Introduction to PCB Fabrication and Its Importance in RF and Microwave Applications
Printed Circuit Board (PCB) fabrication is a crucial process in the electronics industry, especially when it comes to RF (Radio Frequency) and microwave applications. PCBs are the backbone of modern electronic devices, providing a platform for components to be mounted and interconnected. In the realm of RF and microwave technology, PCB fabrication plays a vital role in ensuring optimal performance, reliability, and manufacturability of the final product.
The Challenges of RF and Microwave PCB Fabrication
RF and microwave PCBs pose unique challenges compared to their low-frequency counterparts. These challenges arise from the high-frequency nature of the signals involved, which can lead to various issues such as signal integrity problems, electromagnetic interference (EMI), and power loss. Some of the key challenges in RF and microwave PCB fabrication include:
-
Material selection: Choosing the right substrate material is crucial for RF and microwave PCBs. The material must have low dielectric loss, high thermal stability, and consistent electrical properties over the desired frequency range.
-
Impedance control: Maintaining precise impedance control is essential to minimize signal reflections and ensure proper energy transfer between components.
-
Feature size and spacing: RF and microwave PCBs often require fine feature sizes and tight spacing between traces to minimize parasitic effects and maintain signal integrity.
-
Shielding and grounding: Proper shielding and grounding techniques are necessary to minimize EMI and ensure stable performance.
Advancements in PCB Fabrication Technology for RF and Microwave Applications
To address the challenges of RF and microwave PCB fabrication, various technological advancements have been made in recent years. These advancements aim to improve the performance, reliability, and manufacturability of RF and microwave PCBs.
High-Frequency Laminates and Substrates
One of the key advancements in PCB fabrication technology for RF and microwave applications is the development of high-frequency laminates and substrates. These materials are specifically designed to provide low dielectric loss, high thermal stability, and consistent electrical properties over a wide frequency range. Some examples of high-frequency laminates and substrates include:
-
Rogers RO4000 series: A hydrocarbon ceramic laminate with low dielectric loss and high thermal stability, suitable for applications up to 40 GHz.
-
Isola I-Tera MT: A low-loss, high-performance laminate designed for high-speed digital and RF applications up to 100 GHz.
-
Taconic RF-35: A low-loss, high-performance PTFE-based laminate for RF and microwave applications up to 40 GHz.
Advanced Fabrication Techniques
In addition to high-frequency laminates and substrates, advanced fabrication techniques have been developed to improve the precision and reliability of RF and microwave PCBs. These techniques include:
-
High-Density Interconnect (HDI): HDI technology enables the fabrication of PCBs with fine feature sizes and tight spacing between traces, which is essential for RF and microwave applications.
-
Embedded Passive Components: By embedding passive components such as resistors and capacitors within the PCB substrate, designers can reduce the size and improve the performance of RF and microwave circuits.
-
Microvia Technology: Microvias are small, laser-drilled holes that provide interconnections between layers in a PCB. This technology enables the fabrication of high-density, multilayer PCBs with improved signal integrity and reduced parasitic effects.
Simulation and Modeling Tools
Simulation and modeling tools have become increasingly important in the design and fabrication of RF and microwave PCBs. These tools allow designers to analyze and optimize the performance of their circuits before committing to fabrication, reducing the risk of costly redesigns and improving time-to-market. Some popular simulation and modeling tools for RF and microwave PCBs include:
-
Ansys HFSS: A 3D electromagnetic simulation tool for designing and analyzing high-frequency electronic products.
-
Keysight ADS: A comprehensive electronic design automation software for RF, microwave, and high-speed digital applications.
-
Cadence AWR Design Environment: An integrated suite of tools for designing and simulating RF and microwave circuits.
Best Practices for RF and Microwave PCB Fabrication
To ensure the optimal performance and reliability of RF and microwave PCBs, designers and fabricators should follow best practices throughout the design and manufacturing process.
Design Considerations
-
Material Selection: Choose the appropriate high-frequency laminate or substrate based on the application’s requirements, such as frequency range, dielectric loss, and thermal stability.
-
Impedance Control: Design the PCB with consistent impedance control by carefully selecting trace widths, spacing, and layer stackup.
-
Shielding and Grounding: Incorporate proper shielding and grounding techniques to minimize EMI and ensure stable performance.
-
Component Placement: Optimize component placement to minimize signal path lengths and reduce parasitic effects.
Fabrication Guidelines
-
Fabrication Process: Select the appropriate fabrication process based on the required feature sizes, layer count, and material compatibility.
-
Quality Control: Implement strict quality control measures throughout the fabrication process to ensure consistent and reliable results.
-
Testing and Inspection: Perform thorough testing and inspection of the fabricated PCBs to identify and address any issues before final assembly.
Collaboration and Communication
Effective collaboration and communication between designers, fabricators, and assembly partners are essential for the successful production of RF and microwave PCBs. By working closely together and sharing knowledge and expertise, all parties can contribute to the optimization of the design and fabrication process, ultimately leading to higher-quality products and faster time-to-market.
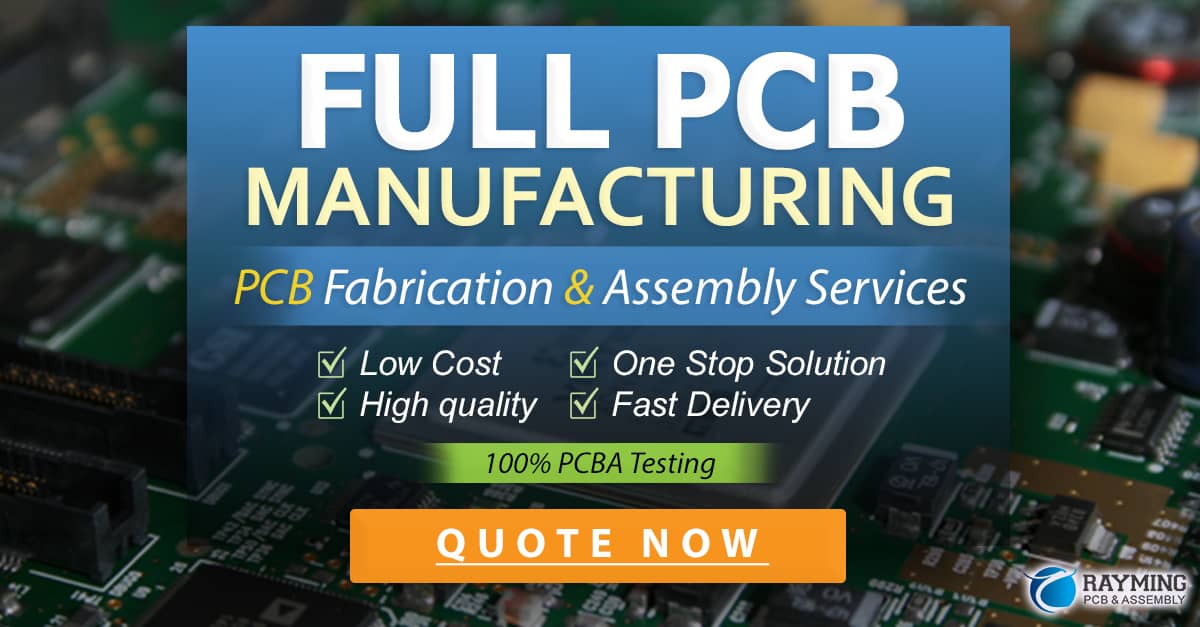
Future Trends in RF and Microwave PCB Fabrication
As the demand for high-performance RF and microwave electronics continues to grow, PCB fabrication technology will need to evolve to keep pace with the industry’s requirements. Some of the future trends in RF and microwave PCB fabrication include:
-
Advanced Materials: The development of new, high-performance materials with improved electrical and thermal properties will enable the fabrication of PCBs for even higher frequency applications.
-
3D Printing: The adoption of 3D printing technology for PCB fabrication could enable the creation of complex, three-dimensional structures with integrated components, leading to more compact and efficient designs.
-
Artificial Intelligence and Machine Learning: The integration of AI and machine learning algorithms into the design and fabrication process could help optimize PCB layouts, predict potential issues, and improve overall quality and reliability.
Frequently Asked Questions (FAQ)
- What is the importance of PCB fabrication in RF and microwave applications?
-
PCB fabrication is crucial for RF and microwave applications because it provides the foundation for mounting and interconnecting components in a way that ensures optimal performance, reliability, and manufacturability of the final product.
-
What are some of the key challenges in RF and microwave PCB fabrication?
-
Some of the key challenges include material selection, impedance control, feature size and spacing, and shielding and grounding. These challenges arise from the high-frequency nature of the signals involved in RF and microwave applications.
-
What are high-frequency laminates and substrates, and why are they important for RF and microwave PCBs?
-
High-frequency laminates and substrates are materials specifically designed for use in RF and microwave PCBs. They provide low dielectric loss, high thermal stability, and consistent electrical properties over a wide frequency range, which is essential for optimal performance in high-frequency applications.
-
What are some advanced fabrication techniques used in RF and microwave PCB manufacturing?
-
Advanced fabrication techniques for RF and microwave PCBs include High-Density Interconnect (HDI), embedded passive components, and microvia technology. These techniques enable the creation of PCBs with fine feature sizes, tight spacing, and improved signal integrity.
-
How can simulation and modeling tools help in the design and fabrication of RF and microwave PCBs?
- Simulation and modeling tools allow designers to analyze and optimize the performance of their circuits before committing to fabrication. This reduces the risk of costly redesigns, improves time-to-market, and ultimately leads to higher-quality products.
Conclusion
PCB fabrication plays a critical role in the performance and reliability of RF and microwave electronics. As technology continues to advance, so too must the approaches and techniques used in PCB fabrication to meet the evolving needs of the industry. By leveraging high-frequency laminates and substrates, advanced fabrication techniques, and simulation and modeling tools, designers and fabricators can create PCBs that deliver optimal performance in even the most demanding RF and microwave applications. As we look to the future, trends such as advanced materials, 3D printing, and AI integration promise to further revolutionize the field of PCB fabrication, enabling the creation of even more innovative and efficient electronic devices.
0 Comments