Introduction to Blind Microvias
In the world of printed circuit board (PCB) manufacturing, the demand for higher integration density and smaller form factors is constantly growing. One key technology that has emerged to meet these requirements is the use of blind microvias. Blind microvias are small, laser-drilled holes that connect inner layers of a PCB without penetrating through the entire board thickness. This article will explore the benefits, manufacturing process, design considerations, and applications of blind microvias in PCB fabrication.
What are Blind Microvias?
A blind microvia is a type of interconnect that connects an outer layer of a PCB to an inner layer without going through the entire board thickness. Unlike through-hole vias, which are drilled mechanically and span the entire board, blind microvias are typically laser-drilled and have a depth that is less than the total board thickness. The term “blind” refers to the fact that these vias are not visible from the opposite side of the board.
Benefits of Using Blind Microvias
The use of blind microvias offers several advantages in PCB design and manufacturing:
-
Increased integration density: By using blind microvias, designers can pack more components and interconnects into a smaller area, enabling the creation of highly miniaturized and complex PCBs.
-
Improved signal integrity: Blind microvias provide shorter signal paths between layers, reducing the risk of signal degradation and cross-talk.
-
Reduced layer count: With the ability to connect inner layers without going through the entire board, blind microvias can help reduce the number of layers required in a PCB, leading to cost savings and thinner board profiles.
-
Enhanced thermal management: Blind microvias can be used to create thermal vias, which help dissipate heat from high-power components more efficiently.
Manufacturing Process of Blind Microvias
The manufacturing process of blind microvias involves several steps:
Laser Drilling
Blind microvias are typically created using laser drilling technology. There are two main types of lasers used for this purpose: CO2 lasers and UV lasers. CO2 lasers are more common and offer a cost-effective solution for larger via sizes, while UV lasers provide higher precision and are suitable for smaller via diameters.
Desmear and Cleaning
After laser drilling, the microvias need to be cleaned to remove any debris and ensure proper electrical connectivity. This process, known as desmearing, involves using a chemical or plasma etching process to remove the resin smear from the via walls.
Electroless Copper Deposition
Once the microvias are cleaned, they are metallized using an electroless copper deposition process. This involves depositing a thin layer of copper onto the via walls to create an electrically conductive path.
Electrolytic Copper Plating
After the initial electroless copper deposition, an electrolytic copper plating process is used to build up the copper thickness inside the microvias. This ensures adequate electrical conductivity and mechanical strength.
Design Considerations for Blind Microvias
When incorporating blind microvias into a PCB design, several factors need to be considered:
Via Size and Aspect Ratio
The size of the blind microvias and their aspect ratio (depth-to-diameter ratio) are critical design parameters. Smaller via sizes enable higher integration density but may pose manufacturing challenges. The aspect ratio should be kept within the capabilities of the manufacturing process to ensure reliable via formation.
Layer Stack-up
The layer stack-up of the PCB needs to be carefully planned when using blind microvias. The depth of the microvias and their location in the stack-up will determine the manufacturing feasibility and the signal integrity performance.
Via Positioning and Routing
The positioning of blind microvias and their routing should be optimized to minimize signal path lengths and reduce the risk of signal integrity issues. Care should be taken to avoid placing microvias too close to each other or to other components, as this can lead to manufacturing defects and reliability problems.
Thermal Management
When using blind microvias for thermal management purposes, the via size, pitch, and placement should be carefully considered to ensure effective heat dissipation. Thermal simulation tools can be used to optimize the via layout for optimal thermal performance.
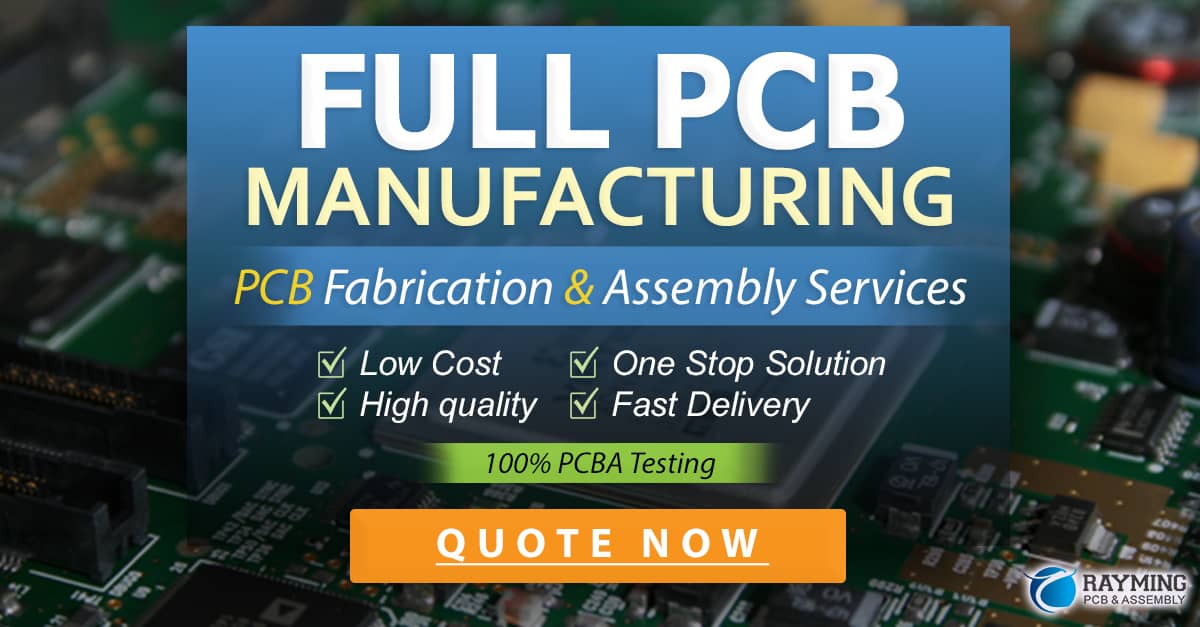
Applications of Blind Microvias
Blind microvias find applications in various industries and product categories:
High-Density Interconnect (HDI) PCBs
HDI PCBs are characterized by their high component density and fine-pitch interconnects. Blind microvias are extensively used in HDI designs to achieve the required integration density and signal integrity performance. Examples include smartphones, tablets, and wearable devices.
High-Speed Digital PCBs
In high-speed digital applications, such as high-performance computing and networking equipment, blind microvias are used to minimize signal path lengths and reduce the risk of signal integrity issues. They enable the routing of high-speed signals between layers with minimal impedance discontinuities.
RF and Microwave PCBs
Blind microvias are also used in RF and microwave PCBs to create compact and low-loss interconnects. They are particularly useful in creating controlled impedance structures and minimizing parasitic effects.
Automotive and Aerospace PCBs
In automotive and aerospace applications, where reliability and durability are critical, blind microvias are used to create robust and compact PCB designs. They enable the integration of high-density electronics in harsh operating environments.
Frequently Asked Questions (FAQ)
-
What is the minimum size of a blind microvia?
The minimum size of a blind microvia depends on the manufacturing capabilities of the PCB fabricator. Typically, blind microvias can have diameters as small as 50-75 microns (0.05-0.075 mm). -
Can blind microvias be stacked?
Yes, blind microvias can be stacked to create interconnects between multiple inner layers. However, Stacked Microvias require careful design and manufacturing considerations to ensure reliability. -
What is the cost impact of using blind microvias?
The use of blind microvias generally increases the manufacturing cost of a PCB compared to through-hole vias. The cost impact depends on factors such as the number of microvias, their size, and the complexity of the design. -
How do blind microvias affect the signal integrity of a PCB?
Blind microvias can improve signal integrity by providing shorter signal paths and reducing the risk of signal degradation and cross-talk. However, proper design and placement of microvias are crucial to achieve optimal signal integrity performance. -
Can blind microvias be used for power delivery?
Yes, blind microvias can be used for power delivery, especially in high-current applications. However, the current-carrying capacity of microvias is limited compared to through-hole vias, so multiple microvias may need to be used in parallel to handle high currents.
Conclusion
Blind microvias have revolutionized the PCB industry by enabling higher integration density, improved signal integrity, and compact form factors. By leveraging laser drilling technology and advanced manufacturing processes, PCB designers can create highly miniaturized and complex designs that meet the demands of modern electronics. However, the successful implementation of blind microvias requires careful consideration of design rules, manufacturing capabilities, and reliability requirements. As technology continues to advance, the use of blind microvias is expected to become even more prevalent in the PCB industry, driving innovation and shaping the future of electronic products.
0 Comments