Key Characteristics of HT-PCBs
To be considered a true high temperature PCB, the board must have the following key properties:
-
Substrate material with a glass transition temperature (Tg) exceeding 170°C. Common HT substrates include polyimide, ceramic, Teflon, and PEEK.
-
Copper foil and plating rated for high temperatures, typically using rolled annealed or electrodeposited copper.
-
Solder mask and silkscreen able to withstand the max operating temperature without degrading. High temp masks are usually made of silicone or other HT polymers.
-
Specialty high melting point solder alloys, such as Sn10Pb90, used for component attachment instead of standard SAC alloys.
HT-PCBs meeting these criteria can have maximum operating temperatures as high as 250°C or more, allowing them to be used in extreme heat applications not possible with standard PCBs.
HT-PCB Substrate Materials
The foundation of any high temperature circuit board is the base substrate material. It provides mechanical support and electrical insulation for the copper traces. The most important property for a HT substrate is a glass transition temperature (Tg) that exceeds the maximum operating temperature the PCB will be exposed to.
Some of the most common HT-PCB substrate materials include:
Material | Tg (°C) | Max Temp (°C) | Dielectric Constant | Dissipation Factor |
---|---|---|---|---|
Polyimide | 250-400 | 225-300 | 3.4-3.5 | 0.002-0.003 |
PTFE/Teflon | 327 | 250 | 2.1 | 0.001 |
Ceramic | >400 | >400 | 5.9-10 | <0.001 |
PEEK | 289 | 260 | 3.2 | 0.003 |
Polyimide (PI)
Polyimide is one of the most widely used HT substrates due to its excellent thermal stability, mechanical toughness, and dielectric properties. PI laminates are available in flexible film or rigid sheet formats. Rigid PI PCBs are fabricated by laminating multiple sheets of PI film together with a binder material under heat and pressure. Flexible polyimide PCBs are made by directly applying the copper traces to the surface of a PI film. Polyimide boards can operate at temperatures up to 300°C continuously, making them suitable for the most demanding HT applications.
PTFE (Teflon)
Polytetrafluoroethylene or Teflon is another popular HT substrate known for its low dielectric constant and dissipation factor which enable high frequency operation. The non-stick surface of PTFE also provides excellent chemical resistance. Standard PTFE PCBs can handle temperatures up to 250°C. For even higher temperature demands up to 325°C, ceramic-filled PTFE laminates are available which increase the Tg and thermal conductivity at the expense of a higher dielectric constant.
Ceramics
For the ultimate in high temperature performance and reliability, ceramic PCBs reign supreme. Alumina (Al2O3) and aluminum nitride (AlN) ceramics have glass transition and melting temperatures far exceeding 400°C, allowing ceramics to operate in the most extreme heat environments. Ceramics also have high thermal conductivity to help dissipate heat. The main downsides are high cost, brittleness, and challenges machining and drilling holes compared to polymer substrates. Ceramic PCBs are often used in military, aerospace, and downhole drilling electronics.
PEEK
Polyether ether ketone is a semi-crystalline thermoplastic with excellent mechanical strength, fatigue resistance, and dimensional stability at high temperatures up to 260°C. PEEK PCBs maintain their properties even after long-term HT exposure and thermal cycling. PEEK has similar electrical properties to polyimide but can be injection molded to form thicker 3D PCB substrates.
High Temperature Solder
The solder used for component attachment is another critical aspect of HT-PCB performance. Standard lead-free SAC solders have a melting point around 220°C, making them unsuitable for soldering components that will operate above 200°C.
High melting point solders containing 90-97% lead are the primary choice for HT-PCBs. Some common HT solder alloys include:
Alloy | Composition | Melting Point (°C) |
---|---|---|
Sn10Pb90 | Tin 10%, Lead 90% | 302 |
Sn5Pb93.5Ag1.5 | Tin 5%, Lead 93.5%, Silver 1.5% | 296-301 |
Pb97Ag1.5Sn1.5 | Lead 97%, Silver 1.5%, Tin 1.5% | 309-310 |
These HMP solders enable components to be attached that can survive at temperatures approaching 300°C. The high lead content does pose some environmental and health concerns that must be dealt with.
For extreme temperatures above 350°C, brazing alloys based on gold, palladium and other metals with melting points over 600°C are used instead of solder.
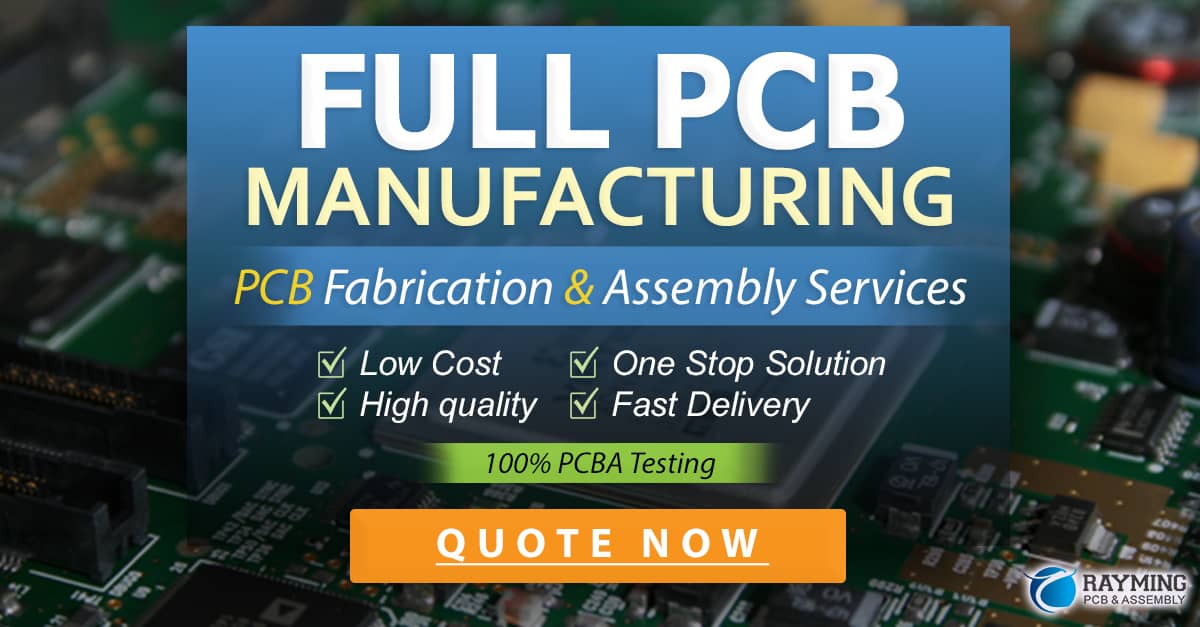
HT-PCB Design Considerations
Designing a high temperature PCB requires careful consideration of material selection, component derating, trace geometry, via structure and other factors to ensure reliability.
Some key design aspects to consider include:
-
Select HT substrate, solder mask, and solder materials rated for maximum expected operating temperature plus a margin of at least 25°C
-
Derate maximum power dissipation and voltage of components by at least 50% at elevated temperatures
-
Use large trace widths and copper weights to minimize resistive losses and voltage drops which increase with temperature
-
Provide adequate spacing between traces for high voltage circuits to maintain HT dielectric strength and creepage distance
-
Use filled thermal vias to conduct heat away from hot components into plane layers and heatsinks
-
Allow for greater thermal expansion in determining trace and via geometry to prevent failures from CTE mismatch
-
Use mechanical fastening like screws, eyelets or potting in addition to solder joints for components
-
Avoid large components and BGA packages which are more prone to failure from thermal stress
Careful design and thermal simulation of the PCB can help mitigate many of the risks of operating electronics at extreme temperatures.
HT-PCB Assembly Process
The assembly and soldering process for HT-PCBs is more challenging than standard PCBs due to the high melting point solders used. Special HT-rated solder flux is required that doesn’t degrade at soldering temperatures of 350°C or higher.
Solder paste stencil printing is rarely used for HMP solders because the paste dries out and crumbles. Instead, solder preforms cut from solder ribbon are placed on the component pads prior to placement. Liquid solder flux applied to the pads helps the solder preform stay in place.
Most HT PCB assembly is done with hand soldering using special HT soldering irons and tips. Nitrogen-purged vapor phase or convection reflow ovens can also be used. The solder joint quality is inspected under microscope more closely than normal to check for voids or cracks that could fail prematurely at high temperatures.
After soldering, it is common to centrifuge HT circuit boards to remove excess flux residue that could carbonize and cause dendritic growth at high temperature. Thorough cleaning of the PCB in HT defluxing solution is critical.
Some HT-PCBs are also encapsulated by potting the components in a thermally conductive epoxy or silicone compound to improve heat dissipation and mechanical robustness. The potting material must be carefully chosen to match the CTE of the solder joints.
HT-PCB Reliability Testing
Validating the reliability of HT-PCBs requires more stringent testing than regular PCBs. Common HT reliability tests include:
High Temperature Operating Life (HTOL)
HTOL testing subjects the powered PCB to the maximum rated operating temperature for 1000 hours or more. This tests the durability of the PCB substrate, conductors, solder joints and components to long-term heat exposure. Periodic electrical testing during HTOL verifies the PCB continues working throughout the test.
Thermal Cycling
HT-PCBs that will experience wide swings in ambient temperature need to be thermal cycled to stress the solder joints and check for failures from CTE mismatch. The IPC-TM-650 standard thermal shock test cycles the PCB between -65 and 150°C for 200 cycles or more.
Interconnect Stress Test (IST)
IST uses special coupons built into the PCB panel to intentionally strain solder joints until failure. This determines the amount of flexure and vibration the solder joints can withstand at high temperatures.
Combined Environments Testing
Some HT-PCB applications involve exposure to vibration, shock, moisture and chemicals in addition to heat. Combined environments testing exposes the PCB to all of these stresses simultaneously to verify its performance under the harshest conditions.
Thorough reliability testing is essential to qualifying HT-PCBs for mission-critical applications where replacement is difficult or impossible. Ongoing monitoring and built-in self test are also used to detect impending HT failures in the field.
Frequently Asked Questions
Q: What is the highest temperature a PCB can withstand?
A: With ceramics and specialty alloys, HT-PCBs can operate at temperatures of 400°C or higher. The exact maximum temperature depends on the substrate, solder, and components used.
Q: Are HT-PCBs more expensive than standard PCBs?
A: Yes, HT-PCB materials can cost 5-10 times more than FR-4 and assembly costs are higher due to manual soldering. However, the total system cost is often lower by eliminating the need for fans and cooling systems.
Q: Can HT solder be reflowed in a standard SMT oven?
A: No, the melting point of 90%+ lead solder is over 300°C, exceeding the max zone temperature of most convection SMT ovens. Vapor phase or hand soldering is typically required.
Q: Are components rated for high temperatures?
A: Semiconductor components are available rated for 175°C or higher operating temperature. Passive components like resistors and capacitors can be rated for 200-300°C. Components are generally the weakest link in HT-PCBs.
Q: What are the main applications for HT-PCBs?
A: High temperature electronics are used for engine and brake controls in automotive, avionics and aerospace systems, downhole drilling instruments for oil and gas exploration, industrial equipment sensors, and military/space systems.
0 Comments