Introduction to Boundary-Scan Testing
Boundary-Scan Testing, also known as JTAG (Joint Test Action Group) testing, is a method used to test interconnects on printed circuit boards (PCBs) or sub-assemblies. It involves using a boundary-scan cell to access and test the interconnects between integrated circuits (ICs) on a board without the need for physical test probes. This testing method has become increasingly important in PCB Assembly due to the growing complexity and density of modern electronic devices.
What is Boundary-Scan Testing?
Boundary-Scan Testing is a method that uses a boundary-scan cell, which is essentially a shift register, to access and test the interconnects between ICs on a PCB. The boundary-scan cells are integrated into the ICs and can be controlled and accessed via a serial interface, such as JTAG. By using this method, it is possible to test the interconnects between ICs without the need for physical test probes, which can be difficult or impossible to use on modern high-density PCBs.
How Does Boundary-Scan Testing Work?
The process of Boundary-Scan Testing involves several steps:
- Design for Testability: The PCB design must incorporate boundary-scan cells into the ICs and provide access to the JTAG interface.
- Boundary-Scan Description Language (BSDL) File Creation: A BSDL file is created for each IC, describing its boundary-scan architecture and capabilities.
- Test Pattern Generation: Test patterns are generated based on the BSDL files and the PCB netlist, which describes the interconnects between the ICs.
- Test Execution: The test patterns are applied to the PCB via the JTAG interface, and the responses are captured and compared to the expected results.
Benefits of Boundary-Scan Testing in PCB Assembly
1. Improved Test Coverage
One of the primary benefits of Boundary-Scan Testing is improved test coverage. With the increasing complexity and density of modern PCBs, it becomes more difficult to access and test all the interconnects using traditional methods, such as in-circuit testing (ICT) or flying probe testing. Boundary-Scan Testing allows for testing of interconnects that are otherwise inaccessible, ensuring a higher level of test coverage.
2. Reduced Test Time and Cost
Boundary-Scan Testing can significantly reduce the time and cost associated with PCB testing. Traditional testing methods often require the use of physical test probes, which can be time-consuming to set up and maintain. In contrast, Boundary-Scan Testing can be automated and performed quickly, reducing the overall test time. Additionally, the reduction in the need for physical test probes can lead to cost savings in terms of equipment and maintenance.
3. Early Defect Detection
Boundary-Scan Testing allows for early detection of defects in the PCB assembly process. By testing the interconnects between ICs, it is possible to identify issues such as open circuits, short circuits, and stuck-at faults early in the manufacturing process. This early defect detection can help reduce the number of defective boards that progress further down the assembly line, ultimately reducing scrap and rework costs.
4. Non-Intrusive Testing
Another benefit of Boundary-Scan Testing is its non-intrusive nature. Unlike traditional testing methods that require physical contact with the PCB, such as ICT or flying probe testing, Boundary-Scan Testing does not require any physical contact with the board. This non-intrusive testing approach reduces the risk of damaging the PCB or its components during the testing process.
5. Design for Testability
Incorporating Boundary-Scan Testing into the PCB design process promotes a design for testability (DFT) approach. By considering testability early in the design phase, engineers can ensure that the necessary boundary-scan cells and JTAG interfaces are included in the PCB design. This DFT approach can lead to improved test coverage, reduced test time, and lower overall manufacturing costs.
Limitations and Challenges of Boundary-Scan Testing
While Boundary-Scan Testing offers numerous benefits, it is essential to be aware of its limitations and challenges:
1. Limited Analog Testing Capabilities
Boundary-Scan Testing is primarily focused on digital circuits and interconnects. Its ability to test analog circuits is limited, and additional testing methods may be required to ensure complete coverage of analog components.
2. Dependency on IC Support
The effectiveness of Boundary-Scan Testing relies on the ICs supporting the boundary-scan architecture. Not all ICs have built-in boundary-scan cells, which can limit the applicability of this testing method in some cases.
3. Increased Design Complexity
Incorporating boundary-scan cells and JTAG interfaces into the PCB design can add complexity to the overall design process. This complexity may require additional time and resources during the design phase.
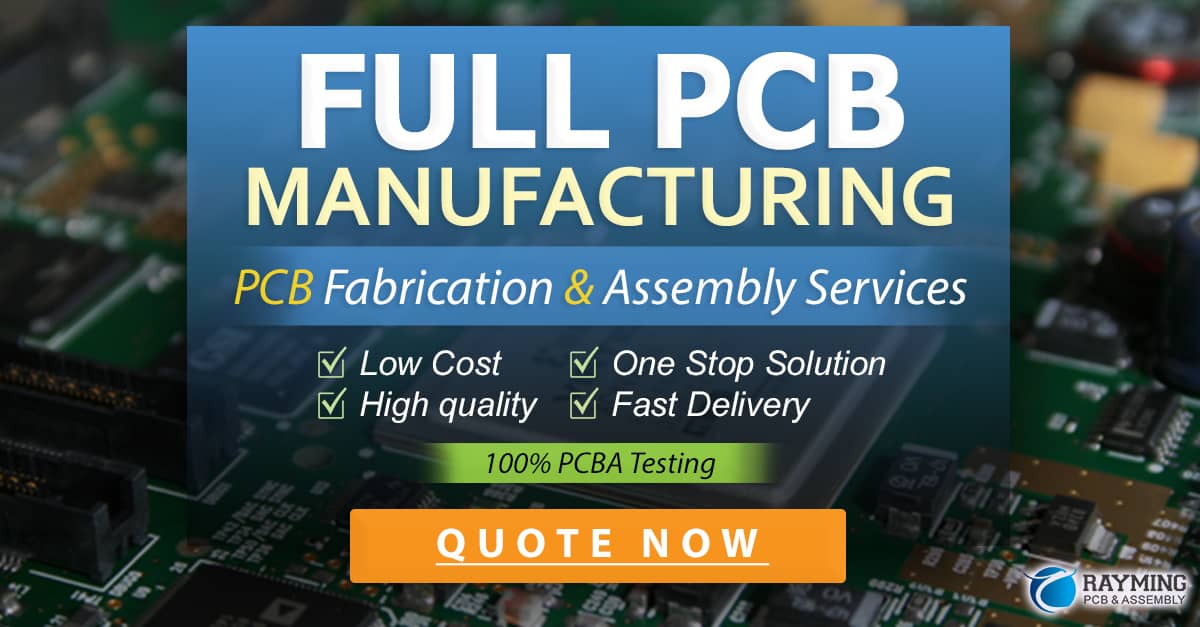
Boundary-Scan Testing in Action
To illustrate the benefits of Boundary-Scan Testing in PCB assembly, let’s consider a case study:
Case Study: Automotive Electronic Control Unit (ECU)
An automotive manufacturer was experiencing issues with the reliability of their electronic control units (ECUs). The high-density PCBs used in these ECUs were difficult to test using traditional methods, leading to a high number of defective units being shipped to customers.
To address this issue, the manufacturer decided to implement Boundary-Scan Testing in their PCB assembly process. By incorporating boundary-scan cells into the PCB design and using JTAG interfaces for testing, they were able to:
- Improve test coverage, detecting defects that were previously undetectable using traditional methods
- Reduce test time by automating the testing process
- Identify defects early in the manufacturing process, reducing scrap and rework costs
- Minimize the risk of damage to the PCBs during testing
The implementation of Boundary-Scan Testing resulted in a significant reduction in the number of defective ECUs shipped to customers, improving overall product quality and customer satisfaction.
Frequently Asked Questions (FAQ)
1. What is the difference between Boundary-Scan Testing and In-Circuit Testing (ICT)?
Boundary-Scan Testing focuses on testing the interconnects between ICs using boundary-scan cells and JTAG interfaces, while In-Circuit Testing involves the use of physical test probes to access and test individual components on the PCB.
2. Can Boundary-Scan Testing completely replace other testing methods?
While Boundary-Scan Testing offers many benefits, it is not a complete replacement for other testing methods. It is most effective when used in conjunction with other methods, such as ICT, flying probe testing, and functional testing, to ensure comprehensive test coverage.
3. How does Boundary-Scan Testing handle analog components?
Boundary-Scan Testing has limited capabilities when it comes to testing analog components. In most cases, additional testing methods, such as analog functional testing, may be required to ensure proper functionality of analog circuits.
4. What is a BSDL file, and why is it important in Boundary-Scan Testing?
A Boundary-Scan Description Language (BSDL) file is a standardized file format that describes the boundary-scan architecture and capabilities of an IC. It is essential for generating accurate test patterns and ensuring the effectiveness of Boundary-Scan Testing.
5. Can Boundary-Scan Testing be used for debugging and programming?
Yes, in addition to testing, Boundary-Scan Testing can also be used for debugging and programming purposes. The JTAG interface can be used to access and control individual ICs, enabling hardware debugging and in-system programming.
Conclusion
Boundary-Scan Testing is a powerful method for testing interconnects on PCBs, offering numerous benefits in the PCB assembly process. By improving test coverage, reducing test time and cost, enabling early defect detection, and promoting a design for testability approach, Boundary-Scan Testing can significantly enhance the quality and reliability of electronic devices.
While it is essential to be aware of its limitations and challenges, such as limited analog testing capabilities and dependency on IC support, the advantages of Boundary-Scan Testing make it an invaluable tool in modern PCB assembly.
As electronic devices continue to increase in complexity and density, the importance of Boundary-Scan Testing will only continue to grow. By embracing this testing method and incorporating it into the PCB design and assembly process, manufacturers can ensure the production of high-quality, reliable electronic products.
0 Comments