What is a Hydrogen Sensor?
A hydrogen sensor is a device designed to detect and measure the presence and concentration of hydrogen gas in a given environment. These sensors play a vital role in ensuring safety by providing early warning signs of hydrogen leaks or accumulations, which can potentially lead to explosions or fires if left undetected.
Hydrogen sensors operate based on various sensing technologies, each with its own advantages and limitations. The most common types of hydrogen sensors include:
- Catalytic bead sensors
- Electrochemical sensors
- Metal oxide semiconductor (MOS) sensors
- Thermal conductivity sensors
- Optical sensors
Catalytic Bead Sensors
Catalytic bead sensors, also known as pellistors, are one of the most widely used hydrogen detection technologies. These sensors consist of two coils of fine platinum wire, each coated with a catalyst. When exposed to hydrogen gas, the catalyst on one of the coils (the active bead) promotes the combustion of hydrogen, causing the wire to heat up and change its electrical resistance. The other coil (the reference bead) remains unchanged, and the difference in resistance between the two coils is used to determine the presence and concentration of hydrogen gas.
Advantages of catalytic bead sensors include:
– High sensitivity
– Fast response time
– Long lifespan
– Relatively low cost
However, catalytic bead sensors also have some limitations:
– Susceptibility to catalyst poisoning by certain compounds (e.g., silicones, sulfur)
– Reduced sensitivity in low-oxygen environments
– Potential for false alarms due to the presence of other combustible gases
Electrochemical Sensors
Electrochemical sensors detect hydrogen gas through an electrochemical reaction that occurs within the sensor. These sensors consist of a sensing electrode, a counter electrode, and a reference electrode, all immersed in an electrolyte solution. When hydrogen gas enters the sensor, it reacts with the sensing electrode, generating an electrical current proportional to the gas concentration.
Advantages of electrochemical sensors include:
– High selectivity to hydrogen gas
– Minimal interference from other gases
– Accurate and stable measurements
– Low power consumption
Limitations of electrochemical sensors include:
– Limited operating temperature range
– Shorter lifespan compared to other sensor types
– Sensitivity to changes in humidity and pressure
Metal Oxide Semiconductor (MOS) Sensors
Metal oxide semiconductor (MOS) sensors rely on the change in electrical conductivity of a metal oxide layer when exposed to hydrogen gas. These sensors typically consist of a heating element and a sensing layer made of a metal oxide material, such as tin dioxide (SnO2) or tungsten trioxide (WO3). When hydrogen gas interacts with the sensing layer, it causes a change in the layer’s electrical resistance, which is measured and correlated to the gas concentration.
Advantages of MOS sensors include:
– High sensitivity
– Fast response and recovery times
– Long lifespan
– Ability to detect a wide range of hydrogen concentrations
Limitations of MOS sensors include:
– Sensitivity to changes in temperature and humidity
– Potential for drift over time
– Cross-sensitivity to other reducing gases
Thermal Conductivity Sensors
Thermal conductivity sensors measure the concentration of hydrogen gas by comparing its thermal conductivity to that of a reference gas, typically air or nitrogen. These sensors consist of two elements: a sensing element exposed to the sample gas and a reference element exposed to the reference gas. When hydrogen is present, it alters the thermal conductivity of the sample gas, causing a change in the temperature and electrical resistance of the sensing element.
Advantages of thermal conductivity sensors include:
– Wide measurement range
– Ability to detect high concentrations of hydrogen
– Robustness and durability
– Low maintenance requirements
Limitations of thermal conductivity sensors include:
– Lower sensitivity compared to other sensor types
– Sensitivity to changes in temperature and pressure
– Potential for cross-sensitivity to other gases with similar thermal conductivities
Optical Sensors
Optical hydrogen sensors detect the presence of hydrogen gas using various optical techniques, such as absorption spectroscopy, fluorescence, or refractive index changes. These sensors typically consist of a light source, an optical sensing element, and a detector. When hydrogen gas interacts with the sensing element, it causes a change in the optical properties of the material, which is detected and correlated to the gas concentration.
Advantages of optical sensors include:
– High selectivity to hydrogen gas
– Fast response time
– Ability to operate in harsh environments
– Immunity to electromagnetic interference
Limitations of optical sensors include:
– Higher cost compared to other sensor types
– Complexity of the sensing system
– Potential for interference from ambient light or other optical sources
Applications of Hydrogen Sensors
Hydrogen sensors find applications in a wide range of industries and settings where hydrogen gas is used, stored, or transported. Some of the key applications include:
- Petroleum refineries and chemical plants
- Fuel cell systems
- Hydrogen storage and distribution facilities
- Battery charging rooms
- Aerospace and aviation
- Laboratories and research facilities
Petroleum Refineries and Chemical Plants
In petroleum refineries and chemical plants, hydrogen is widely used in various processes, such as hydrocracking, hydrodesulfurization, and hydrogen reforming. Due to the flammable nature of hydrogen and the potential for leaks, it is crucial to have reliable hydrogen detection systems in place. Hydrogen sensors are installed at strategic locations throughout the facility to continuously monitor for any hydrogen leaks or accumulations, ensuring the safety of personnel and preventing accidents.
Fuel Cell Systems
Fuel cells are electrochemical devices that convert the chemical energy of hydrogen and oxygen into electrical energy, with water as a byproduct. Hydrogen sensors play a critical role in ensuring the safe operation of fuel cell systems by monitoring for any hydrogen leaks or malfunctions. These sensors are typically installed in the fuel cell stack, as well as in the hydrogen storage and distribution components of the system.
Hydrogen Storage and Distribution Facilities
Hydrogen storage and distribution facilities, such as hydrogen refueling stations and storage tanks, require robust hydrogen detection systems to ensure safe operations. Hydrogen sensors are installed in various locations within these facilities, including storage areas, compressor rooms, and dispensing units. These sensors continuously monitor for any hydrogen leaks or abnormal concentrations, triggering alarms and safety measures when necessary.
Battery Charging Rooms
In battery charging rooms, where lead-acid batteries are charged, hydrogen gas can be generated as a byproduct of the charging process. If allowed to accumulate, this hydrogen can create an explosive atmosphere. Hydrogen sensors are installed in battery charging rooms to detect any buildup of hydrogen gas and alert personnel to take appropriate safety measures, such as increasing ventilation or shutting down the charging process.
Aerospace and Aviation
Hydrogen is increasingly being explored as a potential fuel for aerospace and aviation applications due to its high energy density and clean combustion properties. In these applications, hydrogen sensors are used to monitor for leaks in fuel storage and distribution systems, as well as in propulsion systems that utilize hydrogen fuel cells or combustion engines.
Laboratories and Research Facilities
In laboratories and research facilities where hydrogen is used or studied, hydrogen sensors are essential for maintaining a safe working environment. These sensors are installed in various locations, such as fume hoods, gas storage areas, and experimental setups, to detect any hydrogen leaks or accumulations and alert researchers to take appropriate safety precautions.
Importance of Hydrogen Sensor Maintenance and Calibration
To ensure the reliable and accurate performance of hydrogen sensors, regular maintenance and calibration are essential. Proper maintenance helps to extend the lifespan of the sensors and minimize the risk of false alarms or sensor failures.
Some key maintenance and calibration practices for hydrogen sensors include:
- Regular cleaning and inspection of sensor components
- Replacement of consumable parts, such as filters or electrolytes, as recommended by the manufacturer
- Periodic calibration using certified hydrogen gas standards to ensure accurate measurements
- Functional testing of the sensor and associated alarm systems
- Maintenance of detailed records of sensor performance, calibration, and maintenance activities
By following these practices, facility managers and safety personnel can ensure that hydrogen sensors remain in optimal working condition, providing reliable detection and early warning of hydrogen leaks or accumulations.
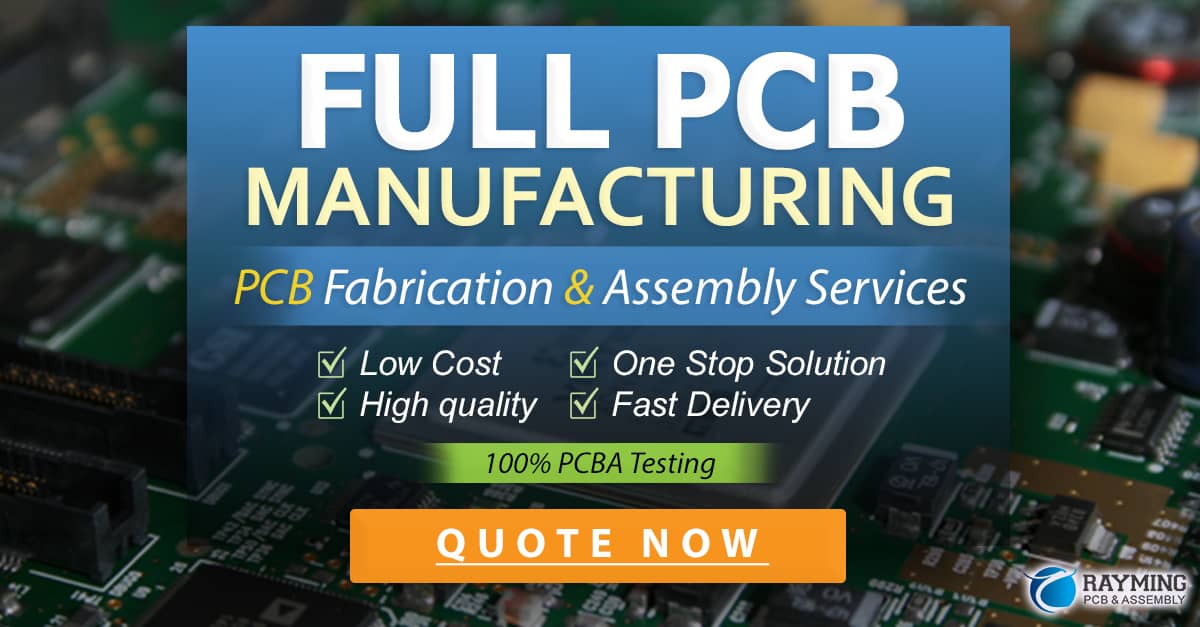
Hydrogen Sensor Selection Considerations
When selecting hydrogen sensors for a particular application, several factors should be considered to ensure optimal performance and safety. These factors include:
- Sensor type and technology
- Measurement range and accuracy
- Response time and recovery time
- Environmental conditions (e.g., temperature, humidity, pressure)
- Interfering gases and cross-sensitivity
- Power requirements and battery life
- Output options and compatibility with existing systems
- Maintenance and calibration requirements
- Cost and overall value
By carefully evaluating these factors and consulting with hydrogen sensor manufacturers or safety experts, facility managers can select the most appropriate hydrogen sensors for their specific applications, ensuring reliable detection and maximum safety.
Future Developments in Hydrogen Sensor Technology
As the use of hydrogen continues to grow across various industries, there is an increasing demand for advanced hydrogen sensor technologies that offer improved performance, reliability, and cost-effectiveness. Some of the key areas of research and development in hydrogen sensor technology include:
- Nanostructured materials for enhanced sensitivity and selectivity
- Wireless sensor networks for real-time monitoring and data analysis
- Integration of hydrogen sensors with the Internet of Things (IoT) platforms
- Development of miniaturized and low-power sensors for portable applications
- Advances in optical and fiber-optic hydrogen sensing techniques
By leveraging these emerging technologies, hydrogen sensor manufacturers can develop more advanced and reliable detection systems that meet the evolving needs of industries and applications that rely on hydrogen gas.
Frequently Asked Questions (FAQ)
- What is the detection range of a typical hydrogen sensor?
-
The detection range of a hydrogen sensor varies depending on the sensor type and technology. Generally, hydrogen sensors can detect concentrations ranging from a few parts per million (ppm) to several percent by volume. For example, catalytic bead sensors can typically detect hydrogen concentrations from 0-100% of the lower explosive limit (LEL), which is approximately 4% by volume in air.
-
How often should hydrogen sensors be calibrated?
-
The calibration frequency for hydrogen sensors depends on factors such as the sensor type, operating conditions, and manufacturer recommendations. As a general guideline, hydrogen sensors should be calibrated at least once every six months to ensure accurate and reliable performance. However, in critical applications or harsh environments, more frequent calibration may be necessary.
-
Can hydrogen sensors detect leaks in outdoor environments?
-
Yes, hydrogen sensors can be used to detect leaks in outdoor environments. However, the performance of the sensor may be affected by factors such as wind, temperature, and humidity. In outdoor applications, it is essential to select hydrogen sensors that are specifically designed for such environments and to install them in strategic locations to maximize the chances of detecting leaks.
-
Are hydrogen sensors intrinsically safe?
-
Some hydrogen sensors are designed to be intrinsically safe, which means they are engineered to prevent the ignition of flammable gases in hazardous environments. Intrinsically safe hydrogen sensors typically have low power consumption and are designed to limit the energy available for ignition. When selecting hydrogen sensors for use in hazardous areas, it is crucial to choose sensors that are certified as intrinsically safe and comply with relevant safety standards.
-
How do I choose the right hydrogen sensor for my application?
- Choosing the right hydrogen sensor for your application involves considering factors such as the sensor type and technology, measurement range and accuracy, environmental conditions, interfering gases, power requirements, and cost. It is essential to assess your specific needs and consult with hydrogen sensor manufacturers or safety experts to determine the most suitable sensor for your application. Additionally, conducting a thorough risk assessment and following relevant safety standards and guidelines can help ensure the optimal selection and implementation of hydrogen sensors in your facility.
Conclusion
Hydrogen sensors play a vital role in ensuring safety and preventing accidents in industries and applications that involve the use, storage, or transportation of hydrogen gas. By understanding the working principles, types, and applications of hydrogen sensors, as well as the importance of proper maintenance and calibration, facility managers and safety personnel can effectively implement and maintain reliable hydrogen detection systems.
As the demand for hydrogen continues to grow across various sectors, it is crucial to stay informed about the latest developments in hydrogen sensor technology and to select the most appropriate sensors for each application. By leveraging advanced sensor technologies and following best practices in hydrogen safety, we can create safer and more sustainable environments for the use of this versatile and clean energy carrier.
Sensor Type | Advantages | Limitations |
---|---|---|
Catalytic Bead | – High sensitivity – Fast response time – Long lifespan – Relatively low cost |
– Susceptibility to catalyst poisoning – Reduced sensitivity in low-oxygen environments – Potential for false alarms |
Electrochemical | – High selectivity to hydrogen gas – Minimal interference from other gases – Accurate and stable measurements – Low power consumption |
– Limited operating temperature range – Shorter lifespan compared to other sensor types – Sensitivity to changes in humidity and pressure |
Metal Oxide Semiconductor (MOS) | – High sensitivity – Fast response and recovery times – Long lifespan – Ability to detect a wide range of hydrogen concentrations |
– Sensitivity to changes in temperature and humidity – Potential for drift over time – Cross-sensitivity to other reducing gases |
Thermal Conductivity | – Wide measurement range – Ability to detect high concentrations of hydrogen – Robustness and durability – Low maintenance requirements |
– Lower sensitivity compared to other sensor types – Sensitivity to changes in temperature and pressure – Potential for cross-sensitivity to other gases with similar thermal conductivities |
Optical | – High selectivity to hydrogen gas – Fast response time – Ability to operate in harsh environments – Immunity to electromagnetic interference |
– Higher cost compared to other sensor types – Complexity of the sensing system – Potential for interference from ambient light or other optical sources |
0 Comments