Introduction to Multilayer PCB Manufacturing
Multilayer PCBs (Printed Circuit Boards) are essential components in modern electronic devices, offering increased functionality and performance in a compact form factor. The manufacturing process of multilayer PCBs involves several intricate steps that require precision and expertise. In this comprehensive guide, we will delve into the various aspects of multilayer PCB manufacturing, providing insights into the techniques, materials, and quality control measures involved in creating these complex circuit boards.
Understanding the Basics of Multilayer PCBs
What is a Multilayer PCB?
A multilayer PCB is a printed circuit board that consists of three or more conductive copper layers laminated together with insulating material. These layers are interconnected using plated through-holes (PTHs) or vias, allowing for more complex circuitry and higher component density compared to single or double-layer PCBs.
Advantages of Multilayer PCBs
- Increased circuit density and functionality
- Improved signal integrity and reduced electromagnetic interference (EMI)
- Enhanced thermal management and power distribution
- Reduced overall board size and weight
- Higher reliability and durability
Multilayer PCB Manufacturing Process
Step 1: PCB Design and Layout
The first step in manufacturing a multilayer PCB is to create a detailed design and layout using specialized PCB design software. This involves:
- Schematic capture: Creating a graphical representation of the circuit’s components and their interconnections
- Component placement: Arranging the components on the board for optimal functionality and manufacturability
- Routing: Connecting the components using conductive traces while adhering to design rules and constraints
- Layer stackup: Determining the number and arrangement of conductive and insulating layers
Step 2: Material Selection and Preparation
Choosing the right materials is crucial for ensuring the quality and reliability of the multilayer PCB. The main materials used in PCB manufacturing include:
- Substrate: FR-4 is the most common substrate material, offering good mechanical and electrical properties
- Copper foil: Typically available in thicknesses ranging from 0.5 oz to 2 oz per square foot
- Prepreg: A pre-impregnated composite material used as an insulating layer between the conductive layers
- Solder mask: A protective coating applied to the outer layers to prevent short circuits and improve solderability
Step 3: Inner Layer Fabrication
The inner layers of the multilayer PCB are fabricated using the following steps:
- Printing the circuit pattern onto the copper-clad laminate using photoresist
- Exposing the photoresist to UV light through a photomask, hardening the exposed areas
- Developing the photoresist to remove the unexposed areas, revealing the copper to be etched
- Etching away the unwanted copper using a chemical solution, leaving only the desired circuit pattern
- Stripping the remaining photoresist and cleaning the board
Step 4: Lamination and Bonding
Once the inner layers are fabricated, they are aligned and laminated together with the prepreg material using heat and pressure. This process ensures a strong bond between the layers and creates a solid, multi-layered structure.
Step 5: Drilling and Plating
To interconnect the layers of the multilayer PCB, holes are drilled through the board using CNC drilling machines. These holes are then plated with copper to create conductive pathways between the layers, known as plated through-holes (PTHs) or vias.
Step 6: Outer Layer Processing
The outer layers of the multilayer PCB undergo a similar process to the inner layers, including:
- Printing the circuit pattern and applying photoresist
- Exposing, developing, and etching the copper
- Applying the solder mask and silkscreen for component identification and protection
Step 7: Surface Finishing
To enhance the solderability and protect the exposed copper, a surface finish is applied to the PCB. Common surface finishes include:
- HASL (Hot Air Solder Leveling): A tin-lead alloy is applied to the copper pads and then leveled using hot air
- ENIG (Electroless Nickel Immersion Gold): A thin layer of gold is deposited over a nickel barrier, providing excellent solderability and shelf life
- OSP (Organic Solderability Preservative): A thin, organic coating is applied to the copper, protecting it from oxidation
Step 8: Electrical Testing and Quality Control
Before the multilayer PCB is shipped to the customer, it undergoes rigorous electrical testing and quality control procedures to ensure its functionality and reliability. This includes:
- Continuity testing: Verifying that all connections are intact and there are no open circuits
- Insulation resistance testing: Checking for any leakage or short circuits between layers or traces
- Visual inspection: Examining the board for any defects, such as scratches, cracks, or contamination
- Microsectioning: Analyzing cross-sections of the board to verify the integrity of the plating and lamination
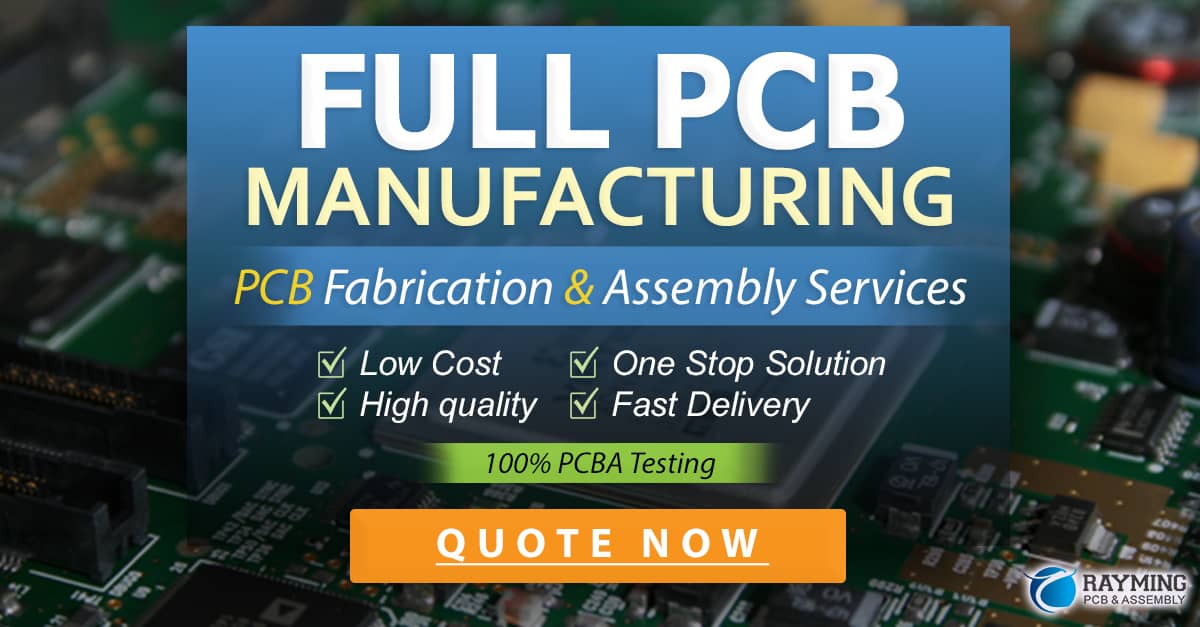
Challenges in Multilayer PCB Manufacturing
Manufacturing multilayer PCBs comes with its own set of challenges that manufacturers must address to ensure high-quality and reliable products:
Signal Integrity
As the number of layers and the complexity of the circuitry increase, maintaining signal integrity becomes more challenging. Manufacturers must consider factors such as impedance matching, crosstalk, and signal reflection when designing and fabricating multilayer PCBs.
Thermal Management
With higher component density and increased power requirements, thermal management becomes crucial in multilayer PCBs. Manufacturers must incorporate adequate heat dissipation techniques, such as thermal vias or heat sinks, to prevent overheating and ensure optimal performance.
Manufacturing Tolerances
Multilayer PCBs require tight manufacturing tolerances to ensure proper alignment and interconnection between layers. Any deviations can lead to signal integrity issues or even complete failure of the board. Manufacturers must adhere to strict quality control measures and use advanced equipment to maintain these tolerances.
Cost Considerations
The complexity and materials involved in manufacturing multilayer PCBs can significantly impact the overall cost. Manufacturers must strike a balance between meeting the customer’s requirements and keeping the costs competitive in the market.
Frequently Asked Questions (FAQ)
-
Q: What is the minimum number of layers required for a PCB to be considered a multilayer PCB?
A: A PCB must have at least three conductive layers to be classified as a multilayer PCB. Boards with fewer layers are referred to as single-layer or double-layer PCBs. -
Q: What is the purpose of using prepreg material in multilayer PCB manufacturing?
A: Prepreg, or pre-impregnated material, is used as an insulating layer between the conductive layers of a multilayer PCB. It provides electrical insulation and helps bond the layers together during the lamination process. -
Q: How do vias connect the different layers in a multilayer PCB?
A: Vias are plated through-holes that are drilled through the multilayer PCB and then plated with copper. They create conductive pathways between the different layers, allowing signals to travel vertically through the board. -
Q: What is the difference between HASL and ENIG surface finishes?
A: HASL (Hot Air Solder Leveling) is a tin-lead alloy surface finish that provides good solderability but may result in uneven surfaces. ENIG (Electroless Nickel Immersion Gold) offers excellent solderability and a flat surface, but it is more expensive than HASL. -
Q: How can manufacturers ensure the reliability and functionality of multilayer PCBs?
A: Manufacturers employ various quality control measures, such as electrical testing, visual inspection, and microsectioning, to verify the integrity and functionality of multilayer PCBs. Adherence to strict manufacturing tolerances and the use of advanced equipment also contribute to ensuring the reliability of the final product.
Conclusion
Multilayer PCB manufacturing is a complex process that involves numerous steps, materials, and techniques. Understanding the intricacies of this process is essential for designing and producing high-quality, reliable circuit boards that meet the ever-increasing demands of modern electronic devices. By adhering to best practices, maintaining strict quality control, and staying up-to-date with the latest manufacturing technologies, PCB Manufacturers can overcome the challenges associated with multilayer PCB production and deliver products that exceed customer expectations.
Layer Count | Typical Applications | Advantages | Disadvantages |
---|---|---|---|
4-8 layers | – Medium complexity devices – Automotive electronics – Industrial control systems |
– Increased functionality and circuit density – Improved signal integrity – Moderate cost |
– Limited thermal management – Increased manufacturing complexity |
8-16 layers | – High-performance computing – Telecommunications equipment – Medical devices |
– High circuit density and functionality – Enhanced signal integrity and EMI reduction – Improved thermal management |
– Higher cost – Increased manufacturing complexity and tolerances |
16+ layers | – Advanced networking equipment – Aerospace and defense systems – High-end servers |
– Extremely high circuit density and functionality – Superior signal integrity and EMI reduction – Advanced thermal management capabilities |
– Very high cost – Highly complex manufacturing process – Strict tolerances and quality control requirements |
As the electronics industry continues to evolve, the demand for more advanced and compact multilayer PCBs will only grow. By staying at the forefront of manufacturing technologies and processes, PCB manufacturers can meet these challenges head-on and contribute to the development of innovative electronic solutions that shape our future.
0 Comments