Understanding the PCB Supply Chain
The PCB supply chain consists of multiple stages, each of which is susceptible to disruptions. These stages include:
- Raw material procurement
- PCB fabrication
- Component sourcing
- PCB Assembly
- Testing and quality control
- Packaging and shipping
Disruptions can occur at any of these stages, and it is essential to have a comprehensive understanding of the entire supply chain to identify potential risks and develop contingency plans.
Common Causes of PCB Supply Chain Disruptions
Several factors can contribute to PCB supply chain disruptions, including:
-
Global economic fluctuations: Economic instability, currency fluctuations, and changes in trade policies can impact the availability and pricing of raw materials and components.
-
Natural disasters: Earthquakes, floods, and other natural calamities can disrupt the production and transportation of PCBs and components.
-
Geopolitical events: Political unrest, trade disputes, and sanctions can affect the supply of raw materials and components from specific regions.
-
Capacity constraints: Limited production capacity at PCB fabrication and assembly facilities can lead to longer lead times and delays.
-
Quality issues: Quality problems with raw materials, components, or finished PCBs can result in rework, delays, and increased costs.
Strategies for Managing PCB Supply Chain Disruptions
To effectively manage PCB supply chain disruptions, consider implementing the following strategies:
1. Diversify Suppliers
Relying on a single supplier for critical components or services can be risky. By diversifying your supplier base, you can reduce the impact of disruptions caused by issues with a specific supplier. Consider the following when diversifying your suppliers:
- Geographic location: Spread your suppliers across different regions to minimize the impact of localized disruptions.
- Capability and capacity: Ensure that your suppliers have the necessary capabilities and capacity to meet your requirements.
- Financial stability: Assess the financial health of potential suppliers to ensure they can withstand economic challenges.
2. Establish Strong Supplier Relationships
Building strong, long-term relationships with your suppliers can help mitigate the impact of supply chain disruptions. Consider the following:
- Regular communication: Maintain open and frequent communication with your suppliers to stay informed about potential issues and collaborate on solutions.
- Partnership approach: Treat your suppliers as partners and work together to improve processes, reduce costs, and enhance quality.
- Supplier development: Invest in supplier development programs to help your suppliers improve their capabilities and resilience.
3. Implement Supply Chain Visibility Tools
Supply chain visibility tools, such as enterprise resource planning (ERP) systems and supply chain management software, can help you monitor your PCB supply chain in real-time. These tools can provide:
- Real-time inventory data: Track inventory levels across your supply chain to identify potential shortages and take proactive measures.
- Supplier performance metrics: Monitor supplier performance, including lead times, quality, and on-time delivery, to identify potential issues early.
- Alerts and notifications: Set up alerts and notifications to inform you of potential disruptions, allowing you to take timely action.
4. Maintain Adequate Inventory Buffers
Maintaining adequate inventory buffers can help you weather short-term supply chain disruptions. However, it is essential to strike a balance between holding too much inventory, which ties up capital, and not having enough, which can lead to stockouts. Consider the following when determining your inventory levels:
- Lead times: Assess the lead times for critical components and adjust your inventory levels accordingly.
- Demand volatility: Analyze historical demand patterns and adjust inventory levels to account for potential spikes in demand.
- Cost of stockouts: Evaluate the cost of stockouts, including lost sales and customer dissatisfaction, when determining inventory levels.
5. Develop Contingency Plans
Despite your best efforts, supply chain disruptions can still occur. Developing contingency plans can help you respond quickly and effectively to minimize the impact of disruptions. Consider the following when developing your contingency plans:
- Identify critical components and suppliers: Identify the components and suppliers that are most critical to your PCB assembly process and prioritize contingency planning for these areas.
- Develop alternative sourcing strategies: Identify alternative suppliers or sourcing strategies that can be activated quickly in the event of a disruption.
- Establish communication protocols: Develop clear communication protocols for informing stakeholders, including customers and employees, about disruptions and your response plans.
6. Foster a Culture of Continuous Improvement
Continuously improving your PCB assembly processes can help you build resilience and adaptability in the face of supply chain disruptions. Consider the following:
- Encourage innovation: Foster a culture of innovation and encourage employees to suggest process improvements and new ideas.
- Invest in technology: Stay up-to-date with the latest PCB assembly technologies and invest in equipment and software that can improve efficiency and flexibility.
- Conduct regular risk assessments: Regularly assess your supply chain risks and update your contingency plans accordingly.
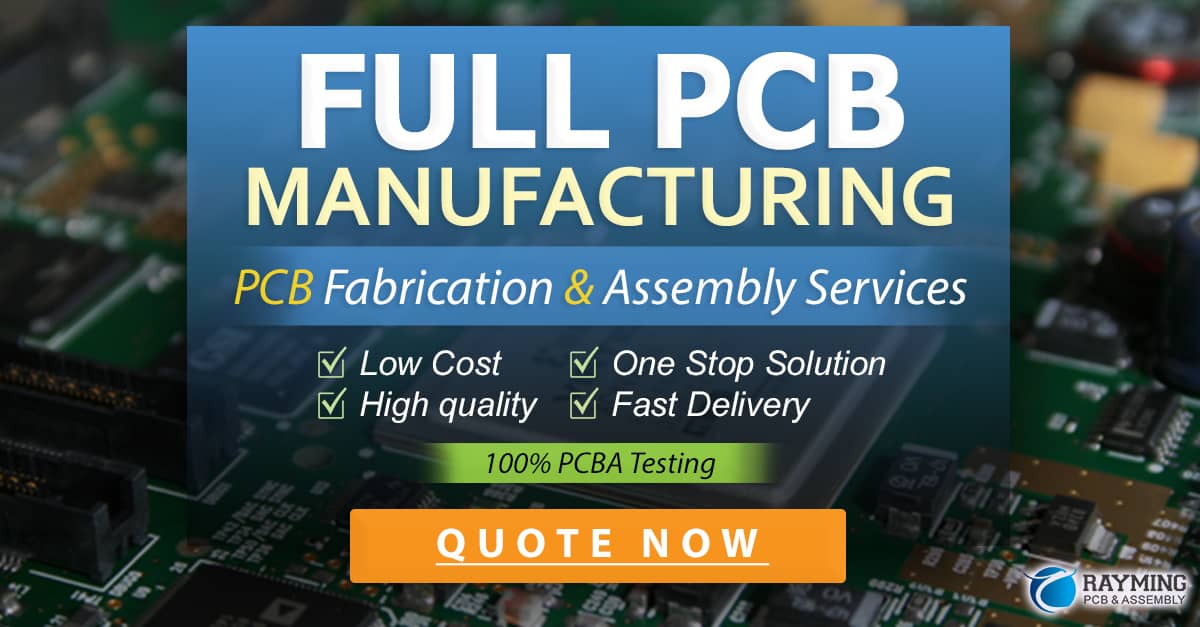
The Role of PCB Design in Supply Chain Resilience
In addition to the strategies mentioned above, PCB design plays a crucial role in building supply chain resilience. Consider the following design best practices:
-
Design for manufacturability (DFM): Designing PCBs with manufacturability in mind can help reduce the risk of quality issues and production delays. This includes following design guidelines, such as minimum trace widths and spacing, and avoiding complex or unnecessary features.
-
Component selection: When selecting components for your PCB, consider factors such as availability, lead times, and the number of suppliers. Avoid using obsolete or hard-to-find components whenever possible.
-
Standardization: Standardizing components and design features across your PCB portfolio can help reduce the impact of supply chain disruptions. This allows for greater flexibility in sourcing and can help you maintain production even if specific components become unavailable.
-
Design for supply chain: Collaborate with your supply chain partners, including suppliers and PCB fabrication and assembly providers, during the design process. This can help ensure that your design is optimized for their capabilities and can help identify potential supply chain risks early in the process.
Frequently Asked Questions (FAQ)
-
What is a PCB supply chain disruption?
A PCB supply chain disruption is any event or issue that interrupts the smooth flow of materials, components, or services required for the production of printed circuit boards. This can include disruptions in raw material availability, component shortages, transportation delays, and quality issues. -
How can I identify potential supply chain risks?
To identify potential supply chain risks, conduct regular risk assessments that consider factors such as supplier concentration, geographic location, lead times, and quality performance. Engage with your suppliers and industry partners to stay informed about potential issues and trends. -
What are the benefits of diversifying my supplier base?
Diversifying your supplier base can help reduce the impact of disruptions caused by issues with a specific supplier. It allows you to spread risk across multiple suppliers, regions, and capabilities, making your supply chain more resilient. -
How can supply chain visibility tools help manage disruptions?
Supply chain visibility tools, such as ERP systems and supply chain management software, can provide real-time data on inventory levels, supplier performance, and potential disruptions. This allows you to identify issues early and take proactive measures to mitigate their impact. -
What role does PCB design play in supply chain resilience?
PCB design plays a crucial role in building supply chain resilience. By designing for manufacturability, selecting appropriate components, standardizing design features, and collaborating with supply chain partners, you can reduce the risk of quality issues, production delays, and supply chain disruptions.
PCB Supply Chain Stage | Potential Disruption | Mitigation Strategy |
---|---|---|
Raw Material Procurement | Shortage of key materials | Diversify suppliers, maintain adequate inventory buffers |
PCB Fabrication | Capacity constraints, quality issues | Partner with multiple fabrication facilities, implement quality control measures |
Component Sourcing | Obsolescence, long lead times | Select readily available components, establish strong supplier relationships |
PCB Assembly | Equipment breakdowns, skilled labor shortage | Implement preventive maintenance, invest in training and development |
Testing and Quality Control | Inadequate testing, quality issues | Establish robust testing procedures, collaborate with suppliers on quality improvement |
Packaging and Shipping | Transportation delays, customs issues | Diversify shipping methods, work with experienced logistics providers |
In conclusion, managing PCB supply chain disruptions requires a proactive and multi-faceted approach. By diversifying suppliers, establishing strong relationships, implementing visibility tools, maintaining adequate inventory buffers, developing contingency plans, fostering continuous improvement, and optimizing PCB design, you can build a more resilient and adaptable supply chain. By staying vigilant and prepared, you can minimize the impact of disruptions and ensure the smooth functioning of your PCB assembly processes.
0 Comments