What is a Land Pattern?
A land pattern, also known as a footprint or pad layout, is the arrangement of copper pads and other features on a printed circuit board (PCB) that allows components to be soldered onto the board. The Land Pattern Design is crucial for ensuring proper electrical connections, mechanical stability, and manufacturability of the PCB Assembly.
Key Elements of a Land Pattern
- Pad size and shape
- Pad spacing
- Solder mask opening
- Solder paste stencil aperture
- Courtyard and keepout areas
Industry Standards for Land Pattern Design
To ensure compatibility and reliability, land patterns should be designed according to industry standards. The most widely recognized standards organizations for PCB design include:
- IPC (Association Connecting Electronics Industries)
- JEDEC (Joint Electron Device Engineering Council)
- EIA (Electronic Industries Alliance)
IPC Standards
IPC provides a comprehensive set of standards for PCB design, including land pattern design. The most relevant IPC standards for land patterns are:
- IPC-7351: Generic Requirements for Surface Mount Design and Land Pattern Standard
- IPC-7093: Design and Assembly Process Implementation for Bottom Termination Components
IPC-7351 Land Pattern Naming Convention
IPC-7351 defines a standardized naming convention for land patterns, which includes the following elements:
Element | Description |
---|---|
Component Type | A two-letter code indicating the component type (e.g., “IC” for integrated circuit) |
Pitch | The distance between the centers of adjacent pads, expressed in millimeters |
Pad Width | The width of the component pads, expressed in millimeters |
Pad Length | The length of the component pads, expressed in millimeters |
Height | The height of the component, expressed in millimeters |
Example: IC-0.5-0.3-0.7-1.0 represents an integrated circuit with a pitch of 0.5 mm, pad width of 0.3 mm, pad length of 0.7 mm, and a height of 1.0 mm.
Designing Land Patterns for Different Component Types
Surface Mount Devices (SMDs)
SMDs are the most common type of component in modern PCB assemblies. They are mounted directly onto the surface of the PCB without through-holes. Common SMD component types include:
- Chip components (resistors, capacitors, inductors)
- SOT (Small Outline Transistor) packages
- QFP (Quad Flat Pack) packages
- BGA (Ball Grid Array) packages
Chip Component Land Patterns
Chip components are the smallest and simplest SMDs. Their land patterns typically consist of two rectangular pads, with the pad size and spacing determined by the component size and the requirements of the soldering process.
Table: Recommended Land Pattern Dimensions for Chip Components (IPC-7351)
Component Size | Pad Width (mm) | Pad Length (mm) | Pad Spacing (mm) |
---|---|---|---|
0201 | 0.25 | 0.35 | 0.30 |
0402 | 0.50 | 0.70 | 0.50 |
0603 | 0.90 | 1.00 | 0.80 |
0805 | 1.15 | 1.45 | 1.00 |
1206 | 1.60 | 2.00 | 1.50 |
QFP Land Patterns
QFP packages have leads on all four sides of the component body. The land pattern for a QFP consists of a row of rectangular pads along each side of the package, with the pad size and spacing determined by the lead pitch and the soldering process requirements.
Table: Recommended Land Pattern Dimensions for QFP Packages (IPC-7351)
Pitch (mm) | Pad Width (mm) | Pad Length (mm) | Pad Spacing (mm) |
---|---|---|---|
0.40 | 0.20 | 1.00 | 0.20 |
0.50 | 0.25 | 1.20 | 0.25 |
0.65 | 0.30 | 1.50 | 0.35 |
0.80 | 0.40 | 1.80 | 0.40 |
1.00 | 0.50 | 2.20 | 0.50 |
Through-Hole Components
Through-hole components have leads that are inserted into holes drilled in the PCB and soldered to pads on the opposite side of the board. Common through-hole component types include:
- DIP (Dual Inline Package) packages
- Connectors
- Electrolytic capacitors
- Transformers
DIP Land Patterns
DIP packages have two rows of leads on opposite sides of the component body. The land pattern for a DIP consists of two rows of circular pads, with the pad size and spacing determined by the lead pitch and the hole size required for the leads.
Table: Recommended Land Pattern Dimensions for DIP Packages (IPC-7251)
Pitch (in) | Hole Diameter (in) | Pad Diameter (in) | Pad Spacing (in) |
---|---|---|---|
0.100 | 0.040 | 0.070 | 0.100 |
0.200 | 0.040 | 0.070 | 0.200 |
0.300 | 0.040 | 0.070 | 0.300 |
0.400 | 0.040 | 0.070 | 0.400 |
0.600 | 0.040 | 0.070 | 0.600 |
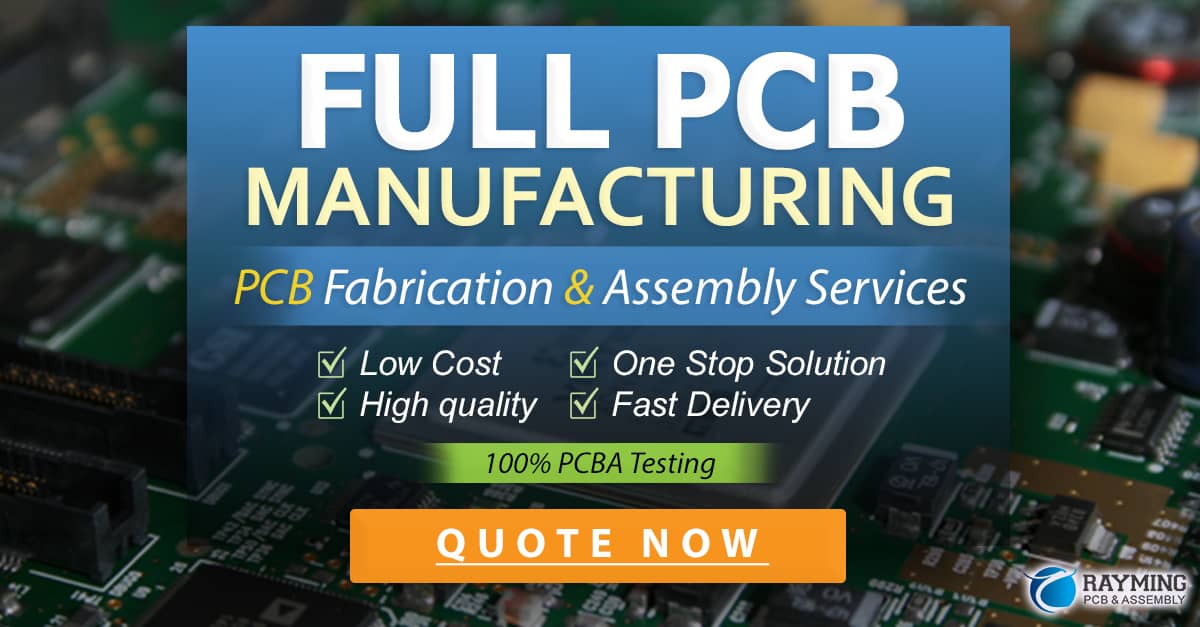
Solder Mask and Paste Stencil Design
In addition to the copper pads, a land pattern also includes solder mask openings and solder paste stencil apertures.
Solder Mask Openings
The solder mask is a layer of polymer applied to the PCB surface to protect the copper traces from oxidation and prevent solder bridges between adjacent pads. Openings in the solder mask are created around the pads to allow the solder to bond to the copper.
IPC-7351 recommends that the solder mask opening should be larger than the copper pad by a certain amount, known as the solder mask expansion. The solder mask expansion ensures that the entire pad is exposed for soldering and compensates for any misalignment between the solder mask and copper layers.
Table: Recommended Solder Mask Expansion (IPC-7351)
Pad Size (mm) | Solder Mask Expansion (mm) |
---|---|
≤ 0.50 | 0.05 |
> 0.50, ≤ 1.00 | 0.10 |
> 1.00 | 0.15 |
Solder Paste Stencil Apertures
The solder paste stencil is a thin metal template used to apply solder paste to the pads during the PCB assembly process. The stencil has apertures (openings) that correspond to the pads on the PCB. The size and shape of the apertures determine the amount of solder paste deposited on each pad.
IPC-7525 provides guidelines for designing solder paste stencil apertures. The aperture size should be slightly smaller than the pad size to prevent solder paste from spreading beyond the pad edges. The aperture reduction is typically 10-20% of the pad size, depending on the solder paste properties and the printing process parameters.
Table: Recommended Solder Paste Stencil Aperture Reduction (IPC-7525)
Pad Size (mm) | Aperture Reduction (mm) |
---|---|
≤ 0.50 | 0.05 |
> 0.50, ≤ 1.00 | 0.10 |
> 1.00 | 0.15 |
Courtyard and Keepout Areas
A land pattern should also include a courtyard and keepout areas to ensure proper spacing between components and prevent interference with other features on the PCB.
Courtyard
The courtyard is a rectangular area around the component that defines the minimum spacing required for assembly and inspection. The courtyard should be large enough to accommodate the component body, leads, and any additional features such as polarization marks or pin 1 indicators.
IPC-7351 defines the courtyard as the smallest rectangular area that encompasses the component body and any additional features, with a minimum clearance of 0.25 mm on all sides.
Keepout Areas
Keepout areas are regions on the PCB where other components, traces, or vias are not allowed to be placed. Keepout areas are used to prevent interference between components, ensure proper signal integrity, and provide space for assembly and inspection.
Keepout areas should be defined based on the specific requirements of the component and the PCB design. For example, a keepout area may be required around a high-speed signal trace to prevent crosstalk, or around a heat-sensitive component to prevent thermal damage.
Designing Land Patterns in CAD Software
Most PCB design software packages include tools for creating and managing land patterns. These tools typically allow the user to define the pad size, shape, and spacing, as well as the solder mask and paste stencil openings, courtyard, and keepout areas.
Some common PCB design software packages with land pattern tools include:
- Altium Designer
- Cadence Allegro
- KiCad
- Mentor Graphics PADS
- Zuken CR-8000
When creating a land pattern in CAD software, it is important to follow the industry standards and guidelines discussed earlier. Many software packages include built-in libraries of standard land patterns for common component types, which can be used as a starting point for custom designs.
It is also important to verify the land pattern design using the software’s design rule check (DRC) tools, which can identify any violations of the design rules and ensure that the land pattern meets the requirements of the manufacturing process.
Frequently Asked Questions (FAQ)
- What is the difference between a land pattern and a footprint?
-
A land pattern and a footprint are essentially the same things – the arrangement of copper pads and other features on a PCB that allows a component to be soldered onto the board. The terms are often used interchangeably.
-
Why is it important to follow industry standards when designing land patterns?
-
Following industry standards ensures compatibility and reliability of the PCB assembly. Standards organizations like IPC and JEDEC provide guidelines for land pattern design based on best practices and empirical data, which helps to minimize the risk of assembly defects and performance issues.
-
Can I use the same land pattern for different component types?
-
Generally, no. Different component types have different sizes, shapes, and lead configurations, which require specific land pattern designs to ensure proper fit and solderability. Using the wrong land pattern can result in poor solder joints, mechanical stress, or even damage to the component or PCB.
-
How do I choose the right solder mask expansion and paste stencil aperture reduction?
-
The solder mask expansion and paste stencil aperture reduction should be chosen based on the size of the pads and the requirements of the soldering process. IPC-7351 and IPC-7525 provide recommended values for these parameters based on empirical data and best practices. It is important to consult with the PCB manufacturer and assembly provider to ensure that the chosen values are compatible with their processes.
-
What should I do if I cannot find a standard land pattern for my component?
- If a standard land pattern is not available for a particular component, it may be necessary to create a custom land pattern based on the component dimensions and the requirements of the soldering process. This can be done using the tools provided by PCB design software packages, following the guidelines and best practices outlined in industry standards like IPC-7351. It is important to verify the custom land pattern design with the component manufacturer and the PCB assembly provider to ensure compatibility and manufacturability.
0 Comments