What is an IMS PCB?
An IMS PCB, also known as a Metal Core PCB or thermal PCB, is a specialized type of printed circuit board that utilizes a metal substrate as its base. The metal substrate, typically aluminum, is coated with a thin layer of dielectric material, followed by a copper circuit layer. This unique construction allows IMS PCBs to efficiently dissipate heat generated by the mounted components.
The structure of an IMS PCB can be broken down into three main layers:
- Metal Substrate (Base Layer)
- Dielectric Layer (Insulation Layer)
- Copper Circuit Layer (Conductive Layer)
The metal substrate serves as the foundation of the IMS PCB, providing mechanical support and excellent thermal conductivity. The dielectric layer acts as an electrical insulator, preventing short circuits between the metal substrate and the copper circuit layer. Finally, the copper circuit layer is where the electronic components are mounted and interconnected.
Advantages of IMS PCBs
IMS PCBs offer several key advantages over traditional FR-4 PCBs:
-
Enhanced Thermal Management: The metal substrate in IMS PCBs acts as a heat sink, efficiently dissipating heat away from the components. This helps in maintaining optimal operating temperatures and prevents thermal damage to sensitive electronic devices.
-
Improved Reliability: By effectively managing heat, IMS PCBs reduce thermal stress on components, leading to improved reliability and longer product lifespans. This is particularly important in applications where high temperatures are encountered.
-
Reduced Size and Weight: IMS PCBs eliminate the need for additional heat sinks or cooling mechanisms, allowing for more compact and lightweight designs. This is especially beneficial in space-constrained applications or where weight reduction is crucial.
-
Cost-Effective: Although the initial cost of IMS PCBs may be higher compared to traditional PCBs, the overall system cost can be reduced. The integrated thermal management capabilities of IMS PCBs often eliminate the need for separate heat sinks, simplifying the assembly process and reducing manufacturing costs.
Applications of IMS PCBs
IMS PCBs find applications in various industries where thermal management is critical. Some common applications include:
-
Power Electronics: IMS PCBs are widely used in power electronics, such as power supplies, motor drives, and inverters. The efficient heat dissipation provided by IMS PCBs ensures reliable operation and prevents thermal runaway in high-power density devices.
-
LED Lighting: IMS PCBs are extensively used in LED lighting applications, where heat generated by the LEDs needs to be effectively dissipated to maintain optimal performance and longevity. The metal substrate in IMS PCBs acts as a heat sink, ensuring proper thermal management of the LED arrays.
-
Automotive Electronics: In the automotive industry, IMS PCBs are employed in various electronic systems, such as engine control units (ECUs), power steering modules, and headlight control systems. The harsh operating conditions in automotive environments, including high temperatures and vibrations, make IMS PCBs an ideal choice for reliable performance.
-
Telecommunications: IMS PCBs are used in telecommunications equipment, such as base stations and wireless transceivers. The heat generated by high-frequency components can be efficiently managed using IMS PCBs, ensuring stable operation and preventing signal degradation.
-
Industrial Control Systems: IMS PCBs find applications in industrial control systems, where they are subjected to harsh environments and elevated temperatures. The thermal management capabilities of IMS PCBs help in maintaining the reliability and longevity of industrial electronics.
Manufacturing Process of IMS PCBs
The manufacturing process of IMS PCBs involves several steps:
-
Substrate Preparation: The metal substrate, typically aluminum, is cleaned and prepared for the application of the dielectric layer. The surface is often roughened to enhance adhesion.
-
Dielectric Layer Application: A thin layer of dielectric material, such as polymer or ceramic, is applied onto the metal substrate. This layer provides electrical insulation between the metal substrate and the copper circuit layer.
-
Copper Foil Lamination: A copper foil is laminated onto the dielectric layer using heat and pressure. The copper foil forms the conductive layer where the electronic components will be mounted.
-
Circuit Patterning: The desired circuit pattern is transferred onto the copper layer using photolithography. This involves applying a photoresist, exposing it to UV light through a patterned mask, and developing the resist to reveal the desired circuit pattern.
-
Etching: The exposed copper areas are etched away using a chemical solution, leaving behind the desired circuit pattern.
-
Drilling: Holes are drilled through the IMS PCB to accommodate through-hole components and vias for inter-layer connections.
-
Surface Finishing: The copper surface is protected from oxidation and enhanced for solderability using various surface finishes, such as HASL (Hot Air Solder Leveling), ENIG (Electroless Nickel Immersion Gold), or OSP (Organic Solderability Preservative).
-
Solder Mask Application: A solder mask is applied over the copper layer, leaving exposed only the areas where components will be soldered. The solder mask provides insulation and protection to the copper traces.
-
Silkscreen Printing: The component designators, labels, and other markings are printed onto the solder mask using silkscreen printing.
-
Electrical Testing: The manufactured IMS PCB undergoes rigorous electrical testing to ensure proper functionality and adherence to the design specifications.
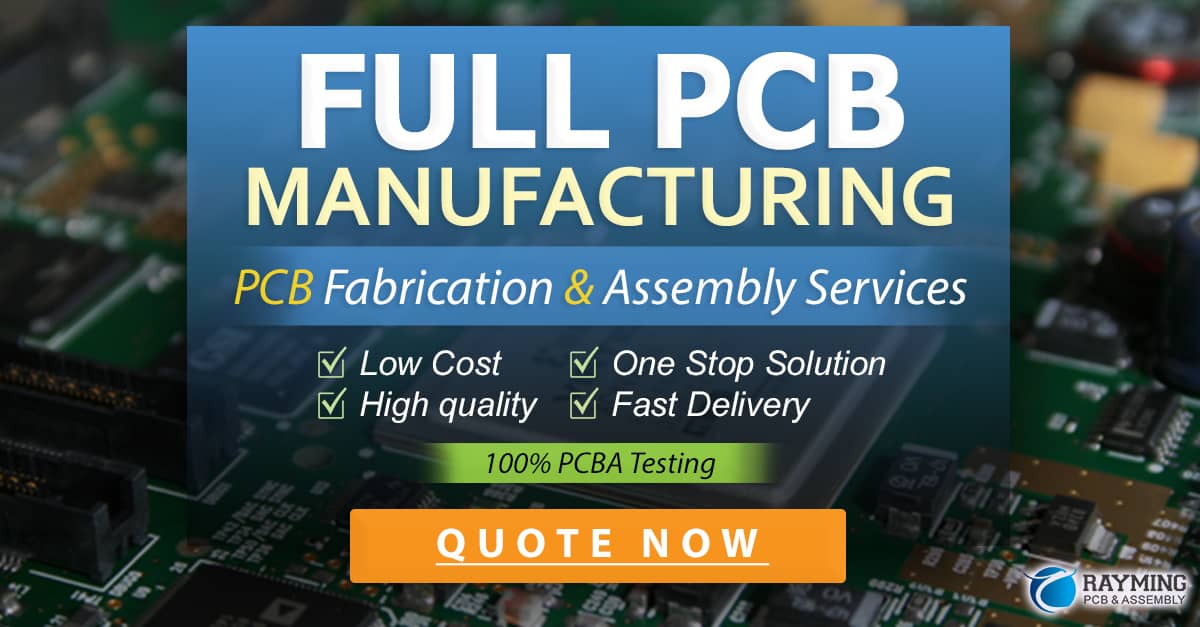
Thermal Management Considerations
When designing with IMS PCBs, several thermal management considerations should be taken into account:
-
Thermal Interface Material (TIM): A TIM, such as thermal grease or thermal pad, is often used between the components and the IMS PCB to enhance heat transfer. The TIM fills any air gaps and improves thermal conductivity.
-
Component Placement: Strategic component placement is crucial for optimal thermal management. Heat-generating components should be placed close to the metal substrate to facilitate efficient heat dissipation. Adequate spacing between components helps in preventing thermal interaction.
-
Copper Thickness: The thickness of the copper circuit layer affects the thermal performance of the IMS PCB. Thicker copper layers provide better thermal conductivity and heat spreading capabilities.
-
Dielectric Layer Thickness: The thickness of the dielectric layer influences the thermal resistance between the copper layer and the metal substrate. A thinner dielectric layer improves heat transfer, but it also affects the electrical insulation properties.
-
Thermal Vias: Thermal vias are used to create a thermal path from the component to the metal substrate. These vias are filled with thermally conductive material, such as copper or thermal epoxy, to enhance heat transfer.
Comparing IMS PCBs with Traditional PCBs
Parameter | IMS PCB | Traditional FR-4 PCB |
---|---|---|
Thermal Management | Excellent, with integrated heat sink | Poor, requires external heat sinks |
Reliability | High, due to effective heat dissipation | Moderate, prone to thermal issues |
Size and Weight | Compact and lightweight | Larger and heavier with external heat sinks |
Cost | Higher initial cost, but cost-effective overall | Lower initial cost, but may require additional cooling solutions |
Flexibility | Limited, due to rigid metal substrate | Flexible, suitable for various applications |
Dielectric Constant | Lower, due to thin dielectric layer | Higher, due to thicker FR-4 substrate |
Frequently Asked Questions (FAQ)
-
What is the primary advantage of using an IMS PCB?
The primary advantage of using an IMS PCB is its excellent thermal management capabilities. The metal substrate in IMS PCBs acts as a built-in heat sink, efficiently dissipating heat away from the components, leading to improved reliability and performance. -
Can IMS PCBs be used in high-frequency applications?
Yes, IMS PCBs can be used in high-frequency applications. However, the metal substrate may introduce some signal integrity challenges due to its effect on impedance and electromagnetic interference (EMI). Proper design considerations, such as controlled impedance routing and EMI shielding, can mitigate these issues. -
Are IMS PCBs suitable for flexible applications?
No, IMS PCBs are not suitable for flexible applications due to the rigid nature of the metal substrate. If flexibility is a requirement, traditional flexible PCBs or Rigid-flex PCBs are more appropriate choices. -
How does the cost of IMS PCBs compare to traditional PCBs?
The initial cost of IMS PCBs is generally higher compared to traditional FR-4 PCBs due to the specialized materials and manufacturing processes involved. However, when considering the overall system cost, IMS PCBs can be more cost-effective as they eliminate the need for additional heat sinks and simplify the assembly process. -
Can IMS PCBs be manufactured with multiple layers?
Yes, IMS PCBs can be manufactured with multiple layers. The number of layers depends on the specific design requirements and the capabilities of the PCB manufacturer. Multi-layer IMS PCBs offer increased layout flexibility and signal routing options while still providing excellent thermal management.
Conclusion
IMS PCBs have emerged as a superior solution for applications demanding effective thermal management. With their integrated metal substrate and excellent heat dissipation capabilities, IMS PCBs offer improved reliability, compact designs, and cost-effectiveness. From power electronics to LED lighting and automotive systems, IMS PCBs find applications in various industries where thermal management is critical.
When designing with IMS PCBs, careful consideration should be given to thermal interface materials, component placement, copper thickness, dielectric layer thickness, and the use of thermal vias. By optimizing these factors, designers can leverage the full potential of IMS PCBs in managing heat and ensuring reliable performance.
As technology advances and the demand for efficient thermal management grows, IMS PCBs are poised to play an increasingly important role in the electronics industry. Their unique characteristics and benefits make them an ideal choice for applications where heat dissipation is a primary concern.
By understanding the structure, advantages, applications, and design considerations of IMS PCBs, engineers and designers can make informed decisions when selecting the most suitable PCB technology for their projects. Embracing IMS PCBs opens up new possibilities for creating reliable, high-performance electronic systems that can withstand the challenges of heat-intensive environments.
0 Comments