Introduction to PCB Soldering
PCB soldering is a crucial process in the manufacturing of electronic devices. It involves the joining of electronic components to a printed circuit board (PCB) using a molten metal alloy called solder. The quality of the solder joint determines the reliability and performance of the electronic device. One of the most important aspects of PCB soldering is the formation of solder balls.
What are Solder Balls?
Solder balls are small spheres of solder that are used to connect electronic components to a PCB. They are typically made of a tin-lead alloy, although lead-free alloys are becoming increasingly popular due to environmental concerns. Solder balls are used in a variety of PCB Assembly techniques, including ball grid array (BGA), chip scale packaging (CSP), and flip-chip packaging.
Why are Solder Balls Important?
Solder balls play a critical role in the reliability and performance of electronic devices. They provide a strong mechanical and electrical connection between the electronic component and the PCB. A good solder ball should have a uniform shape, size, and composition. It should also be free of defects such as voids, cracks, or contamination.
Poor quality solder balls can lead to a variety of problems, including:
- Open or intermittent connections
- Short circuits
- Reduced electrical conductivity
- Reduced mechanical strength
- Reduced thermal conductivity
These problems can cause the electronic device to malfunction or fail prematurely. Therefore, it is essential to ensure that the solder balls used in PCB assembly are of high quality.
Factors Affecting Solder Ball Quality
Several factors can affect the quality of solder balls used in PCB assembly. These include:
Solder Alloy Composition
The composition of the solder alloy used to make the solder balls can have a significant impact on their quality. The most common solder alloys used in PCB assembly are tin-lead (SnPb) and lead-free alloys such as tin-silver-copper (SAC).
SnPb alloys have been used in PCB assembly for many years due to their low melting point, good wetting properties, and low cost. However, the use of lead in electronic devices has been restricted due to environmental and health concerns. As a result, lead-free alloys such as SAC have become increasingly popular.
SAC alloys have a higher melting point than SnPb alloys, which can make them more difficult to work with. However, they offer several advantages, including better mechanical strength, increased resistance to fatigue and creep, and improved thermal cycling performance.
The choice of solder alloy composition depends on several factors, including the application, the PCB design, and the environmental requirements.
Solder Ball Size and Shape
The size and shape of the solder balls can also affect their quality. Solder balls that are too small or too large can lead to problems such as bridging or open connections. Solder balls that are not perfectly spherical can also cause issues, such as uneven stress distribution or reduced contact area.
The size of the solder balls is typically determined by the pitch of the PCB. The pitch is the distance between the centers of adjacent pads or holes on the PCB. Smaller pitch sizes require smaller solder balls to avoid bridging or short circuits.
The shape of the solder balls is typically determined by the manufacturing process used to produce them. There are several methods for producing solder balls, including:
- Droplet formation: Molten solder is dispensed through a nozzle to form droplets that solidify into spherical balls.
- Gas atomization: Molten solder is atomized into small droplets using a high-pressure gas stream. The droplets solidify into spherical balls as they cool.
- Plasma atomization: Molten solder is atomized into small droplets using a plasma torch. The droplets solidify into spherical balls as they cool.
The choice of manufacturing process depends on several factors, including the solder alloy composition, the desired ball size and shape, and the production volume.
Surface Finish
The surface finish of the PCB and the electronic components can also affect the quality of the solder joint. The surface finish is a thin layer of metal that is applied to the PCB pads and component leads to improve solderability and protect against oxidation.
The most common surface finishes used in PCB assembly are:
- Hot air solder leveling (HASL): A thin layer of solder is applied to the PCB pads and then leveled using hot air.
- Electroless nickel immersion gold (ENIG): A layer of nickel is plated onto the PCB pads, followed by a thin layer of gold.
- Immersion silver (IAg): A thin layer of silver is plated onto the PCB pads.
- Organic solderability preservative (OSP): A thin layer of organic compound is applied to the PCB pads to protect against oxidation.
The choice of surface finish depends on several factors, including the solder alloy composition, the PCB design, and the environmental requirements.
Flux
Flux is a chemical compound that is used to remove oxides and other contaminants from the surface of the PCB and component leads during soldering. It also helps to improve the wetting and flow properties of the solder.
There are several types of flux used in PCB assembly, including:
- Rosin-based flux: Contains rosin, a natural resin derived from pine trees. It is available in several activity levels, ranging from mild to highly active.
- Water-soluble flux: Contains organic acids that are soluble in water. It requires cleaning after soldering to remove residues.
- No-clean flux: Contains a low level of solids that do not require cleaning after soldering.
The choice of flux depends on several factors, including the solder alloy composition, the PCB design, and the environmental requirements.
Solder Ball Manufacturing Process
The manufacturing process for solder balls typically involves several steps, including:
Melting the Solder Alloy
The first step in manufacturing solder balls is to melt the solder alloy. This is typically done in a crucible or melting pot that is heated to a temperature above the melting point of the alloy. The temperature and time required for melting depend on the alloy composition and the size of the batch.
Atomizing the Molten Solder
Once the solder alloy is melted, it is atomized into small droplets using one of the methods described earlier (droplet formation, gas atomization, or plasma atomization). The size and shape of the droplets depend on several factors, including the atomization method, the nozzle size, and the gas pressure.
Cooling and Solidifying the Droplets
After atomization, the molten solder droplets are allowed to cool and solidify into spherical balls. This is typically done in a cooling chamber or tower that is designed to control the cooling rate and prevent oxidation.
Sieving and Sorting the Solder Balls
Once the solder balls have solidified, they are sieved and sorted by size using a series of mesh screens. The size of the mesh openings determines the size range of the solder balls. The sorted solder balls are then packaged for shipment to the customer.
Quality Control
Throughout the manufacturing process, several quality control measures are implemented to ensure that the solder balls meet the required specifications for size, shape, and composition. These measures may include:
- Visual inspection: The solder balls are inspected visually for defects such as voids, cracks, or contamination.
- X-ray inspection: The solder balls are X-rayed to check for internal defects such as voids or inclusions.
- Composition analysis: The composition of the solder balls is analyzed using techniques such as X-ray fluorescence (XRF) or inductively coupled plasma (ICP) to ensure that they meet the required specifications.
- Mechanical testing: The mechanical properties of the solder balls, such as hardness and tensile strength, are tested to ensure that they meet the required specifications.
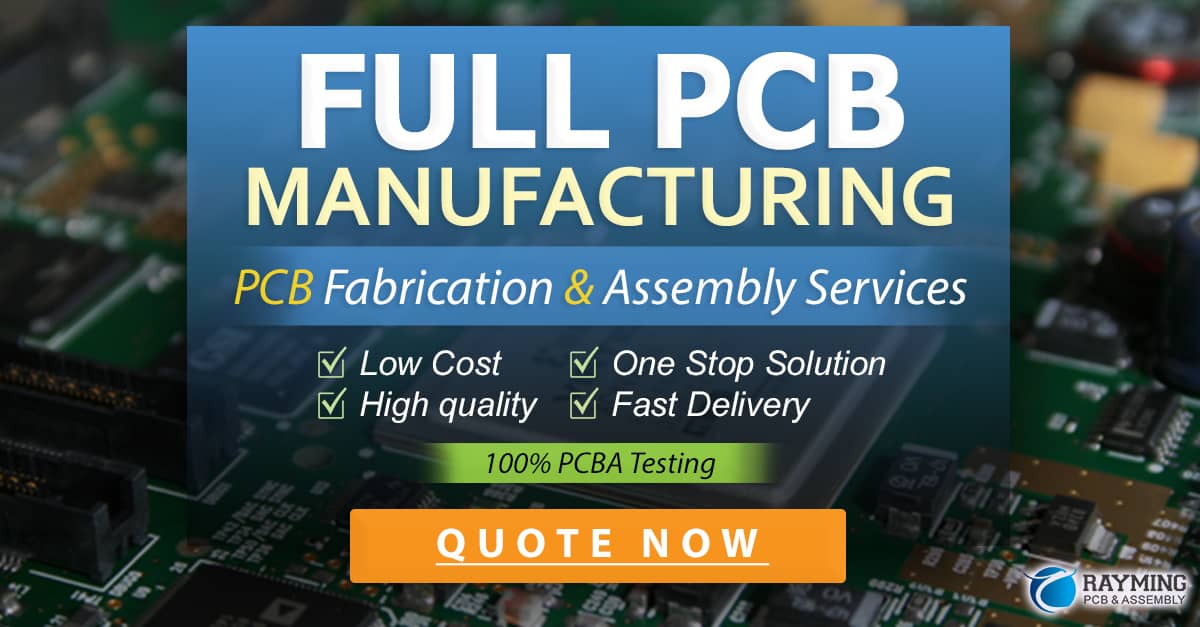
Best Practices for PCB Soldering with Solder Balls
To ensure high-quality solder joints when using solder balls in PCB assembly, several best practices should be followed, including:
Proper Storage and Handling
Solder balls should be stored in a cool, dry place away from sources of contamination such as dust or moisture. They should also be handled with care to prevent damage or deformation.
Proper Placement
Solder balls should be placed accurately on the PCB pads using a pick-and-place machine or a stencil printer. The placement should be checked visually or with a camera system to ensure that the balls are centered on the pads and not touching each other.
Proper Reflow Profile
The reflow profile used for soldering solder balls should be optimized for the specific alloy composition and PCB design. The profile should include a preheat stage to activate the flux and remove volatiles, a soak stage to allow the components to reach the same temperature, a reflow stage to melt the solder and form the joint, and a cooling stage to solidify the joint.
Proper Cleaning
After soldering, any flux residues should be removed using an appropriate cleaning method, such as aqueous cleaning or solvent cleaning. Cleaning is especially important for water-soluble fluxes, which can leave corrosive residues if not removed.
Proper Inspection
After soldering, the solder joints should be inspected visually or with a microscope to check for defects such as bridging, open joints, or voids. X-ray inspection may also be used to check for internal defects.
Troubleshooting Common Solder Ball Issues
Despite following best practices, issues can still arise during PCB soldering with solder balls. Some common issues and their potential causes and solutions are:
Bridging
Bridging occurs when solder balls touch each other, creating a short circuit between adjacent pads. Potential causes include:
- Solder balls too large for the pad size or pitch
- Improper placement of solder balls
- Excessive solder paste or flux
- Improper reflow profile
Solutions include:
- Use smaller solder balls or increase the pad size or pitch
- Improve the accuracy of solder ball placement
- Reduce the amount of solder paste or flux
- Optimize the reflow profile
Open Joints
Open joints occur when there is no electrical connection between the solder ball and the pad. Potential causes include:
- Insufficient solder paste or flux
- Oxidation or contamination on the pad surface
- Improper reflow profile
- Solder ball not centered on the pad
Solutions include:
- Increase the amount of solder paste or flux
- Clean the pad surface before soldering
- Optimize the reflow profile
- Improve the accuracy of solder ball placement
Voids
Voids are small air pockets or holes inside the solder joint. Potential causes include:
- Trapped flux or volatiles
- Improper reflow profile
- Contamination or oxidation on the pad or component surface
Solutions include:
- Use a vacuum reflow oven to remove trapped air
- Optimize the reflow profile
- Clean the pad and component surfaces before soldering
Head-in-Pillow (HIP)
HIP defects occur when the solder ball does not collapse fully during reflow, resulting in a partial or incomplete joint. Potential causes include:
- Oxidation or contamination on the ball or pad surface
- Improper reflow profile
- Insufficient flux or solder paste
- Warped or uneven PCB or component
Solutions include:
- Clean the ball and pad surfaces before soldering
- Optimize the reflow profile
- Increase the amount of flux or solder paste
- Use a PCB or component with better flatness and coplanarity
Conclusion
Making good solder balls for PCB assembly requires careful control of several factors, including the solder alloy composition, ball size and shape, surface finish, and flux. The manufacturing process for solder balls typically involves melting the alloy, atomizing it into small droplets, cooling and solidifying the droplets, and sieving and sorting the balls by size.
To ensure high-quality solder joints when using solder balls in PCB assembly, several best practices should be followed, including proper storage and handling, placement, reflow profiling, cleaning, and inspection. Common issues such as bridging, open joints, voids, and HIP defects can be prevented or resolved by identifying and addressing their potential causes.
By understanding the factors that affect solder ball quality and following best practices for PCB soldering, manufacturers can produce reliable and high-performing electronic devices.
Frequently Asked Questions (FAQ)
1. What are the most common solder alloys used for making solder balls?
The most common solder alloys used for making solder balls are tin-lead (SnPb) and lead-free alloys such as tin-silver-copper (SAC). SnPb alloys have a lower melting point and better wetting properties, but are being phased out due to environmental and health concerns. SAC alloys have a higher melting point and better mechanical and thermal properties, but can be more difficult to work with.
2. What is the difference between gas atomization and plasma atomization for making solder balls?
Gas atomization and plasma atomization are two methods for producing solder balls by breaking up molten solder into small droplets. Gas atomization uses a high-pressure gas stream to break up the molten solder, while plasma atomization uses a plasma torch. Plasma atomization can produce smaller and more uniform droplets than gas atomization, but is more expensive and complex.
3. What is the purpose of flux in PCB soldering?
Flux is a chemical compound used in PCB soldering to remove oxides and other contaminants from the surface of the PCB and component leads, and to improve the wetting and flow properties of the solder. Flux helps to ensure a strong and reliable solder joint by promoting the formation of a metallurgical bond between the solder and the surfaces being joined.
4. What are some common defects that can occur in solder joints made with solder balls?
Some common defects that can occur in solder joints made with solder balls include bridging (short circuits between adjacent pads), open joints (no electrical connection), voids (air pockets or holes inside the joint), and head-in-pillow (HIP) defects (incomplete collapse of the solder ball during reflow). These defects can be caused by various factors such as improper solder ball size or placement, insufficient flux or solder paste, oxidation or contamination on the surfaces being joined, and improper reflow profiling.
5. How can the quality of solder balls be tested and verified?
The quality of solder balls can be tested and verified using various methods, including visual inspection (for defects such as voids or cracks), X-ray inspection (for internal defects), composition analysis (using techniques such as X-ray fluorescence or inductively coupled plasma to verify the alloy composition), and mechanical testing (for properties such as hardness and tensile strength). Quality control measures should be implemented throughout the manufacturing process to ensure that the solder balls meet the required specifications for size, shape, composition, and performance.
0 Comments