Introduction to FR PCBs
Printed Circuit Boards (PCBs) are essential components in modern electronic devices. They provide a platform for mounting and connecting electronic components, allowing for efficient and reliable operation. Among the various types of PCBs available, FR (Flame Retardant) PCBs are widely used due to their excellent fire resistance properties. In this article, we will focus on FR1 PCB and how it differs from FR2, FR3, and FR4 PCBs.
What is FR1 PCB?
FR1 PCB is a type of printed circuit board that is made from a flame-retardant material, typically a paper-based laminate. The “FR” in FR1 stands for “Flame Retardant,” indicating its ability to resist the spread of fire. FR1 PCBs are known for their low cost and ease of fabrication, making them a popular choice for simple, low-frequency applications.
Composition of FR1 PCB
FR1 PCBs are composed of a paper-based substrate that is impregnated with a flame-retardant resin, usually phenolic resin. The paper substrate provides the necessary insulation and mechanical support, while the phenolic resin enhances the board’s fire resistance properties. The conductive layers in FR1 PCBs are typically made of copper, which is laminated onto the substrate using heat and pressure.
Applications of FR1 PCB
FR1 PCBs are commonly used in various low-end electronic applications, such as:
- Consumer electronics (e.g., toys, calculators)
- Low-power electronic devices
- Single-sided PCBs for simple circuits
- Prototyping and hobbyist projects
Due to their limited thermal and electrical properties, FR1 PCBs are not suitable for high-frequency or high-power applications.
FR2 PCB: An Overview
FR2 PCB is another type of flame-retardant PCB that shares some similarities with FR1 PCB. Like FR1, FR2 PCBs are made from a paper-based substrate impregnated with a flame-retardant resin. However, FR2 PCBs use a different type of resin, typically a phenolic-paper resin, which offers slightly better thermal and electrical properties compared to FR1.
Composition of FR2 PCB
FR2 PCBs are composed of a paper-based substrate that is impregnated with a phenolic-paper resin. This resin provides better thermal stability and electrical insulation compared to the phenolic resin used in FR1 PCBs. The conductive layers in FR2 PCBs are also made of copper, which is laminated onto the substrate.
Applications of FR2 PCB
FR2 PCBs find applications in similar areas as FR1 PCBs, but they can handle slightly higher temperatures and electrical requirements. Some common applications of FR2 PCBs include:
- Low-power electronic devices
- Simple Multi-layer PCBs
- Consumer electronics
- Automotive electronics (low-end)
While FR2 PCBs offer some improvements over FR1 PCBs, they still have limitations in terms of thermal and electrical performance, making them unsuitable for high-frequency or high-power applications.
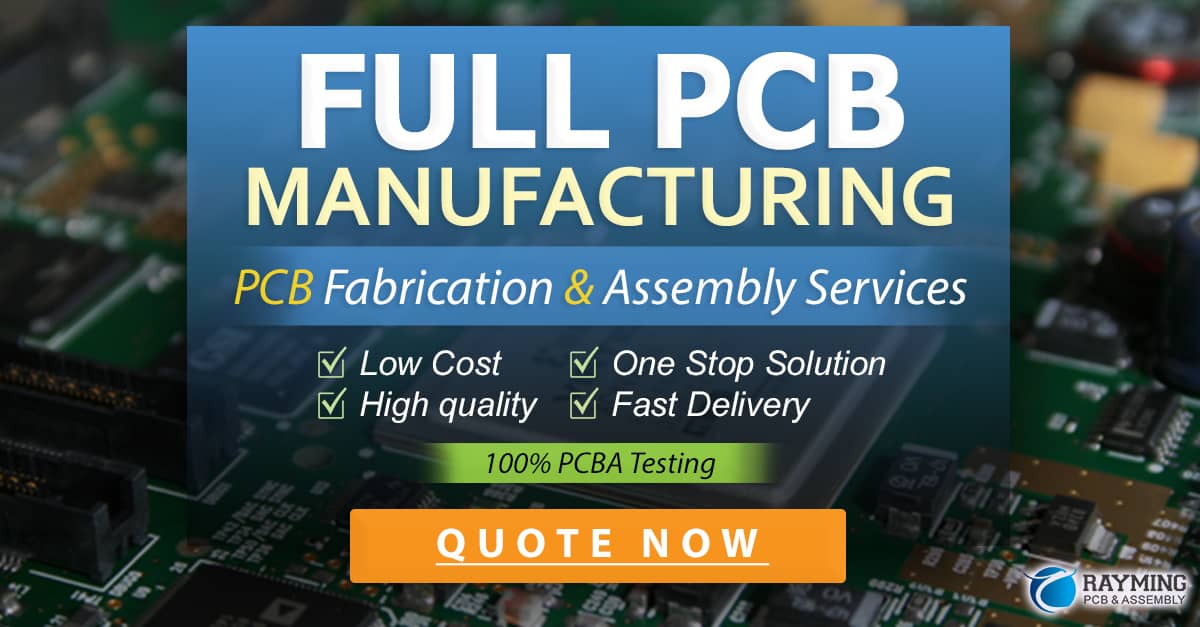
FR3 PCB: An Overview
FR3 PCB is a less common type of flame-retardant PCB that sits between FR2 and FR4 in terms of performance. FR3 PCBs are made from a composite substrate that combines paper and epoxy resin, offering better thermal and electrical properties compared to FR1 and FR2 PCBs.
Composition of FR3 PCB
FR3 PCBs are composed of a composite substrate made from paper and epoxy resin. The epoxy resin provides better thermal stability and electrical insulation compared to the phenolic resins used in FR1 and FR2 PCBs. The conductive layers in FR3 PCBs are typically made of copper, which is laminated onto the substrate.
Applications of FR3 PCB
FR3 PCBs find applications in areas that require better thermal and electrical performance than FR1 and FR2 PCBs, but do not necessitate the high-performance characteristics of FR4 PCBs. Some common applications of FR3 PCBs include:
- Automotive electronics (mid-range)
- Industrial control systems
- Telecommunications equipment
- Medical devices (low-end)
FR3 PCBs offer a balance between cost and performance, making them suitable for applications that require moderate thermal and electrical properties.
FR4 PCB: The High-Performance Option
FR4 PCB is the most widely used type of flame-retardant PCB, known for its excellent thermal, mechanical, and electrical properties. FR4 PCBs are made from a glass-reinforced epoxy laminate, which provides superior performance compared to FR1, FR2, and FR3 PCBs.
Composition of FR4 PCB
FR4 PCBs are composed of a glass-reinforced epoxy laminate substrate. The glass fibers embedded in the epoxy resin provide excellent mechanical strength and dimensional stability, while the epoxy resin offers superior thermal and electrical insulation properties. The conductive layers in FR4 PCBs are made of copper, which is laminated onto the substrate using heat and pressure.
Applications of FR4 PCB
FR4 PCBs are widely used in a variety of high-performance electronic applications, such as:
- Telecommunications equipment
- Aerospace and defense systems
- Medical devices (high-end)
- Industrial control systems
- High-frequency circuits
- Multilayer PCBs
FR4 PCBs are the preferred choice for applications that demand high reliability, thermal stability, and excellent electrical performance.
Comparison of FR1, FR2, FR3, and FR4 PCBs
To better understand the differences between FR1, FR2, FR3, and FR4 PCBs, let’s compare their key properties and characteristics:
Property | FR1 | FR2 | FR3 | FR4 |
---|---|---|---|---|
Substrate Material | Paper-based | Paper-based | Paper-Epoxy Composite | Glass-Reinforced Epoxy |
Flame Retardant Resin | Phenolic | Phenolic-Paper | Epoxy | Epoxy |
Thermal Stability | Low | Low to Moderate | Moderate | High |
Electrical Insulation | Low | Low to Moderate | Moderate | High |
Mechanical Strength | Low | Low to Moderate | Moderate | High |
Frequency Range | Low | Low to Moderate | Moderate | High |
Cost | Low | Low to Moderate | Moderate | High |
As evident from the table, FR4 PCBs offer the best overall performance, followed by FR3, FR2, and FR1 PCBs. The choice of PCB material depends on the specific requirements of the application, such as thermal stability, electrical insulation, mechanical strength, and cost constraints.
Frequently Asked Questions (FAQ)
-
Q: Can FR1 PCBs be used for high-frequency applications?
A: No, FR1 PCBs are not suitable for high-frequency applications due to their limited thermal and electrical properties. For high-frequency applications, FR4 PCBs are the preferred choice. -
Q: What is the main difference between FR2 and FR3 PCBs?
A: The main difference between FR2 and FR3 PCBs lies in their substrate composition. FR2 PCBs use a paper-based substrate impregnated with a phenolic-paper resin, while FR3 PCBs use a composite substrate made from paper and epoxy resin, offering better thermal and electrical properties. -
Q: Are FR4 PCBs more expensive than other FR PCBs?
A: Yes, FR4 PCBs are generally more expensive than FR1, FR2, and FR3 PCBs due to their superior performance and the use of high-quality materials, such as glass-reinforced epoxy laminates. -
Q: Can FR3 PCBs be used for multilayer designs?
A: Yes, FR3 PCBs can be used for multilayer designs, although they may not offer the same level of performance and reliability as FR4 PCBs in complex, high-layer count designs. -
Q: Are FR1 PCBs suitable for prototyping?
A: Yes, FR1 PCBs are often used for prototyping and hobbyist projects due to their low cost and ease of fabrication. However, for more advanced prototypes or final products, higher-grade PCBs like FR3 or FR4 may be more appropriate.
Conclusion
In conclusion, FR1 PCBs are a low-cost, flame-retardant option suitable for simple, low-frequency applications. They differ from FR2, FR3, and FR4 PCBs in terms of their substrate composition, thermal stability, electrical insulation, and mechanical strength. FR2 PCBs offer slightly better performance than FR1, while FR3 PCBs provide a balance between cost and performance. FR4 PCBs, on the other hand, are the high-performance choice, offering excellent thermal, mechanical, and electrical properties, making them suitable for a wide range of demanding applications.
When selecting the appropriate FR PCB for a specific application, it is essential to consider factors such as the required thermal stability, electrical insulation, mechanical strength, frequency range, and cost constraints. By understanding the differences between FR1, FR2, FR3, and FR4 PCBs, engineers and designers can make informed decisions and choose the most suitable PCB material for their projects.
0 Comments