Introduction to Immersion Silver (ImAg)
Immersion Silver (ImAg) is a popular surface finish for printed circuit boards (PCBs) due to its excellent solderability, flatness, and electrical performance. ImAg is a chemical process that deposits a thin layer of silver onto the exposed copper surfaces of a PCB. This silver layer protects the copper from oxidation and provides a solderable surface for component assembly.
Advantages of ImAg Surface Finish
- Excellent solderability
- Flat surface for fine-pitch components
- Good electrical conductivity
- Suitable for high-frequency applications
- RoHS compliant and environmentally friendly
Comparison of ImAg with Other Surface Finishes
Surface Finish | Solderability | Shelf Life | Cost | Flatness | Electrical Performance |
---|---|---|---|---|---|
ImAg | Excellent | 12 months | Low | Excellent | Good |
ENIG | Good | 12 months | High | Good | Excellent |
OSP | Good | 6 months | Low | Excellent | Good |
HASL | Good | 12 months | Low | Poor | Good |
The ImAg Process
Pre-treatment
Before the ImAg process can begin, the PCB must undergo a thorough cleaning process to remove any contaminants or oxides from the copper surface. This typically involves a series of chemical baths, such as:
- Acid cleaner to remove organic contaminants
- Micro-etch to remove copper oxide
- Acid dip to activate the copper surface
Silver Deposition
Once the copper surface is clean and activated, the PCB is immersed in the ImAg solution. The ImAg solution contains silver ions (Ag+) and a reducing agent. The reducing agent reacts with the silver ions, causing them to precipitate onto the copper surface as metallic silver (Ag).
The silver deposition process is self-limiting, meaning that once a thin layer of silver (typically 0.1-0.3 µm) has formed, the reaction stops. This ensures a consistent and uniform silver layer across the entire PCB.
Post-treatment
After the silver deposition, the PCB is rinsed with deionized water to remove any excess ImAg solution. A post-treatment step, such as a protective organic coating, may be applied to improve the tarnish resistance of the silver layer.
Advantages of ImAg in PCB Manufacturing
Cost-effectiveness
ImAg is a cost-effective surface finish compared to other options like ENIG (Electroless Nickel Immersion Gold). The raw materials for ImAg are less expensive, and the process is simpler, requiring fewer steps and less equipment.
Environmentally Friendly
ImAg is an environmentally friendly surface finish as it does not contain any hazardous substances like lead or nickel. It is RoHS compliant and meets the requirements for green electronics manufacturing.
Excellent Solderability
ImAg provides excellent solderability, even after multiple reflow cycles. The silver layer is easily wetted by molten solder, resulting in reliable solder joints. ImAg also has a longer shelf life compared to OSP (Organic Solderability Preservative), which can degrade over time.
Flat Surface for Fine-pitch Components
ImAg provides a flat and uniform surface, making it suitable for fine-pitch component assembly. The thin silver layer does not significantly increase the thickness of the copper pads, ensuring good co-planarity for small components like BGAs and CSPs.
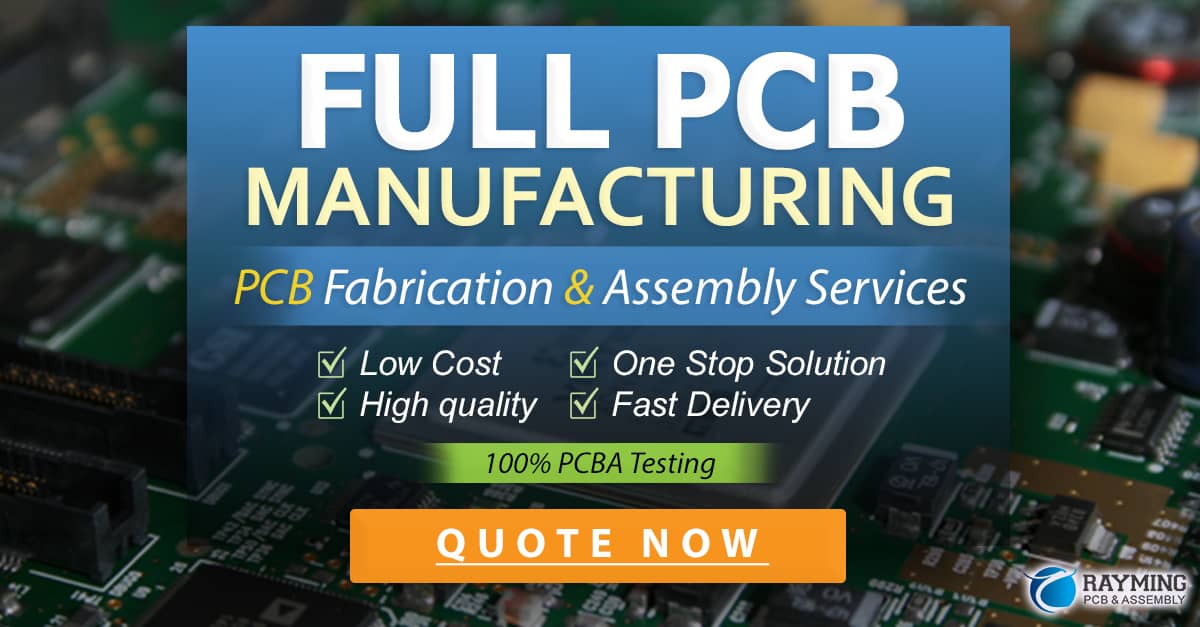
Challenges and Considerations
Tarnishing
One of the main challenges with ImAg is its susceptibility to tarnishing. When exposed to air, the silver layer can react with sulfur compounds to form silver sulfide, which appears as a dark discoloration on the surface. Tarnishing can affect the solderability and appearance of the PCB.
To mitigate tarnishing, PCBs with ImAg surface finish should be stored in a controlled environment with low humidity and minimal exposure to sulfur-containing compounds. Protective packaging materials, such as anti-tarnish bags, can also be used to extend the shelf life of ImAg PCBs.
Whisker Growth
Another potential issue with ImAg is the formation of silver whiskers. Whiskers are thin, filament-like growths that can develop on the silver surface over time. These whiskers can cause short circuits and reliability issues in the PCB.
The exact cause of whisker growth is not fully understood, but factors such as mechanical stress, temperature fluctuations, and contamination can contribute to their formation. To minimize the risk of whisker growth, PCB manufacturers must carefully control the ImAg process parameters and ensure a clean and stress-free surface.
Compatibility with Other Finishes
When using ImAg in a PCB design, it is important to consider its compatibility with other surface finishes that may be present on the board. For example, if a PCB has both ImAg and ENIG finishes, there may be a risk of galvanic corrosion due to the potential difference between the two metals.
To avoid compatibility issues, PCB designers should follow guidelines for mixed-finish boards and ensure proper isolation between different surface finishes.
ImAg in High-frequency Applications
ImAg is a suitable surface finish for high-frequency PCB applications due to its good electrical conductivity and low insertion loss. The thin silver layer does not significantly affect the impedance of the copper traces, making it suitable for high-speed digital and RF circuits.
However, designers must consider the skin effect when using ImAg in high-frequency applications. At high frequencies, the electrical current tends to flow on the surface of the conductor rather than through its entire cross-section. This can lead to increased losses and signal attenuation.
To minimize the impact of the skin effect, PCB designers can use wider traces, thicker copper layers, or low-loss dielectric materials. Simulation tools can also be used to optimize the PCB layout for high-frequency performance.
Quality Control and Testing
To ensure the quality and reliability of ImAg PCBs, manufacturers must implement strict quality control measures and testing procedures. Some of the key quality control steps include:
- Visual inspection: Checking the PCB surface for any visible defects, such as discoloration, pitting, or scratches.
- Thickness measurement: Verifying that the silver layer thickness is within the specified range (typically 0.1-0.3 µm) using X-ray fluorescence (XRF) or other methods.
- Solderability testing: Evaluating the solderability of the ImAg surface using wetting balance tests or other methods.
- Tarnish resistance testing: Exposing the PCB to controlled environmental conditions to assess its resistance to tarnishing.
- Whisker growth testing: Subjecting the PCB to thermal cycling or other stress tests to evaluate its susceptibility to whisker growth.
By implementing these quality control measures, PCB manufacturers can ensure that their ImAg products meet the required standards and specifications.
Alternatives to ImAg
While ImAg is a popular choice for PCB surface finish, there are other alternatives available depending on the specific requirements of the application. Some of the common alternatives include:
ENIG (Electroless Nickel Immersion Gold)
ENIG is a two-layer surface finish that consists of a nickel layer (3-6 µm) and a thin gold layer (0.05-0.1 µm). ENIG offers excellent solderability, corrosion resistance, and shelf life. However, it is more expensive than ImAg and may have issues with black pad formation.
OSP (Organic Solderability Preservative)
OSP is a thin, organic coating that is applied to the copper surface to prevent oxidation. It is a low-cost and environmentally friendly option, but it has a limited shelf life and may not be suitable for multiple reflow cycles.
HASL (Hot Air Solder Leveling)
HASL involves dipping the PCB in molten solder and then using hot air to level the surface. It provides good solderability and is a low-cost option, but it results in a less flat surface compared to ImAg or ENIG.
The choice of surface finish depends on factors such as cost, solderability requirements, shelf life, and compatibility with the assembly process.
Conclusion
Immersion Silver (ImAg) is a reliable and cost-effective surface finish for PCBs. It offers excellent solderability, flatness, and electrical performance, making it suitable for a wide range of applications, including high-frequency circuits.
However, PCB manufacturers and designers must be aware of the potential challenges, such as tarnishing and whisker growth, and take appropriate measures to mitigate these risks. By implementing strict quality control and testing procedures, manufacturers can ensure the reliability and longevity of ImAg PCBs.
As the electronics industry continues to evolve, it is essential for PCB manufacturers to stay up-to-date with the latest advancements in surface finish technologies. ImAg, with its many advantages, is likely to remain a popular choice for PCB surface finish in the foreseeable future.
FAQs
-
What is Immersion Silver (ImAg) surface finish?
ImAg is a chemical process that deposits a thin layer of silver onto the exposed copper surfaces of a PCB, providing a solderable and protective finish. -
What are the advantages of using ImAg surface finish?
ImAg offers excellent solderability, flat surface for fine-pitch components, good electrical conductivity, suitability for high-frequency applications, and is RoHS compliant and environmentally friendly. -
How does ImAg compare to other surface finishes like ENIG and OSP?
ImAg is more cost-effective than ENIG and has a longer shelf life than OSP. It provides a flatter surface than HASL and is suitable for fine-pitch components. -
What are the potential challenges with ImAg surface finish?
The main challenges with ImAg are its susceptibility to tarnishing and the potential for whisker growth, which can affect the solderability and reliability of the PCB. -
How can PCB manufacturers ensure the quality and reliability of ImAg PCBs?
PCB manufacturers can implement strict quality control measures and testing procedures, such as visual inspection, thickness measurement, solderability testing, tarnish resistance testing, and whisker growth testing, to ensure the quality and reliability of ImAg PCBs.
0 Comments