of Gerber files that contain the information needed to fabricate the board.
Step 2: Inner Layer Fabrication
The inner layers of the multilayer PCB are fabricated separately using a process called photolithography. The steps involved are:
-
Cleaning: The copper-clad laminate is cleaned to remove any contaminants.
-
Photoresist application: A light-sensitive polymer called photoresist is applied evenly on both sides of the laminate.
-
Exposure: The photoresist is exposed to UV light through a photomask that contains the desired pattern for the layer.
-
Developing: The exposed photoresist is removed using a developer solution, leaving behind the desired pattern.
-
Etching: The unwanted copper is removed using an etchant solution, leaving behind the copper traces that form the circuit pattern.
-
Stripping: The remaining photoresist is stripped off, leaving behind the finished inner layer.
Step 3: Layer Stacking and Lamination
The fabricated inner layers are stacked together with prepreg (pre-impregnated) insulating layers in between. The stack is then placed in a lamination press, where heat and pressure are applied to bond the layers together. The result is a solid, multi-layered board.
Step 4: Drilling and Plating
After lamination, holes are drilled through the board to allow for component placement and layer interconnection. The holes are then plated with copper to create electrical connections between layers. This process is called through-hole plating.
Step 5: Outer Layer Fabrication
The outer layers of the PCB are fabricated using the same photolithography process as the inner layers. However, additional steps are involved, such as applying the solder mask and silkscreen.
Step 6: Surface Finishing
The final step in the manufacturing process is to apply a surface finish to the exposed copper areas to protect them from oxidation and enhance solderability. Common surface finishes include:
- Hot Air Solder Leveling (HASL)
- Electroless Nickel Immersion Gold (ENIG)
- Immersion Silver
- Immersion Tin
- Organic Solderability Preservative (OSP)
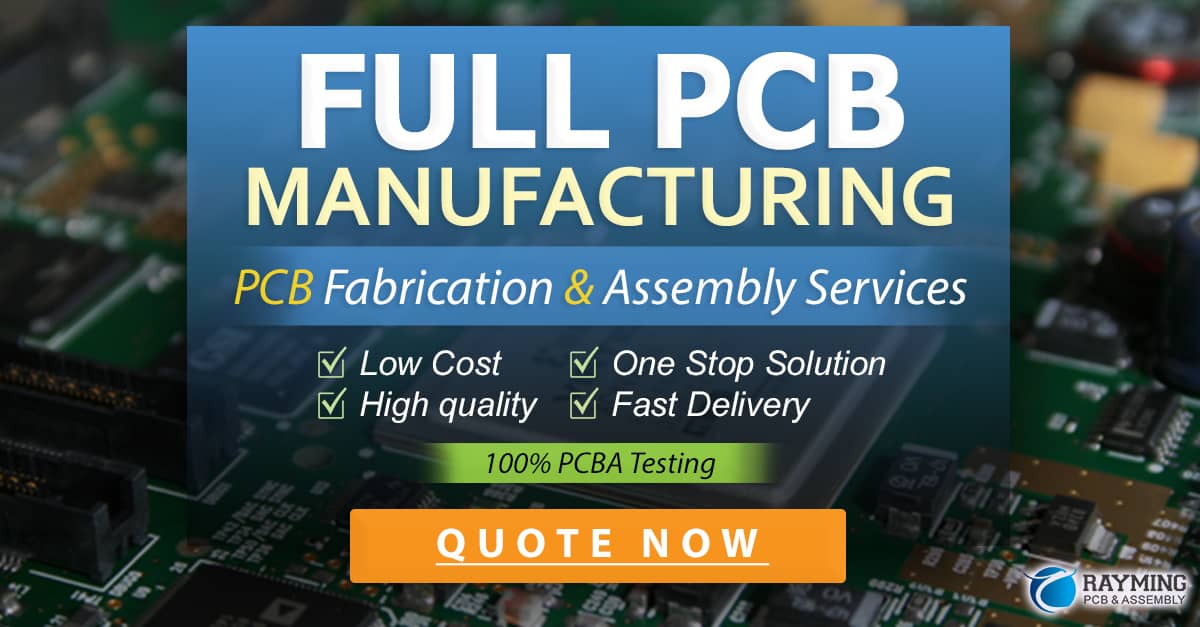
Applications of Multilayer PCBs
Multilayer PCBs find applications in a wide range of industries due to their high-density interconnections, improved signal integrity, and compact designs. Some of the major applications include:
Consumer Electronics
Multilayer PCBs are extensively used in consumer electronics such as smartphones, tablets, laptops, and wearables. The high component density and compact form factor of multilayer PCBs enable manufacturers to create sleek and feature-rich devices.
Automotive Electronics
The automotive industry relies heavily on multilayer PCBs for various electronic systems, such as engine control units (ECUs), infotainment systems, and advanced driver assistance systems (ADAS). The robust construction and reliability of multilayer PCBs make them suitable for the harsh operating conditions in vehicles.
Medical Devices
Medical devices, such as implantable devices, diagnostic equipment, and monitoring systems, require high-reliability PCBs that can operate in sensitive environments. Multilayer PCBs, with their improved signal integrity and EMI Shielding, are well-suited for these applications.
Aerospace and Defense
Multilayer PCBs are used in aerospace and defense applications, such as avionics, radar systems, and satellite communication devices. The ability to withstand extreme temperatures, vibrations, and shock makes multilayer PCBs a preferred choice for these mission-critical applications.
Industrial Automation
Industrial automation systems, such as programmable logic controllers (PLCs), human-machine interfaces (HMIs), and sensors, rely on multilayer PCBs for their high-speed data processing and reliable operation in harsh industrial environments.
Frequently Asked Questions (FAQ)
1. What is the maximum number of layers that can be used in a multilayer PCB?
There is no theoretical limit to the number of layers in a multilayer PCB. However, in practice, most PCBs have between 4 and 12 layers. Some advanced designs may use up to 50 layers or more, but these are rare and expensive to manufacture.
2. What is the difference between a Through-hole via and a blind via?
A through-hole via is a plated hole that goes through all layers of the PCB, connecting the top and bottom layers. A blind via, on the other hand, connects an outer layer to an inner layer without going through the entire board. Blind vias are used to save space and improve signal integrity.
3. Can multilayer PCBs be flexible?
Yes, multilayer PCBs can be made flexible by using flexible substrates such as polyimide or polyester. Flexible multilayer PCBs are used in applications that require the board to bend or flex, such as wearable devices or foldable displays.
4. How does the number of layers affect the cost of a multilayer PCB?
The cost of a multilayer PCB increases with the number of layers due to the increased complexity of the manufacturing process. Each additional layer requires more materials, processing steps, and testing, leading to higher costs. However, the cost per unit area may decrease with higher volumes due to economies of scale.
5. What are the challenges in designing and manufacturing multilayer PCBs?
Designing and manufacturing multilayer PCBs comes with several challenges, such as ensuring proper signal integrity, managing Thermal dissipation, and maintaining manufacturability. Other challenges include minimizing crosstalk and EMI, selecting the right materials for the application, and ensuring reliable plated through-holes. Overcoming these challenges requires careful design, simulation, and collaboration between the designer and the manufacturer.
Conclusion
Multilayer PCBs have become an essential part of modern electronics, enabling high-density interconnections, improved signal integrity, and compact designs. The manufacturing process of multilayer PCBs involves several steps, each requiring precision and attention to detail. From consumer electronics to aerospace and defense, multilayer PCBs find applications in a wide range of industries due to their reliability, robustness, and performance.
As technology continues to advance, the demand for multilayer PCBs with higher layer counts, finer features, and advanced materials will only increase. Designers and manufacturers must stay up-to-date with the latest trends and technologies to meet the ever-growing demands of the electronics industry. By understanding the fundamentals of multilayer PCBs and their manufacturing process, engineers can design and develop innovative products that push the boundaries of what is possible.
0 Comments