Introduction
Printed circuit board (PCB) assembly is a crucial process in electronics manufacturing that involves soldering electronic components onto a printed circuit board to create a functional electronic device. Efficient PCB Assembly is essential for successful prototyping and mass production of electronic products. In this article, we will discuss the key steps involved in PCB assembly and provide tips for optimizing the process for efficiency and quality.
Understanding PCB Assembly
PCB assembly is the process of populating a bare printed circuit board with electronic components to create a functional electronic device. The process involves several steps, including:
- Solder paste application
- Component placement
- Reflow soldering
- Inspection and testing
Each step plays a critical role in ensuring the quality and reliability of the final product. Let’s take a closer look at each step.
Solder Paste Application
Solder paste is a mixture of tiny solder balls suspended in flux. It is applied to the PCB pads where components will be placed. The most common method of solder paste application is stencil printing. A stencil is a thin metal sheet with openings that match the PCB pads. The stencil is placed over the PCB, and solder paste is spread across the stencil using a squeegee. The solder paste is deposited onto the pads through the openings in the stencil.
Factors that affect the quality of solder paste application include:
- Stencil thickness
- Aperture size and shape
- Solder paste viscosity
- Printing parameters (speed, pressure, separation distance)
Factor | Recommended Value |
---|---|
Stencil thickness | 0.1 – 0.15 mm |
Aperture size | 1:1 with pad size |
Solder paste viscosity | 800 – 1000 kcps |
Print speed | 20 – 50 mm/s |
Pressure | 0.2 – 0.4 kg/cm^2 |
Separation distance | 0.5 – 1.0 mm |
Component Placement
After solder paste application, the next step is to place the components onto the PCB. This can be done manually or using an automated pick-and-place machine. Manual placement is suitable for low-volume prototyping, while automated placement is necessary for high-volume production.
Factors that affect the accuracy of component placement include:
- Component size and shape
- PCB pad design
- Placement machine accuracy
- Operator skill (for manual placement)
Factor | Recommended Value |
---|---|
Placement accuracy | ± 0.05 mm |
Component size range | 0201 – 55 mm × 55 mm |
PCB pad size | 1:1 with component |
Placement speed (CPH) | 5,000 – 200,000 |
Reflow Soldering
After component placement, the PCB goes through a reflow soldering process to permanently attach the components to the board. Reflow soldering involves heating the PCB and components in a controlled manner to melt the solder paste and form a strong bond between the components and PCB pads.
The reflow soldering process typically follows a temperature profile that includes four stages:
- Preheat: The PCB is gradually heated to activate the flux and remove moisture.
- Soak: The temperature is maintained to allow the components to reach thermal equilibrium.
- Reflow: The temperature is increased above the melting point of the solder to allow the solder to melt and form a bond.
- Cooling: The PCB is cooled to solidify the solder joints.
Stage | Temperature Range | Time |
---|---|---|
Preheat | 150 – 180°C | 60 – 120 s |
Soak | 180 – 200°C | 60 – 120 s |
Reflow | 220 – 250°C | 60 – 90 s |
Cooling | < 100°C | 60 – 120 s |
Inspection and Testing
After reflow soldering, the PCB undergoes inspection and testing to ensure that all components are properly soldered and functioning as expected. Inspection can be done visually or using automated optical inspection (AOI) machines. Testing can include functional testing, in-circuit testing (ICT), and boundary scan testing.
Factors that affect the quality of inspection and testing include:
- Solder joint quality
- Component placement accuracy
- Test coverage and accuracy
- Operator skill (for manual inspection)
Factor | Recommended Value |
---|---|
Solder joint quality | IPC-A-610 Class 2 |
AOI defect detection | > 95% |
ICT test coverage | > 90% |
Boundary scan coverage | > 80% |
Tips for Efficient PCB Assembly
Design for Manufacturing (DFM)
One of the most important aspects of efficient PCB assembly is designing the PCB with manufacturing in mind. This is known as Design for Manufacturing (DFM). DFM involves following certain guidelines and best practices to ensure that the PCB can be manufactured easily and reliably.
Some key DFM guidelines include:
- Choosing appropriate component packages and sizes
- Providing adequate spacing between components
- Avoiding sharp angles and small features in the PCB layout
- Using standard sizes and shapes for PCB panels
- Including fiducial marks and tooling holes for alignment and registration
By following DFM guidelines, you can reduce the risk of manufacturing defects and improve the efficiency of the assembly process.
Process Optimization
Another key aspect of efficient PCB assembly is optimizing the assembly process itself. This involves analyzing each step of the process and identifying areas for improvement.
Some ways to optimize the assembly process include:
- Using automated equipment for solder paste application and component placement
- Optimizing the reflow soldering profile for the specific PCB and components
- Implementing statistical process control (SPC) to monitor and control key process parameters
- Using lean manufacturing principles to eliminate waste and improve flow
- Providing training and resources for operators to improve their skills and knowledge
By continuously optimizing the assembly process, you can improve throughput, reduce defects, and lower costs.
Supply Chain Management
Efficient PCB assembly also requires effective management of the supply chain. This involves ensuring that all necessary components and materials are available when needed and that they meet the required quality standards.
Some tips for effective supply chain management include:
- Establishing long-term relationships with reliable suppliers
- Implementing a robust quality management system (QMS) to ensure consistent quality of incoming materials
- Using inventory management software to track stock levels and forecast demand
- Negotiating favorable terms and pricing with suppliers
- Regularly auditing suppliers to ensure compliance with quality and delivery requirements
By managing the supply chain effectively, you can reduce the risk of delays and quality issues that can impact the efficiency of the assembly process.
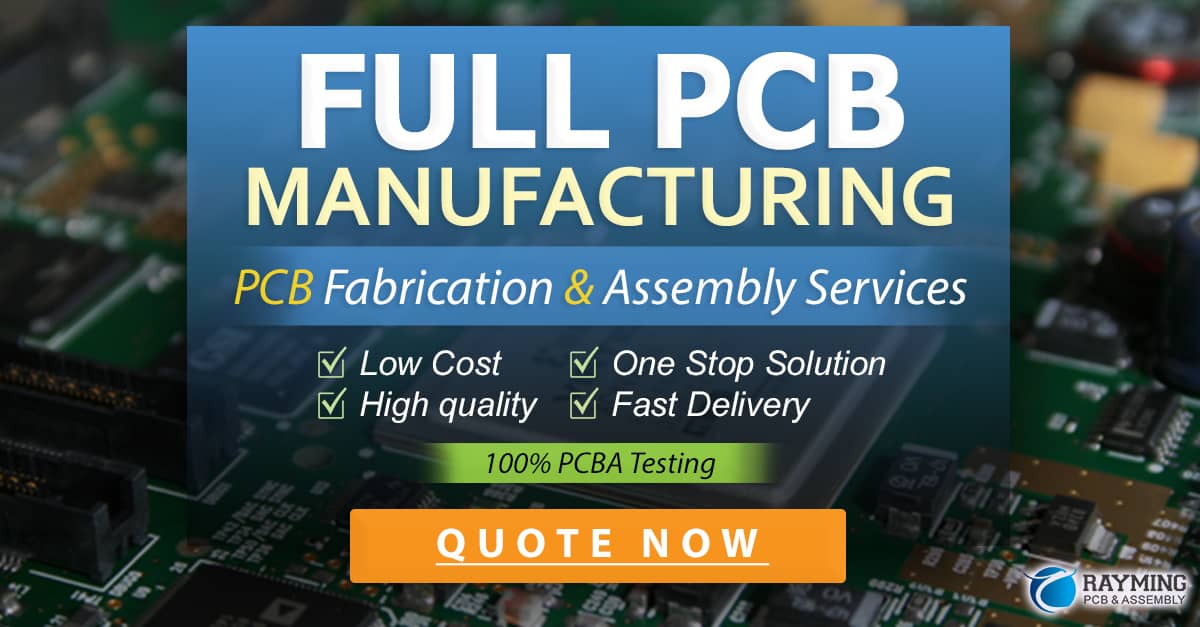
FAQ
What is the difference between wave soldering and reflow soldering?
Wave soldering is a process where the PCB is passed over a wave of molten solder to attach through-hole components. Reflow soldering, on the other hand, is used for surface mount components and involves applying solder paste to the PCB pads, placing the components, and then heating the PCB to melt the solder and form a bond.
What is the purpose of a stencil in solder paste application?
A stencil is a thin metal sheet with openings that match the PCB pads. It is used to apply solder paste to the pads in a controlled and consistent manner. The stencil is placed over the PCB, and solder paste is spread across the stencil using a squeegee. The solder paste is deposited onto the pads through the openings in the stencil.
What is the difference between AOI and ICT?
AOI (Automated Optical Inspection) is a process where a machine uses cameras and image processing software to inspect the PCB for defects such as missing components, incorrect polarity, and solder bridges. ICT (In-Circuit Testing) is a process where the PCB is tested for functionality by applying electrical signals to the board and measuring the response. ICT can detect defects such as short circuits, open circuits, and incorrect component values.
What is the purpose of fiducial marks on a PCB?
Fiducial marks are small, precise features on a PCB that are used for alignment and registration during the assembly process. They are typically circular or crosshair-shaped and are located in the corners or edges of the PCB. Fiducial marks are used by automated equipment such as pick-and-place machines and inspection systems to accurately locate and align the PCB.
What is the difference between Class 2 and Class 3 solder joints?
IPC-A-610 is a standard that defines the acceptability criteria for solder joints. Class 2 and Class 3 are two different levels of acceptability. Class 2 is the most common and is suitable for most commercial and industrial applications. It allows for some minor defects such as small voids and slightly uneven solder fillets. Class 3 is a higher level of acceptability and is typically used for high-reliability applications such as aerospace and medical devices. It requires near-perfect solder joints with no visible defects.
Conclusion
PCB assembly is a complex process that requires careful planning, execution, and optimization to achieve efficient and reliable results. By understanding the key steps involved in PCB assembly, following best practices for design and manufacturing, and continuously optimizing the process, you can improve the quality and efficiency of your PCB Prototyping and production. Whether you are a startup or an established manufacturer, investing in PCB assembly excellence is essential for success in today’s competitive electronics industry.
0 Comments