Introduction to High Current PCB
In the world of electronics, printed circuit boards (PCBs) play a crucial role in connecting and supporting various components. Among the different types of PCBs, high current PCBs stand out for their ability to handle significant amounts of electrical current without compromising performance or reliability. These specialized boards find applications in power electronics, automotive systems, industrial equipment, and more.
In this comprehensive article, we will dive deep into the world of high current PCBs, exploring their unique characteristics, design considerations, manufacturing processes, and common applications. Whether you are an electrical engineer, a PCB designer, or simply curious about the capabilities of these powerful boards, this article will provide you with valuable insights and information.
What is a High Current PCB?
A high current PCB is a type of printed circuit board specifically designed to handle high levels of electrical current. Unlike standard PCBs, which are primarily focused on signal routing and component placement, high current PCBs prioritize current carrying capacity and thermal management.
The key characteristics of a high current PCB include:
-
Thicker copper traces: To accommodate higher currents, the copper traces on a high current PCB are significantly thicker than those on a standard PCB. This increased thickness allows for better current flow and reduces resistance.
-
Wider trace widths: In addition to being thicker, the traces on a high current PCB are also wider. The increased width further enhances the current carrying capacity and helps distribute heat more effectively.
-
Specialized substrate materials: High current PCBs often utilize specialized substrate materials that offer improved thermal conductivity and heat dissipation properties. These materials help prevent excessive heat buildup, which can lead to component failure or reduced performance.
-
Robust power and ground planes: To ensure stable power delivery and minimize voltage drops, high current PCBs incorporate robust power and ground planes. These planes provide low-impedance paths for current flow and help maintain signal integrity.
Design Considerations for High Current PCBs
Designing a high current PCB requires careful consideration of various factors to ensure optimal performance, reliability, and safety. Let’s explore some of the key design considerations:
Current Carrying Capacity
One of the primary considerations when designing a high current PCB is the current carrying capacity of the traces. The amount of current a trace can handle depends on several factors, including the trace width, thickness, and the ambient temperature.
To determine the appropriate trace width and thickness, designers often refer to charts or calculators that provide guidelines based on the desired current rating and temperature rise. The IPC-2152 standard, which is widely accepted in the industry, offers comprehensive charts and equations for calculating trace dimensions.
Here’s an example table showing the current carrying capacity for different trace widths and thicknesses at an ambient temperature of 25°C:
Trace Width (mm) | Trace Thickness (oz) | Current Carrying Capacity (A) |
---|---|---|
0.5 | 1 | 2.5 |
1.0 | 1 | 4.0 |
1.5 | 1 | 5.5 |
2.0 | 2 | 10.0 |
3.0 | 2 | 14.0 |
It’s important to note that these values are just guidelines, and the actual current carrying capacity may vary based on factors such as the PCB material, copper quality, and environmental conditions.
Thermal Management
Handling high currents inevitably leads to heat generation, which can have detrimental effects on the performance and longevity of the PCB and its components. Effective thermal management is crucial in high current PCB design.
Designers employ various techniques to dissipate heat and prevent thermal issues:
-
Copper pours: Large copper pours, also known as copper fills or polygons, are used to increase the heat dissipation area. These pours act as heat sinks, spreading the heat over a larger surface and facilitating its transfer to the surrounding environment.
-
Thermal vias: Thermal vias are strategically placed vias that connect the high current traces to the ground or power planes. These vias provide additional paths for heat to flow away from the traces and into the planes, where it can be dissipated more efficiently.
-
Heatsinks and cooling solutions: In some cases, external heatsinks or active cooling solutions, such as fans or liquid cooling systems, may be necessary to manage the heat generated by high current components. These solutions help maintain a stable operating temperature and prevent thermal runaway.
Voltage Drop and Power Distribution
Voltage drop is another critical consideration in high current PCB design. As current flows through the traces, there is a voltage drop due to the inherent resistance of the copper. This voltage drop can lead to reduced performance and efficiency, particularly in sensitive analog circuits.
To minimize voltage drop, designers must carefully plan the power distribution network on the PCB. This involves:
-
Proper trace routing: The traces carrying high currents should be kept as short as possible to minimize resistance. They should also be routed away from sensitive signal traces to avoid interference.
-
Adequate power and ground planes: Incorporating dedicated power and ground planes helps distribute the current evenly across the PCB. These planes provide low-impedance paths for current flow and reduce voltage drops.
-
Decoupling capacitors: Placing decoupling capacitors close to high current components helps stabilize the local power supply and reduces voltage fluctuations caused by sudden current demands.
Component Selection and Placement
Choosing the right components and placing them strategically on the PCB is critical for high current applications. Designers must consider factors such as current ratings, power dissipation, and thermal characteristics when selecting components.
High current components, such as power MOSFETs, rectifier diodes, and large capacitors, should be placed close to their respective power and ground connections to minimize trace lengths and reduce voltage drops. They should also be positioned in a way that allows for effective heat dissipation, with sufficient spacing between components to prevent thermal coupling.
Proper component placement also helps optimize the overall layout of the PCB, reducing the risk of electromagnetic interference (EMI) and improving signal integrity.
Manufacturing Process for High Current PCBs
The manufacturing process for high current PCBs differs from that of standard PCBs due to the unique requirements for thick copper traces and specialized materials. Let’s take a closer look at the key steps involved:
PCB Material Selection
The choice of PCB material is crucial for high current applications. The substrate must have excellent thermal conductivity and heat dissipation properties to prevent excessive heat buildup. Common materials used for high current PCBs include:
-
Aluminum-backed PCBs: These PCBs have an aluminum substrate that acts as a heatsink, efficiently dissipating heat away from the components and traces.
-
Ceramic-based PCBs: Ceramic substrates offer excellent thermal conductivity and can withstand high temperatures, making them suitable for high power applications.
-
Metal Core PCBs (MCPCBs): MCPCBs have a metal core, typically aluminum or copper, sandwiched between the layers of the PCB. The metal core provides a low thermal resistance path for heat dissipation.
Copper Plating and Etching
To achieve the thick copper traces required for high current PCBs, a specialized plating process is employed. The PCB undergoes electroplating, where additional copper is deposited onto the traces to increase their thickness. This process is carefully controlled to ensure uniform copper distribution and avoid any defects.
After plating, the PCB undergoes etching to remove the unwanted copper and define the final trace patterns. The etching process for high current PCBs requires precise control to maintain the desired trace widths and ensure consistent current carrying capacity.
Drilling and Vias
Drilling and via creation are critical steps in the manufacturing of high current PCBs. The vias must be properly sized and positioned to accommodate the high currents and facilitate heat dissipation.
Thermal vias, as mentioned earlier, are often used to transfer heat from the traces to the power and ground planes. These vias are typically filled with a conductive material, such as copper or silver epoxy, to enhance their thermal conductivity.
Solder Mask and Silkscreen
The solder mask and silkscreen layers are applied to the PCB to protect the traces and provide component identification. In high current PCBs, the solder mask must be carefully selected to withstand the elevated temperatures and prevent any degradation over time.
The silkscreen layer is used to label components and provide assembly instructions. It is important to ensure that the silkscreen markings are clear and durable, as high current PCBs may be subjected to harsh environmental conditions.
Quality Control and Testing
Stringent quality control measures are implemented throughout the manufacturing process of high current PCBs. Visual inspections, automated optical inspection (AOI), and electrical testing are performed to identify any defects or inconsistencies.
High current PCBs undergo rigorous testing to verify their current carrying capacity, thermal performance, and overall reliability. These tests may include:
-
Current stress testing: The PCB is subjected to its maximum rated current for an extended period to ensure it can handle the specified current without any issues.
-
Thermal imaging: Thermal cameras are used to monitor the temperature distribution across the PCB during operation, identifying any hot spots or areas of concern.
-
Insulation resistance testing: This test measures the resistance between the conductors and the insulation to ensure there are no leakage paths or shorts.
-
Microsectioning: In some cases, a cross-section of the PCB may be examined under a microscope to verify the integrity of the copper plating and the bonding between layers.
Passing these quality control checks and tests ensures that the high current PCB meets the required specifications and is ready for assembly and deployment in the intended application.
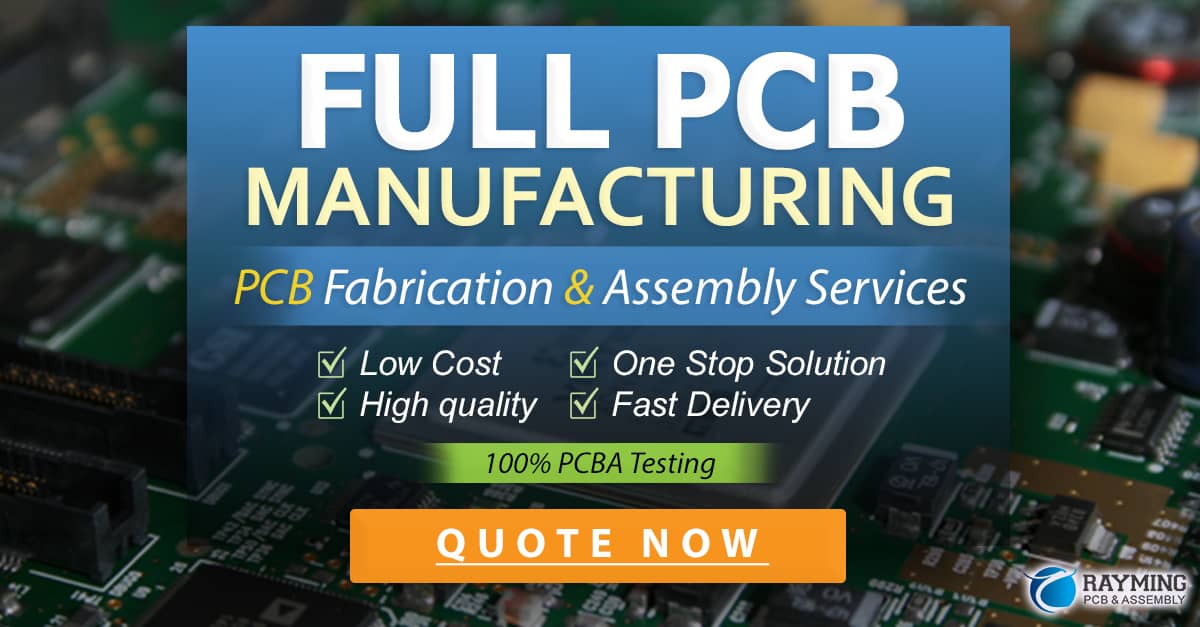
Common Applications of High Current PCBs
High current PCBs find applications in various industries and sectors where reliable and efficient handling of high currents is crucial. Some common applications include:
Power Electronics
Power electronics involve the conversion, control, and conditioning of electrical power. High current PCBs are extensively used in power electronic circuits, such as:
-
Switched-mode power supplies (SMPS): These power supplies convert AC to DC or DC to DC and require high current handling capabilities for efficient power conversion.
-
Motor drives and controllers: PCBs used in motor control applications must handle high currents to drive the motor windings and ensure smooth operation.
-
Inverters and converters: High current PCBs are used in inverter and converter circuits to manage the flow of power between different electrical systems.
Automotive Electronics
The automotive industry relies heavily on high current PCBs for various electronic systems within vehicles. Some examples include:
-
Engine control units (ECUs): ECUs manage various aspects of the vehicle’s engine, such as fuel injection, ignition timing, and emissions control. They require high current PCBs to handle the power demands of the engine.
-
Electric vehicle (EV) powertrains: EVs rely on high current PCBs to control the flow of power from the battery to the electric motors and manage the charging process.
-
Lighting and infotainment systems: High current PCBs are used in automotive lighting systems, such as headlights and taillights, as well as in infotainment systems that require reliable power delivery.
Industrial Equipment
Industrial equipment often demands high current handling capabilities due to the power-intensive nature of the applications. Some examples include:
-
Motor control systems: Industrial motors, such as those used in conveyor belts, cranes, and robotics, require high current PCBs to control and regulate their operation.
-
Power distribution systems: High current PCBs are used in industrial power distribution systems to manage the flow of electricity and ensure safe and efficient operation.
-
Welding equipment: Welding machines generate high currents to create the heat necessary for melting and joining metals. High current PCBs are used to control and regulate the welding process.
Renewable Energy Systems
Renewable energy systems, such as solar panels and wind turbines, rely on high current PCBs for power management and control. These PCBs handle the high currents generated by the energy sources and ensure efficient power conversion and distribution.
-
Solar inverters: High current PCBs are used in solar inverters to convert the DC power generated by solar panels into AC power suitable for grid integration or local consumption.
-
Wind turbine controllers: PCBs in wind turbine systems manage the generator’s output and control the pitch and yaw of the turbine blades to optimize power generation.
Telecommunications Infrastructure
Telecommunications infrastructure, including base stations and data centers, requires high current PCBs to handle the power demands of the equipment. These PCBs ensure reliable power delivery to the communication systems, enabling seamless connectivity and data transmission.
Frequently Asked Questions (FAQ)
-
What is the difference between a high current PCB and a standard PCB?
A high current PCB is specifically designed to handle higher levels of electrical current compared to a standard PCB. It features thicker copper traces, wider trace widths, specialized substrate materials, and robust power and ground planes to accommodate the increased current flow and manage heat dissipation effectively. -
How do I determine the appropriate trace width and thickness for a high current PCB?
The appropriate trace width and thickness for a high current PCB depends on factors such as the desired current rating, ambient temperature, and the PCB material. Designers often refer to industry standards, such as IPC-2152, which provide guidelines and charts for calculating trace dimensions based on these factors. It’s important to consult the relevant standards and consider the specific requirements of the application when determining the trace dimensions. -
What are some common materials used for high current PCBs?
Some common materials used for high current PCBs include aluminum-backed PCBs, ceramic-based PCBs, and Metal Core PCBs (MCPCBs). These materials offer excellent thermal conductivity and heat dissipation properties, making them suitable for high power applications. The choice of material depends on factors such as the operating temperature range, thermal management requirements, and cost considerations. -
How does the manufacturing process differ for high current PCBs compared to standard PCBs?
The manufacturing process for high current PCBs involves specialized techniques to achieve the required thick copper traces and ensure reliable performance. Key differences include the use of electroplating to deposit additional copper onto the traces, precise etching to maintain the desired trace widths, and the incorporation of thermal vias to facilitate heat dissipation. Quality control measures, such as current stress testing and thermal imaging, are also more stringent for high current PCBs to ensure they meet the specified requirements. -
What are some common applications of high current PCBs?
High current PCBs find applications in various industries, including power electronics, automotive systems, industrial equipment, renewable energy systems, and telecommunications infrastructure. They are used in circuits and systems that require reliable and efficient handling of high currents, such as switched-mode power supplies, motor drives, electric vehicle powertrains, welding equipment, solar inverters, and base stations. The specific application dictates the design requirements and considerations for the high current PCB.
Conclusion
High current PCBs are essential components in applications that demand reliable and efficient handling of significant electrical currents. By understanding the unique characteristics, design considerations, and manufacturing processes involved in creating these specialized boards, engineers and designers can develop robust and high-performing electronic systems.
From power electronics and automotive systems to industrial equipment and renewable energy, high current PCBs play a crucial role in ensuring the smooth operation and longevity of various applications. As technology continues to advance and power demands increase, the importance of high current PCBs will only continue to grow.
By staying informed about the latest advancements and best practices in high current PCB design and manufacturing, engineers can push the boundaries of what is possible and create innovative solutions that meet the ever-evolving needs of the electronics industry.
0 Comments