What is HDI PCB?
HDI stands for High Density Interconnector. HDI PCB refers to a printed circuit board with a higher density of electrical connections per unit area compared to conventional PCBs. This increased density is achieved through finer circuit traces, smaller vias, and higher connection pad density.
HDI PCBs enable the miniaturization of electronic devices by packing more functionality into smaller form factors. They are widely used in smartphones, tablets, laptops, wearables, medical devices and other advanced electronics that demand compact designs with high performance and reliability.
Advantages of HDI PCB
There are several key advantages of using HDI PCBs in electronic product designs:
1. Miniaturization
The main advantage of HDI PCB is that it enables significant miniaturization of electronic devices. By using finer traces, smaller vias, and higher component density, HDI PCBs can fit more functionality into a smaller PCB area compared to traditional PCBs. This is critical for compact consumer devices like smartphones that need to pack a lot of features and performance into slim, pocketable form factors.
2. Improved Signal Integrity
HDI PCBs can improve signal integrity in high-speed designs. The shorter, finer traces enabled by HDI reduce signal reflections and EMI/RFI issues. Smaller, laser-drilled microvias provide more direct routing between layers, minimizing signal path lengths. Blind and buried vias remove the need for traces to route around vias on the outer layers. All of this contributes to cleaner signals with less noise and distortion.
3. Lower Power Consumption
By virtue of their higher density, HDI PCBs have shorter signal paths. This reduces overall track resistance and capacitance, which in turn lowers power consumption. Lower power consumption means longer battery life for portable devices and reduced cooling requirements.
4. Increased Reliability
HDI PCBs can offer higher reliability than conventional PCBs. The use of microvias reduces the number of drilled through-holes, which are a common point of failure. Blind and buried vias are less susceptible to contamination and stress than through-hole vias. The higher density also leaves less exposed copper that could potentially cause short circuits.
5. Cost Reduction
Although HDI PCBs have a higher cost per unit area than conventional PCBs, they can reduce overall system costs in several ways. By fitting more functionality into a smaller PCB area, HDI can reduce the number of PCB Layers needed, simplifying assembly. HDI also enables the use of smaller, lower-cost components. Miniaturization reduces packaging and shipping costs too.
HDI PCB Design Considerations
Designing HDI PCBs involves different considerations than traditional PCBs. Here are some key factors to keep in mind:
1. Material Selection
The choice of base material is critical for HDI PCBs. The material must be able to withstand the high temperatures and harsh chemicals used in HDI manufacturing processes like sequential lamination cycles. It should have a low CTE (coefficient of thermal expansion) to avoid via failures under thermal stress. Popular HDI material choices include:
- FR-4: Standard PCB material, usable for HDI but with limitations
- High-Tg FR-4: FR-4 with higher glass transition temp, better for HDI
- Polyimide: Excellent thermal resistance but more expensive
- Teflon: Low loss for high frequency but limited availability and high cost
2. Layer Stack-up
Defining the optimal layer stack-up is crucial for HDI designs. The stack-up must provide a sufficient number of signal and plane layers while accommodating the desired via structure and impedance requirements. Factors to consider include:
- Number of layers (typically 8 to 24 for HDI)
- Layer assignment (signal, power, ground)
- Dielectric material and thickness
- Copper weight and finished thickness
- Drill spans and via structure
Here is an example 8-layer HDI stack-up:
Layer | Type | Material | Thickness (um) |
---|---|---|---|
1 | Signal | HR FR-4 | 50 |
2 | Ground | HR FR-4 | 50 |
3 | Signal | HR FR-4 | 100 |
4 | Signal | HR FR-4 | 100 |
5 | Power | HR FR-4 | 100 |
6 | Signal | HR FR-4 | 100 |
7 | Signal | HR FR-4 | 50 |
8 | Signal | HR FR-4 | 50 |
3. Via Types and Structures
One of the key features of HDI PCBs is the use of microvias, which are vias with diameters of 0.15mm or less. Microvias can be laser-drilled to form blind, buried, or stacked structures. The via type and structure used depends on the routing requirements and manufacturing capabilities. Common HDI via types include:
- Through vias: Drilled through the entire board, used for layer transitions
- Blind vias: Connect an outer layer to an inner layer, laser-drilled
- Buried vias: Connect two or more inner layers, laser-drilled
- Stacked vias: Two or more vias stacked to span multiple layers
- Staggered vias: Partial stacks with an offset to span multiple layers
The via aspect ratio (depth:diameter) is an important consideration. Most HDI PCB Fabricators have an aspect ratio limit of 0.8:1 for laser-drilled microvias.
4. Trace Width and Spacing
HDI PCBs use finer trace widths and spacings than traditional PCBs. This enables higher routing density but also introduces new constraints. The minimum trace width and spacing depends on the PCB fabricator’s capabilities. Typical minimum trace/space for HDI is 3/3 mils (75/75 um), although some advanced fabricators can go as low as 2/2 mils (50/50 um).
Finer traces have higher resistance and are more susceptible to impedance variations and manufacturing defects. It’s important to work closely with the PCB fabricator to ensure the design is within their manufacturing tolerances.
5. Component Selection and Placement
HDI PCBs typically use smaller components to take full advantage of the increased density. Popular component packages for HDI include:
- Chip Scale Packages (CSPs)
- Ball Grid Arrays (BGAs)
- Quad Flat No-Leads (QFNs)
These packages have fine pin pitches (0.4mm, 0.5mm, 0.8mm) that are well-suited for the finer traces of HDI PCBs. However, they also require careful placement and routing to ensure manufacturability.
Key considerations for HDI component placement include:
- Placement clearances for automated assembly
- Thermal management and heat spreading
- Signal integrity and EMI/RFI avoidance
- Design for test (DFT) and in-circuit test (ICT) accessibility
6. Design Rule Checking (DRC)
Thorough design rule checking is critical for HDI PCBs to ensure manufacturability and reliability. The DRC checks should be based on the specific capabilities of the chosen PCB fabricator and assembler. Key DRC checks for HDI include:
- Trace width and spacing
- Via size and spacing
- Annular ring size
- Copper-to-edge clearance
- Solder mask alignment
- Silk screen legibility
It’s important to involve the PCB fabricator early in the design process to ensure the design is within their capabilities and to resolve any DRC issues.
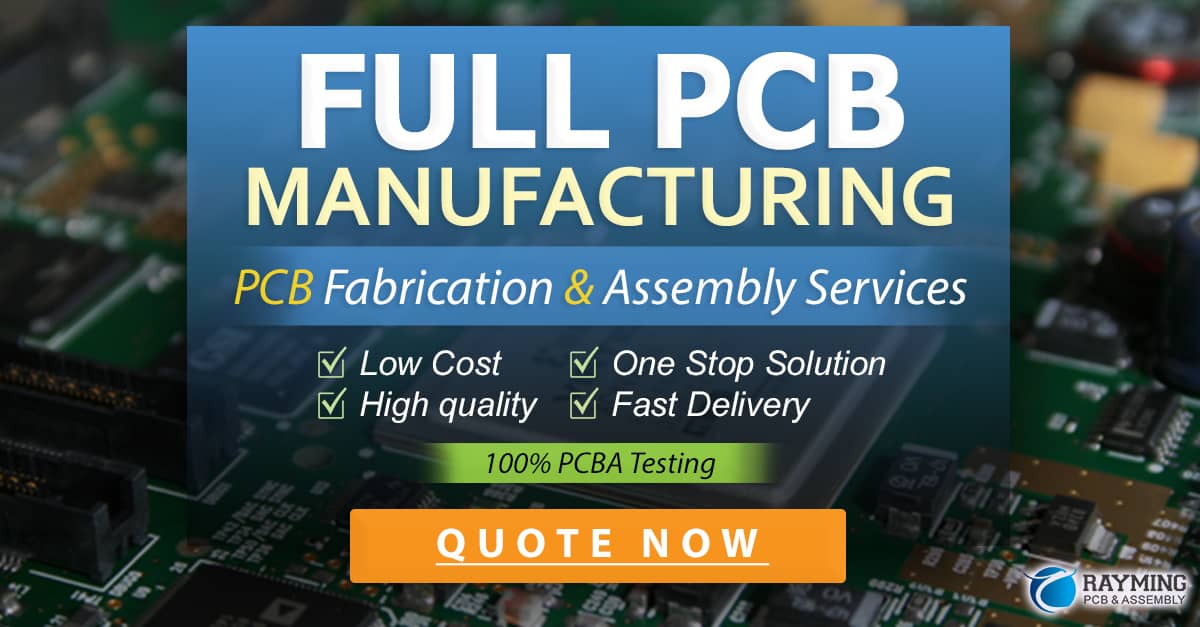
HDI PCB Manufacturing Process
The manufacturing process for HDI PCBs is more complex than for traditional PCBs due to the use of microvias and sequential lamination. Here is a simplified overview of the HDI PCB manufacturing process:
-
Inner layer processing: The inner layers are patterned using standard photolithography and etching processes.
-
Lamination: The inner layers are laminated together with prepreg and copper foil to form the initial multilayer structure.
-
Drilling: Mechanical through-holes and blind vias are drilled.
-
Desmear: The drilled holes are cleaned and roughened to improve copper adhesion.
-
Metallization: Copper is deposited onto the holes and surface using electroless and electrolytic plating.
-
Outer layer processing: The outer layers are patterned using photolithography and etching.
-
Solder mask application: Liquid photoimageable (LPI) solder mask is applied and patterned to protect the copper traces.
-
Surface finish application: The exposed pads are coated with a surface finish (ENIG, OSP, HASL, etc.) to prevent oxidation and improve solderability.
-
Electrical test: The finished PCB is electrically tested for opens and shorts using flying probe or Bed-of-Nails Testers.
For HDI PCBs with sequential lamination, steps 2-6 are repeated for each additional lamination cycle. This allows for the creation of complex via structures and higher layer counts.
FAQ
1. What is the difference between HDI PCB and regular PCB?
The main difference is the density of electrical connections. HDI PCBs have finer traces, smaller vias, and higher connection pad density compared to regular PCBs. This allows HDI PCBs to pack more functionality into a smaller area.
2. What are the advantages of HDI PCB?
The advantages of HDI PCB include:
– Miniaturization of electronic devices
– Improved signal integrity
– Lower power consumption
– Increased reliability
– Cost reduction at the system level
3. What are microvias in HDI PCB?
Microvias are small vias with diameters of 0.15mm or less used in HDI PCBs. They can be laser-drilled to form blind, buried, or stacked via structures. Microvias enable higher routing density and more direct connections between layers.
4. What materials are used for HDI PCB?
Common materials for HDI PCB include:
– High-Tg FR-4: High glass transition temp variant of standard FR-4
– Polyimide: Offers excellent thermal resistance
– Teflon: Has low loss for high frequency applications
The material must withstand the high temperatures and chemicals used in HDI manufacturing processes.
5. What is sequential lamination in HDI PCB?
Sequential lamination is a process used to fabricate HDI PCBs with complex via structures and high layer counts. It involves repeating the lamination, drilling, and plating steps for each additional layer. This allows for the creation of blind, buried, and Stacked Microvias that span multiple layers.
0 Comments