Introduction to PCB laser drilling
PCB (Printed Circuit Board) laser drilling is a precise and efficient method for creating small, high-quality holes in PCBs. This advanced technology has revolutionized the PCB manufacturing process, enabling the production of more complex and densely packed circuit boards. In this article, we will dive into the details of how PCB laser drilling works and explore the numerous advantages it offers over traditional drilling methods.
What is PCB Laser Drilling?
PCB laser drilling is a non-contact process that uses a focused laser beam to create holes in printed circuit boards. The laser beam vaporizes the material, leaving behind a clean and precise hole without causing any mechanical stress or damage to the surrounding area. This technology is particularly useful for creating micro-vias, which are tiny holes that connect different layers of a multi-layer PCB.
Types of Lasers Used in PCB Drilling
There are two main types of lasers used in PCB drilling:
- CO2 Lasers: These lasers have a wavelength of 9.3-10.6 μm and are suitable for drilling larger holes (>200 μm) in PCBs.
- UV Lasers: Ultraviolet lasers, such as Nd:YAG (neodymium-doped yttrium aluminum garnet) lasers, have a shorter wavelength (355 nm) and are used for drilling smaller holes (<200 μm) with higher precision.
How PCB Laser Drilling Works
The PCB laser drilling process involves several steps:
- PCB Preparation: The PCB is cleaned and placed on a high-precision X-Y motion table.
- Laser Positioning: The laser beam is focused on the desired location using a high-quality lens system.
- Laser Pulsing: The laser emits short, high-energy pulses that vaporize the PCB material, creating a hole.
- Debris Removal: A vacuum system removes the vaporized material and any debris from the hole.
- Quality Control: The drilled holes are inspected for accuracy, size, and quality using automated vision systems.
Laser Drilling Parameters
Several parameters influence the quality and efficiency of PCB laser drilling:
Parameter | Description |
---|---|
Laser Power | The energy output of the laser, which determines the drilling speed and hole size. |
Pulse Duration | The length of each laser pulse, which affects the amount of material removed per pulse. |
Pulse Frequency | The number of laser pulses per second, which influences the drilling speed. |
Focal Point | The distance between the laser lens and the PCB surface, which determines the hole size and shape. |
Assist Gas | A gas, such as oxygen or nitrogen, used to improve drilling efficiency and remove debris. |
Advantages of PCB Laser Drilling
PCB laser drilling offers numerous advantages over traditional mechanical drilling methods:
- High Precision: Laser drilling can create holes as small as 25 μm with tight tolerances, enabling the production of high-density PCBs.
- Increased Flexibility: Laser drilling allows for the creation of non-standard hole shapes and sizes, such as tapered or stepped holes.
- Reduced Damage: As a non-contact process, laser drilling minimizes mechanical stress and damage to the PCB, improving overall board quality.
- Faster Production: Laser drilling is a high-speed process, capable of drilling thousands of holes per second, significantly reducing production time.
- Cost-Effective: The increased efficiency and precision of laser drilling lead to lower production costs, especially for high-volume manufacturing.
Applications of PCB Laser Drilling
PCB laser drilling is widely used in various industries, including:
- Consumer Electronics: Smartphones, tablets, and wearable devices require high-density PCBs with micro-vias, which can be efficiently produced using laser drilling.
- Automotive Industry: Advanced driver assistance systems (ADAS) and in-vehicle infotainment systems rely on complex PCBs that benefit from laser drilling technology.
- Aerospace and Defense: Military and aerospace applications demand reliable, high-performance PCBs that can withstand harsh environments. Laser drilling enables the creation of robust and compact PCBs for these critical applications.
- Medical Devices: Laser-drilled PCBs are essential for medical devices, such as implantable devices and diagnostic equipment, which require miniaturization and high reliability.
- Telecommunications: 5G networks and high-speed data transmission systems require advanced PCBs with micro-vias, which can be produced efficiently using laser drilling.
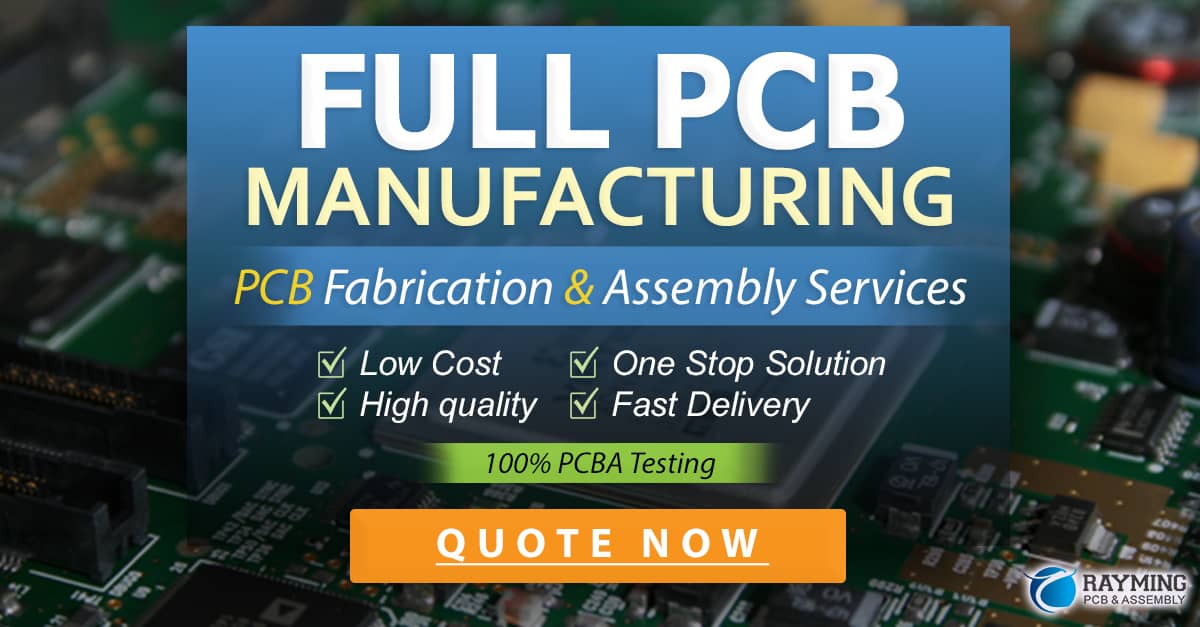
Challenges and Future Developments
While PCB laser drilling offers numerous benefits, there are still some challenges to overcome:
- Material Compatibility: Some PCB materials, such as copper-clad laminates with high glass transition temperatures, can be difficult to laser drill efficiently.
- Thermal Damage: Laser drilling can cause localized heating, which may lead to thermal damage in sensitive PCB materials.
- Hole Quality: Ensuring consistent hole quality, especially for high aspect ratio holes, can be challenging.
Researchers and industry experts are continuously working on improving PCB laser drilling technology to address these challenges. Some of the future developments in this field include:
- Advanced Laser Sources: The development of more efficient and precise laser sources, such as ultrashort pulse lasers, can improve drilling quality and reduce thermal damage.
- Intelligent Process Control: The integration of machine learning and artificial intelligence algorithms can optimize laser drilling parameters in real-time, enhancing process efficiency and hole quality.
- Hybrid Drilling Techniques: Combining laser drilling with other methods, such as plasma or chemical etching, can improve the drilling of challenging materials and create more complex hole geometries.
Frequently Asked Questions (FAQ)
- What is the smallest hole size that can be achieved with PCB laser drilling?
-
PCB laser drilling can create holes as small as 25 μm in diameter, depending on the laser type and material properties.
-
How does laser drilling compare to mechanical drilling in terms of speed?
-
Laser drilling is much faster than mechanical drilling, capable of creating thousands of holes per second, while mechanical drilling is limited to a few hundred holes per minute.
-
Can laser drilling be used on all types of PCB materials?
-
While laser drilling is compatible with most common PCB materials, some materials with high glass transition temperatures or unique properties may be more challenging to drill efficiently.
-
Is laser drilling more expensive than mechanical drilling?
-
Initially, laser drilling systems may have a higher upfront cost than mechanical drilling machines. However, the increased efficiency, precision, and reduced production time of laser drilling often lead to lower overall costs, especially for high-volume manufacturing.
-
What is the role of assist gas in PCB laser drilling?
- Assist gas, such as oxygen or nitrogen, is used to improve the efficiency of laser drilling by removing vaporized material and debris from the hole. It also helps to control the thermal effects and improve hole quality.
Conclusion
PCB laser drilling is a game-changer in the world of PCB manufacturing, offering unparalleled precision, flexibility, and efficiency. By understanding how this technology works and its numerous advantages, PCB designers and manufacturers can leverage laser drilling to create advanced, high-density PCBs for a wide range of applications. As research and development continue, we can expect to see even more innovative solutions and improvements in PCB laser drilling, further pushing the boundaries of what is possible in the world of electronic manufacturing.
0 Comments