What is SMT PCB Assembly?
SMT PCB Assembly is a method of mounting electronic components directly onto the surface of a printed circuit board. In contrast to through-hole technology, where component leads are inserted into drilled holes and soldered on the opposite side of the board, SMT components are placed and soldered directly onto the PCB surface. This process allows for smaller component sizes, higher component density, and faster assembly speeds.
Advantages of SMT PCB Assembly
- Miniaturization: SMT components are significantly smaller than their through-hole counterparts, enabling the production of more compact electronic devices.
- Higher component density: With SMT, more components can be placed on a single PCB, allowing for more complex designs and functionality within a smaller footprint.
- Faster assembly: SMT PCB assembly is highly automated, resulting in faster production times and lower labor costs compared to through-hole assembly.
- Improved reliability: SMT components have shorter lead lengths, which reduces the risk of damage from vibration and improves overall device reliability.
- Better high-frequency performance: The shorter lead lengths of SMT components also result in reduced parasitic capacitance and inductance, enhancing high-frequency performance.
History of SMT PCB Assembly
The development of SMT PCB assembly can be traced back to the 1960s when IBM introduced the first surface mount package for semiconductors. However, it wasn’t until the 1980s that SMT began to gain widespread adoption in the electronics industry. The introduction of smaller, more advanced SMT components and the development of automated assembly equipment played a crucial role in the growth of SMT PCB assembly.
Decade | Developments in SMT PCB Assembly |
---|---|
1960s | IBM introduces the first surface mount package for semiconductors |
1970s | Development of surface mount resistors and capacitors |
1980s | Widespread adoption of SMT in the electronics industry |
1990s | Advancement of fine-pitch SMT components and assembly equipment |
2000s | Introduction of lead-free solder and environment-friendly manufacturing processes |
2010s | Continued miniaturization and the rise of advanced packaging technologies |
SMT PCB Assembly Process
The SMT PCB assembly process consists of several key steps, each requiring specialized equipment and expertise. The following sections will provide an overview of the main stages in the SMT PCB assembly process.
1. Solder Paste Printing
The first step in SMT PCB assembly is the application of solder paste to the PCB surface. Solder paste is a mixture of tiny solder particles suspended in a flux medium. A stencil is used to apply the solder paste to the desired locations on the PCB, ensuring precise placement and the correct amount of paste for each component pad.
2. Component Placement
Once the solder paste has been applied, the next step is to place the SMT components onto the PCB. This process is typically performed using automated pick-and-place machines, which use vacuum nozzles to pick up components from reels or trays and place them onto the PCB with high accuracy and speed. Some common types of pick-and-place machines include:
- Chip shooters: High-speed machines designed for placing small, simple components like resistors and capacitors.
- Flexible placement machines: Versatile machines capable of placing a wide range of component sizes and types.
- Multi-head placement machines: High-end machines with multiple placement heads for maximum throughput and flexibility.
3. Reflow Soldering
After the components have been placed, the PCB undergoes reflow soldering. In this process, the PCB is passed through a reflow oven, which applies a controlled temperature profile to melt the solder paste and form a permanent electrical and mechanical connection between the components and the PCB. The reflow soldering process typically consists of four stages:
- Preheat: The PCB is gradually heated to activate the flux and remove any moisture from the components and PCB surface.
- Thermal soak: The temperature is maintained to ensure even heat distribution across the PCB.
- Reflow: The temperature is increased above the melting point of the solder, allowing it to flow and form a connection between the components and the PCB pads.
- Cooling: The PCB is cooled to allow the solder joints to solidify, forming a strong and reliable connection.
4. Inspection and Testing
After the reflow soldering process, the assembled PCB undergoes inspection and testing to ensure the quality and functionality of the final product. Various methods are used, including:
- Visual inspection: Manual or automated optical inspection to identify any visible defects, such as misaligned components, solder bridges, or insufficient solder joints.
- Automated Optical Inspection (AOI): High-speed, computer-based systems that use cameras and image processing algorithms to detect assembly defects.
- X-ray inspection: Used to inspect solder joints hidden under components, such as ball grid arrays (BGAs) or quad flat no-lead (QFN) packages.
- In-circuit testing (ICT): Electrical testing using dedicated test fixtures to verify the functionality and performance of individual components and circuits.
- Functional testing: Testing the assembled PCB in its final application to ensure it meets the desired specifications and requirements.
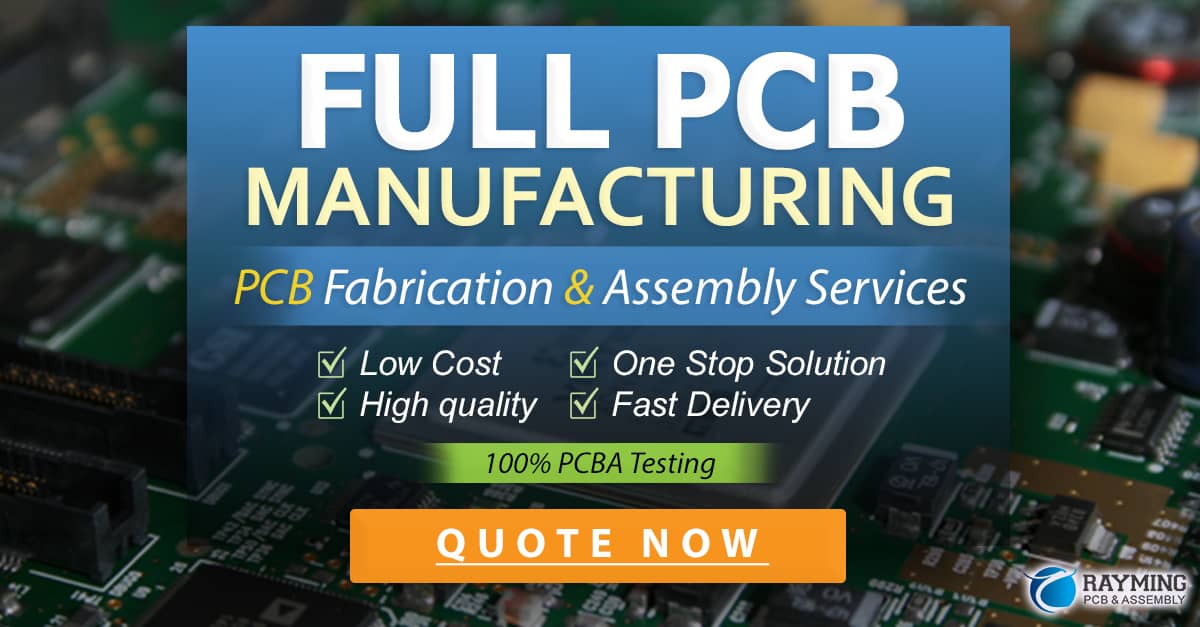
Common Challenges in SMT PCB Assembly
While SMT PCB assembly offers numerous benefits, it also presents several challenges that manufacturers must address to ensure high-quality, reliable products.
1. Miniaturization and Increasing Component Density
As electronic devices continue to shrink in size and increase in complexity, PCB designers must deal with the challenges of placing more components in smaller spaces. This requires advanced design techniques, such as 3D component placement and the use of embedded components, as well as the development of new materials and manufacturing processes to accommodate these trends.
2. Thermal Management
With higher component density comes increased heat generation, which can negatively impact the performance and reliability of electronic devices. Effective thermal management strategies, such as the use of thermal vias, heat sinks, and thermally conductive materials, are essential to ensure proper heat dissipation and prevent component damage.
3. Solder Joint Reliability
The quality and reliability of solder joints are critical factors in the overall performance and longevity of SMT PCB assemblies. Common solder joint defects, such as cold joints, solder bridges, and insufficient solder, can lead to electrical failures and reduced product lifespan. Manufacturers must implement strict process controls and use advanced inspection techniques to minimize the occurrence of these defects.
4. Handling and Storage of SMT Components
SMT components, particularly moisture-sensitive devices (MSDs), require proper handling and storage to prevent damage during the assembly process. Exposure to moisture can cause cracking or delamination of component packages during reflow soldering, leading to device failure. Manufacturers must follow established industry guidelines, such as IPC/JEDEC J-STD-033, to ensure the proper handling, storage, and processing of MSDs.
5. Lead-Free Soldering
The transition to lead-free solder alloys, driven by environmental regulations such as the Restriction of Hazardous Substances (RoHS) directive, has presented new challenges for SMT PCB assembly. Lead-free solders typically have higher melting points and different wetting characteristics compared to traditional tin-lead solders, requiring adjustments to the reflow soldering process and the development of new solder paste formulations.
Frequently Asked Questions (FAQ)
- What is the difference between SMT and Through-hole PCB assembly?
-
SMT components are mounted directly onto the surface of the PCB, while through-hole components have leads that are inserted into drilled holes and soldered on the opposite side of the board. SMT allows for smaller component sizes, higher component density, and faster assembly compared to through-hole technology.
-
What are the main steps in the SMT PCB assembly process?
-
The main steps in SMT PCB assembly are solder paste printing, component placement, reflow soldering, and inspection and testing.
-
What types of inspection methods are used in SMT PCB assembly?
-
Common inspection methods include visual inspection, automated optical inspection (AOI), X-ray inspection, in-circuit testing (ICT), and functional testing.
-
What are moisture-sensitive devices (MSDs), and why do they require special handling?
-
MSDs are components that are susceptible to damage from moisture absorption. Exposure to moisture can cause cracking or delamination of component packages during reflow soldering, leading to device failure. Proper handling, storage, and processing of MSDs according to industry guidelines are essential to prevent damage.
-
What challenges have manufacturers faced with the transition to lead-free soldering?
- Lead-free solders have higher melting points and different wetting characteristics compared to traditional tin-lead solders, requiring adjustments to the reflow soldering process and the development of new solder paste formulations. Manufacturers have had to adapt their processes and materials to ensure the reliability and performance of lead-free solder joints.
Conclusion
SMT PCB assembly has transformed the electronics industry, enabling the production of smaller, more complex, and more reliable electronic devices. By understanding the history, benefits, process, and challenges of SMT PCB assembly, manufacturers can optimize their production processes and ensure the highest quality products for their customers. As electronic devices continue to evolve, the SMT PCB assembly process will undoubtedly adapt to meet the ever-changing demands of the industry.
0 Comments