What is PCB Soldermask?
PCB soldermask, also known as solder resist or solder mask, is a thin layer of polymer applied to the copper traces of a PCB. Its primary functions include:
- Protecting the copper traces from oxidation
- Providing electrical insulation between adjacent traces
- Preventing solder bridges during the soldering process
- Improving the PCB’s overall durability and resistance to environmental factors
Soldermask is typically applied using screen printing or photoimaging techniques and is available in various colors, with green being the most common.
Why is PCB Soldermask Testing Important?
Testing the PCB soldermask is essential to ensure that it meets the required standards and can perform its intended functions effectively. Some of the key reasons for conducting soldermask testing include:
- Ensuring proper adhesion between the soldermask and the copper traces
- Verifying the soldermask’s ability to withstand the soldering process without deterioration
- Confirming the soldermask’s electrical insulation properties
- Checking the soldermask’s resistance to chemicals, moisture, and other environmental factors
- Guaranteeing the consistency and uniformity of the soldermask across the entire PCB
By conducting thorough soldermask testing, PCB manufacturers can identify and address any issues early in the production process, reducing the risk of defects and ensuring the overall quality of the final product.
PCB Soldermask Testing Methods
There are several methods for testing PCB soldermask, each focusing on different aspects of its performance and quality. Some of the most common testing methods include:
1. Adhesion Testing
Adhesion testing evaluates the bond strength between the soldermask and the copper traces. This test is crucial to ensure that the soldermask remains firmly attached to the PCB during the manufacturing process and throughout the product’s life cycle. There are two primary methods for adhesion testing:
1.1. Tape Test (IPC-TM-650 2.4.1)
The tape test involves applying a piece of pressure-sensitive tape to the soldermask surface and then quickly removing it at a 90-degree angle. The amount of soldermask removed by the tape is then visually inspected and rated according to the IPC-TM-650 2.4.1 standard.
Classification | Description |
---|---|
5B | No peeling or removal |
4B | Trace peeling or removal along edges |
3B | Jagged removal along edges with 5-15% area removed |
2B | Jagged removal along most edges with 15-35% area removed |
1B | Removal from most of the area (35-65%) under the tape |
0B | Removal beyond the area under the tape |
1.2. Cross-Cut Test (IPC-TM-650 2.4.2)
The cross-cut test involves making a series of perpendicular cuts through the soldermask and into the copper traces using a sharp blade. A piece of pressure-sensitive tape is then applied over the cut area and quickly removed at a 90-degree angle. The amount of soldermask removed by the tape is visually inspected and rated according to the IPC-TM-650 2.4.2 standard.
Classification | Description |
---|---|
5B | The edges of the cuts are completely smooth; none of the squares of the lattice is detached |
4B | Small flakes of the coating are detached at intersections; less than 5% of the area is affected |
3B | Small flakes of the coating are detached along edges and at intersections of cuts; 5-15% of the area is affected |
2B | The coating has flaked along the edges and on parts of the squares; 15-35% of the area is affected |
1B | The coating has flaked along the edges of cuts in large ribbons and whole squares have detached; 35-65% of the area is affected |
0B | Flaking and detachment worse than Grade 1 |
2. Thickness Testing
Soldermask Thickness testing is essential to ensure that the soldermask layer is uniform and meets the specified requirements. Insufficient thickness can lead to inadequate insulation and protection, while excessive thickness can cause issues with component placement and solderability. There are two primary methods for measuring soldermask thickness:
2.1. Microscopic Examination (IPC-TM-650 2.2.8)
Microscopic examination involves cross-sectioning a sample of the PCB and measuring the soldermask thickness using a calibrated microscope. This method provides accurate measurements and allows for the inspection of the soldermask’s uniformity across the board.
2.2. Eddy Current Testing (IPC-TM-650 2.2.13)
Eddy current testing is a non-destructive method that uses electromagnetic induction to measure the soldermask thickness. This technique involves placing a probe on the soldermask surface and measuring the change in the probe’s impedance, which correlates to the soldermask thickness. Eddy current testing is faster and more convenient than microscopic examination but may not provide the same level of accuracy.
3. Resistance Testing
Resistance testing evaluates the soldermask’s ability to withstand various environmental factors and maintain its protective properties over time. Some of the key resistance tests include:
3.1. Chemical Resistance (IPC-TM-650 2.3.25)
Chemical resistance testing involves exposing the soldermask to a range of chemicals, such as acids, bases, solvents, and fluxes, for a specified duration. The soldermask is then visually inspected for any signs of degradation, discoloration, or loss of adhesion.
3.2. Moisture and Insulation Resistance (IPC-TM-650 2.6.3)
Moisture and insulation resistance testing involves subjecting the PCB to high humidity conditions (typically 90-95% relative humidity) at an elevated temperature (usually 40°C) for a specified duration. The insulation resistance between the conductors is then measured using a megohmmeter to ensure that the soldermask maintains its electrical insulation properties under these conditions.
3.3. Thermal Shock (IPC-TM-650 2.6.7)
Thermal shock testing involves exposing the PCB to rapid temperature changes, typically from a high temperature (e.g., 125°C) to a low temperature (e.g., -55°C), for a specified number of cycles. The soldermask is then visually inspected for any signs of cracking, delamination, or other damage.
4. Solder Resistance Testing
Solder resistance testing evaluates the soldermask’s ability to withstand the soldering process without degradation or loss of adhesion. There are two primary methods for solder resistance testing:
4.1. Solder Float Test (IPC-TM-650 2.4.13)
The solder float test involves floating a sample of the PCB on the surface of molten solder for a specified duration (typically 10-20 seconds) at a temperature of 288°C. The soldermask is then visually inspected for any signs of degradation, discoloration, or loss of adhesion.
4.2. Solder Dip Test (IPC-TM-650 2.4.14)
The solder dip test involves dipping a sample of the PCB into molten solder at a temperature of 288°C for a specified duration (typically 5-10 seconds). The soldermask is then visually inspected for any signs of degradation, discoloration, or loss of adhesion.
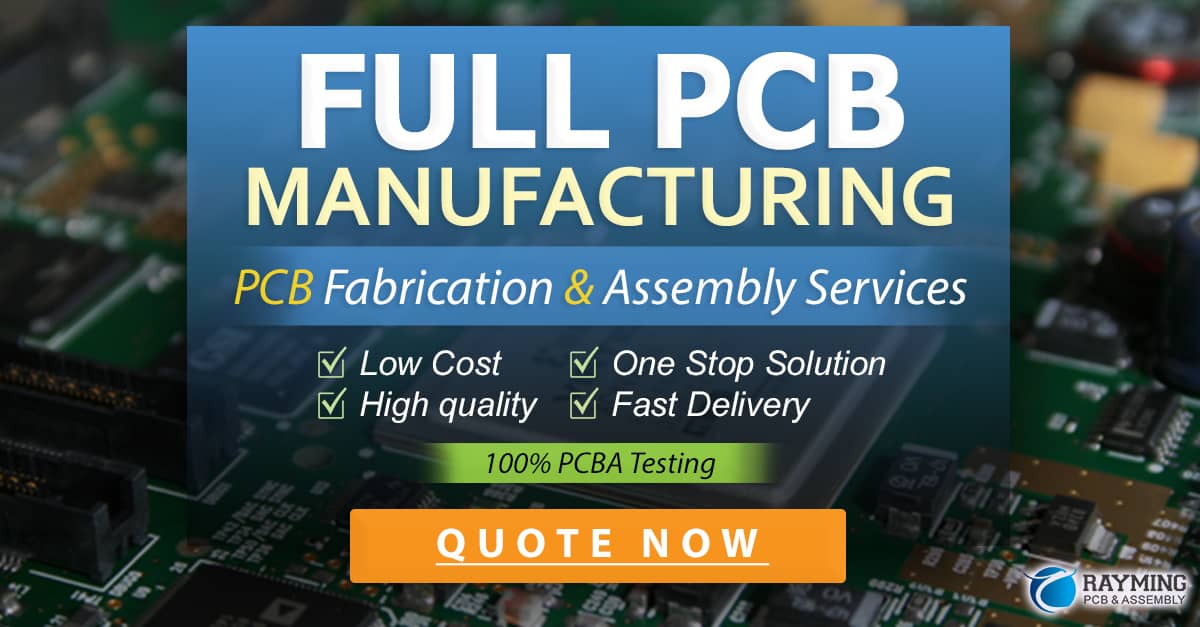
Frequently Asked Questions (FAQ)
1. What is the most common color for PCB soldermask?
The most common color for PCB soldermask is green. However, other colors such as blue, red, yellow, and black are also available.
2. Can PCB soldermask be applied selectively to certain areas of the board?
Yes, soldermask can be applied selectively to specific areas of the PCB using techniques such as spot masking or selective masking. This allows for the exposure of certain areas of the board, such as contact pads or test points, while protecting the rest of the circuitry.
3. How does the soldermask affect the PCB’s impedance?
The soldermask’s dielectric constant and thickness can affect the PCB’s impedance. Thicker soldermask layers or those with higher dielectric constants can increase the impedance of the traces, which may impact high-frequency signal integrity. It is essential to consider these factors when designing PCBs for high-speed applications.
4. Can damaged soldermask be repaired?
In some cases, minor damage to the soldermask can be repaired using specialized touch-up materials. However, for more extensive damage or critical applications, it is generally recommended to replace the affected PCB rather than attempt a repair.
5. How often should PCB soldermask testing be performed?
PCB soldermask testing should be performed regularly throughout the manufacturing process to ensure consistent quality and catch any issues early on. The specific frequency of testing may vary depending on the production volume, complexity of the PCB design, and customer requirements. It is common to perform soldermask testing on a sample basis for each production lot or at predetermined intervals during the manufacturing process.
Conclusion
PCB soldermask testing is a critical aspect of the PCB manufacturing process, ensuring that the protective layer applied to the copper traces meets the required standards and can perform its intended functions effectively. By conducting thorough testing using methods such as adhesion testing, thickness testing, resistance testing, and solder resistance testing, PCB manufacturers can identify and address any issues early in the production process, reducing the risk of defects and ensuring the overall quality of the final product.
As PCB designs continue to advance and become more complex, the importance of reliable soldermask testing will only continue to grow. By staying up-to-date with the latest testing methods and standards, PCB manufacturers can remain competitive and deliver high-quality products that meet the ever-increasing demands of the electronics industry.
0 Comments