Introduction to Polyimide PCBs
Polyimide PCBs, also known as PI PCBs, are printed circuit boards that use polyimide as the base material instead of the more commonly used FR-4 (Flame Retardant-4). Polyimide is a high-performance polymer that offers several unique properties, making it an ideal choice for demanding industrial applications. In this article, we will explore the distinctive features of Polyimide PCBs and how they benefit various industrial sectors.
What is Polyimide?
Polyimide is a synthetic polymer known for its exceptional thermal, mechanical, and electrical properties. It belongs to a class of plastics called imides, characterized by their high heat resistance and excellent dimensional stability. Polyimide is produced by the condensation reaction between a dianhydride and a diamine, resulting in a polymer chain with imide linkages.
Chemical Structure of Polyimide
The chemical structure of polyimide consists of aromatic rings linked by imide groups. The general formula for polyimide can be represented as:
[-CO-NR-CO-Ar-]n
Where:
– CO: Carbonyl group
– NR: Imide group (R can be an aromatic or aliphatic group)
– Ar: Aromatic ring
– n: Degree of polymerization
The aromatic rings in the polyimide structure contribute to its high thermal stability and mechanical strength, while the imide groups provide excellent electrical insulation properties.
Key Features of Polyimide PCBs
Polyimide PCBs exhibit several unique features that set them apart from traditional FR-4 PCBs. These features make them suitable for applications that demand high reliability, performance, and durability.
1. High Temperature Resistance
One of the most significant advantages of Polyimide PCBs is their exceptional temperature resistance. Polyimide has a glass transition temperature (Tg) ranging from 360°C to 410°C, depending on the specific formulation. This high Tg allows Polyimide PCBs to maintain their structural integrity and electrical properties even at elevated temperatures.
Material | Glass Transition Temperature (Tg) |
---|---|
FR-4 | 130°C – 140°C |
Polyimide | 360°C – 410°C |
The high temperature resistance of Polyimide PCBs makes them ideal for applications that involve exposure to extreme heat, such as:
- Aerospace and aviation electronics
- Automotive under-the-hood components
- High-power LED lighting systems
- Oil and gas exploration equipment
2. Excellent Dimensional Stability
Polyimide PCBs exhibit outstanding dimensional stability, which means they maintain their shape and size even when subjected to thermal stress or mechanical strain. The coefficient of thermal expansion (CTE) of polyimide is significantly lower than that of FR-4, resulting in minimal warping or twisting of the PCB during temperature fluctuations.
Material | Coefficient of Thermal Expansion (CTE) |
---|---|
FR-4 | 14-16 ppm/°C |
Polyimide | 3-6 ppm/°C |
The excellent dimensional stability of Polyimide PCBs is particularly valuable in applications that require precise alignment and high-density interconnections, such as:
- Microelectronics packaging
- High-frequency radio frequency (RF) circuits
- Flexible printed circuits (FPCs)
- Chip-on-board (COB) assemblies
3. Superior Electrical Insulation
Polyimide PCBs offer superior electrical insulation properties compared to FR-4 PCBs. The dielectric constant (Dk) and dissipation factor (Df) of polyimide are lower than those of FR-4, resulting in reduced signal loss and improved signal integrity.
Material | Dielectric Constant (Dk) | Dissipation Factor (Df) |
---|---|---|
FR-4 | 4.2 – 4.5 | 0.02 – 0.03 |
Polyimide | 3.2 – 3.5 | 0.002 – 0.003 |
The superior electrical insulation properties of Polyimide PCBs make them suitable for high-frequency and high-speed applications, such as:
- 5G telecommunications equipment
- Radar systems
- Satellite communications
- High-speed digital circuits
4. High Mechanical Strength
Polyimide PCBs possess high mechanical strength and toughness, which enables them to withstand harsh environmental conditions and mechanical stresses. The tensile strength and elongation at break of polyimide are significantly higher than those of FR-4, making Polyimide PCBs more resilient to physical damage.
Material | Tensile Strength (MPa) | Elongation at Break (%) |
---|---|---|
FR-4 | 415 – 450 | 1.2 – 1.5 |
Polyimide | 350 – 400 | 10 – 20 |
The high mechanical strength of Polyimide PCBs is advantageous in applications that involve vibration, shock, or flexing, such as:
- Wearable electronics
- Aerospace and defense systems
- Robotics and automation
- Medical implantable devices
5. Chemical Resistance
Polyimide PCBs exhibit excellent chemical resistance, making them resistant to a wide range of solvents, acids, and bases. This property is crucial in applications where the PCB may be exposed to harsh chemicals or corrosive environments.
Chemical | FR-4 Resistance | Polyimide Resistance |
---|---|---|
Hydrochloric Acid (10%) | Poor | Excellent |
Sulfuric Acid (10%) | Poor | Excellent |
Sodium Hydroxide (10%) | Fair | Excellent |
Acetone | Fair | Excellent |
Isopropyl Alcohol | Good | Excellent |
The chemical resistance of Polyimide PCBs is valuable in industries such as:
- Chemical processing plants
- Pharmaceutical manufacturing
- Food and beverage processing
- Automotive fuel systems
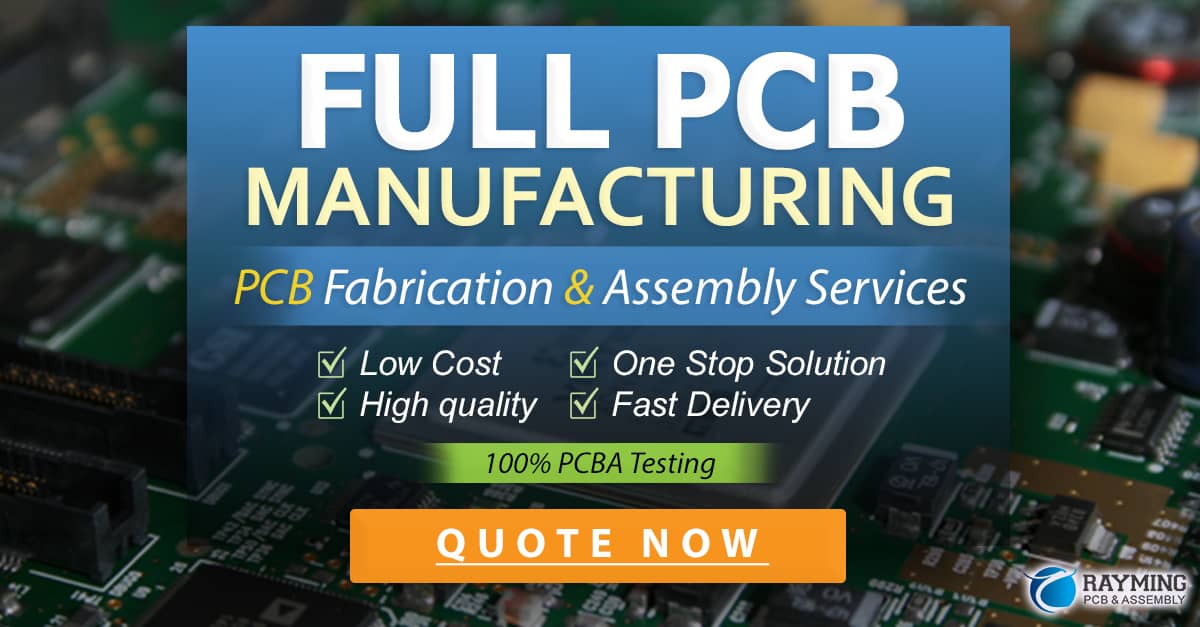
Applications of Polyimide PCBs in Various Industries
The unique features of Polyimide PCBs make them suitable for a wide range of industrial applications. Let’s explore some of the key sectors that benefit from the use of Polyimide PCBs.
1. Aerospace and Aviation
Polyimide PCBs are extensively used in the aerospace and aviation industry due to their ability to withstand extreme temperatures, vibrations, and mechanical stresses. They are employed in various applications, such as:
- Avionics systems
- Radar and navigation equipment
- Engine control units
- Satellite communications
The high temperature resistance and dimensional stability of Polyimide PCBs ensure reliable performance in the harsh conditions encountered in aerospace and aviation environments.
2. Automotive Electronics
The automotive industry has seen a significant increase in the use of electronic components, and Polyimide PCBs play a crucial role in enabling advanced features and functionalities. Some of the automotive applications that utilize Polyimide PCBs include:
- Engine control modules
- Transmission control units
- Hybrid and electric vehicle power electronics
- Advanced driver assistance systems (ADAS)
The ability of Polyimide PCBs to withstand high temperatures and mechanical stresses makes them ideal for under-the-hood applications, where reliability and durability are paramount.
3. Industrial Automation and Robotics
Polyimide PCBs are widely used in industrial automation and robotics applications, where high precision, reliability, and flexibility are essential. Some examples include:
- Motor control systems
- Sensor interfaces
- Robotic arms and grippers
- Industrial communication networks
The excellent electrical insulation properties and high mechanical strength of Polyimide PCBs enable the development of compact and robust control systems for automation and robotics.
4. Medical Devices
Polyimide PCBs find extensive applications in the medical device industry, particularly in implantable and wearable devices. Some of the medical applications that benefit from Polyimide PCBs are:
- Pacemakers and defibrillators
- Neurostimulators
- Wearable health monitoring devices
- Surgical instruments
The biocompatibility, flexibility, and high reliability of Polyimide PCBs make them suitable for medical devices that require long-term implantation or close contact with the human body.
5. Telecommunications
The telecommunications industry relies heavily on Polyimide PCBs for high-frequency and high-speed applications. Some examples include:
- 5G base stations and antennas
- Fiber-optic communication systems
- Microwave and millimeter-wave circuits
- Satellite communication equipment
The low dielectric constant and dissipation factor of Polyimide PCBs enable the design of high-performance RF and microwave circuits with minimal signal loss and distortion.
Frequently Asked Questions (FAQ)
-
Q: What is the maximum operating temperature for Polyimide PCBs?
A: Polyimide PCBs can typically withstand continuous operating temperatures up to 260°C and short-term exposure to temperatures as high as 400°C, depending on the specific formulation and manufacturing process. -
Q: Can Polyimide PCBs be used for flexible circuit applications?
A: Yes, Polyimide PCBs are well-suited for flexible circuit applications due to their high flexibility, mechanical strength, and ability to withstand repeated bending and flexing. -
Q: Are Polyimide PCBs more expensive than FR-4 PCBs?
A: Yes, Polyimide PCBs are generally more expensive than FR-4 PCBs due to the higher cost of the polyimide material and the specialized manufacturing processes required. However, the added cost is often justified by the superior performance and reliability offered by Polyimide PCBs in demanding applications. -
Q: Can Polyimide PCBs be soldered using standard soldering techniques?
A: Yes, Polyimide PCBs can be soldered using standard soldering techniques, such as reflow soldering and wave soldering. However, due to the high temperature resistance of polyimide, higher soldering temperatures and longer dwell times may be required compared to FR-4 PCBs. -
Q: Are Polyimide PCBs environmentally friendly?
A: Polyimide PCBs are considered more environmentally friendly than FR-4 PCBs due to their halogen-free nature and the absence of brominated flame retardants. Additionally, polyimide is inherently flame-retardant, eliminating the need for added flame retardants that may have adverse environmental impacts.
Conclusion
Polyimide PCBs offer a range of unique features that make them highly beneficial for demanding industrial applications. Their exceptional temperature resistance, dimensional stability, electrical insulation properties, mechanical strength, and chemical resistance set them apart from traditional FR-4 PCBs.
These distinctive characteristics enable Polyimide PCBs to excel in industries such as aerospace, automotive, industrial automation, medical devices, and telecommunications, where reliability, performance, and durability are critical.
As technology continues to advance and the demands on electronic systems become more stringent, the adoption of Polyimide PCBs is expected to grow further. Their ability to withstand harsh environments, maintain signal integrity, and provide long-term reliability makes them an indispensable component in the development of cutting-edge industrial applications.
By leveraging the unique features of Polyimide PCBs, engineers and designers can push the boundaries of what is possible in terms of performance, miniaturization, and functionality. As a result, Polyimide PCBs will continue to play a crucial role in driving innovation and enabling the next generation of industrial electronics.
0 Comments