Introduction to HDI PCB Technology
High-Density Interconnect (HDI) PCB technology has revolutionized the electronics industry by enabling the creation of smaller, lighter, and more complex printed circuit boards. HDI PCBs offer numerous advantages over traditional PCBs, including increased signal integrity, reduced signal loss, and improved thermal management. As a result, HDI PCBs are widely used in various applications, such as smartphones, tablets, wearables, and medical devices.
What is an HDI PCB?
An HDI PCB is a printed circuit board that features higher wiring density per unit area than conventional PCBs. This is achieved through the use of smaller vias, finer trace widths, and thinner dielectric layers. HDI PCBs can have multiple layers, typically ranging from 4 to 12 layers, and can incorporate advanced technologies like blind and buried vias, microvias, and sequential lamination.
Advantages of HDI PCBs
-
Miniaturization: HDI PCBs enable the creation of smaller and lighter electronic devices, which is crucial for applications where space is limited, such as smartphones and wearables.
-
Improved Signal Integrity: The shorter signal paths and reduced layer count in HDI PCBs result in improved signal integrity and reduced signal loss, ensuring reliable performance of high-speed applications.
-
Enhanced Thermal Management: HDI PCBs offer better thermal management due to the increased copper density and the use of thermal vias, which help dissipate heat more efficiently.
-
Cost-Effective: Although the initial setup costs for HDI PCBs may be higher, they offer long-term cost savings by reducing the overall size and weight of the device, simplifying assembly, and improving reliability.
HDI PCB Design Considerations
Trace Width and Spacing
One of the key aspects of HDI PCB design is the use of finer trace widths and spacing. Typical HDI PCBs feature trace widths ranging from 3 to 6 mils (0.075 to 0.15 mm) and spacing between traces of 3 to 5 mils (0.075 to 0.125 mm). These dimensions enable higher wiring density and allow for more complex routing in a smaller area.
Via Types and Sizes
HDI PCBs utilize various types of vias to interconnect different layers:
-
Through Vias: These vias extend through the entire thickness of the PCB and are typically used for power and ground connections.
-
Blind Vias: Blind vias are visible only on one side of the PCB and terminate at a specific inner layer.
-
Buried Vias: Buried vias are located entirely within the inner layers of the PCB and are not visible on either surface.
-
Microvias: Microvias are small vias with a diameter of less than 6 mils (0.15 mm) and are typically laser-drilled. They are used for high-density interconnections between layers.
The choice of via type and size depends on the specific design requirements, such as signal integrity, layer count, and manufacturing capabilities.
Layer Stack-up
The layer stack-up of an HDI PCB plays a crucial role in determining its performance and manufacturability. A typical HDI PCB stack-up consists of the following layers:
-
Signal Layers: These layers contain the traces that carry signals between components.
-
Power and Ground Layers: These layers provide a stable reference plane for the signal layers and help reduce electromagnetic interference (EMI).
-
Dielectric Layers: Dielectric layers, such as prepreg or core material, separate the conductive layers and provide insulation.
When designing the layer stack-up, it is essential to consider factors such as impedance control, signal integrity, and manufacturability. The thickness and material properties of each layer must be carefully selected to ensure optimal performance and reliability.
Component Placement and Routing
Component placement and routing are critical aspects of HDI PCB design. The high density of components and traces in HDI PCBs requires careful planning and optimization to ensure manufacturability and reliability.
When placing components, designers should consider the following:
-
Placement Density: Components should be placed as close together as possible to minimize trace lengths and reduce signal loss.
-
Thermal Management: High-power components should be placed in a way that allows for efficient heat dissipation, such as near the edge of the board or close to thermal vias.
-
Signal Integrity: Critical components, such as high-speed devices or sensitive analog circuits, should be placed in a way that minimizes crosstalk and interference.
Routing in HDI PCBs involves the use of advanced techniques, such as:
-
Controlled Impedance Routing: Traces are designed with specific widths and spacing to maintain a constant impedance throughout the signal path, minimizing reflections and signal distortion.
-
Differential Pair Routing: Differential signals are routed as a pair of traces with a specific spacing and length matching to ensure signal integrity.
-
Via Optimization: The placement and use of vias should be optimized to minimize signal degradation and improve manufacturability.
HDI PCB Fabrication Process
The fabrication process for HDI PCBs is more complex than that of traditional PCBs due to the use of advanced technologies and materials. The main steps involved in HDI PCB fabrication are:
1. Material Selection and Preparation
The first step in HDI PCB fabrication is the selection of suitable materials, such as copper-clad laminate (CCL), prepreg, and solder mask. The materials are then cut to the required size and cleaned to remove any contaminants.
2. Drilling and Plating
The next step involves drilling the vias and through holes using specialized equipment, such as laser drills or mechanical drills. After drilling, the holes are plated with copper to establish electrical connections between layers.
3. Patterning and Etching
The copper layers are then patterned using photolithography techniques. A photoresist layer is applied to the copper surface, exposed to UV light through a photomask, and developed to create the desired pattern. The exposed copper is then etched away using a chemical solution, leaving behind the desired traces and pads.
4. Lamination and Pressing
The patterned layers are then stacked and aligned according to the designed layer stack-up. The stack is then laminated and pressed under high temperature and pressure to bond the layers together.
5. Surface Finishing
After lamination, the PCB undergoes surface finishing to protect the exposed copper and improve solderability. Common surface finishes for HDI PCBs include Electroless Nickel Immersion Gold (ENIG), Immersion Silver, and Organic Solderability Preservative (OSP).
6. Inspection and Testing
The fabricated HDI PCB undergoes rigorous inspection and testing to ensure that it meets the specified quality and performance requirements. This includes visual inspection, electrical testing, and automated optical inspection (AOI).
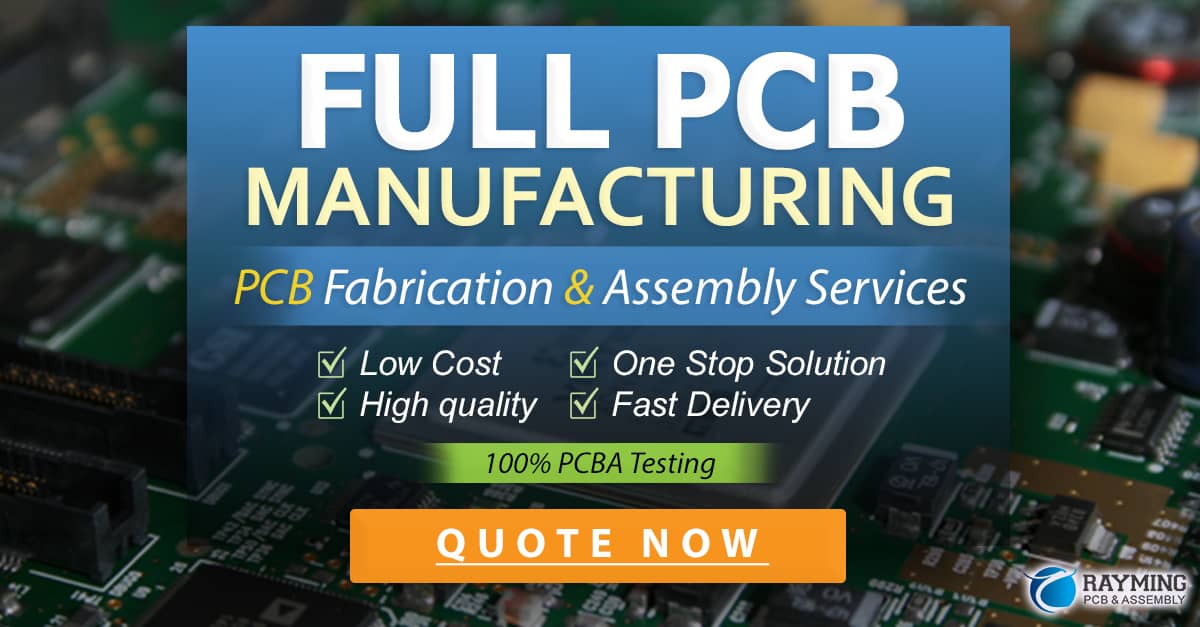
HDI PCB Assembly Techniques
The assembly of HDI PCBs requires specialized techniques and equipment due to the high component density and fine pitch sizes. The main HDI PCB assembly techniques are:
1. Surface Mount Technology (SMT)
SMT is the most common assembly technique for HDI PCBs. It involves the placement of surface mount components onto the PCB surface using automated pick-and-place machines. The components are then soldered to the pads using reflow soldering techniques.
2. Flip Chip Assembly
Flip chip assembly is used for high-density interconnections between bare die and the PCB substrate. The die is flipped and bonded directly to the PCB using solder bumps or conductive adhesives. This technique enables shorter signal paths and reduced package size compared to wire bonding.
3. Chip-on-Board (COB) Assembly
COB assembly involves the direct attachment of bare die to the PCB substrate using wire bonding or flip chip techniques. This technique is often used for high-performance applications that require minimal package size and maximum performance.
4. Package-on-Package (PoP) Assembly
PoP assembly involves the stacking of multiple packaged devices on top of each other to create a 3D package. This technique enables higher packaging density and reduced board space compared to traditional side-by-side placement.
HDI PCB Testing and Inspection
To ensure the reliability and performance of HDI PCBs, various testing and inspection techniques are employed during and after the assembly process. These include:
1. In-Circuit Testing (ICT)
ICT is a test method that verifies the proper assembly and functionality of individual components on the PCB. It involves the use of a bed-of-nails fixture that makes contact with specific test points on the PCB to measure electrical characteristics and detect faults.
2. Flying Probe Testing
Flying probe testing is an alternative to ICT that uses movable probes to make contact with test points on the PCB. This technique is more flexible and does not require a dedicated test fixture, making it suitable for low-volume production or prototype testing.
3. Boundary Scan Testing
Boundary scan testing, also known as JTAG testing, is a method that uses a built-in test architecture to test the interconnections and functionality of digital components on the PCB. This technique is particularly useful for testing complex HDI PCBs with limited physical access to test points.
4. X-ray Inspection
X-ray inspection is used to examine the internal structure of the PCB assembly, particularly for hidden features such as vias, solder joints, and component placement. This technique can detect defects such as voids, bridging, and misalignment that may not be visible through visual inspection.
Applications of HDI PCBs
HDI PCBs find applications in a wide range of industries and products, including:
-
Consumer Electronics: Smartphones, tablets, smartwatches, and other portable devices rely on HDI PCBs to achieve high functionality in a compact form factor.
-
Automotive Electronics: Advanced driver assistance systems (ADAS), infotainment systems, and engine control units (ECUs) employ HDI PCBs for reliable performance in harsh automotive environments.
-
Medical Devices: Implantable devices, diagnostic equipment, and wearable health monitors use HDI PCBs for miniaturization and high reliability.
-
Aerospace and Defense: Avionics systems, satellite communications, and military equipment require HDI PCBs for high-speed data processing and rugged performance.
-
Industrial Automation: Factory automation systems, robotics, and process control equipment use HDI PCBs for high-density interconnections and reliable operation in industrial environments.
Challenges and Future Trends in HDI PCB Technology
Despite the numerous advantages of HDI PCBs, there are several challenges and future trends that the industry must address:
1. Signal Integrity at High Frequencies
As electronic devices continue to operate at higher frequencies and data rates, maintaining signal integrity becomes increasingly challenging. HDI PCB designers must employ advanced techniques such as adaptive routing, impedance matching, and signal conditioning to ensure reliable performance at high frequencies.
2. Thermal Management
The high component density in HDI PCBs can lead to increased heat generation and thermal management challenges. Future HDI PCB designs must incorporate advanced thermal management solutions, such as embedded heat spreaders, thermal vias, and advanced materials with high thermal conductivity.
3. Miniaturization and 3D Packaging
The demand for smaller and more compact electronic devices will drive further miniaturization of HDI PCBs. This will require the development of advanced packaging technologies, such as 3D packaging, embedded components, and wafer-level packaging, to achieve higher density and performance.
4. Sustainable and Eco-Friendly Materials
As environmental concerns continue to grow, the electronics industry is under pressure to adopt sustainable and eco-friendly materials for PCB fabrication. This includes the use of halogen-free and lead-free materials, as well as the development of recyclable and Biodegradable PCB substrates.
Frequently Asked Questions (FAQ)
1. What is the difference between HDI PCBs and traditional PCBs?
HDI PCBs feature higher wiring density per unit area compared to traditional PCBs. They use smaller vias, finer trace widths, and thinner dielectric layers to achieve higher interconnect density and performance.
2. What are the advantages of using HDI PCBs in electronic devices?
HDI PCBs offer several advantages, including miniaturization, improved signal integrity, enhanced thermal management, and cost-effectiveness. They enable the creation of smaller, lighter, and more complex electronic devices with reliable performance.
3. What are the different types of vias used in HDI PCBs?
HDI PCBs use various types of vias, including through vias, blind vias, buried vias, and microvias. Each type of via serves a specific purpose in interconnecting different layers of the PCB.
4. What are the main assembly techniques used for HDI PCBs?
The main assembly techniques for HDI PCBs include Surface Mount Technology (SMT), Flip Chip Assembly, Chip-on-Board (COB) Assembly, and Package-on-Package (PoP) Assembly. These techniques enable high-density interconnections and miniaturization of electronic packages.
5. What are the future trends in HDI PCB technology?
Future trends in HDI PCB technology include addressing challenges in signal integrity at high frequencies, advanced thermal management solutions, further miniaturization and 3D packaging, and the adoption of sustainable and eco-friendly materials for PCB fabrication.
Conclusion
HDI PCB technology has revolutionized the electronics industry by enabling the creation of smaller, lighter, and more complex electronic devices. The use of finer trace widths, smaller vias, and advanced packaging techniques has allowed for higher interconnect density and improved performance in a wide range of applications, from consumer electronics to aerospace and defense.
However, the industry must continue to address challenges such as signal integrity, thermal management, and miniaturization to keep pace with the ever-increasing demands for high-performance electronic devices. The adoption of sustainable and eco-friendly materials will also play a crucial role in the future development of HDI PCB technology.
As HDI PCBs continue to evolve and advance, they will undoubtedly shape the future of the electronics industry, enabling the creation of innovative and revolutionary products that enhance our daily lives.
0 Comments