What is PCB inspection?
PCB (Printed Circuit Board) inspection is a crucial process in the manufacturing of electronic devices. It involves examining the PCB for any defects, errors, or inconsistencies that may affect its functionality and reliability. The purpose of PCB inspection is to ensure that the board meets the required quality standards and specifications before it is assembled into the final product.
Types of PCB Inspection
There are several types of PCB inspection methods, each with its own advantages and limitations. The most common types of PCB inspection are:
-
Visual Inspection: This is the most basic form of PCB inspection, where the board is visually examined for any obvious defects, such as scratches, cracks, or missing components.
-
Automated Optical Inspection (AOI): AOI uses cameras and image processing software to automatically detect defects on the PCB surface, such as Solder Bridges, missing components, or incorrect component placement.
-
X-Ray Inspection: This method uses X-rays to inspect the internal structure of the PCB, including the solder joints and vias, for any defects or voids.
-
In-Circuit Testing (ICT): ICT involves using a bed-of-nails fixture to make electrical contact with specific points on the PCB and test the functionality of individual components and circuits.
-
Functional Testing: This type of inspection tests the overall functionality of the PCB by simulating its intended operating conditions and verifying that it performs as expected.
Inspection Type | Advantages | Limitations |
---|---|---|
Visual Inspection | Low cost, simple to perform | Limited to surface defects, subjective |
AOI | Fast, consistent, high coverage | Limited to surface defects, high initial cost |
X-Ray Inspection | Can detect internal defects | Expensive, slower than AOI |
ICT | Can detect component and circuit faults | Requires custom fixtures, limited coverage |
Functional Testing | Tests overall functionality | Requires custom test setup, limited fault isolation |
PCB Inspection Process
The PCB inspection process typically involves the following steps:
-
Design Review: Before the PCB is manufactured, the design files are reviewed to ensure that they meet the required specifications and standards.
-
Incoming Inspection: When the PCBs are received from the manufacturer, they are inspected for any obvious defects or damage that may have occurred during shipping.
-
Pre-Assembly Inspection: Before the components are assembled onto the PCB, the board is inspected for any defects that may have been missed during the incoming inspection.
-
Post-Assembly Inspection: After the components are assembled onto the PCB, the board is inspected again to ensure that all components are correctly placed and soldered.
-
Final Inspection: Before the PCB is shipped to the customer, a final inspection is performed to ensure that it meets all the required quality standards and specifications.
Inspection Checklist
To ensure that the PCB inspection process is thorough and consistent, it is important to have a checklist of items to look for during each stage of the inspection. A typical PCB inspection checklist may include the following items:
- Correct PCB dimensions and thickness
- Proper alignment of layers and vias
- Presence of all required components
- Correct component placement and orientation
- Proper solder joint formation and fillets
- Absence of solder bridges, shorts, or opens
- Cleanliness of the PCB surface
- Proper marking and labeling of the PCB
Benefits of PCB Inspection
Implementing a robust PCB inspection process offers several benefits, including:
-
Improved Quality: By identifying and correcting defects early in the manufacturing process, PCB inspection helps to improve the overall quality of the final product.
-
Reduced Costs: Catching defects early reduces the cost of rework and scrap, as well as the potential for warranty claims and returns.
-
Increased Reliability: By ensuring that the PCB meets all the required quality standards, inspection helps to increase the reliability and longevity of the final product.
-
Faster Time-to-Market: A streamlined inspection process can help to reduce the overall manufacturing time and get the product to market faster.
-
Enhanced Customer Satisfaction: Delivering high-quality, reliable products helps to enhance customer satisfaction and loyalty.
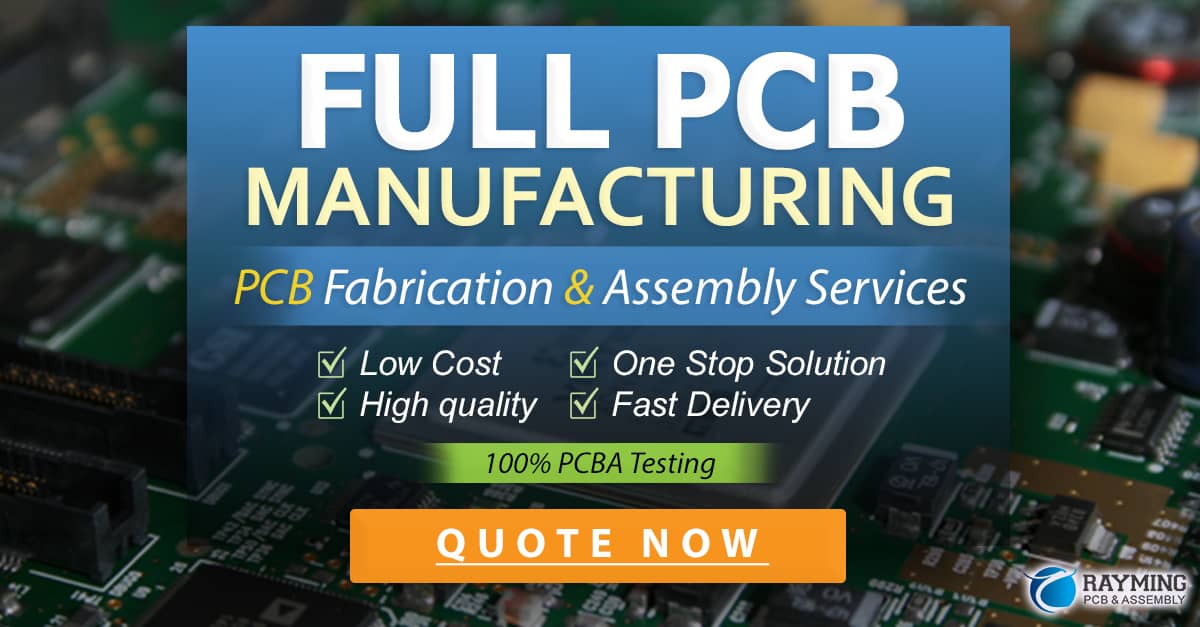
Best Practices for PCB Inspection
To ensure the effectiveness of the PCB inspection process, it is important to follow some best practices, such as:
-
Establish Clear Specifications: Before beginning the inspection process, ensure that the PCB specifications and requirements are clearly defined and documented.
-
Use Appropriate Inspection Methods: Select the appropriate inspection methods based on the complexity of the PCB, the required level of quality, and the available resources.
-
Implement Statistical Process Control: Use statistical process control methods to monitor the inspection process and identify any trends or issues that may require corrective action.
-
Train and Certify Inspectors: Ensure that the inspectors are properly trained and certified to perform the required inspection tasks.
-
Document and Analyze Results: Document the results of each inspection and analyze the data to identify any areas for improvement or corrective action.
Frequently Asked Questions (FAQ)
-
What is the difference between AOI and X-ray inspection?
AOI is used to inspect the surface of the PCB for defects, while X-ray inspection is used to inspect the internal structure of the PCB, including solder joints and vias. -
How often should PCB inspection be performed?
PCB inspection should be performed at various stages throughout the manufacturing process, including incoming inspection, pre-assembly inspection, post-assembly inspection, and final inspection. -
What are some common defects that can be detected during PCB inspection?
Common defects that can be detected during PCB inspection include missing or incorrect components, solder bridges or shorts, poor solder joint formation, and contamination or damage to the PCB surface. -
Can PCB inspection be automated?
Yes, some PCB inspection methods, such as AOI and X-ray inspection, can be automated using specialized equipment and software. -
What are the benefits of implementing a robust PCB inspection process?
Implementing a robust PCB inspection process can help to improve the overall quality and reliability of the final product, reduce costs associated with rework and scrap, and enhance customer satisfaction and loyalty.
Conclusion
PCB inspection is a critical process in the manufacturing of electronic devices, ensuring that the PCBs meet the required quality standards and specifications. By implementing a thorough and consistent inspection process, manufacturers can improve the overall quality and reliability of their products, reduce costs associated with rework and scrap, and enhance customer satisfaction and loyalty. To ensure the effectiveness of the PCB inspection process, it is important to establish clear specifications, use appropriate inspection methods, implement statistical process control, train and certify inspectors, and document and analyze the results. By following these best practices, manufacturers can deliver high-quality, reliable products to their customers and maintain a competitive edge in the market.
0 Comments