What is HDI PCB?
HDI (High Density Interconnect) PCB is a type of printed circuit board that features a higher wiring density per unit area than conventional PCBs. This is achieved through the use of smaller vias, finer trace widths and spaces, and higher connection pad density. HDI PCBs allow for more complex designs with increased functionality in a smaller footprint, making them ideal for applications where space is limited, such as smartphones, tablets, and wearable devices.
Key Features of HDI PCBs
-
Microvias: HDI PCBs use microvias, which are small holes drilled by lasers, typically with diameters less than 150μm. This allows for higher density interconnections between layers.
-
Fine pitch: The distance between the centers of two adjacent pads or holes is reduced, enabling the placement of more components in a smaller area.
-
Thin traces: HDI PCBs have trace widths and spaces as small as 50μm, allowing for more routing paths in a limited space.
-
High layer count: With the use of microvias and buried vias, HDI PCBs can have a higher number of layers compared to traditional PCBs, facilitating more complex designs.
HDI PCB Manufacturing Process
The manufacturing process of HDI PCBs involves several key steps to ensure high quality and reliability.
1. Material Selection
Choosing the right substrate material is crucial for HDI PCBs. The most commonly used materials are:
- FR-4: A glass-reinforced epoxy laminate with good mechanical and electrical properties.
- Polyimide: A high-performance material with excellent thermal stability and flexibility.
- Rogers: A low-loss, high-frequency material suitable for RF applications.
2. Drilling
HDI PCBs require precise drilling techniques to create microvias and through-holes. There are two main methods:
- Mechanical drilling: Used for larger holes and through-holes.
- Laser drilling: Employed for creating microvias, as it offers higher precision and smaller hole sizes.
3. Plating and Patterning
After drilling, the PCB undergoes a series of plating and patterning processes:
- Electroless copper plating: A thin layer of copper is deposited onto the drilled holes and the surface of the PCB.
- Photoresist application: A light-sensitive material is applied to the copper surface.
- Exposure and development: The photoresist is exposed to UV light through a patterned mask and then developed, leaving the desired circuit pattern on the copper surface.
- Electrolytic copper plating: Additional copper is plated onto the exposed areas to achieve the required thickness.
- Etching: The unwanted copper is removed using a chemical etching process, leaving only the desired circuit pattern.
4. Lamination and Stacking
For multi-layer HDI PCBs, the individual layers are laminated together using heat and pressure. The layers are aligned precisely, and the microvias are filled with conductive material to create interconnections between layers.
5. Surface Finishing
The final step is to apply a surface finish to the PCB to protect the copper traces and pads from oxidation and to enhance solderability. Common surface finishes for HDI PCBs include:
- ENIG (Electroless Nickel Immersion Gold)
- ENEPIG (Electroless Nickel Electroless Palladium Immersion Gold)
- OSP (Organic Solderability Preservative)
HDI PCB Design Considerations
To achieve a perfect HDI PCB, several design considerations must be taken into account:
1. Signal Integrity
HDI PCBs often deal with high-speed signals, making signal integrity a critical factor. To maintain signal integrity:
- Use controlled impedance traces to match the impedance of the source and load.
- Minimize crosstalk by properly spacing traces and using guard traces or ground planes.
- Employ differential pair routing for high-speed signals.
2. Thermal Management
With the high density of components on HDI PCBs, thermal management becomes essential. To dissipate heat effectively:
- Use thermal vias to transfer heat from components to the opposite side of the board or to dedicated thermal layers.
- Incorporate adequate copper pour for heat spreading.
- Consider using thermally conductive materials, such as metal-Core PCBs or thermal interface materials.
3. Manufacturing Constraints
Designers must consider the capabilities and limitations of the chosen PCB manufacturer. This includes:
- Minimum via size and pitch
- Minimum trace width and spacing
- Allowed layer count and stacking options
- Available surface finishes
4. Testing and Validation
Thorough testing and validation are essential to ensure the reliability and functionality of HDI PCBs. This may involve:
- In-circuit testing (ICT) to verify the proper assembly of components.
- Flying probe testing to check for short circuits and open connections.
- Boundary scan testing (JTAG) to test the functionality of individual components and interconnections.
- X-ray inspection to verify the quality of microvias and hidden connections.
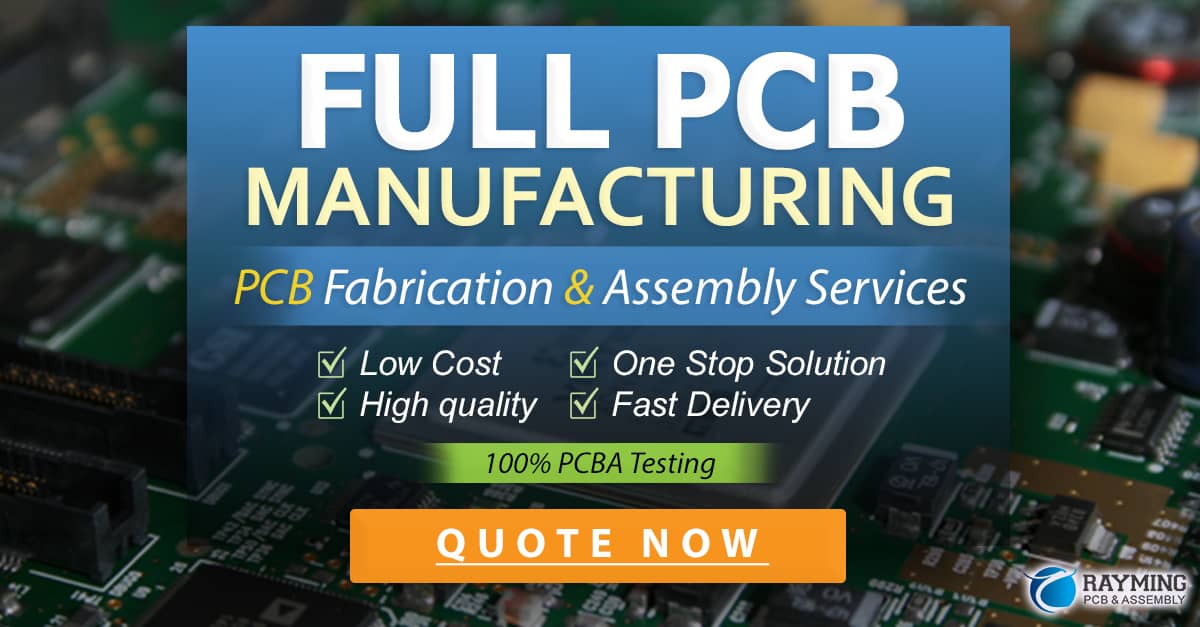
HDI PCB Applications
HDI PCBs find applications in various industries where high performance, miniaturization, and reliability are essential. Some common applications include:
- Consumer Electronics:
- Smartphones
- Tablets
- Smartwatches
-
Digital cameras
-
Medical Devices:
- Implantable devices
- Wearable health monitors
-
Diagnostic equipment
-
Automotive Electronics:
- Advanced driver assistance systems (ADAS)
- In-vehicle infotainment systems
-
Engine control units (ECUs)
-
Aerospace and Defense:
- Avionics systems
- Satellite communication devices
-
Military wearables
-
Industrial Automation:
- Robotics
- Machine vision systems
- Industrial IoT devices
FAQ
-
What is the difference between HDI PCBs and traditional PCBs?
HDI PCBs have higher wiring density, smaller vias, finer trace widths and spaces, and higher connection pad density compared to traditional PCBs. This allows for more complex designs in a smaller form factor. -
What are microvias, and why are they important in HDI PCBs?
Microvias are small holes drilled by lasers, typically with diameters less than 150μm. They enable higher density interconnections between layers in HDI PCBs, allowing for more complex routing and increased functionality in a limited space. -
What materials are commonly used for HDI PCBs?
The most common materials used for HDI PCBs are FR-4 (a glass-reinforced epoxy laminate), polyimide (a high-performance material with excellent thermal stability and flexibility), and Rogers (a low-loss, high-frequency material suitable for RF applications). -
How can designers ensure signal integrity in HDI PCBs?
To maintain signal integrity in HDI PCBs, designers should use controlled impedance traces, minimize crosstalk by properly spacing traces and using guard traces or ground planes, and employ differential pair routing for high-speed signals. -
What are some common applications of HDI PCBs?
HDI PCBs are widely used in various industries, including consumer electronics (smartphones, tablets, smartwatches), medical devices (implantable devices, wearable health monitors), automotive electronics (ADAS, infotainment systems), aerospace and defense (avionics systems, satellite communication devices), and industrial automation (robotics, machine vision systems).
Conclusion
HDI PCBs offer numerous advantages over traditional PCBs, enabling the development of highly complex and compact electronic devices. By understanding the manufacturing process, design considerations, and applications of HDI PCBs, engineers and designers can create cutting-edge products that meet the demands of today’s technology-driven world. With proper planning, execution, and testing, achieving a perfect HDI PCB is within reach, paving the way for innovative and reliable electronic solutions.
0 Comments