What is PCB etching?
PCB etching is the process of selectively removing copper from a printed circuit board (PCB) to create the desired circuit pattern. It involves applying a resist layer to protect the areas of copper that will form the circuit traces, then chemically dissolving away the unprotected copper.
PCB etching is a key step in the PCB fabrication process. It allows complex circuits to be precisely transferred from a design to a functional PCB. There are various methods and chemical etchants that can be used for PCB etching.
PCB Etching Methods
There are two main methods used for etching PCBs:
Subtractive Etching
In subtractive etching, a copper-clad board with a photoresist layer is selectively exposed to light through a photomask or printed transparency. The photoresist hardens where exposed. The unexposed photoresist is then removed, leaving bare copper that is etched away in a chemical bath. This is the most common PCB etching method.
Additive Etching
In additive etching, a bare substrate board is covered with a photoresist. The photoresist is selectively exposed and developed to create a negative image of the circuit pattern. Copper is then electroplated into the channels formed in the photoresist. Finally, the resist is stripped away, leaving only the copper traces. This method is used less frequently.
PCB Etching Process Steps
Here is an overview of the basic steps involved in etching a PCB using the subtractive method:
- Design: Create your PCB artwork and generate photomask or printout
- Printing: Print the artwork onto a transparency or purchase a photomask
- Presensitized Boards: Purchase or prepare a copper clad board with presensitized positive photoresist
- Exposing: Expose the photoresist by placing the photomask or transparency on top and shining UV light
- Developing: Submerge the board in developer solution to remove the unexposed photoresist
- Etching: Immerse the board in etchant solution to chemically remove the unprotected copper
- Stripping: Remove the remaining hardened photoresist using a stripping solution
- Tinning (optional): Electroplate a thin layer of tin onto the copper traces to prevent oxidation
- Drilling: Drill any required holes for through-hole components and vias
- Finishing: Apply solder mask and silkscreen layers if desired
The exact process can vary depending on the fabrication method, photoresist type, and etchant chemistry used. But these are the core steps for typical PCB etching.
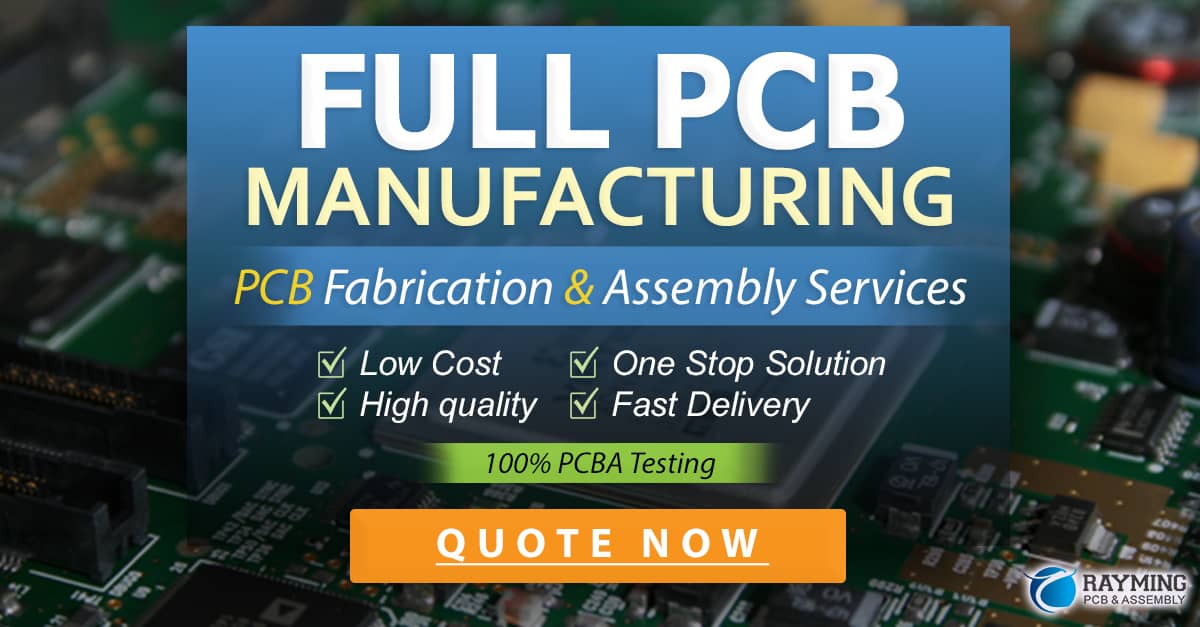
PCB Etching Chemicals
Various chemicals can be used as etchants to dissolve the unprotected copper on a PCB. Each has advantages and disadvantages in terms of etching speed, surface finish, safety, and disposal. Some common PCB etchants include:
Etchant | Composition | Pros | Cons |
---|---|---|---|
Ferric Chloride (FeCl3) | Ferric chloride pellets or solution | Very effective, moderate etch rate | Corrosive, stains surfaces, difficult to dispose |
Ammonium Persulfate (NH4)2S2O8 | Ammonium persulfate crystals mixed with water | Fast etch rate, clean surface finish | Dangerous if inhaled, limited shelf life once mixed |
Copper Chloride (CuCl2) | Copper chloride solution, hydrochloric acid, hydrogen peroxide | Inexpensive, etches cleanly | Slow etch rate, not very aggressive |
Sodium Persulfate (Na2S2O8) | Sodium persulfate mixed with water | Fast acting, clean | High pH, limited shelf life |
Ferric chloride is the most widely used due to its low cost and high effectiveness. But ammonium and sodium persulfate are gaining popularity as cleaner, less toxic alternatives. Proper safety precautions must always be followed when handling these harsh chemicals.
Video: PCB Etching Process Demonstration
To help visualize the PCB etching process, here is a video demonstrating the basic steps using the toner transfer method with ferric chloride etchant:
[Embed YouTube video showing PCB etching process]
The key steps shown in the video are:
- Print inverted PCB artwork onto glossy laser printer paper
- Clean the copper clad board and carefully place the laser print on top
- Use a clothes iron to transfer the toner to the copper, forming an etch resist
- Allow the board to cool then soak in water to remove the paper backing
- Immerse the board in a heated ferric chloride bath to etch away the exposed copper
- Agitate regularly and etch until all unprotected copper is removed, about 15-30 minutes
- Rinse the board thoroughly with water then remove the toner with acetone
As you can see, with simple tools and some patience, functional PCBs can be made at home using the toner transfer PCB etching method.
FAQ
What is the best PCB etchant for beginners?
For those new to etching PCBs, ferric chloride is a good etchant to start with. It is inexpensive, effective, and easy to find. However, it can be messy and difficult to dispose of. A somewhat safer alternative is ammonium persulfate.
How long does it take to etch a PCB?
Etch time depends on the type and temperature of etchant used, and the amount of copper to remove. In general, it takes about 15-30 minutes to etch an average PCB. Heating the etchant and agitating the board speeds up etching. The board is done etching when all the unprotected copper is removed.
What are some common problems encountered when etching PCBs?
Some issues that can occur when etching PCBs include:
– Over-etching or under-etching due to incorrect etch time or etchant strength
– Etchant undercutting the resist, causing traces to be etched too narrow
– Pinholes or imperfections in the etch resist leading to unintended etching
– Uneven etching from inadequate agitation or uneven etchant distribution
– Accidents or messes from mishandling corrosive etchant chemicals
Can I reuse PCB etchant?
Etchants become exhausted after dissolving a certain amount of copper, slowing down and producing rough etching. Ferric chloride is typically one-use, while acid-based etchants can be regenerated a few times by adding oxygen. For best results, it’s recommended to use fresh etchant for each PCB.
What safety precautions are needed when etching PCBs?
Etching PCBs involves hazardous chemicals that require safety measures:
– Always wear gloves, goggles, and protective clothing when handling etchants
– Work in a well-ventilated area or use a fume hood to avoid inhaling fumes
– Avoid skin contact with etchants, developers, and strippers; rinse thoroughly if exposed
– Never pour etchants down the drain; collect and dispose of properly as hazardous waste
– Keep chemicals away from food and drinks, and inaccessible to children and pets
– Have neutralizing agents like sodium bicarbonate on hand in case of chemical spills
By following the proper precautions and disposal procedures, PCBs can be etched safely.
0 Comments