Introduction to High Current PCB Design
High current PCB design is a critical aspect of modern electronics, particularly in applications such as power supplies, electric vehicles, and industrial automation. Designing a PCB that can handle high currents efficiently and reliably requires careful consideration of various factors, including thermal management, conductor sizing, and layout optimization. In this article, we will explore the key principles and techniques for designing and optimizing high current PCBs to achieve optimal performance and reliability.
Understanding the Challenges of High Current PCB Design
Thermal Management
One of the primary challenges in high current PCB design is managing the heat generated by the high current flow. As current passes through the conductors on the PCB, it generates heat due to the resistance of the copper traces. If this heat is not effectively dissipated, it can lead to various issues, such as:
- Component overheating and failure
- PCB substrate degradation
- Reduced overall system reliability
To mitigate these issues, it is essential to implement proper thermal management techniques in the PCB design process.
Conductor Sizing and Current Capacity
Another critical aspect of high current PCB design is ensuring that the conductors on the board are properly sized to handle the required current. The current-carrying capacity of a conductor is determined by several factors, including:
- Cross-sectional area of the conductor
- Conductor material (typically copper)
- Ambient temperature
- Maximum allowable temperature rise
Inadequate conductor sizing can result in excessive heat generation, voltage drop, and even conductor failure.
EMI and Signal Integrity
High current PCBs can also be susceptible to electromagnetic interference (EMI) and signal integrity issues. The high current flows can generate significant electromagnetic fields, which can couple with nearby traces and components, causing unwanted noise and interference. Additionally, the large current transients associated with high current applications can cause voltage fluctuations and ground bounce, which can disrupt the operation of sensitive components.
Designing High Current PCBs
Choosing the Right PCB Material
The choice of PCB material is crucial in high current applications. The substrate must have good thermal conductivity to facilitate heat dissipation, as well as adequate dielectric strength to withstand the high voltages often associated with high current circuits. Some common PCB materials suitable for high current applications include:
- FR-4: A glass-reinforced epoxy laminate, widely used in PCB fabrication. It has good thermal stability and dielectric strength, making it suitable for many high current applications.
- Metal Core PCBs (MCPCBs): These PCBs feature a metal core, typically aluminum, which acts as a heat spreader. The metal core helps to efficiently dissipate heat from the components and conductors, making MCPCBs ideal for high power density applications.
- Ceramic PCBs: Made from materials such as alumina or aluminum nitride, ceramic PCBs offer excellent thermal conductivity and dielectric strength. They are often used in high-temperature and high-voltage applications.
Thermal Management Techniques
To ensure proper thermal management in high current PCBs, several techniques can be employed:
-
Copper pours and planes: Using large copper pours and planes on the PCB helps to distribute heat more evenly across the board. These copper areas act as heat spreaders, conducting heat away from hot spots and towards the edges of the board, where it can be dissipated through convection or conduction to a heatsink.
-
Thermal vias: Thermal vias are small, plated through-holes that are strategically placed beneath high-power components to provide a low-resistance thermal path to the opposite side of the board or to an internal copper plane. By allowing heat to flow through the PCB substrate, thermal vias help to reduce component temperatures and improve overall thermal performance.
-
Heatsinks and cooling solutions: In some cases, passive or active cooling solutions may be necessary to effectively dissipate heat from high current PCBs. Heatsinks can be attached to high-power components or to the PCB itself to increase the surface area available for heat dissipation. Active cooling solutions, such as fans or liquid cooling systems, can be employed in more demanding applications to provide enhanced thermal management.
Conductor Sizing and Layout
Proper conductor sizing and layout are essential for ensuring reliable operation and minimizing losses in high current PCBs. When designing conductors for high current applications, consider the following guidelines:
-
Use appropriate trace widths: The width of the copper traces on the PCB should be selected based on the expected current flow and the maximum allowable temperature rise. Wider traces have lower resistance and can handle higher currents without excessive heating. IPC-2152, a standard for trace current capacity, provides guidelines for determining the appropriate trace widths based on various factors such as copper thickness, temperature rise, and ambient temperature.
-
Minimize trace length: To reduce resistive losses and voltage drop, it is important to keep the length of high current traces as short as possible. This can be achieved by placing components strategically and routing traces efficiently.
-
Use multiple layers: In high current PCBs, it is often necessary to use multiple copper layers to accommodate the required current-carrying capacity. By distributing the current across multiple layers, the overall current density can be reduced, minimizing heat generation and voltage drop.
-
Implement proper grounding: A robust grounding scheme is crucial for maintaining signal integrity and minimizing EMI in high current PCBs. Use dedicated ground planes and carefully route return paths to ensure low-impedance grounding throughout the board.
EMI Reduction Techniques
To minimize EMI and maintain signal integrity in high current PCBs, several techniques can be employed:
-
Decoupling capacitors: Place decoupling capacitors close to high-current components to reduce high-frequency noise and stabilize the power supply. These capacitors provide a local, low-impedance source of charge, minimizing voltage fluctuations and ground bounce.
-
Shielding: In some cases, sensitive components or traces may need to be shielded from the electromagnetic fields generated by high current flows. This can be achieved using conductive shields, such as metal cans or conductive tape, which are placed over the sensitive areas to provide electromagnetic isolation.
-
Proper routing and spacing: When routing high current traces, it is important to maintain adequate spacing from sensitive signals to minimize crosstalk and interference. Follow guidelines for trace spacing and parallelism to ensure signal integrity.
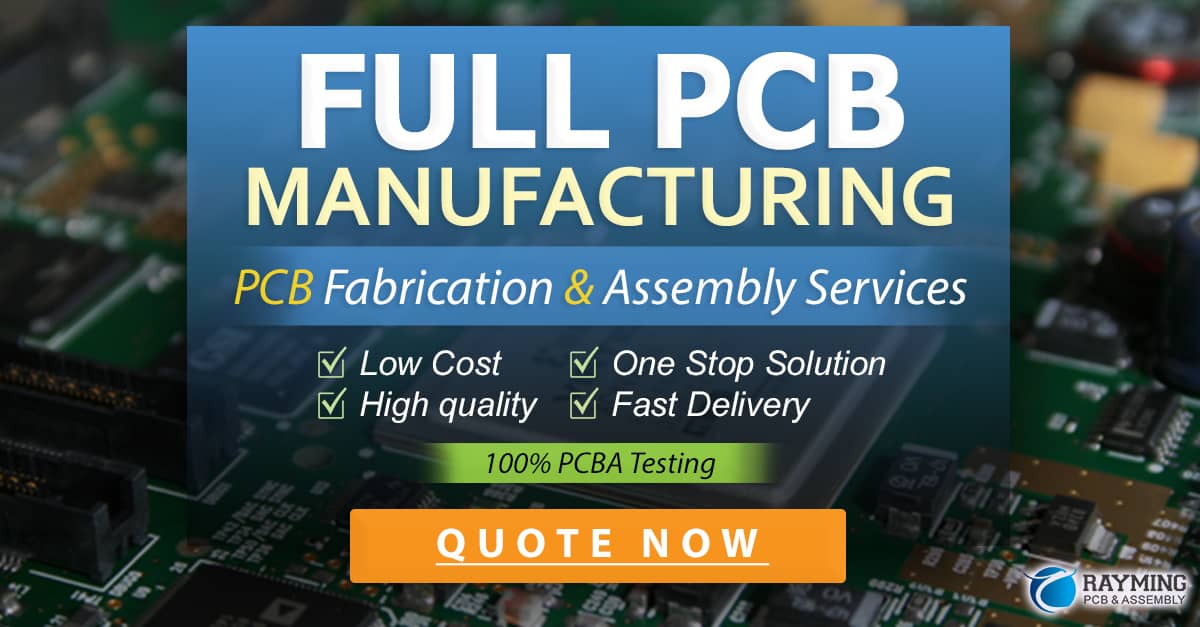
Optimizing High Current PCB Design
Simulation and Analysis
To optimize the performance of high current PCBs, it is essential to perform simulations and analyses during the design process. Some key analyses to consider include:
-
Thermal analysis: Use thermal simulation tools to predict the temperature distribution across the PCB and identify potential hot spots. This information can be used to optimize the placement of components and cooling solutions, ensuring that the board operates within safe temperature limits.
-
Current density analysis: Analyze the current density in the conductors to ensure that no areas are exceeding the maximum allowable current density. This helps to identify potential bottlenecks and allows for optimizing the conductor layout and sizing.
-
Signal integrity analysis: Perform signal integrity simulations to evaluate the impact of high current flows on sensitive signals. This can help to identify potential issues, such as crosstalk or ground bounce, and guide the implementation of appropriate mitigation techniques.
Design for Manufacturing (DFM)
To ensure the manufacturability and reliability of high current PCBs, it is important to follow Design for Manufacturing (DFM) principles. Some key considerations include:
-
Copper balancing: Ensure that the copper distribution across the layers of the PCB is balanced to minimize warpage and stress during the manufacturing process. This is particularly important for high current PCBs, which often have thick copper layers.
-
Solder mask and silkscreen: Use solder mask and silkscreen to protect the PCB and provide clear labeling for components and test points. This helps to prevent short circuits and makes the board easier to assemble and debug.
-
Testability: Incorporate test points and other features that facilitate testing and debugging of the high current PCB. This can include the use of test pads, vias, or connectors that allow for easy access to critical signals and power rails.
Case Studies and Examples
To illustrate the principles and techniques discussed in this article, let’s explore a few real-world examples of high current PCB design and optimization.
Example 1: High Power LED Driver
In this example, a high current PCB is designed to drive a high-power LED array. The key design challenges include:
- Managing the heat generated by the LEDs and driver circuitry
- Ensuring adequate current-carrying capacity for the LED current
- Minimizing voltage drop and power loss
To address these challenges, the following optimizations were implemented:
- A metal core PCB (MCPCB) was selected to provide excellent thermal conductivity and heat spreading.
- The LED driver IC was placed on the bottom side of the board, directly beneath the LED array, to minimize the length of the high current traces.
- Thermal vias were used to provide a low-resistance thermal path from the LED array to the metal core, enhancing heat dissipation.
- The high current traces were sized based on the maximum LED current and allowable temperature rise, ensuring reliable operation.
Example 2: High Current Motor Controller
In this example, a high current PCB is designed to control a high-power brushless DC motor. The key design challenges include:
- Managing the high currents required by the motor windings
- Ensuring proper thermal management for the power electronic components
- Minimizing EMI and maintaining signal integrity
To address these challenges, the following optimizations were implemented:
- The PCB was designed using a 4-layer stackup, with dedicated power and ground planes to minimize impedance and provide a low-inductance current path.
- The power electronic components, such as MOSFETs and sense resistors, were selected based on their current ratings and thermal characteristics.
- Large copper pours were used to spread heat across the board, and thermal vias were employed to transfer heat to the bottom side of the PCB, where a heatsink was attached.
- Decoupling capacitors were placed close to the power electronic components to reduce high-frequency noise and ensure stable operation.
- Sensitive control signals were routed away from high current traces, and shielding was used to minimize EMI.
FAQ
- What are the most important considerations when designing a high current PCB?
-
Thermal management, conductor sizing, and layout optimization are the most critical aspects of high current PCB design. Ensuring proper heat dissipation, selecting appropriate conductor widths, and minimizing voltage drop and power loss are essential for reliable operation.
-
How can I determine the appropriate trace width for a given current?
-
The appropriate trace width can be determined using guidelines such as IPC-2152, which provides charts and formulas for calculating the required trace width based on factors such as current, copper thickness, temperature rise, and ambient temperature.
-
What are the benefits of using a metal core PCB (MCPCB) in high current applications?
-
MCPCBs offer excellent thermal conductivity and heat spreading capabilities, thanks to their metal core (usually aluminum). This makes them ideal for high power density applications where effective heat dissipation is crucial.
-
How can I minimize EMI and ensure signal integrity in high current PCBs?
-
To minimize EMI and maintain signal integrity, use techniques such as placing decoupling capacitors close to high-current components, shielding sensitive areas, and properly routing and spacing traces. Maintaining a robust grounding scheme is also essential.
-
What are some Design for Manufacturing (DFM) considerations for high current PCBs?
- Key DFM considerations for high current PCBs include ensuring copper balancing to minimize warpage, using solder mask and silkscreen for protection and clear labeling, and incorporating features that facilitate testing and debugging, such as test points and accessible vias or connectors.
Conclusion
Designing and optimizing high current PCBs requires careful consideration of thermal management, conductor sizing, layout optimization, and EMI reduction techniques. By understanding the challenges associated with high current PCB design and implementing appropriate strategies, designers can create reliable and efficient boards that meet the demands of modern power electronic applications.
Through the use of advanced PCB materials, thermal management techniques, and simulation-driven optimization, high current PCBs can be designed to handle even the most demanding requirements. By following best practices for design and manufacturing, engineers can ensure that their high current PCBs perform optimally and reliably in the field.
As power electronic applications continue to push the boundaries of performance and efficiency, the importance of effective high current PCB design will only continue to grow. By staying up-to-date with the latest techniques and technologies, designers can create PCBs that not only meet the needs of today’s applications but also lay the foundation for future innovations in the field.
0 Comments