Introduction
Printed circuit boards (PCBs) are an essential component of most electronic devices and products. As products become more advanced and miniaturized, PCBs have become more complex, requiring tighter tolerances and more layers. This increased complexity makes PCB manufacturing more challenging, especially for low volume production runs.
Low volume PCB production typically refers to batch sizes of 10-100 boards. At these quantities, traditional mass production techniques become inefficient and expensive on a per board basis. Therefore, a different manufacturing approach is required to produce affordable and high-quality low volume PCBs.
This guide will provide a complete overview of low volume PCB manufacturing, covering topics such as:
- The benefits and challenges of low volume PCB production
- Key factors to consider when selecting a low volume PCB manufacturer
- Common low volume PCB manufacturing techniques
- How to design for manufacturability at low volumes
- Cost drivers and how to minimize costs
- Quality control and testing
- Final considerations when ordering low volume PCBs
Properly approaching low volume PCB manufacturing requires an understanding of the entire process. With the right knowledge, even complex boards can be produced affordably in small batches.
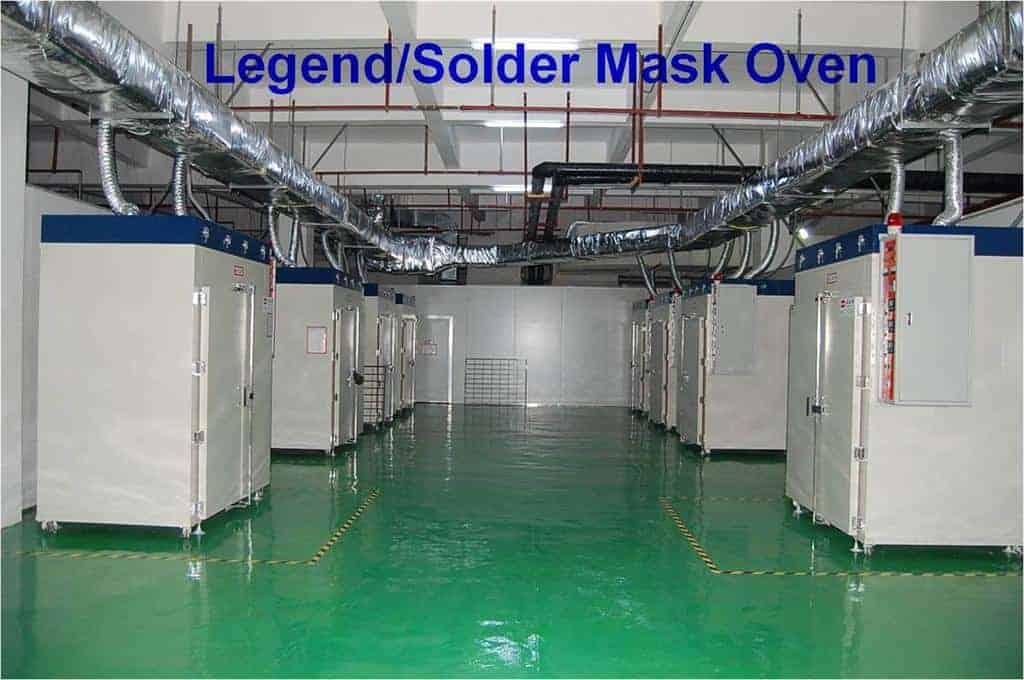
Benefits and Challenges of Low Volume PCB Production
Low volume PCB production provides several advantages over high volume manufacturing:
Faster time-to-market: Low volumes allow products to be designed, prototyped, and brought to market rapidly without requiring large production tooling and high NRE (non-recurring engineering) costs. This enables faster field testing, validation, and end-user feedback.
Design flexibility: Design changes are much easier and cheaper to implement at lower volumes. This allows for more design iterations and optimizations before finalizing a design for mass production.
Lower inventory costs: With small batch sizes, inventory costs are minimized and less working capital is tied up. This reduces financial risk, especially for new products.
Cost effective prototyping: Producing 10-100 boards is ideal for design verification, prototyping, field trials and other activities prior to mass production.
No volume commitments: Low volume services do not require firm commitments to high production quantities in order to get favorable pricing.
However, low volume PCB production also comes with some key challenges:
- Higher per unit costs: With small batches, the fixed costs of production are amortized over fewer boards, increasing the per board cost. Economies of scale are not achievable.
- Process limitations: Not all manufacturing capabilities and tolerances are available at low volumes. Some advanced processes require high volume production.
- Potential quality issues: With shorter production runs, maintaining quality and consistency can be harder. Risk of defects and variability is increased.
- Higher touch labor: More manual preparation and handling is required for short runs, increasing labor costs. Automation optimized for high volumes is less feasible.
- Increased process management: Switching between small batch orders must be coordinated to maximize efficiency and avoid errors.
Understanding these tradeoffs enables smart compromises and decisions when manufacturing low volumes of PCBs.
Key Factors When Selecting a Low Volume PCB Manufacturer
Choosing the right PCB manufacturer is critical for successfully producing low volume boards. Here are key factors to evaluate potential vendors:
Low volume expertise & capabilities
Look for manufacturers that specialize in low volume boards and have optimized their processes, equipment, and quality systems accordingly. They should understand the unique challenges and how to address them.
Range of available capabilities
Evaluate capabilities like number of layers, minimum feature sizes, substrate types, tolerances, finishes, lead times, and other parameters. Find a supplier able to meet all your technical requirements.
Quality certifications
Relevant quality standards like ISO 9001 and environmental certifications like ISO 14001 should be met. This ensures consistent quality processes are in place.
Responsive customer service
Good communication and customer service is essential for low volume orders. Prioritize vendors that provide excellent technical support and account management.
Flexible order quantities
Suppliers should be able to accommodate the exact quantity needed at a reasonable cost. There shouldn???t be high minimum order sizes.
Value-added services
Additional services like design for manufacturing (DFM) reviews, prototyping, assembly, and testing reduce overall project timelines and risks.
Competitive pricing
Get detailed quotations and compare. Be wary of prices that seem too low, as quality and service may suffer. Seek the best balance of cost, capabilities, and quality.
Selecting based on these criteria will help identify the best partner for delivering high-quality, cost-effective low volume PCB production.
Common Low Volume PCB Manufacturing Techniques
Achieving the technical capabilities, quality, and cost targets required for low volume PCBs depends heavily on the manufacturing techniques used. Here are some of the most common methods:
Laser Direct Imaging (LDI)
Laser direct imaging uses a laser to selectively expose the copper laminate, eliminating the need for physical photo tools. This allows quick and easy changes to circuit patterns and rapid turnaround of small batches. LDI is one of the most common processes for low volume PCBs.
Printed Circuit Board Plotters
Plotters use a mechanical milling technique to remove copper foil, tracing the desired circuit patterns. While slower than laser methods, this allows even the smallest volumes to be produced without high mask tooling costs.
Photolithographic Methods
Conventional photolithographic processes use ultraviolet light to transfer a mask pattern to a photosensitive material on the copper laminate. While more efficient for high volumes, liquid photoresists and cleanrooms enable small scale batches.
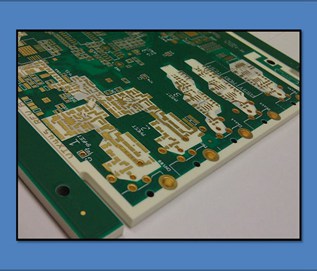
Semi-Additive and Subtractive Etching
Semi-additive techniques first pattern and electroplate only the required copper before etching to isolate circuits. This provides better tolerances and line resolution than full subtractive etching while using less copper than a full additive process.
Multi-Up Panelization
Grouping multiple small PCB designs together on a larger panel that is then split apart after manufacturing reduces handling and tooling costs compared to processing boards individually.
Manual Assembly and Rework
Automated assembly lines are not practical for assembling a small number of boards. Instead, skilled operators will manually place and solder components. Re-working any defects is also done manually.
The combination of techniques used depends on the PCB requirements, tolerances, and cost targets. An experienced low volume manufacturer will assess design needs and select an optimal process plan.
Key Manufacturing Capabilities Comparison
Capability | Mass Production | Low Volume |
---|---|---|
Minimum Feature Size | 3 mils | 8 mils |
Layers | 20+ | 6-8 |
Tolerances | +/- 0.5 mils | +/- 5 mils |
Lead Time | ~8-10 weeks | ~5-10 days |
Starts Costs | $10k+ | <$1k |
Unit Price | Low | Higher |
This table summarizes how the manufacturing capabilities differ between traditional mass production methods and low volume techniques optimized for small batches. Lower volumes tradeoff some technical capabilities for much faster turnaround and lower costs.
Designing PCBs for Low Volume Manufacturability
To achieve good yield and quality at low volumes, the PCB layouts must be designed while keeping manufacturability in mind. Here are some key design considerations:
Provide adequate spacing
Use larger spaces between traces and pads than the minimum. This accounts for greater process variability. A good rule of thumb is at least 8 mil clearance for designs with 8 mil trace/space.
Limit panelization requirements
Stacking tiny PCBs together on panels requires very accurate CNC machining to isolate the boards. Design panelizable blocks as large as possible.
Use restraining tabs
Add tabs to hold boards in the panel during depanelization to prevent shifting and cracking.
Avoid tiny and odd-shaped cutouts
Small holes and intricate internal cutouts are prone to filling in or being misshaped. Consider breaking up large cutouts into multiple smaller openings.
Ease tolerances where possible
Identify where looser tolerances are acceptable and specify accordingly to reduce cost. This gives the manufacturer more process leeway.
Minimize layer count
While possible, each additional layer compounds alignment complexity and tolerances for drilling, lamination, and vias. Keep layer count as low as feasible.
Check design manufacturability
Have your manufacturer review the design. They can catch any areas of concern early and suggest improvements for better yield and reliability.
By designing with low volume manufacturability in mind from the outset, PCB fabrication and assembly is easier, faster, and more cost effective.
Cost Drivers and How to Minimize PCB Costs
When manufacturing PCBs in low volumes, costs per board are higher so it???s important to minimize expenses where possible. Here are some of the biggest cost factors and ways to reduce them:
Board size – Minimize dimensions and consolidate space usage to allow more boards per panel.
Layer count ??? Require the fewest number of conductive layers needed for the design to reduce materials and lamination costs.
Fine features ??? Wider trace/space allows looser tolerances and simpler imaging. Specify larger features unless tight precision is mandatory.
Solder mask ??? Skip solder mask if not essential for your design to reduce processing steps and materials.
Surface finishing ??? Standard HASL lead-free hot air solder leveling is lowest cost. Other finishes add expense.
Panel utilization ??? Optimize board shapes and quantities per panel to use as much of the panel area as possible and reduce waste.
Testing and inspection ??? Perform only the critical quality checks needed to validate your product, such as basic electrical testing.
Lead time – Allow longer lead times of 1-2 weeks to enable more batching and optimization of manufacturing.
Order volumes ??? Because of high recurring costs per batch, increasing order quantities reduces the cost per board significantly. Plan for extra boards or combining orders.
Location of manufacturer ??? Locating the supplier near you minimizes shipping, duties, and inventory costs.
Taking the time to optimize the design and order specifics for low cost, quality, and delivery is an essential exercise. Work closely with your PCB manufacturer early in the design stage to implement cost saving strategies.
Quality Control and Testing for Low Volume PCBs
Maintaining quality and consistency at low production volumes can be challenging. Here are some of the key processes used to ensure each small batch meets specifications:
- Material traceability – Rigorously track copper clad laminate, soldermasks, and other base materials used in each lot. Maintain detailed records of material types, sizes, and suppliers.
- Process control ??? Standardize and monitor key parameters like exposure times, chemical concentrations, temperatures, and machine settings. Control variability within tested limits.
- Frequent calibration ??? More frequently calibrate imagers, etching tools, test equipment, and other instruments to maintain precision despite low usage.
- Visual inspection – Thoroughly visually inspect every PCB under magnification. Check features like track width, spacing, alignment, soldermask application, etc.
- Automated optical inspection (AOI) ??? Use AOI tools to scan boards and precisely measure size, position, and other parameters against the CAD data to catch defects.
- Test point coupon – Include test point grids, spaces, and vias on panels specifically for quality checks via flying probe or bed-of-nails testers.
- Random sampling – Statistically evaluate 1-2 boards per batch through additional detailed inspection and testing to confirm process stability.
- Documentation – Meticulously record the results and all parameters of every low volume manufacturing run for traceability and analysis.
With diligent quality processes tailored for low volume production, PCB quality and repeatability can match that of higher volume batches.
Final Considerations When Ordering Low Volume PCBs
To ensure you receive the best boards in the fastest time at the lowest prices, keep these final tips in mind when procuring low volume PCB manufacturing services:
- Share your expectations upfront ??? Clearly communicate with your supplier about target cost, tolerances, lead times, and any other requirements at the start.
- Design for manufacturability ??? Optimize your PCB layouts as discussed earlier to avoid production issues and maximize yield.
- Plan ahead – Confirm production lead times and schedule well in advance to avoid expedite fees. Leaving time for potential re-spins is wise.
- Provide manufacturer a meaningful forecast ??? Even if not committed orders, share your expected usage over the coming ~6 months so the supplier can plan capacities.
- Check certifications and quality processes ??? Ask details about the manufacturer???s capabilities, equipment, quality systems, and certifications to ensure they can deliver the quality you need.
- Nurture the relationship – Develop a good relationship with your supplier’s engineering and account management team for strong communications and support.
- Expect changes ??? Be prepared to update designs and improve manufacturability as needed through the prototyping process for the optimal final result.
Finding the right PCB manufacturing partner equipped for low volume production and closely collaborating with them will lead to successful procurement of even complex printed circuit boards in small batches.
Frequently Asked Questions
What volume is considered “low volume” for PCB manufacturing?
Low volume PCB production generally refers to quantities of 10 boards per batch on the low end up to about 100 boards per batch on the high side. Some manufacturers may extend this to a maximum of about 500 boards. Above that volume, other higher volume techniques become more efficient.
What are some key disadvantages of low volume PCB production?
The main drawbacks are higher per unit costs due to lack of economies of scale, more difficult process control leading to greater variability, more manual labor requirements, and limitations on some advanced manufacturing capabilities needed for very sophisticated boards.
How long is the typical lead time for low volume PCB orders?
Lead times for low volume batches are typically between 5 and 10 working days on average. For complex boards requiring more fabrication steps, lead times could extend up to 15 working days. Prototyping services supporting very fast 3-5 day turnaround are also available.
What design and order options help reduce costs for low volume PCBs?
Using looser tolerances, fewer layers, larger features, skipping soldermask and certain finishes whenever possible, maximizing panel utilization, standard lead times, and increasing quantities will all help drive down costs for low volume PCB production.
What key quality processes do low volume PCB manufacturers implement?
Frequent calibration, detailed material and parameter record keeping, extensive visual inspection of every board, automated optical inspection against the original CAD files, test point coupons, and rigorous sampling help maintain quality despite the challenges of low volume production.
0 Comments