What is a PCB Substrate?
The PCB substrate is the base material on which the conductive copper traces and other components are placed. It provides mechanical support and electrical insulation between the conductive layers. The most common PCB substrate materials are:
FR-4 (Flame Retardant 4)
FR-4 is the most widely used PCB substrate material. It is a composite material made of woven fiberglass cloth impregnated with an epoxy resin. FR-4 offers excellent mechanical strength, electrical insulation properties, and high resistance to heat and moisture. It is suitable for a wide range of applications, from consumer electronics to industrial equipment.
High-Frequency Materials
For high-frequency applications, such as RF (Radio Frequency) and microwave circuits, specialized substrate materials are used to minimize signal loss and maintain signal integrity. Some common high-frequency substrate materials include:
- Rogers RO4003C: A hydrocarbon ceramic laminate with low dielectric loss and stable electrical properties.
- Isola IS680: A low-loss, high-speed laminate designed for high-frequency applications.
- PTFE (Polytetrafluoroethylene): A fluoropolymer material known for its low dielectric constant and excellent high-frequency performance.
Flexible Substrates
Flexible PCBs require substrate materials that can withstand bending and flexing without compromising their electrical and mechanical properties. Common flexible substrate materials include:
- Polyimide (PI): A high-performance polymer with excellent thermal stability and mechanical strength.
- Polyester (PET): A cost-effective option for less demanding flexible PCB applications.
Copper Foil: The Conductive Layer
Copper foil is the conductive material used to create the traces, pads, and planes on a PCB. It is laminated onto the substrate material using heat and pressure. The thickness of the copper foil is typically measured in ounces per square foot (oz/ft²), with common thicknesses being 0.5 oz/ft², 1 oz/ft², and 2 oz/ft².
Electrodeposited (ED) Copper Foil
ED copper foil is manufactured by electroplating copper onto a rotating drum. It has a smooth, shiny surface on one side (drum side) and a matte, rough surface on the other side (matte side). The rough surface provides better adhesion to the substrate material.
Rolled Copper Foil
Rolled copper foil is produced by mechanically rolling copper into thin sheets. It has a more uniform grain structure compared to ED copper foil and offers better mechanical and electrical properties. However, it is more expensive than ED copper foil.
Solder Mask: Protecting the PCB
Solder mask, also known as solder resist, is a protective coating applied to the PCB surface to prevent solder bridging and protect the copper traces from oxidation and contamination. It also provides electrical insulation between adjacent traces. Solder mask is typically green in color but can also be found in other colors such as red, blue, and black.
Liquid Photoimageable Solder Mask (LPISM)
LPISM is the most common type of solder mask used in PCB manufacturing. It is applied as a liquid coating and then exposed to UV light through a photomask to create the desired pattern. The unexposed areas are then developed and removed, leaving the solder mask only on the desired areas.
Dry Film Solder Mask (DFSM)
DFSM is a solid film that is laminated onto the PCB surface using heat and pressure. It is then exposed to UV light through a photomask and developed, similar to LPISM. DFSM offers better edge definition and is suitable for fine-pitch components.
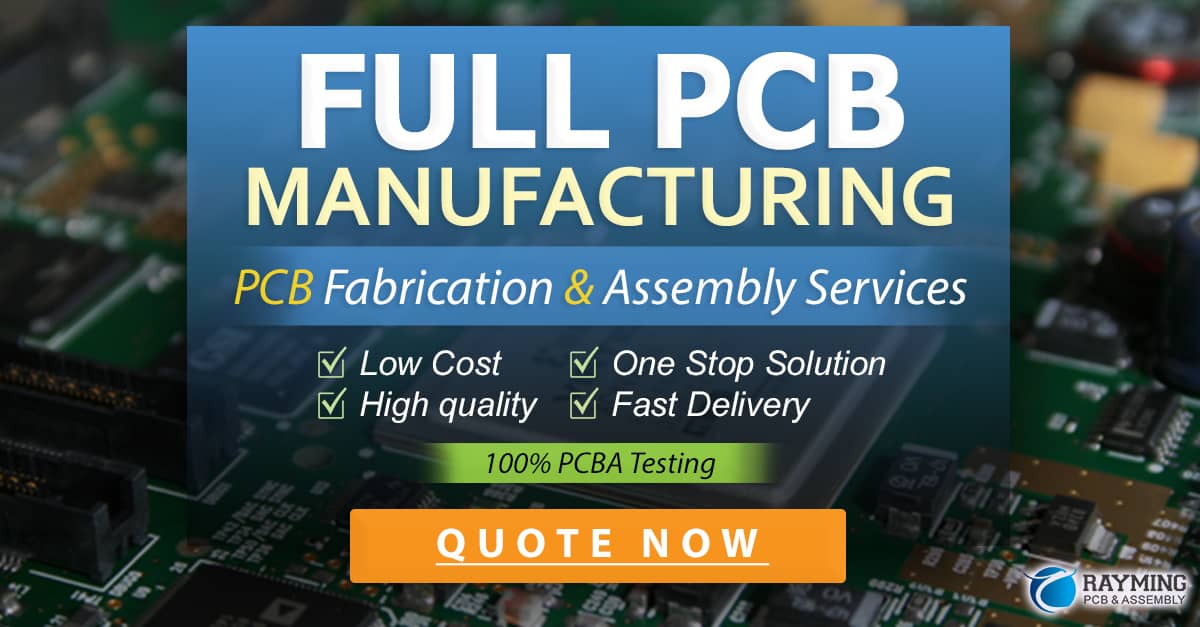
Silkscreen: Labeling and Identification
Silkscreen, also known as legend or nomenclature, is a printed layer on the PCB surface that provides labeling and identification for components, test points, and other features. It is typically white in color but can also be found in other colors such as black or yellow.
Silkscreen is applied using a screen-printing process, where ink is forced through a fine mesh screen onto the PCB surface. The screen has a stencil of the desired pattern, allowing the ink to pass through only in the desired areas.
Surface Finishes: Protecting and Enhancing Solderability
Surface finishes are applied to the exposed copper surfaces of a PCB to protect them from oxidation and enhance their solderability. The choice of surface finish depends on factors such as the application, soldering process, and shelf life requirements. Some common surface finishes include:
Hot Air Solder Leveling (HASL)
HASL involves dipping the PCB into a molten solder bath and then using hot air to blow off the excess solder, leaving a thin, uniform layer of solder on the copper surfaces. HASL is a cost-effective and widely used surface finish.
Electroless Nickel Immersion Gold (ENIG)
ENIG is a two-layer surface finish consisting of a nickel underlay and a thin gold top layer. The nickel provides a diffusion barrier and the gold protects the nickel from oxidation. ENIG offers excellent solderability and is suitable for fine-pitch components.
Immersion Silver (IAg)
IAg is a single-layer surface finish that deposits a thin layer of silver onto the copper surfaces through a chemical process. It provides good solderability and is a cost-effective alternative to ENIG.
Immersion Tin (ISn)
ISn is another single-layer surface finish that deposits a thin layer of tin onto the copper surfaces. It offers good solderability and is suitable for applications with shorter shelf life requirements.
Frequently Asked Questions (FAQ)
- What is the most common PCB substrate material?
-
FR-4 (Flame Retardant 4) is the most widely used PCB substrate material. It is a composite material made of woven fiberglass cloth impregnated with an epoxy resin.
-
What is the purpose of solder mask on a PCB?
-
Solder mask is a protective coating applied to the PCB surface to prevent solder bridging and protect the copper traces from oxidation and contamination. It also provides electrical insulation between adjacent traces.
-
What is the difference between HASL and ENIG surface finishes?
-
HASL (Hot Air Solder Leveling) involves dipping the PCB into a molten solder bath and using hot air to level the solder, while ENIG (Electroless Nickel Immersion Gold) is a two-layer finish with a nickel underlay and a thin gold top layer. ENIG offers better solderability and is suitable for fine-pitch components.
-
What are the advantages of using high-frequency substrate materials?
-
High-frequency substrate materials, such as Rogers RO4003C and Isola IS680, offer low dielectric loss and stable electrical properties. They are used in applications that require high signal integrity and minimal signal loss, such as RF and microwave circuits.
-
What is the purpose of silkscreen on a PCB?
- Silkscreen, also known as legend or nomenclature, is a printed layer on the PCB surface that provides labeling and identification for components, test points, and other features. It helps in the assembly and debugging of PCBs.
PCB Raw Material | Description |
---|---|
Substrate | The base material on which the conductive copper traces and other components are placed. Common substrate materials include FR-4, high-frequency materials, and flexible substrates. |
Copper Foil | The conductive material used to create the traces, pads, and planes on a PCB. It is available in different thicknesses and can be electrodeposited (ED) or rolled. |
Solder Mask | A protective coating applied to the PCB surface to prevent solder bridging and protect the copper traces from oxidation and contamination. It is available in liquid photoimageable (LPISM) and dry film (DFSM) forms. |
Silkscreen | A printed layer on the PCB surface that provides labeling and identification for components, test points, and other features. It is typically white in color and applied using a screen-printing process. |
Surface Finish | A protective layer applied to the exposed copper surfaces of a PCB to protect them from oxidation and enhance their solderability. Common surface finishes include HASL, ENIG, IAg, and ISn. |
In conclusion, understanding the basic knowledge of PCB raw materials is essential for anyone involved in the design, manufacturing, or procurement of PCBs. By familiarizing yourself with the substrate, copper foil, solder mask, silkscreen, and surface finishes, you can make informed decisions and ensure the quality and reliability of your PCBs. Whether you are a designer, engineer, or purchasing professional, having a solid grasp of these fundamental concepts will help you navigate the world of PCBs with confidence.
0 Comments