What is an Automotive PCB?
An automotive printed circuit board (PCB) is a crucial component in modern vehicles that enables various electronic systems to function seamlessly. These PCBs are designed to withstand harsh environmental conditions, such as extreme temperatures, vibrations, and moisture, ensuring reliable performance in automotive applications.
Automotive PCBs are found in various systems within a vehicle, including:
- Engine control units (ECUs)
- Infotainment systems
- Advanced driver assistance systems (ADAS)
- Body control modules
- Powertrain control modules
The Importance of Automotive PCBs in Modern Vehicles
As vehicles become more advanced and reliant on electronic systems, the role of automotive PCBs has become increasingly significant. These PCBs enable the integration of various sensors, actuators, and control units, allowing for efficient communication and coordination between different vehicle subsystems.
Some of the key benefits of automotive PCBs include:
-
Enhanced vehicle performance: Automotive PCBs enable precise control over engine performance, fuel efficiency, and emissions, resulting in better overall vehicle performance.
-
Improved safety features: Advanced driver assistance systems (ADAS) and other safety features rely on automotive PCBs to function effectively, helping to reduce the risk of accidents and protect vehicle occupants.
-
Increased comfort and convenience: Infotainment systems, climate control, and other comfort features are made possible by automotive PCBs, enhancing the driving experience for passengers.
-
Reduced wiring complexity: By consolidating multiple functions onto a single PCB, automotive manufacturers can reduce the amount of wiring required in a vehicle, leading to reduced weight, improved reliability, and lower production costs.
Design Considerations for Automotive PCBs
Designing automotive PCBs requires careful consideration of various factors to ensure reliable performance in challenging environments. Some of the key design considerations include:
1. Temperature Resistance
Automotive PCBs must be able to withstand extreme temperature fluctuations, ranging from sub-zero temperatures to high heat generated by the engine and other components. PCB materials and components must be selected to ensure reliable operation across this wide temperature range.
Common temperature ranges for automotive PCBs include:
Temperature Range | Description |
---|---|
-40°C to +85°C | Standard operating temperature range for most automotive PCBs |
-40°C to +105°C | Extended temperature range for PCBs in harsher environments |
-40°C to +125°C | Extreme temperature range for PCBs in the most demanding applications |
2. Vibration and Shock Resistance
Vehicles are subjected to constant vibrations and occasional shocks during operation, which can cause mechanical stress on PCBs and their components. Automotive PCBs must be designed to withstand these forces without suffering from mechanical failure or compromised performance.
Some strategies for improving vibration and shock resistance include:
- Using thicker PCB substrates
- Incorporating additional mounting points and support structures
- Selecting components with higher mechanical strength
- Applying Conformal Coatings to protect against vibration-induced damage
3. Moisture and Corrosion Resistance
Exposure to moisture, salt, and other corrosive elements can degrade PCB performance and lead to premature failure. Automotive PCBs must be designed with appropriate protective measures to ensure reliable operation in these environments.
Some common methods for improving moisture and corrosion resistance include:
- Applying conformal coatings or potting compounds
- Using gold or other noble metal finishes on exposed contacts
- Selecting PCB substrates with low moisture absorption
- Incorporating drainage holes and vents to prevent moisture accumulation
4. Electromagnetic Compatibility (EMC)
Automotive PCBs must be designed to minimize electromagnetic interference (EMI) and ensure compatibility with other electronic systems within the vehicle. Proper EMC design practices help to prevent signal integrity issues and ensure reliable communication between different vehicle subsystems.
Some EMC design considerations for automotive PCBs include:
- Proper grounding and shielding techniques
- Minimizing loop areas and trace lengths
- Using differential signaling for high-speed communication
- Incorporating EMI filters and suppression components
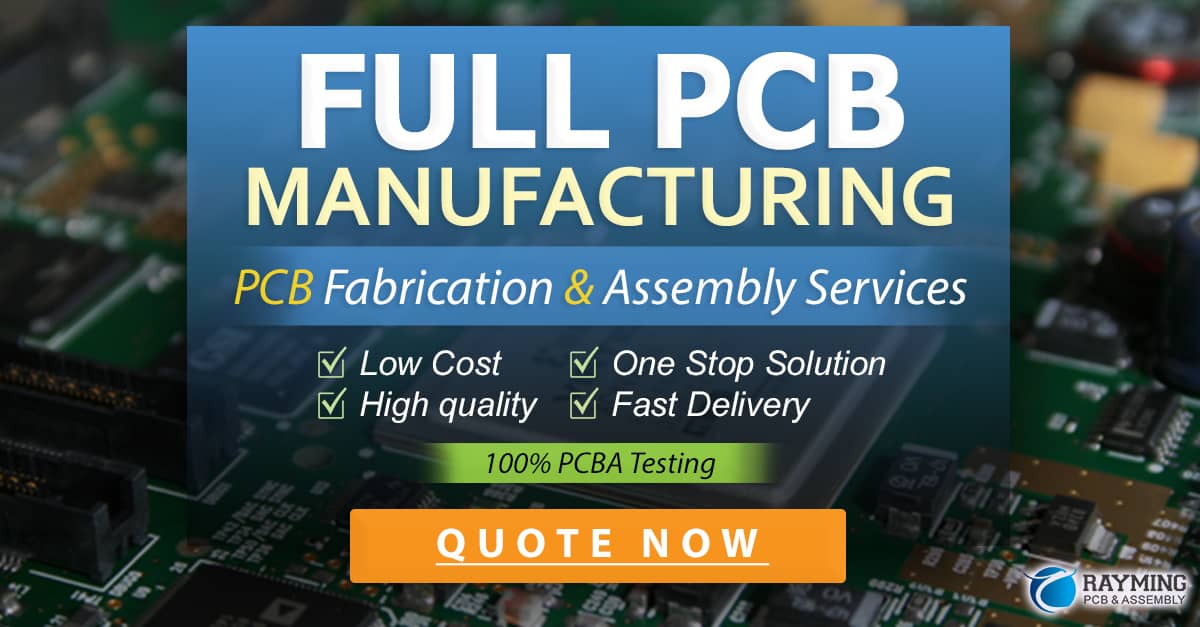
Manufacturing and Testing of Automotive PCBs
To ensure the highest quality and reliability, automotive PCBs must undergo rigorous manufacturing and testing processes.
Manufacturing Process
The manufacturing process for automotive PCBs typically involves the following steps:
- PCB design and layout
- Material selection and substrate preparation
- Copper etching and plating
- Solder mask and silkscreen application
- Component placement and soldering
- Conformal coating or potting (if required)
Throughout the manufacturing process, strict quality control measures are implemented to ensure consistent and defect-free production.
Testing and Validation
Before being integrated into vehicles, automotive PCBs must pass a series of tests to validate their performance and reliability. Some common testing methods include:
-
Environmental testing: PCBs are subjected to temperature cycling, humidity exposure, and vibration testing to simulate real-world operating conditions.
-
Functional testing: PCBs are tested to ensure they perform their intended functions correctly, including communication with other vehicle systems.
-
Accelerated life testing: PCBs are subjected to increased stress levels to identify potential failure modes and estimate the product’s lifespan.
-
Electromagnetic compatibility (EMC) testing: PCBs are tested for EMI emissions and susceptibility to ensure they meet relevant standards and regulations.
Successful completion of these tests ensures that automotive PCBs are ready for integration into vehicles and can provide reliable performance throughout the vehicle’s lifespan.
Future Trends in Automotive PCBs
As vehicle technology continues to advance, automotive PCBs are evolving to keep pace with new requirements and challenges. Some of the key trends shaping the future of automotive PCBs include:
1. Miniaturization and Increased Complexity
As vehicles incorporate more electronic features and functions, there is a growing demand for smaller, more complex PCBs that can fit into limited space. This trend is driving the adoption of advanced PCB technologies, such as high-density interconnect (HDI) and embedded components.
2. Adoption of Advanced Materials
New PCB materials, such as low-loss dielectrics and high-thermal-conductivity substrates, are being developed to meet the demands of high-speed communication and increased power densities in automotive applications.
3. Integration of Wireless Technologies
As vehicles become more connected, automotive PCBs are incorporating wireless technologies, such as Wi-Fi, Bluetooth, and cellular communication, to enable seamless integration with external networks and devices.
4. Increased Focus on Reliability and Safety
With the growing importance of electronic systems in vehicles, there is an increased focus on ensuring the reliability and safety of automotive PCBs. This trend is driving the development of more robust design and testing methodologies, as well as the adoption of redundant systems and fail-safe mechanisms.
FAQ
-
Q: What is the typical lifespan of an automotive PCB?
A: The lifespan of an automotive PCB depends on various factors, such as the specific application, environmental conditions, and design quality. However, most automotive PCBs are designed to last for the entire lifespan of the vehicle, which can be 10-15 years or more. -
Q: Can automotive PCBs be repaired or replaced?
A: In most cases, automotive PCBs are not designed to be repaired or serviced by end-users. If a PCB fails, it typically needs to be replaced with a new unit. However, some manufacturers may offer remanufactured or refurbished PCBs as a cost-effective alternative to new replacements. -
Q: Are automotive PCBs recyclable?
A: Yes, automotive PCBs can be recycled to recover valuable materials, such as copper, gold, and other metals. However, the recycling process is complex and requires specialized facilities to ensure proper handling and disposal of hazardous substances. -
Q: How do automotive PCBs differ from PCBs used in other industries?
A: Automotive PCBs are designed to withstand harsher environmental conditions and more stringent reliability requirements compared to PCBs used in other industries. They often incorporate additional protective measures, such as conformal coatings and more robust components, to ensure reliable operation in challenging automotive environments. -
Q: What are the key standards and regulations governing automotive PCBs?
A: Automotive PCBs are subject to various standards and regulations, depending on the specific application and region. Some of the key standards include: -
AEC-Q100: Failure mechanism based stress test qualification for integrated circuits
- AEC-Q200: Stress test qualification for passive components
- ISO 26262: Road vehicles – Functional safety
- IPC-6012: Qualification and performance specification for rigid printed boards
Compliance with these standards ensures that automotive PCBs meet the necessary quality, reliability, and safety requirements for use in vehicles.
Conclusion
Automotive PCBs play a critical role in enabling the advanced electronic features and functions that define modern vehicles. By providing reliable, high-performance connectivity between various vehicle systems, automotive PCBs contribute to improved safety, efficiency, and comfort for drivers and passengers alike.
As vehicle technology continues to evolve, so too will the demands placed on automotive PCBs. Designers and manufacturers must stay at the forefront of these trends, adopting new materials, technologies, and processes to ensure that automotive PCBs can meet the challenges of the future.
By understanding the unique requirements and considerations involved in automotive PCB design and manufacturing, engineers and decision-makers can make informed choices that contribute to the development of safer, more reliable, and more advanced vehicles.
0 Comments