What is HDI PCB?
HDI PCB, or High Density Interconnector Printed Circuit Board, is a type of PCB that offers higher density interconnections than traditional PCBs. This is achieved through the use of smaller vias, finer traces, and advanced manufacturing techniques. HDI PCBs allow for more complex designs and higher component density, making them ideal for applications that require miniaturization and high performance.
Key Features of HDI PCBs
- Smaller vias (microvias) with diameters less than 150 microns
- Finer trace widths and spacings, typically less than 100 microns
- Higher layer count, often 8 or more layers
- Buried and blind vias for increased routing density
- Sequential lamination process for building up layers
Benefits of Using HDI PCBs
1. Miniaturization
One of the primary benefits of HDI PCBs is their ability to enable miniaturization. With smaller vias and finer traces, designers can pack more components into a smaller space, reducing the overall size of the PCB and the end product. This is particularly important for applications such as smartphones, wearables, and medical devices, where space is at a premium.
2. Improved Signal Integrity
HDI PCBs offer improved signal integrity compared to traditional PCBs. The shorter signal paths and reduced layer count help minimize signal loss, crosstalk, and electromagnetic interference (EMI). This is crucial for high-speed applications, such as 5G networks, where signal integrity is critical for reliable performance.
3. Higher Reliability
The advanced manufacturing techniques used in HDI PCBs, such as laser drilling and sequential lamination, result in higher reliability and durability. The smaller vias and finer traces are less susceptible to mechanical stress and thermal expansion, reducing the risk of failures and improving the overall reliability of the PCB.
4. Cost-effective for High-volume Production
While HDI PCBs may have a higher initial cost compared to traditional PCBs due to the advanced manufacturing processes involved, they can be cost-effective for high-volume production. The increased density and miniaturization enabled by HDI technology can lead to reduced material costs and smaller form factors, ultimately lowering the overall cost per unit.
Applications of HDI PCBs
HDI PCBs find applications in various industries and products, including:
- Consumer Electronics
- Smartphones
- Tablets
- Wearables
-
Smart home devices
-
Automotive Electronics
- Advanced driver assistance systems (ADAS)
- Infotainment systems
-
Electronic control units (ECUs)
-
Medical Devices
- Implantable devices
- Wearable health monitors
-
Diagnostic equipment
-
Aerospace and Defense
- Avionics
- Satellite communication systems
-
Military equipment
-
Industrial Automation
- Robotics
- Industrial IoT devices
- Process control systems
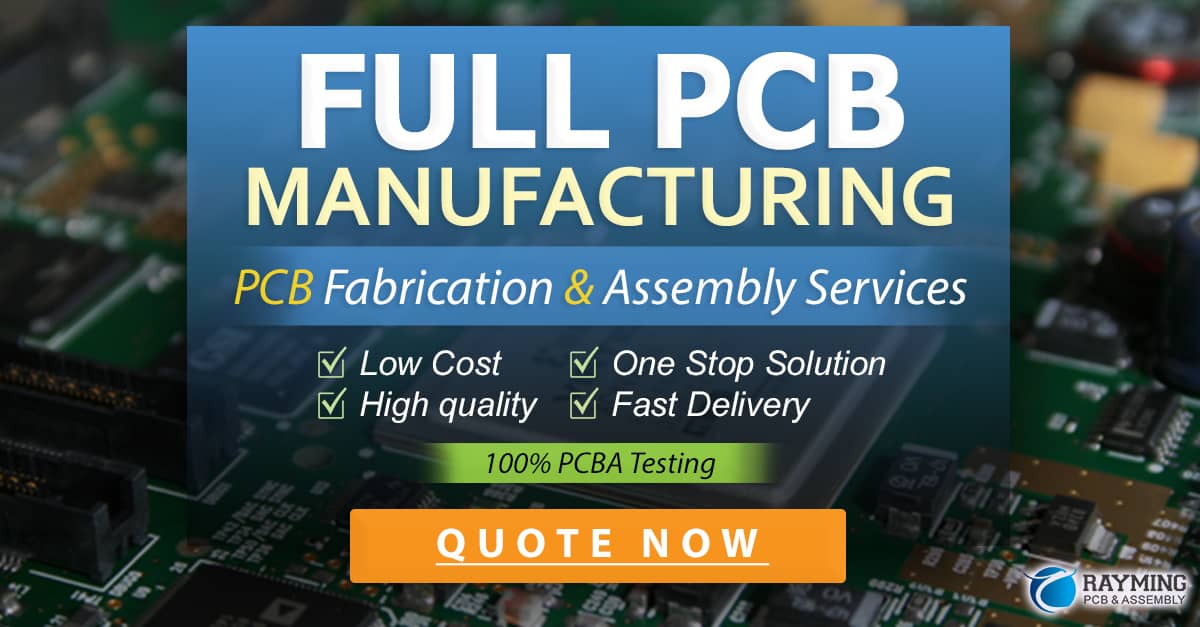
HDI PCB design considerations
When designing an HDI PCB, there are several key considerations to keep in mind:
1. Via Types and Sizes
HDI PCBs utilize different types of vias, including through-hole vias, blind vias, and buried vias. Designers must choose the appropriate via type and size based on the specific requirements of the design, such as layer count, routing density, and signal integrity.
Via Type | Description | Typical Size Range |
---|---|---|
Through-hole Via | Extends through all layers of the PCB | 200-400 microns |
Blind Via | Connects an outer layer to an inner layer | 50-150 microns |
Buried Via | Connects two or more inner layers | 50-150 microns |
2. Trace Width and Spacing
To achieve higher density and improved signal integrity, HDI PCBs use finer trace widths and spacings compared to traditional PCBs. Designers must adhere to the minimum trace width and spacing requirements specified by the PCB manufacturer and consider factors such as signal speed, impedance control, and current carrying capacity.
3. Layer Stack-up
The layer stack-up of an HDI PCB is critical for achieving the desired electrical performance and manufacturability. Designers must carefully plan the layer stack-up, considering factors such as signal integrity, power distribution, and manufacturing constraints. The use of high-performance materials, such as low-loss dielectrics and smooth copper foils, can help optimize the layer stack-up for HDI designs.
4. Design for Manufacturing (DFM)
To ensure the manufacturability and reliability of HDI PCBs, designers must follow DFM guidelines. This includes adhering to minimum feature sizes, maintaining appropriate clearances, and using standard via and pad sizes. Collaborating with the PCB manufacturer early in the design process can help identify and address any potential manufacturability issues.
HDI PCB Manufacturing Process
The manufacturing process for HDI PCBs involves several advanced techniques and processes:
-
Laser Drilling: High-precision lasers are used to drill microvias in the PCB Layers, enabling higher density interconnections.
-
Sequential Lamination: HDI PCBs are built up in a sequential lamination process, where each layer is laminated and drilled separately before being combined into the final stack-up.
-
Plasma Etching: Plasma etching is used to remove the resin smear from the via walls, ensuring reliable electrical connections between layers.
-
Copper Filling: Microvias are filled with electroplated copper to create solid interconnections between layers.
-
Surface Finishing: Various surface finishes, such as ENIG (Electroless Nickel Immersion Gold) or ENEPIG (Electroless Nickel Electroless Palladium Immersion Gold), are applied to the PCB to protect the exposed copper and enhance solderability.
Choosing the Right HDI PCB Manufacturer
When selecting an HDI PCB manufacturer, consider the following factors:
-
Technical Capabilities: Ensure the manufacturer has the necessary equipment and expertise to produce HDI PCBs with the required features and specifications.
-
Quality Standards: Look for manufacturers with strict quality control processes and certifications, such as ISO 9001, IATF 16949, or AS9100.
-
Experience and Reputation: Choose a manufacturer with a proven track record of successfully delivering HDI PCBs for applications similar to yours.
-
Customer Support: Work with a manufacturer that offers excellent customer support, including design assistance, technical support, and responsive communication.
-
Cost and Lead Time: Consider the manufacturer’s pricing and lead times to ensure they align with your budget and project timeline.
Frequently Asked Questions (FAQ)
- What is the minimum via size achievable with HDI PCBs?
-
HDI PCBs can achieve via sizes as small as 50 microns, depending on the specific manufacturing capabilities of the PCB manufacturer.
-
Can HDI PCBs be used for high-power applications?
-
Yes, HDI PCBs can be designed for high-power applications by using thicker copper layers, appropriate trace widths, and efficient thermal management techniques.
-
Are HDI PCBs more expensive than traditional PCBs?
-
HDI PCBs generally have a higher cost per unit compared to traditional PCBs due to the advanced manufacturing processes involved. However, they can be cost-effective for high-volume production and can lead to overall cost savings through miniaturization and improved performance.
-
What is the typical turnaround time for HDI PCB manufacturing?
-
The turnaround time for HDI PCB manufacturing varies depending on the complexity of the design, the manufacturer’s capacity, and the required quantities. Typical lead times range from 2-4 weeks, but expedited services may be available for urgent projects.
-
Can HDI PCBs be used for flexible or rigid-flex applications?
- Yes, HDI technology can be applied to both flexible and rigid-Flex PCBs, enabling high-density interconnections and advanced packaging solutions for a wide range of applications.
Conclusion
HDI PCBs offer numerous benefits, including miniaturization, improved signal integrity, higher reliability, and cost-effectiveness for high-volume production. They are well-suited for applications that require high density, high performance, and compact form factors, such as consumer electronics, automotive systems, medical devices, and aerospace equipment.
When designing HDI PCBs, it is essential to consider factors such as via types and sizes, trace widths and spacings, layer stack-up, and DFM guidelines. Collaborating with an experienced HDI PCB manufacturer that offers the necessary technical capabilities, quality standards, and customer support can help ensure the success of your project.
As technology continues to advance and the demand for smaller, more powerful electronic devices grows, HDI PCBs will play an increasingly important role in enabling the next generation of innovative products and solutions.
0 Comments