What is Mixed Assembly and How Does it Benefit Manufacturing?
Mixed assembly is a manufacturing process that combines both automated and manual assembly techniques to create a more efficient and cost-effective production line. This approach takes advantage of the strengths of both methods while minimizing their weaknesses, resulting in improved product quality, increased production speed, and reduced costs.
Advantages of Automated Assembly
Automated assembly relies on machines, robots, and other automated systems to perform tasks that are repetitive, precise, and require high speed. Some of the key advantages of automated assembly include:
- Increased production speed
- Improved accuracy and consistency
- Reduced labor costs
- Enhanced safety for workers
- 24/7 operation capabilities
Advantages of Manual Assembly
Manual assembly involves human workers performing tasks that require dexterity, flexibility, and problem-solving skills. Some of the main advantages of manual assembly include:
- Adaptability to changes in product design or production requirements
- Ability to handle delicate or complex components
- Faster setup times for small batches or custom orders
- Lower initial investment compared to fully automated systems
- Valuable human insight and decision-making capabilities
Combining the Best of Both Worlds
Mixed assembly leverages the strengths of both automated and manual assembly to create a more efficient and flexible production process. By strategically allocating tasks to either machines or human workers based on their respective advantages, manufacturers can optimize their production lines to achieve the best possible results.
Example of Mixed Assembly in Action
Consider a company that manufactures electronic devices. In a mixed assembly setup, the production line might look something like this:
- Automated systems place small components, such as resistors and capacitors, onto printed Circuit Boards (PCBs) with high speed and precision.
- Human workers manually insert larger or more delicate components, such as connectors and displays, that require careful handling and alignment.
- Automated soldering machines create secure connections between components on the PCBs.
- Human workers perform visual inspections and functional tests to ensure product quality and catch any defects.
- Automated packaging systems seal and label the finished products for shipping.
By using this mixed assembly approach, the company can take advantage of the speed and accuracy of automated systems for repetitive tasks while leveraging the flexibility and problem-solving skills of human workers for more complex or variable tasks.
Benefits of Mixed Assembly for Manufacturers
Implementing a mixed assembly process offers several key benefits for manufacturers, including:
1. Increased Efficiency and Productivity
By optimizing the allocation of tasks between machines and human workers, mixed assembly can significantly increase the overall efficiency and productivity of a production line. Automated systems can perform repetitive tasks at high speeds, while human workers can focus on tasks that require more flexibility and adaptability.
2. Improved Product Quality
Mixed assembly can help improve product quality by leveraging the strengths of both automated and manual processes. Automated systems ensure consistent and precise placement of components, while human workers can perform visual inspections and catch any defects that machines might miss.
3. Reduced Costs
Implementing a mixed assembly process can help manufacturers reduce costs in several ways. Automated systems can reduce labor costs for repetitive tasks, while human workers can provide valuable insight and problem-solving skills that can help optimize production processes and minimize waste.
4. Enhanced Flexibility
Mixed assembly allows manufacturers to be more flexible in their production processes. Human workers can quickly adapt to changes in product design or production requirements, while automated systems can be reprogrammed or reconfigured to handle new tasks or products.
5. Improved Safety for Workers
By allocating dangerous or repetitive tasks to automated systems, mixed assembly can help improve safety for human workers. This reduces the risk of workplace injuries and creates a more ergonomic and comfortable working environment.
Implementing Mixed Assembly in Your Manufacturing Process
To successfully implement a mixed assembly process in your manufacturing operation, consider the following steps:
1. Analyze Your Current Production Process
Start by thoroughly analyzing your current production process to identify tasks that are suitable for automation and those that require human intervention. Consider factors such as task complexity, variability, and the need for flexibility or problem-solving skills.
2. Develop a Strategic Plan
Based on your analysis, develop a strategic plan for implementing mixed assembly in your production line. This plan should include:
- Specific tasks to be automated and those to be performed by human workers
- Required equipment, software, and infrastructure investments
- Training and education for your workforce
- Timeline for implementation and expected milestones
- Metrics for measuring success and identifying areas for improvement
3. Invest in the Right Technology and Equipment
To successfully implement mixed assembly, you’ll need to invest in the right technology and equipment. This may include:
- Automated systems, such as robots, conveyor belts, and vision systems
- Software for programming and controlling automated systems
- Sensors and monitoring devices for ensuring process efficiency and product quality
- Ergonomic workstations and tools for human workers
4. Train and Educate Your Workforce
Providing proper training and education for your workforce is critical to the success of your mixed assembly implementation. This may include:
- Training on new equipment, software, and processes
- Education on the benefits and goals of mixed assembly
- Encouraging open communication and collaboration between human workers and automated systems
- Providing opportunities for continuous learning and skill development
5. Continuously Monitor and Optimize
Implementing mixed assembly is an ongoing process that requires continuous monitoring and optimization. Regularly review your production metrics, gather feedback from your workforce, and identify areas for improvement. Be prepared to make adjustments and refinements as needed to ensure the best possible results.
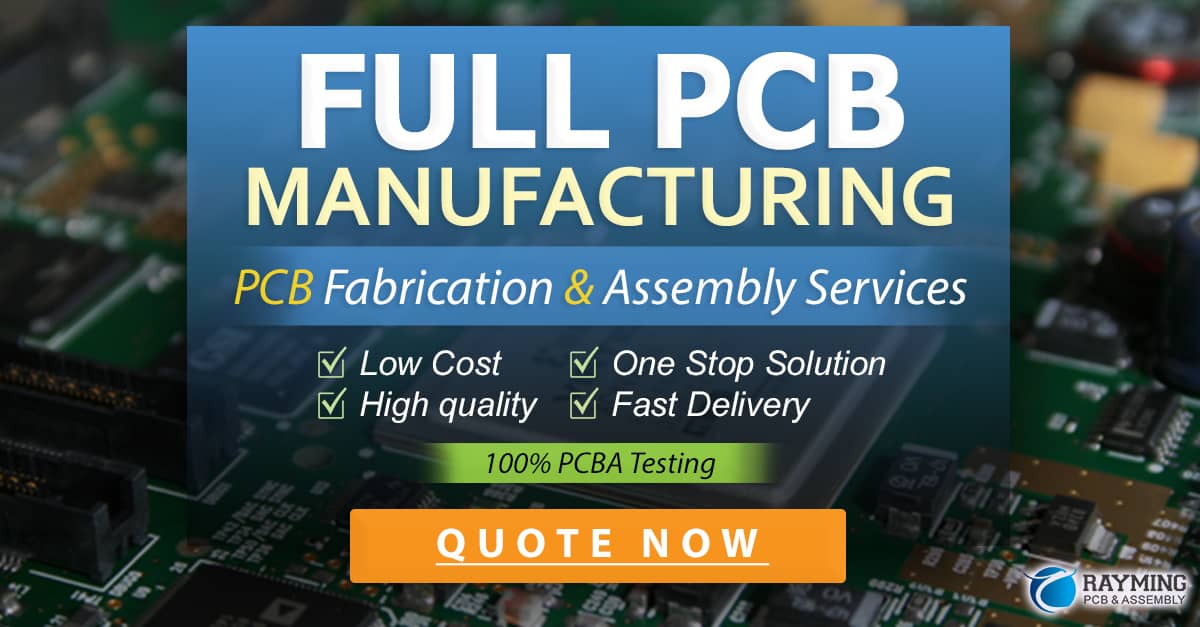
Real-World Examples of Mixed Assembly Success
Many companies across various industries have successfully implemented mixed assembly processes to improve efficiency, reduce costs, and enhance product quality. Here are a few examples:
1. Toyota
Toyota, the world’s largest automaker, has long been a pioneer in mixed assembly. The company’s famous Toyota Production System (TPS) combines automated systems with human workers to create a highly efficient and flexible manufacturing process. By leveraging the strengths of both machines and people, Toyota has consistently produced high-quality vehicles while minimizing waste and costs.
2. Apple
Apple, the world’s most valuable technology company, relies on mixed assembly to produce its iconic iPhones and other devices. The company’s manufacturing partners, such as Foxconn, use a combination of automated systems and human workers to assemble the various components of each device. This approach allows Apple to maintain high product quality while also adapting quickly to changes in design or demand.
3. Boeing
Boeing, the world’s largest aerospace company, uses mixed assembly to build its commercial airplanes and defense products. The company’s production lines feature a mix of automated systems, such as robots for drilling and riveting, and skilled human workers for more complex tasks, such as wiring and final assembly. This approach helps Boeing achieve the precision and efficiency needed to produce safe and reliable aircraft.
Frequently Asked Questions (FAQ)
1. What types of products are best suited for mixed assembly?
Mixed assembly can be applied to a wide range of products, from simple consumer goods to complex industrial equipment. However, it is particularly well-suited for products that require a mix of repetitive and variable tasks, such as:
- Electronics and appliances
- Automotive components and vehicles
- Medical devices and equipment
- Aerospace and defense products
- Consumer packaged goods
2. How much does it cost to implement mixed assembly?
The cost of implementing mixed assembly varies depending on factors such as the size and complexity of your production line, the types of equipment and technology needed, and the training and education required for your workforce. While there may be significant upfront costs for investing in automation and other infrastructure, the long-term benefits of mixed assembly, such as increased efficiency and reduced labor costs, can often offset these initial investments.
3. How long does it take to implement mixed assembly?
The timeline for implementing mixed assembly depends on the scope and complexity of your project, as well as the readiness of your organization. A small-scale implementation may take just a few weeks, while a larger, more complex project could take several months or even years. It’s essential to develop a realistic timeline as part of your strategic plan and to allow for adequate time for testing, refining, and optimizing your new processes.
4. What skills do human workers need for mixed assembly?
Human workers in a mixed assembly environment need a combination of technical and soft skills, such as:
- Familiarity with automated systems and software
- Ability to perform complex or variable tasks that require dexterity and problem-solving
- Strong communication and collaboration skills for working alongside machines and other team members
- Adaptability and willingness to learn new skills and processes
- Attention to detail and commitment to quality
5. How can mixed assembly help with mass customization?
Mixed assembly is well-suited for supporting mass customization, which involves producing products that are tailored to individual customer preferences while maintaining the efficiency and cost-effectiveness of mass production. By leveraging the flexibility and adaptability of human workers alongside the speed and precision of automated systems, manufacturers can quickly and efficiently produce a wide variety of customized products to meet the unique needs of each customer.
Conclusion
Mixed assembly is a powerful approach to manufacturing that combines the strengths of both automated and manual processes to create a more efficient, flexible, and cost-effective production line. By strategically allocating tasks to either machines or human workers based on their respective advantages, manufacturers can optimize their production processes to achieve improved product quality, increased production speed, and reduced costs.
Implementing mixed assembly requires careful planning, investment in the right technology and equipment, and ongoing training and education for your workforce. However, the benefits of this approach, as demonstrated by successful examples from companies like Toyota, Apple, and Boeing, can be significant and long-lasting.
As the manufacturing landscape continues to evolve, with increasing demands for customization, flexibility, and efficiency, mixed assembly will likely play an increasingly important role in helping companies stay competitive and meet the needs of their customers. By embracing this approach and continuously optimizing their processes, manufacturers can position themselves for success in the years to come.
0 Comments