What are IPC Standards?
IPC, formerly known as the Institute for Printed Circuits, is a global trade association that develops and publishes standards for the electronics industry. These standards cover a wide range of topics, including:
- Printed circuit board (PCB) design and fabrication
- Electronics assembly
- Quality and reliability testing
- Materials and processes
- Environmental and safety compliance
IPC standards are developed through a consensus-based process that involves input from industry experts, manufacturers, and end-users. This ensures that the standards reflect the latest technologies and best practices, while also addressing the needs of the entire supply chain.
Benefits of IPC Standards
Adhering to IPC standards offers numerous benefits for manufacturers and end-users alike, including:
- Improved Quality and Reliability
- IPC standards ensure that products are designed and manufactured to the highest levels of quality and reliability.
-
This reduces the risk of field failures and improves customer satisfaction.
-
Reduced Costs
- By following IPC standards, manufacturers can reduce costs associated with rework, scrap, and warranty claims.
-
Standardized processes also improve efficiency and reduce manufacturing time.
-
Enhanced Communication
- IPC standards provide a common language for communication between manufacturers, suppliers, and customers.
-
This reduces misunderstandings and improves collaboration throughout the supply chain.
-
Increased Market Access
- Many customers, particularly in industries such as aerospace, defense, and medical, require compliance with IPC standards.
- By meeting these standards, manufacturers can access new markets and expand their customer base.
Key IPC Standards
There are numerous IPC standards covering various aspects of electronics manufacturing. Some of the most widely used standards include:
IPC-A-610 – Acceptability of Electronic Assemblies
IPC-A-610 is the most widely used standard for electronics assembly. It provides criteria for acceptability of electronic assemblies, including soldering, component placement, and mechanical assembly. The standard includes detailed illustrations and photographs to help manufacturers understand and apply the criteria.
Class | Description | Typical Applications |
---|---|---|
1 | General Electronic Products | Consumer products, computer peripherals |
2 | Dedicated Service Electronic Products | Industrial controls, automotive electronics |
3 | High Performance Electronic Products | Aerospace, medical devices, military equipment |
IPC-A-600 – Acceptability of Printed Boards
IPC-A-600 provides criteria for the acceptability of printed circuit boards. It covers various aspects of PCB Fabrication, including:
- Visual requirements
- Dimensional requirements
- Physical properties
- Electrical properties
- Fabrication integrity
The standard includes detailed illustrations and photographs to help manufacturers understand and apply the criteria.
IPC J-STD-001 – Requirements for Soldered Electrical and Electronic Assemblies
IPC J-STD-001 is a joint standard developed by IPC and the Electronic Industries Alliance (EIA). It provides requirements for materials, methods, and verification criteria for producing high-quality soldered interconnections.
The standard covers various soldering processes, including:
- Wave soldering
- Reflow soldering
- Hand soldering
- Rework and repair
IPC-A-620 – Requirements and Acceptance for Cable and Wire Harness Assemblies
IPC-A-620 provides requirements and acceptance criteria for cable and wire harness assemblies. It covers various aspects of cable and harness manufacturing, including:
- Conductors and insulation
- Cable and harness construction
- Connectors and terminals
- Shielding and grounding
- Marking and labeling
The standard includes detailed illustrations and photographs to help manufacturers understand and apply the requirements.
Implementing IPC Standards
Implementing IPC standards requires a commitment from the entire organization, from top management to individual operators. Key steps in implementing IPC standards include:
- Training
- All personnel involved in electronics manufacturing should receive training on the relevant IPC standards.
-
IPC offers a variety of training programs, including classroom courses, online learning, and certification programs.
-
Documentation
- Manufacturers should develop detailed documentation of their processes and procedures to ensure compliance with IPC standards.
-
This includes work instructions, quality plans, and inspection and testing procedures.
-
Equipment and Materials
- Manufacturers should use equipment and materials that meet the requirements of the relevant IPC standards.
-
This may require investing in new equipment or updating existing processes.
-
Continuous Improvement
- Implementing IPC standards is not a one-time event, but an ongoing process of continuous improvement.
- Manufacturers should regularly review their processes and procedures to identify opportunities for improvement and ensure ongoing compliance with IPC standards.
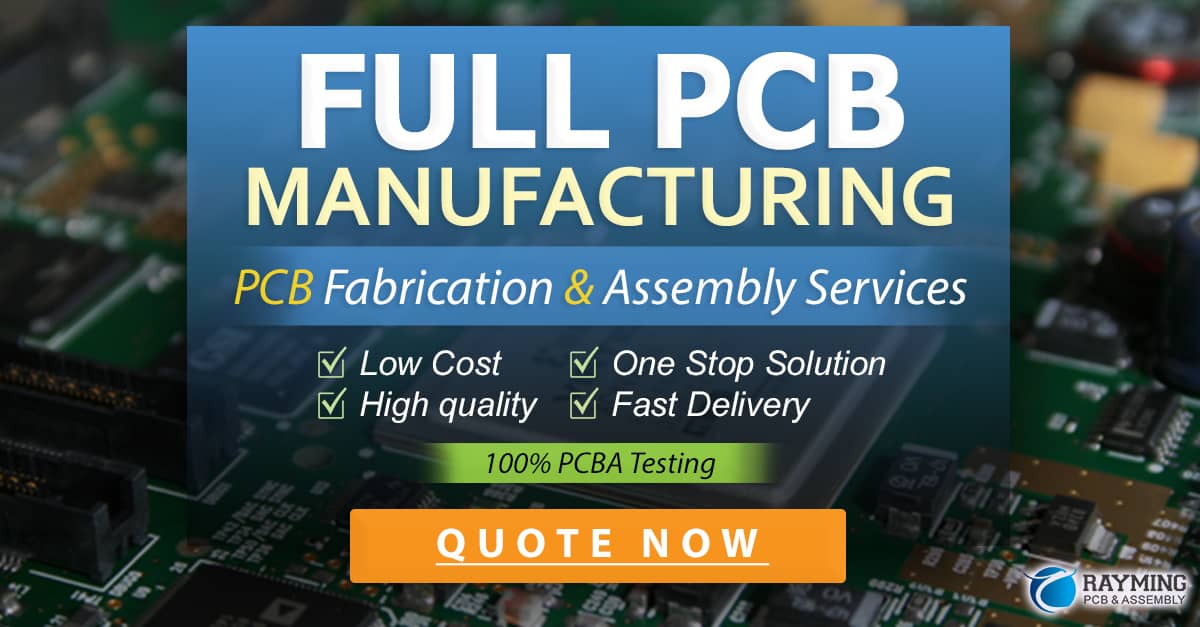
Frequently Asked Questions (FAQ)
-
Q: Are IPC standards mandatory?
A: IPC standards are voluntary, but many customers and industries require compliance with these standards as a condition of doing business. -
Q: How often are IPC standards updated?
A: IPC standards are regularly reviewed and updated to reflect the latest technologies and best practices. Most standards are updated every 5-7 years. -
Q: Can IPC standards be customized for specific applications?
A: While IPC standards provide a baseline for electronics manufacturing, they can be customized to meet the specific needs of individual companies or industries. However, any customization should be clearly documented and communicated to all stakeholders. -
Q: What happens if a product does not meet IPC standards?
A: If a product does not meet IPC standards, it may be subject to rework, scrap, or rejection by the customer. In some cases, non-compliance with IPC standards can also lead to legal or regulatory action. -
Q: How can manufacturers ensure compliance with IPC standards?
A: Manufacturers can ensure compliance with IPC standards by providing training to all personnel, developing detailed documentation of processes and procedures, using appropriate equipment and materials, and regularly reviewing and improving their processes through continuous improvement initiatives.
Conclusion
IPC standards are essential for ensuring the quality, reliability, and consistency of electronic products. By adhering to these standards, manufacturers can reduce costs, improve efficiency, and enhance customer satisfaction. Implementing IPC standards requires a commitment from the entire organization, as well as ongoing training, documentation, and continuous improvement efforts. As the electronics industry continues to evolve, IPC standards will remain a critical tool for manufacturers looking to stay competitive and meet the demands of their customers.
0 Comments