Understanding Your Project Requirements
Before you begin your search for an Electronic Assembly service provider, it is essential to have a clear understanding of your project requirements. This includes:
Product Specifications
- What is the purpose of your electronic device?
- What are the dimensions and weight of the product?
- What are the power requirements?
- What are the environmental conditions the device will be subjected to?
Component Selection
- What types of electronic components will be used in your product?
- Are there any special requirements for component sourcing?
- Do you need assistance with component selection and procurement?
Production Volume
- What is the expected production volume for your project?
- Is it a one-time prototype or a large-scale production run?
- What are your forecasted sales volumes?
Timeline and Budget
- When do you need the assembled products delivered?
- What is your budget for the electronic assembly service?
- Are there any specific cost constraints you need to consider?
By clearly defining your project requirements, you can effectively communicate your needs to potential electronic assembly service providers and ensure that they can meet your expectations.
Factors to Consider When Choosing an Electronic Assembly Service
Technical Capabilities
One of the primary factors to consider when choosing an electronic assembly service is their technical capabilities. You want to ensure that the provider has the necessary equipment, expertise, and experience to handle your specific project requirements. Some key technical capabilities to look for include:
Surface Mount Technology (SMT) Assembly
SMT assembly is the process of mounting electronic components directly onto the surface of a PCB. This technology allows for smaller, more compact designs and is widely used in modern electronic devices. Ensure that the electronic assembly service provider has experience with SMT assembly and the necessary equipment, such as pick-and-place machines and reflow ovens.
Through-Hole Technology (THT) Assembly
THT assembly involves inserting electronic components through holes in the PCB and soldering them in place. While not as common as SMT assembly, THT is still used for certain types of components and applications. If your project requires THT assembly, make sure the provider has the capability to handle it.
Mixed Technology Assembly
Some electronic devices require a combination of SMT and THT assembly. If your project falls into this category, choose an electronic assembly service provider that has experience with mixed technology assembly and can efficiently handle both types of components.
Automated Optical Inspection (AOI)
AOI is a quality control process that uses cameras and image processing software to inspect assembled PCBs for defects such as missing components, incorrect placement, or soldering issues. An electronic assembly service provider with AOI capabilities can help ensure the quality and reliability of your products.
Quality Management Systems
Another critical factor to consider when choosing an electronic assembly service is their quality management systems. You want to work with a provider that has robust quality control processes in place to ensure that your products meet the required specifications and standards. Look for providers with the following quality management certifications:
ISO 9001
ISO 9001 is an international standard that sets out the requirements for a quality management system. It focuses on customer satisfaction, continuous improvement, and the effective management of processes. An electronic assembly service provider with ISO 9001 certification demonstrates a commitment to quality and reliability.
IPC Standards
IPC (Association Connecting Electronics Industries) is a global trade association that develops standards for the electronic manufacturing industry. IPC standards cover various aspects of PCB design, assembly, and quality control. Choose an electronic assembly service provider that adheres to relevant IPC standards, such as:
- IPC-A-610: Acceptability of Electronic Assemblies
- IPC-J-STD-001: Requirements for Soldered Electrical and Electronic Assemblies
- IPC-A-600: Acceptability of Printed Boards
Compliance with these standards ensures that your products are manufactured according to industry-recognized best practices.
Supply Chain Management
Effective supply chain management is crucial for ensuring the timely delivery of your products and managing costs. When evaluating electronic assembly service providers, consider their supply chain capabilities:
Component Sourcing
Does the provider have established relationships with component suppliers? Can they source components at competitive prices and ensure a stable supply? A provider with strong component sourcing capabilities can help you avoid delays and manage costs effectively.
Inventory Management
How does the provider manage inventory? Do they offer consignment inventory or just-in-time (JIT) delivery options? Efficient inventory management can help reduce storage costs and minimize the risk of obsolete components.
Lead Time Management
Can the provider meet your required lead times? Do they have a track record of delivering products on schedule? Choose a provider that can demonstrate their ability to manage lead times effectively and has a history of meeting delivery commitments.
Cost and Value
Cost is always a consideration when choosing an electronic assembly service provider, but it should not be the sole deciding factor. Instead, focus on finding a provider that offers the best value for your money. Consider the following aspects:
Pricing Structure
How does the provider structure their pricing? Do they offer transparent and detailed quotes? Are there any hidden costs or fees? Make sure you understand the pricing structure and what is included in the quoted price.
Value-Added Services
Does the provider offer any value-added services, such as design support, testing, or packaging? These additional services can help streamline your project and reduce overall costs.
Cost Reduction Opportunities
Is the provider proactive in identifying cost reduction opportunities? Can they suggest alternative components or design modifications that can help reduce costs without compromising quality?
Communication and Customer Support
Effective communication and customer support are essential for a successful electronic assembly project. Consider the following factors when evaluating providers:
Responsiveness
How quickly does the provider respond to your inquiries and requests? Do they have a dedicated point of contact for your project? Choose a provider that is responsive and easy to communicate with.
Technical Support
Does the provider offer technical support throughout the project? Can they assist with troubleshooting and problem-solving if issues arise? A provider with strong technical support can help ensure the success of your project.
Project Management
How does the provider manage projects? Do they have a structured project management process in place? Look for a provider that assigns a dedicated project manager to oversee your project and keep you informed of progress and any potential issues.
Questions to Ask Electronic Assembly Service Providers
When evaluating potential electronic assembly service providers, it is essential to ask the right questions to gather the information you need to make an informed decision. Here are some key questions to consider:
- What experience do you have with projects similar to mine?
- What certifications and quality management systems do you have in place?
- Can you provide references from previous clients?
- How do you handle component sourcing and inventory management?
- What is your pricing structure, and are there any additional fees or costs?
- What is your typical lead time for a project like mine?
- How do you ensure the quality and reliability of the assembled products?
- What value-added services do you offer, such as design support or testing?
- How do you handle project management and communication with clients?
- What is your process for handling issues or defects that may arise?
By asking these questions and carefully evaluating the responses, you can gain valuable insights into the capabilities, experience, and customer service of potential electronic assembly service providers.
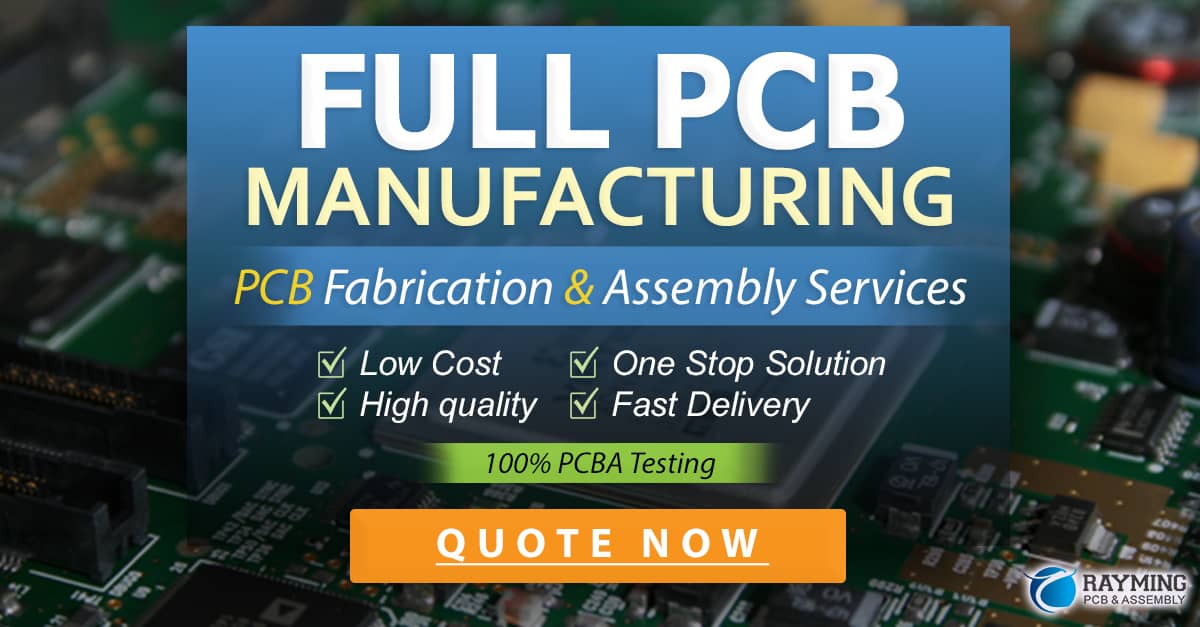
Making Your Final Decision
After gathering information and evaluating potential electronic assembly service providers, it’s time to make your final decision. Consider the following factors when making your choice:
Alignment with Your Project Requirements
Does the provider have the technical capabilities and experience to meet your specific project requirements? Can they handle your production volume and timeline?
Quality and Reliability
Does the provider have robust quality management systems in place? Do they have a track record of delivering high-quality products?
Cost and Value
Does the provider offer competitive pricing and value for your money? Have they identified any cost reduction opportunities?
Communication and Customer Service
Is the provider responsive and easy to communicate with? Do they have a structured project management process in place?
Gut Feeling
Finally, trust your gut feeling. If you have any doubts or concerns about a provider, it may be best to explore other options. Choose a provider that you feel confident in and comfortable working with.
Conclusion
Choosing the right electronic assembly service provider is a critical decision that can impact the success of your project. By understanding your project requirements, evaluating key factors such as technical capabilities, quality management systems, supply chain management, cost, and customer service, and asking the right questions, you can make an informed decision and select a provider that meets your needs. Remember to prioritize quality, reliability, and value over solely focusing on cost. With the right electronic assembly service provider as your partner, you can bring your electronic products to market with confidence.
Frequently Asked Questions (FAQ)
-
What is electronic assembly?
Electronic assembly is the process of assembling various electronic components onto a printed circuit board (PCB) to create a functional electronic device. -
What are the different types of electronic assembly technologies?
The two main types of electronic assembly technologies are Surface Mount Technology (SMT) and Through-Hole Technology (THT). SMT involves mounting components directly onto the surface of the PCB, while THT involves inserting components through holes in the PCB and soldering them in place. -
What certifications should I look for in an electronic assembly service provider?
Look for providers with quality management certifications such as ISO 9001 and adherence to relevant IPC standards, such as IPC-A-610, IPC-J-STD-001, and IPC-A-600. -
How important is supply chain management when choosing an electronic assembly service provider?
Effective supply chain management is crucial for ensuring the timely delivery of your products and managing costs. Choose a provider with strong component sourcing capabilities, efficient inventory management, and the ability to meet your required lead times. -
What should I consider when evaluating the cost of electronic assembly services?
While cost is an important factor, it should not be the sole deciding factor. Focus on finding a provider that offers the best value for your money, considering factors such as pricing structure, value-added services, and cost reduction opportunities.
0 Comments