Printed circuit boards (PCBs) are essential components in nearly all electronic devices. During the design and development process, engineers need prototype PCBs to test their circuits and ensure they function properly before going into mass production. High quality PCB prototypes are critical for catching errors early and delivering a successful finished product. This article explores what constitutes a high quality PCB prototype and best practices for procuring them.
What Makes a High Quality PCB Prototype?
Several key factors determine the quality of a PCB prototype:
Accuracy and Precision
The PCB must match the original design files precisely. Even minor deviations from the specifications can cause functional issues. High tolerance manufacturing standards ensure each trace width, hole size, and pad spacing are extremely accurate.
Reliable Components
Quality components must be used, even for prototypes. This includes the PCB substrate, copper layers, solder mask, and silkscreen. Failure to use robust materials can lead to cracks, delamination, or other defects during assembly and testing.
Clean Build
A high quality PCB prototype has a clean, professional build. There should be no extraneous markings, leftover flux, or scratches on the boards. Reflowed solder joints should exhibit a smooth shine. A clean prototype gives confidence in the manufacturer’s attention to detail.
Rigorous Testing
Extensive testing ensures the PCB functions as intended before shipping. This includes inspecting for shorts, opens, impedance issues, and verifying board stackup and finishes. Thorough testing reduces chances of problems down the line.
Quick Turnaround
Rapid turnaround allows designers to test prototypes sooner. Manufacturers able to produce quality boards in 5-10 days enable faster design iterations and product development.
Responsive Communication
Good communication and transparency throughout the process is essential. Engineers rely on updates from manufacturers to track progress and be alerted to any potential issues.
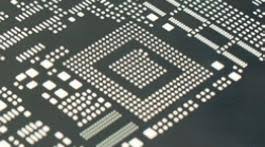
Best Practices for Procuring High Quality Prototypes
Following best practices helps ensure you receive high quality PCB prototypes:
Choose a Reputable Manufacturer
Select a manufacturer known for quality and reliability. Check reviews and ask colleagues for recommendations. Domestic manufacturers may provide tighter tolerances and better communication than some budget offshore options.
Provide Complete Design Files
Ensure gerbers, drill files, netlists, and other necessary files are complete, error-free, and clearly labeled. This reduces chances of ambiguity or misinterpretation by the manufacturer.
Request a Design Review
Have the manufacturer conduct a design for manufacturability (DFM) review of your files. They can catch any red flags early and suggest improvements before problems arise.
Order 1-2 Test Boards First
Before ordering a full prototyping run, request 1-2 test boards be built first. Review these boards thoroughly to confirm quality standards are met before proceeding.
Inspect Boards Upon Receipt
Carefully examine boards as soon as they are received. Look for any flaws in the PCB quality and assembly. Identify any issues immediately rather than later during testing.
Build a Relationship with the Manufacturer
Cultivate a relationship with your prototype manufacturer through clear communication. Work together to achieve the highest quality boards for your needs.
Comparing PCB Prototype Manufacturers
With many options available, here are key factors to consider when selecting a PCB prototype manufacturer:<div class=”table-responsive”>
Manufacturer | Location | Turnaround Time | Capabilities | Pricing | Quality Reputation |
---|---|---|---|---|---|
PCBCart | China | 5 days | Moderate | Low | Good |
PCBWay | China | 24 hours | Wide range | Low | Excellent |
Advanced Circuits | Colorado, USA | 4 days | Wide range | Medium | Excellent |
Sierra Circuits | California, USA | 10 days | Wide range | Medium | Excellent |
JLCPCB | China | 24 hours | Limited | Low | Good |
</div>
Domestic manufacturers like Advanced Circuits and Sierra Circuits are good options when quality and fast turnaround are critical, despite their higher costs. For more affordable lower-volume runs, PCBWay and JLCPCB have proven track records.
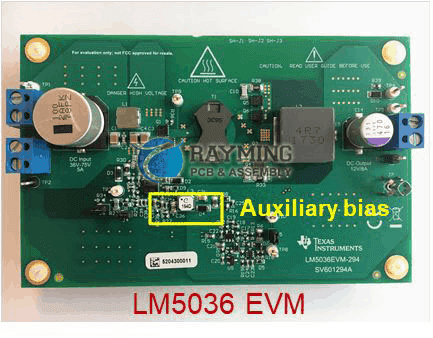
High Quality Prototype Case Study
Here is an example highlighting the benefits of using a high quality PCB prototype manufacturer:
Scenario
An automotive company is developing a new vehicle backup camera system. The engineering team needs several prototype camera PCBs to test in vehicles before finalizing the design.
Solution
The team selects Advanced Circuits to build the prototype PCBs. They choose Advanced for their reputation of high quality domestic manufacturing.
Advanced works closely with the engineering team on a DFM analysis to optimize the design for producibility. They provide rapid 5 day turnaround on building the first test boards.
The engineers thoroughly evaluate the initial PCBs. The boards meet all their precision tolerances and exhibit excellent soldering. A couple minor issues are identified on the first boards, which Advanced corrects for the second iteration.
With high quality prototype boards in hand, the team successfully evaluates the camera performance in test vehicles. This confirms the design is ready for mass production. The strong prototyping partnership with Advanced Circuits enables the project to stay on schedule.
Frequently Asked Questions
What are the most important specs to check for a quality PCB prototype?
The most critical specifications are: trace width/spacing, hole size/tolerance, substrate thickness, metal layer thickness, impedance control, and coplanarity. Verify these are all within your required tolerances.
Should I include a solder mask on a prototype PCB?
Yes, solder mask should be included even on prototypes. It protects against shorts and oxidation during assembly. Prototype testing best replicates the final product when a solder mask is applied.
How many times can prototype PCBs be reworked/assembled?
Quality PCB prototypes can be reworked and assembled multiple times during testing. Lower quality boards may lose adhesion or warp after 1-2 passes through an oven. The best prototypes maintain integrity through dozens of cycles.
Should I pay extra for controlled impedance on prototype boards?
It depends. For very high frequency or sensitive analog circuits, controlled impedance is recommended. For more robust digital circuits, it may not be necessary for early prototyping. Assess your specific needs.
How long does full functional testing take?
Functional testing time varies based on board complexity, but often takes 1-3 days. Critical components and nets are checked for shorts/opens. Boards may be powered on to verify current draw and basic operation. Extended functional testing with connected components can take a week or longer.
In summary, high quality PCB prototypes are invaluable for validating electronic device designs. Carefully selecting a capable manufacturer, inspecting boards thoroughly, and working collaboratively enables optimal prototypes. Investing in quality prototyping reduces development risk and accelerates time-to-market.
0 Comments