Introduction to Flexible PCBs
Flexible printed circuit boards (PCBs) have revolutionized the electronics industry by providing a versatile and reliable solution for connecting electronic components in a wide range of applications. Unlike traditional Rigid PCBs, Flexible PCBs are made from thin, flexible materials that allow them to bend and conform to various shapes and sizes. This unique characteristic has made flexible PCBs increasingly popular in modern electronic devices, from consumer electronics to medical equipment and aerospace technology.
In this comprehensive article, we will delve into the world of flexible PCBs, exploring their advantages and disadvantages, manufacturing processes, applications, and future trends. By the end of this article, you will have a thorough understanding of flexible PCBs and their significance in the electronics industry.
What are Flexible PCBs?
Flexible PCBs, also known as flex circuits or Flex PCBs, are printed circuit boards made from flexible materials, such as polyimide or polyester. These materials allow the PCB to bend and flex without damaging the electrical connections or components. Flexible PCBs consist of a thin layer of conductive material, typically copper, which is laminated between two layers of flexible insulating material.
The flexibility of these PCBs enables designers to create more compact and lightweight electronic devices, as well as to accommodate unique form factors and packaging requirements. Flexible PCBs can be single-sided, double-sided, or multi-layered, depending on the complexity and density of the circuit design.
Types of Flexible PCBs
There are three main types of flexible PCBs:
-
Single-sided flexible PCBs: These PCBs have conductive traces on only one side of the flexible substrate. They are the simplest and most cost-effective type of flexible PCB.
-
Double-sided flexible PCBs: These PCBs have conductive traces on both sides of the flexible substrate, allowing for more complex circuit designs and higher component density.
-
Multi-layer flexible PCBs: These PCBs consist of three or more layers of flexible substrate with conductive traces sandwiched between them. Multi-layer flexible PCBs offer the highest level of circuit complexity and density.
Advantages of Flexible PCBs
Flexible PCBs offer numerous advantages over traditional rigid PCBs, making them an attractive choice for many electronic applications. Some of the key advantages include:
Flexibility and Durability
The most obvious advantage of flexible PCBs is their ability to bend and flex without damaging the electrical connections or components. This flexibility allows designers to create electronic devices with unique form factors and packaging requirements, such as Wearable Technology, medical implants, and aerospace applications.
Flexible PCBs are also highly durable and resistant to vibration and shock. The flexible substrate can absorb mechanical stress and strain, reducing the risk of damage to the electronic components and connections. This durability makes flexible PCBs ideal for applications that require high reliability and long-term performance.
Lightweight and Compact Design
Flexible PCBs are significantly thinner and lighter than rigid PCBs, making them ideal for applications where weight and size are critical factors. The thin profile of flexible PCBs allows designers to create more compact and streamlined electronic devices, such as smartphones, tablets, and portable medical devices.
The ability to bend and fold flexible PCBs also enables more efficient use of space within an electronic device. Designers can route flexible PCBs around obstacles and components, reducing the overall size and weight of the device.
Improved Signal Integrity
Flexible PCBs offer superior signal integrity compared to traditional rigid PCBs. The flexible substrate and thinner dielectric layers reduce the distance between conductive traces, minimizing signal loss and interference. This improved signal integrity is particularly important in high-frequency applications, such as wireless communication devices and high-speed data transmission.
Additionally, flexible PCBs can be designed with controlled impedance, ensuring consistent signal quality and reducing the risk of signal reflections and distortions.
Cost-Effective Manufacturing
While the initial setup costs for flexible PCB manufacturing may be higher than those for rigid PCBs, the overall cost-effectiveness of flexible PCBs can be significant in the long run. The ability to create more compact and lightweight devices reduces material costs and shipping expenses.
Furthermore, flexible PCBs can simplify the assembly process by reducing the number of connectors and wires required. This streamlined assembly can lead to lower manufacturing costs and faster production times.
Enhanced Thermal Management
Flexible PCBs offer better thermal management compared to rigid PCBs. The thin profile and flexible nature of the substrate allow for more efficient heat dissipation, reducing the risk of thermal damage to electronic components.
In applications where heat generation is a concern, flexible PCBs can be designed with thermal management features, such as heat sinks and thermal vias, to further enhance heat dissipation and ensure reliable performance.
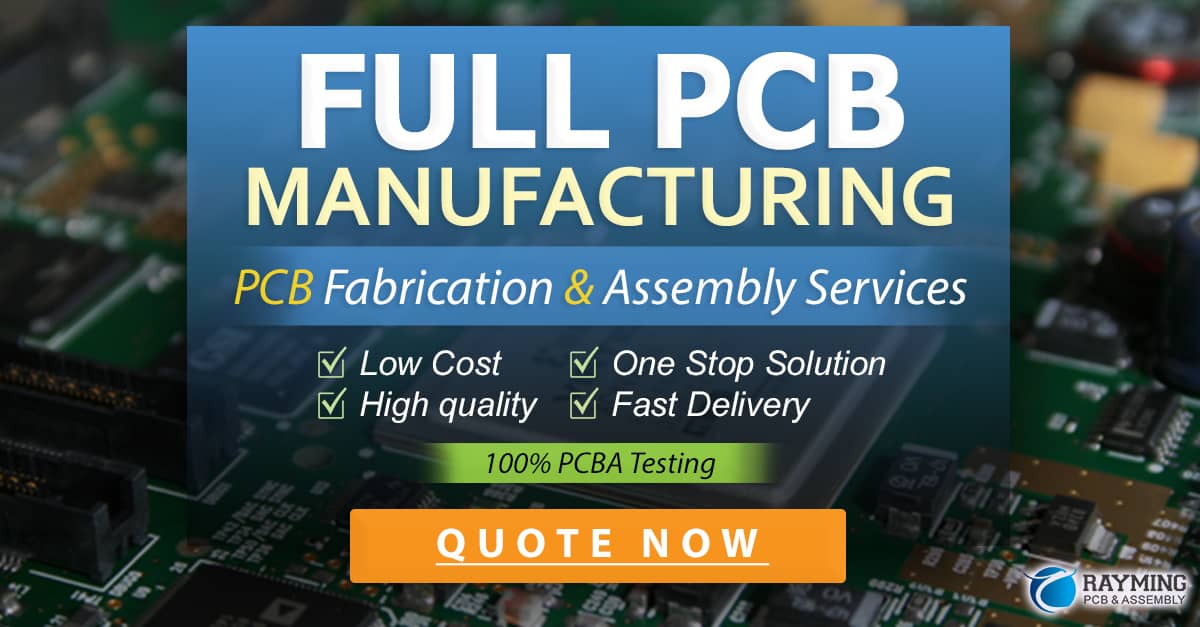
Disadvantages of Flexible PCBs
Despite their numerous advantages, flexible PCBs also have some disadvantages that should be considered when deciding whether to use them in a particular application. Some of the main disadvantages include:
Limited Component Mounting Options
Flexible PCBs have limitations when it comes to mounting electronic components. Due to the flexible nature of the substrate, it can be challenging to securely attach heavy or large components without causing stress on the PCB or compromising its flexibility.
In some cases, additional support structures or stiffeners may be required to ensure proper component mounting and reliability. This can add complexity and cost to the design and manufacturing process.
Reduced Conductor Thickness
To maintain flexibility, the conductive traces on flexible PCBs are typically thinner than those on rigid PCBs. This reduced conductor thickness can lead to higher electrical resistance and increased power loss, particularly in high-current applications.
Designers must carefully consider the trade-offs between flexibility and electrical performance when designing flexible PCBs, and may need to use wider traces or multiple layers to compensate for the reduced conductor thickness.
Increased Complexity in Design and Manufacturing
Designing and manufacturing flexible PCBs can be more complex than rigid PCBs. The flexible nature of the substrate requires special consideration for bend radii, stress distribution, and material selection.
Additionally, the manufacturing process for flexible PCBs involves specialized equipment and techniques, such as laser cutting, selective bonding, and cover lay application. This increased complexity can lead to higher design and manufacturing costs, as well as longer lead times compared to rigid PCBs.
Limited Operating Temperature Range
Flexible PCBs typically have a more limited operating temperature range compared to rigid PCBs. The flexible substrate materials, such as polyimide, can degrade or lose their flexibility at high temperatures, while the adhesives used in the manufacturing process may become brittle at low temperatures.
This limited operating temperature range can restrict the use of flexible PCBs in certain applications, such as those exposed to extreme heat or cold. Designers must carefully consider the expected operating conditions and select appropriate materials and manufacturing processes to ensure reliable performance.
Challenges in Repair and Rework
Repairing or reworking flexible PCBs can be more challenging than rigid PCBs. The thin and flexible nature of the substrate makes it more susceptible to damage during repair or rework processes.
Additionally, the specialized materials and manufacturing techniques used in flexible PCBs may require unique repair and rework methods, which can be more time-consuming and costly compared to rigid PCBs.
Manufacturing Process of Flexible PCBs
The manufacturing process for flexible PCBs involves several specialized steps and techniques to ensure the desired flexibility, reliability, and performance. The main steps in the manufacturing process include:
-
Substrate Preparation: The flexible substrate material, typically polyimide or polyester, is cleaned and prepared for the manufacturing process.
-
Conductor Patterning: The conductive traces are patterned onto the flexible substrate using techniques such as photolithography, screen printing, or laser direct imaging.
-
Lamination: Multiple layers of the flexible substrate with conductive traces are laminated together using heat and pressure to form a multi-layer flexible PCB.
-
Drilling and Cutting: Through-holes and vias are drilled into the flexible PCB, and the board is cut to its final shape using laser cutting or die-cutting techniques.
-
Surface Finishing: The exposed copper traces are coated with a protective finish, such as gold, nickel, or solder, to prevent oxidation and ensure reliable electrical connections.
-
Cover Lay Application: A protective cover lay is applied to the flexible PCB to insulate and protect the conductive traces and components.
-
Component Assembly: Electronic components are attached to the flexible PCB using specialized techniques, such as surface mount technology (SMT) or chip-on-flex (COF) assembly.
Applications of Flexible PCBs
Flexible PCBs find applications in a wide range of industries and products, thanks to their unique characteristics and advantages. Some of the most common applications include:
Consumer Electronics
Flexible PCBs are widely used in consumer electronics, such as smartphones, tablets, laptops, and wearable devices. The flexibility and compact design of flexible PCBs allow for thinner, lighter, and more ergonomic devices, while also enabling unique form factors and folding mechanisms.
Medical Devices
Flexible PCBs are increasingly used in medical devices, such as hearing aids, pacemakers, and prosthetic limbs. The flexibility and biocompatibility of certain flexible substrate materials make them suitable for implantable and wearable medical devices, while the compact design enables miniaturization and improved patient comfort.
Automotive Electronics
Flexible PCBs are used in various automotive electronics applications, such as instrument clusters, infotainment systems, and advanced driver assistance systems (ADAS). The flexibility and durability of flexible PCBs make them well-suited for the harsh environmental conditions and vibrations encountered in automotive applications.
Aerospace and Defense
Flexible PCBs are used in aerospace and defense applications, such as satellites, aircraft, and military equipment. The lightweight and compact design of flexible PCBs helps reduce overall system weight and size, while their flexibility and durability enable reliable performance in extreme environmental conditions and high-stress situations.
Industrial Equipment
Flexible PCBs are used in industrial equipment, such as robotics, automation systems, and process control devices. The flexibility and durability of flexible PCBs allow for reliable operation in harsh industrial environments, while their compact design enables more efficient use of space and improved system integration.
Future Trends in Flexible PCBs
As the demand for smaller, lighter, and more advanced electronic devices continues to grow, flexible PCBs are expected to play an increasingly important role in shaping the future of the electronics industry. Some of the key trends and developments in flexible PCBs include:
Increased Adoption of High-Frequency Materials
With the growing demand for high-speed data transmission and wireless communication, there is a growing trend towards the use of high-frequency materials in flexible PCBs. These materials, such as liquid crystal polymer (LCP) and polytetrafluoroethylene (PTFE), offer superior dielectric properties and signal integrity, enabling faster and more reliable data transmission.
Integration of Advanced Components and Sensors
Flexible PCBs are expected to incorporate more advanced components and sensors, such as microelectromechanical systems (MEMS), optical sensors, and biometric sensors. This integration will enable new applications and functionalities in fields such as wearable technology, medical devices, and the Internet of Things (IoT).
Adoption of Additive Manufacturing Techniques
Additive manufacturing techniques, such as 3D printing and inkjet printing, are expected to play a larger role in the production of flexible PCBs. These techniques offer greater design flexibility, faster prototyping, and the potential for more cost-effective small-batch production.
Development of Stretchable and Self-Healing Materials
Researchers are exploring the development of stretchable and self-healing materials for use in flexible PCBs. These materials could enable even greater flexibility and durability, as well as the ability to self-repair in the event of damage, leading to longer-lasting and more reliable electronic devices.
Increasing Focus on Sustainability and Recyclability
As environmental concerns continue to grow, there is an increasing focus on the sustainability and recyclability of electronic components, including flexible PCBs. Manufacturers are exploring the use of eco-friendly materials and processes, as well as designing flexible PCBs for easier disassembly and recycling at the end of their life cycle.
Frequently Asked Questions (FAQ)
-
What is the difference between flexible and rigid PCBs?
Flexible PCBs are made from thin, flexible materials that allow them to bend and conform to various shapes, while rigid PCBs are made from rigid, non-flexible materials and maintain a fixed shape. -
Can flexible PCBs be used in high-temperature applications?
Flexible PCBs typically have a more limited operating temperature range compared to rigid PCBs, as the flexible substrate materials can degrade or lose their flexibility at high temperatures. However, careful material selection and design considerations can enable the use of flexible PCBs in some high-temperature applications. -
Are flexible PCBs more expensive than rigid PCBs?
The initial setup costs for flexible PCB manufacturing may be higher than those for rigid PCBs due to the specialized materials and processes involved. However, the overall cost-effectiveness of flexible PCBs can be significant in the long run, thanks to their ability to enable more compact and lightweight designs, streamline assembly, and reduce material and shipping costs. -
How do I choose the right type of flexible PCB for my application?
Choosing the right type of flexible PCB depends on factors such as the complexity of the circuit design, the required level of flexibility and durability, the expected operating conditions, and the cost and manufacturing constraints. Consultation with experienced PCB designers and manufacturers can help guide the selection process. -
Can flexible PCBs be repaired or reworked?
Repairing or reworking flexible PCBs can be more challenging than rigid PCBs due to their thin and flexible nature, as well as the specialized materials and processes involved. However, with the right expertise and techniques, flexible PCBs can be successfully repaired or reworked when necessary.
Conclusion
Flexible PCBs have emerged as a game-changing technology in the electronics industry, offering numerous advantages over traditional rigid PCBs. Their flexibility, durability, lightweight and compact design, improved signal integrity, and cost-effective manufacturing make them an attractive choice for a wide range of applications, from consumer electronics to medical devices and aerospace technology.
While flexible PCBs also have some disadvantages, such as limited component mounting options and increased complexity in design and manufacturing, ongoing research and development efforts are helping to address these challenges and unlock new possibilities for flexible PCBs.
As the demand for smaller, lighter, and more advanced electronic devices continues to grow, flexible PCBs are poised to play an increasingly important role in shaping the future of the electronics industry. By staying informed about the latest trends and developments in flexible PCBs, designers and manufacturers can leverage this versatile technology to create innovative and reliable electronic solutions for a wide range of applications.
Characteristic | Flexible PCBs | Rigid PCBs |
---|---|---|
Flexibility | High | Low |
Durability | High | Moderate |
Weight | Low | High |
Size | Compact | Larger |
Signal Integrity | High | Moderate |
Manufacturing Cost | Higher (initial) | Lower (initial) |
Component Mounting | Limited | Versatile |
Operating Temperature Range | Limited | Wider |
Repair and Rework | Challenging | Easier |
0 Comments