What is PCB Inspection?
PCB inspection is the process of examining printed circuit boards (PCBs) to ensure they meet the required quality standards. This process is crucial in the PCB assembly process as it helps identify defects and issues that could lead to malfunctions or failures in the final product. PCB inspection can be performed at various stages of the assembly process, from the bare board stage to the final assembled PCB.
Types of PCB Inspection
There are several types of PCB inspection methods used in the industry, including:
-
Visual Inspection: This is the most basic form of PCB inspection, where the board is visually examined for defects such as scratches, cracks, or incorrect component placement.
-
Automated Optical Inspection (AOI): AOI uses cameras and image processing software to automatically inspect PCBs for defects. This method is faster and more accurate than visual inspection.
-
X-Ray Inspection: X-ray inspection is used to examine the internal structure of the PCB, including solder joints and component placement. This method is particularly useful for inspecting high-density boards or boards with hidden components.
-
In-Circuit Testing (ICT): ICT is used to test the functionality of individual components on the PCB. This method involves using a bed of nails fixture to make contact with specific points on the board and test for continuity, resistance, and other parameters.
The Importance of PCB Inspection
PCB inspection plays a crucial role in ensuring the quality and reliability of the final product. Here are some reasons why PCB inspection is important:
1. Identifying Defects Early
PCB inspection helps identify defects early in the assembly process, which can save time and money in the long run. Catching defects early means they can be corrected before the board moves on to the next stage of assembly, reducing the risk of costly rework or scrap.
2. Ensuring Functionality
PCB inspection helps ensure that the board is functioning as intended. By testing individual components and checking for proper connections, PCB inspection can identify issues that could lead to malfunctions or failures in the final product.
3. Meeting Quality Standards
PCB inspection helps ensure that the board meets the required quality standards. This is particularly important in industries such as aerospace, medical, and automotive, where high reliability and safety are critical.
4. Improving Yield
PCB inspection can help improve the yield of the assembly process by identifying and correcting defects early on. This can lead to higher quality products and reduced costs associated with rework and scrap.
The PCB Assembly Process
The PCB assembly process involves several stages, each of which may require PCB inspection. Here is a brief overview of the PCB assembly process:
-
Solder Paste Printing: Solder paste is applied to the PCB using a stencil or screen printing process.
-
Component Placement: Components are placed on the PCB using pick-and-place machines or by hand.
-
Reflow Soldering: The PCB is heated in a reflow oven to melt the solder paste and form a permanent connection between the components and the board.
-
Wave Soldering: Through-hole components are soldered to the board using a wave soldering machine.
-
Final Inspection: The assembled PCB undergoes a final inspection to ensure it meets the required quality standards.
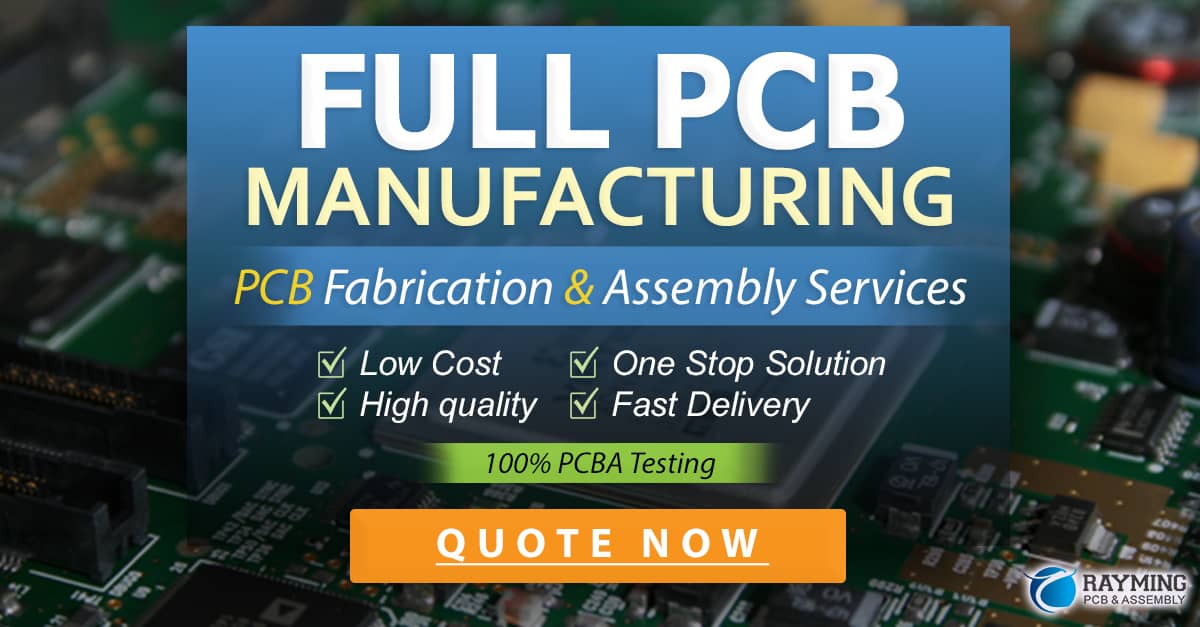
PCB Inspection at Each Stage of Assembly
PCB inspection can be performed at various stages of the assembly process, depending on the complexity of the board and the quality requirements. Here are some examples of PCB inspection at each stage of assembly:
Solder Paste Inspection
Solder paste inspection is performed after the solder paste printing stage to ensure that the correct amount of solder paste has been applied to the pads. This inspection can be performed using 2D or 3D solder paste inspection machines, which use cameras and laser sensors to measure the height, volume, and position of the solder paste deposits.
Inspection Method | Description |
---|---|
2D Solder Paste Inspection | Uses a camera to capture images of the solder paste deposits and analyze their shape and position. |
3D Solder Paste Inspection | Uses a laser sensor to measure the height and volume of the solder paste deposits. |
Component Placement Inspection
Component placement inspection is performed after the component placement stage to ensure that the components have been placed correctly on the board. This inspection can be performed using AOI machines or by visual inspection.
Inspection Method | Description |
---|---|
AOI | Uses cameras and image processing software to automatically inspect the board for component placement errors. |
Visual Inspection | A human operator visually inspects the board for component placement errors. |
Reflow Soldering Inspection
Reflow soldering inspection is performed after the reflow soldering stage to ensure that the solder joints have formed correctly and that there are no defects such as bridges, opens, or voids. This inspection can be performed using X-ray inspection machines or by visual inspection.
Inspection Method | Description |
---|---|
X-Ray Inspection | Uses X-rays to examine the internal structure of the solder joints and identify defects such as voids or bridges. |
Visual Inspection | A human operator visually inspects the solder joints for defects. |
Final Inspection
Final inspection is performed after the assembly process is complete to ensure that the board meets the required quality standards. This inspection can include functional testing, ICT, and visual inspection.
Inspection Method | Description |
---|---|
Functional Testing | Tests the board’s functionality by applying power and signals to the board and measuring its response. |
ICT | Uses a bed of nails fixture to test individual components and connections on the board. |
Visual Inspection | A human operator visually inspects the board for defects such as scratches, cracks, or incorrect labeling. |
Frequently Asked Questions (FAQ)
1. What is the difference between AOI and visual inspection?
AOI uses cameras and image processing software to automatically inspect PCBs for defects, while visual inspection is performed by a human operator. AOI is faster and more accurate than visual inspection, but visual inspection may still be necessary for certain types of defects or for low-volume production.
2. What is the purpose of X-ray inspection?
X-ray inspection is used to examine the internal structure of the PCB, including solder joints and component placement. This method is particularly useful for inspecting high-density boards or boards with hidden components that cannot be inspected visually or with AOI.
3. What is the difference between 2D and 3D solder paste inspection?
2D solder paste inspection uses a camera to capture images of the solder paste deposits and analyze their shape and position, while 3D solder paste inspection uses a laser sensor to measure the height and volume of the solder paste deposits. 3D inspection provides more accurate measurements of the solder paste volume, which is critical for ensuring reliable solder joints.
4. What is the purpose of ICT?
ICT is used to test the functionality of individual components on the PCB. This method involves using a bed of nails fixture to make contact with specific points on the board and test for continuity, resistance, and other parameters. ICT is useful for identifying defects that may not be visible during visual or AOI inspection.
5. How can PCB inspection improve the yield of the assembly process?
PCB inspection can help improve the yield of the assembly process by identifying and correcting defects early on. This can lead to higher quality products and reduced costs associated with rework and scrap. By catching defects early, PCB inspection can also help prevent issues from propagating to later stages of assembly, where they may be more difficult and expensive to correct.
Conclusion
PCB inspection plays a critical role in ensuring the quality and reliability of PCBs during the assembly process. By identifying defects early and ensuring that boards meet the required quality standards, PCB inspection can help reduce costs, improve yield, and ensure the functionality of the final product. There are several types of PCB inspection methods used in the industry, including visual inspection, AOI, X-ray inspection, and ICT, each with its own strengths and weaknesses. By selecting the appropriate inspection methods for each stage of assembly and implementing a comprehensive quality control program, manufacturers can ensure that their PCBs meet the highest standards of quality and reliability.
0 Comments