Introduction to Flex PCB Manufacturing
Flexible printed circuit boards (Flex PCBs) have revolutionized the electronics industry by providing a versatile and reliable solution for applications that require flexibility, durability, and compact designs. Unlike traditional rigid PCBs, flex PCBs can bend, twist, and conform to various shapes, making them ideal for wearable devices, medical equipment, automotive systems, and aerospace applications. In this article, we will delve into the intricacies of the flex PCB manufacturing process, exploring the materials, techniques, and quality control measures involved in creating these innovative circuit boards.
What are Flex PCBs?
Flex PCBs, also known as flexible printed circuits (FPCs), are a type of printed circuit board that consists of a thin, flexible substrate made of materials such as polyimide or polyester. These substrates are laminated with conductive copper traces and can be populated with electronic components, just like rigid PCBs. The key difference lies in their ability to bend and flex without damaging the circuitry or components, enabling designers to create more compact and adaptable electronic devices.
Advantages of Flex PCBs
Flex PCBs offer several advantages over traditional rigid PCBs, including:
- Flexibility and durability: Flex PCBs can withstand repeated bending and flexing without losing their electrical properties or structural integrity.
- Space-saving designs: By eliminating the need for bulky connectors and wires, flex PCBs enable more compact and lightweight electronic devices.
- Improved signal integrity: The shorter trace lengths and reduced interconnections in flex PCBs minimize signal loss and interference.
- Enhanced reliability: Flex PCBs are resistant to vibration, shock, and extreme temperatures, making them suitable for harsh environments.
- Cost-effective: Although the initial cost of flex PCBs may be higher than rigid PCBs, they can reduce overall system costs by simplifying assembly and minimizing the need for additional connectors and wires.
Flex PCB Manufacturing Process
The flex PCB manufacturing process involves several critical steps that ensure the quality, reliability, and functionality of the final product. These steps include:
1. Design and Layout
The first step in the flex PCB manufacturing process is designing the circuit layout using specialized software tools. The design must consider the specific requirements of the application, such as the desired flexibility, bend radius, and component placement. The designer must also adhere to the design rules and guidelines specific to flex PCBs, such as minimum trace widths, spacing, and bend radius limitations.
2. Material Selection
Selecting the appropriate materials for the flex PCB is crucial to ensure its performance and durability. The most common substrate materials used in flex PCBs are polyimide (PI) and polyester (PET). Polyimide is known for its excellent thermal stability, chemical resistance, and mechanical strength, making it suitable for high-reliability applications. Polyester, on the other hand, is a more cost-effective option for less demanding applications.
The conductive traces on flex PCBs are typically made of copper, which is laminated onto the substrate material. The copper thickness can vary depending on the current-carrying requirements and the desired flexibility of the PCB.
3. Imaging and Etching
Once the design is finalized and the materials are selected, the next step is to transfer the circuit pattern onto the copper-clad substrate. This process involves applying a photoresist layer onto the copper and exposing it to UV light through a photomask that contains the circuit pattern. The exposed areas of the photoresist become soluble and can be removed using a developer solution, leaving behind the desired copper traces.
After developing, the unwanted copper is removed through an etching process, typically using a chemical solution such as ferric chloride or ammonium persulfate. The remaining photoresist is then stripped away, revealing the final copper circuit pattern.
4. Lamination and Coverlay
To protect the copper traces and provide additional insulation, a coverlay film is laminated onto the flex PCB. The coverlay is a thin, flexible film made of materials such as polyimide or polyester, and it is typically applied using heat and pressure. The coverlay also serves as a solder mask, preventing solder bridges and short circuits during the assembly process.
In some cases, multiple layers of flex PCBs may be laminated together to create a multi-layer flex PCB. This process involves aligning the layers precisely and bonding them together using heat and pressure.
5. Drilling and Cutting
After lamination, the flex PCB undergoes drilling and cutting processes to create holes for component mounting and to define the final shape of the board. Laser drilling is often used for flex PCBs due to its precision and ability to create small, accurate holes without damaging the substrate or copper traces.
The cutting process can be performed using various methods, such as die-cutting, laser cutting, or routing. The choice of cutting method depends on the complexity of the board shape, the required accuracy, and the production volume.
6. Surface Finishing
To enhance the solderability and protect the exposed copper traces from oxidation, a surface finish is applied to the flex PCB. Common surface finishes for flex PCBs include:
- ENIG (Electroless Nickel Immersion Gold): A layer of nickel is deposited onto the copper, followed by a thin layer of gold. ENIG provides excellent solderability and shelf life.
- OSP (Organic Solderability Preservative): A thin, organic coating is applied to the copper to prevent oxidation. OSP is a cost-effective option but has a limited shelf life.
- Immersion Silver: A thin layer of silver is deposited onto the copper, providing good solderability and electrical conductivity.
7. Quality Control and Inspection
Throughout the flex PCB manufacturing process, strict quality control measures are implemented to ensure the reliability and functionality of the final product. These measures include:
- Visual inspection: Automated optical inspection (AOI) systems and manual visual checks are performed to identify any defects, such as shorts, opens, or misalignments.
- Electrical testing: Flying probe testing and fixtureless in-circuit testing (ICT) are used to verify the electrical continuity and functionality of the flex PCB.
- Mechanical testing: Bend and twist tests are conducted to ensure the flex PCB can withstand the required flexing and bending without losing its electrical properties.
- Environmental testing: Flex PCBs may be subjected to thermal cycling, humidity, and vibration tests to validate their performance in the intended operating environment.
Flex PCB Assembly
Once the flex PCB manufacturing process is complete, the board is ready for component assembly. The assembly process for flex PCBs is similar to that of rigid PCBs, with a few additional considerations:
-
Handling: Flex PCBs require careful handling during assembly to prevent damage or excessive bending. Specialized fixtures and support structures may be used to ensure proper alignment and stability.
-
Soldering: Surface mount technology (SMT) is the most common method for assembling components onto flex PCBs. Reflow soldering, where solder paste is applied to the pads and components are placed before heating, is widely used. Hand soldering or selective soldering may be employed for through-hole components or rework.
-
Stiffeners: In some cases, stiffeners may be attached to specific areas of the flex PCB to provide additional support for components or to maintain a desired shape.
-
Connectors: Flex PCBs often utilize specialized connectors, such as zero insertion force (ZIF) or low insertion force (LIF) connectors, to allow for easy and reliable connections to other parts of the system.
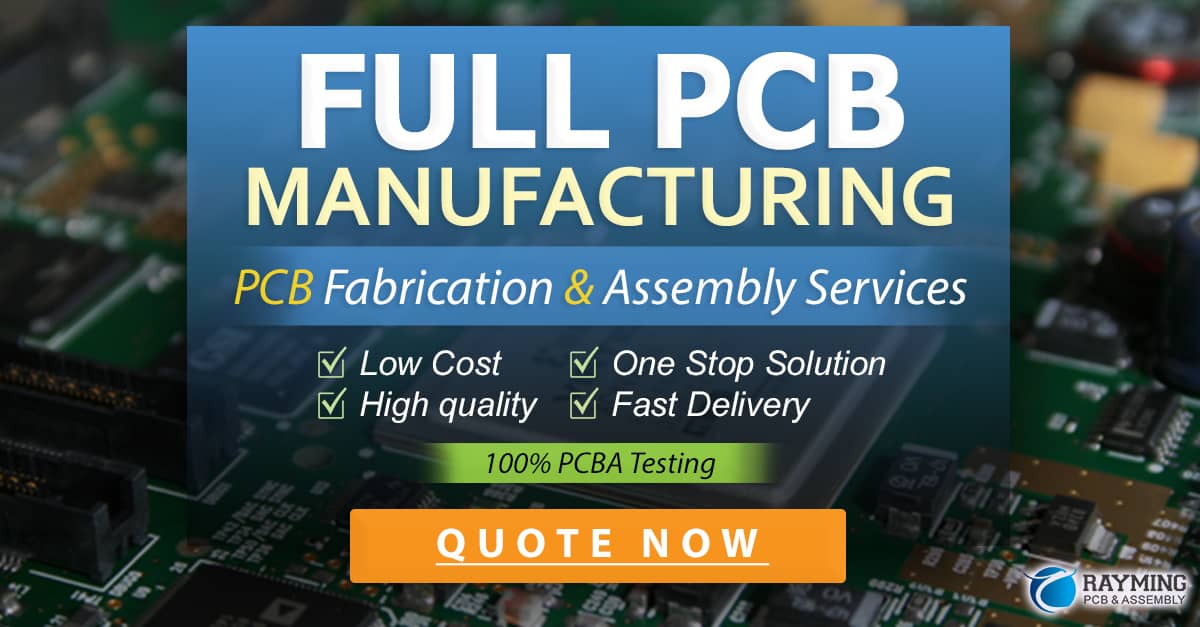
Applications of Flex PCBs
Flex PCBs find applications in a wide range of industries and products, including:
-
Wearable electronics: Smartwatches, fitness trackers, and medical monitoring devices leverage flex PCBs to achieve compact, lightweight, and comfortable designs.
-
Medical devices: Flex PCBs are used in medical equipment such as hearing aids, endoscopes, and implantable devices, where flexibility and reliability are crucial.
-
Automotive electronics: Flex PCBs are employed in automotive applications such as dashboard displays, camera modules, and sensor systems, where space constraints and harsh environments are common.
-
Aerospace and defense: Flex PCBs are used in avionics, satellites, and military equipment, where high reliability, vibration resistance, and weight reduction are essential.
-
Consumer electronics: Smartphones, tablets, and laptops utilize flex PCBs for connecting displays, batteries, and other components, enabling slimmer and more compact designs.
Challenges and Future Trends in Flex PCB Manufacturing
While flex PCBs offer numerous benefits, their manufacturing process also presents some challenges, such as:
-
Design complexity: Designing flex PCBs requires specialized knowledge and tools to ensure proper functionality and reliability.
-
Material selection: Choosing the right substrate and copper thickness for a specific application can be challenging, as it affects the flexibility, durability, and cost of the PCB.
-
Process control: Maintaining tight process control during the manufacturing process is essential to ensure consistent quality and yield.
-
Assembly challenges: The flexible nature of flex PCBs can make the assembly process more complex, requiring specialized handling and fixturing techniques.
Despite these challenges, the demand for flex PCBs continues to grow as electronic devices become smaller, smarter, and more connected. Future trends in flex PCB manufacturing include:
-
Advanced materials: The development of new substrate materials with improved thermal, mechanical, and electrical properties will enable flex PCBs to be used in even more demanding applications.
-
High-density interconnects (HDI): The adoption of HDI techniques, such as microvias and fine-pitch traces, will allow for greater circuit density and miniaturization in flex PCBs.
-
3D printing: The integration of 3D printing technologies in flex PCB manufacturing could enable the creation of complex, three-dimensional circuit structures and further optimize space utilization.
-
Sustainable manufacturing: As environmental concerns grow, there will be an increased focus on developing eco-friendly materials and processes for flex PCB manufacturing, such as halogen-free substrates and recyclable materials.
Frequently Asked Questions (FAQ)
1. What is the difference between flex PCBs and rigid PCBs?
Flex PCBs are made of flexible substrate materials, such as polyimide or polyester, which allow them to bend and flex without losing their electrical properties. Rigid PCBs, on the other hand, are made of a rigid substrate material, typically FR-4, and cannot bend or flex.
2. What are the advantages of using flex PCBs?
Flex PCBs offer several advantages, including increased flexibility and durability, space-saving designs, improved signal integrity, enhanced reliability, and potential cost savings by reducing the need for connectors and wires.
3. What are the common materials used in flex PCB manufacturing?
The most common substrate materials used in flex PCBs are polyimide (PI) and polyester (PET). Copper is the primary conductive material used for the traces, and coverlay films made of polyimide or polyester are used for insulation and protection.
4. How are flex PCBs assembled?
Flex PCBs are typically assembled using surface mount technology (SMT), with components being soldered onto the board using reflow soldering. Specialized fixtures and handling techniques are employed to prevent damage or excessive bending during the assembly process.
5. What industries commonly use flex PCBs?
Flex PCBs are used in a wide range of industries, including wearable electronics, medical devices, automotive electronics, aerospace and defense, and consumer electronics, where flexibility, reliability, and compact designs are essential.
Conclusion
Flex PCB manufacturing is a complex and intricate process that involves several critical steps, from design and material selection to imaging, etching, lamination, and quality control. By understanding the materials, techniques, and challenges involved in flex PCB manufacturing, designers and engineers can leverage the benefits of these versatile circuit boards to create innovative, reliable, and compact electronic devices.
As the demand for smaller, smarter, and more connected devices continues to grow, the importance of flex PCBs in the electronics industry will only increase. With advancements in materials, processes, and technologies, flex PCB manufacturing is poised to evolve and adapt to meet the ever-changing needs of the market, enabling the development of even more groundbreaking and transformative electronic products.
Step | Description |
---|---|
1. Design and Layout | Creating the circuit layout using specialized software tools, considering the specific requirements of the application. |
2. Material Selection | Choosing the appropriate substrate materials (e.g., polyimide or polyester) and copper thickness for the flex PCB. |
3. Imaging and Etching | Transferring the circuit pattern onto the copper-clad substrate using photoresist and UV exposure, followed by etching away the unwanted copper. |
4. Lamination and Coverlay | Applying a coverlay film to protect the copper traces and provide additional insulation, and laminating multiple layers together if required. |
5. Drilling and Cutting | Creating holes for component mounting and defining the final shape of the board using methods such as laser drilling, die-cutting, or routing. |
6. Surface Finishing | Applying a surface finish (e.g., ENIG, OSP, or immersion silver) to enhance solderability and protect the exposed copper traces. |
7. Quality Control and Inspection | Implementing strict quality control measures, including visual inspection, electrical testing, mechanical testing, and environmental testing. |
In conclusion, the flex PCB manufacturing process is a testament to the ingenuity and precision of the electronics industry, enabling the creation of innovative, flexible, and reliable circuit boards that power the devices we rely on every day.
0 Comments